El correcto desarrollo de esta solución determinará la calidad de la obra realizada. Se debe prestar atención a cada detalle del diseño y contar con un personal capacitado para que no se generen problemas en el proceso de aplicación. Esa es la clave.
Ampliamente usado en obras de construcción subterránea, el hormigón proyectado se ha comenzado a emplear en la construcción de taludes, donde forma parte vital en el sistema primario de soporte.
En construcción de taludes, el desarrollo de esta solución ha tomado lugar a través de una estrecha colaboración entre usuarios y fabricantes de equipos y aditivos, logrando que el actual rango de equipos y productos disponibles en diversos países satisfaga la demanda por la alta calidad y economía de este material.
El shotcrete es un método de colocación de hormigón, que utiliza en forma combinada y simultánea, sistemas de bombeo y aire a alta presión, con lo cual se consigue impulsar con velocidad, mezclas de mortero sobre superficies comúnmente verticales o sobre cabeza. Para ello, la mezcla a proyectar debe cumplir con características especiales relacionadas con la combinación adecuada de las arenas, dosis de finos y razón agua/cemento. Por su parte, el revestimiento de taludes mediante la proyección del hormigón permitiría estabilizar el comportamiento del suelo, evitando desmoronamientos ya sea por falta de cohesión o bien, por la acción del viento o lluvia, que generan erosión sobre estos terrenos. La finalidad con este método, es conseguir un refuerzo estructural que permita absorber todas las deficiencias que posee el suelo en su estado natural.
Bernardo Vicencio, Constructor Civil y consultor del Instituto del Cemento y del Hormigón de Chile, ICH, en temas de shotcrete, cuenta que este material usado en taludes constituye una buena solución para el ingeniero responsable de su diseño y estabilidad. Lo anterior, porque el shotcrete puede conformar desde un “sello” del terreno expuesto hasta una “placa” de soporte. Asimismo explica que constituiría una buena solución para el sostenimiento de taludes por su gran versatilidad para ajustarse a los requerimientos del diseño. Esto, porque su uso en taludes puede ser solo o combinado con otros elementos como armaduras, mallas y fibras que complementan y/o mejoran sus prestaciones ampliando las opciones del ingeniero, diseñador o calculista.
Preparación
El diseño de dosificaciones para hormigón proyectado se basa normalmente en la resistencia a la compresión. En aplicaciones especiales, pueden requerirse propiedades distintas a la resistencia a la compresión, tales como impermeabilidad o durabilidad. Hay dos aproximaciones distintas para especificar una dosificación: por comportamiento o por prescripción. En el primer caso, se especifica la calidad requerida por el diseño y el constructor decide cómo cumplir con ella, situación en la que normalmente se especifica la calidad de materias primas y la resistencia a la compresión. En el caso de dosificación por prescripción, se indica solamente la calidad de materias primas y su proporción en masa.
A esto, el consultor del ICH agrega que una de las dificultades que debe superar una mezcla para shotcrete es la “bombeabilidad”, es decir el desplazarse o pasar por las tuberías y mangueras de diferente diámetro del equipo de proyección. Esta dificultad para moverse y acomodarse entre tuberías de 4” y mangueras de 2” deben considerarse en el diseño de la mezcla con una adecuada granulometría de la arena y una adecuada cantidad de cemento.
Cuando se trate de dosificación para mezclas por vía húmeda, se indica adicionalmente el asentamiento y el contenido de aire (si se requiere).
El contenido de aglomerante en mezclas proyectadas, oscila normalmente entre los 400 y 500 kilos de cemento por 1.000 litros de mezcla. La dosificación por vía húmeda se puede hacer de acuerdo con métodos conocidos, para hormigones bombeados. El asentamiento debe ser el mínimo que pueda colocarse con el equipo empleado, ya que el exceso de este puede producir mezclas más débiles y deslizamiento o desprendimiento en colocación sobre superficies verticales o sobre cabeza.
En algunos casos, las pruebas previas a la construcción apuntan a verificar el efecto de la cantidad y espaciamiento de las enfierraduras u otras condiciones similares, a fin de proveer una indicación confiable de la calidad que puede obtenerse de la estructura. Estas pruebas previas pueden efectuarse en paralelo con el inicio de la obra, o bien los testigos pueden extraerse de las primeras mezclas proyectadas en la estructura. Estos tienen la ventaja adicional de entrar hasta el soporte (por ejemplo: roca u hormigón) y permiten examinar la adherencia.
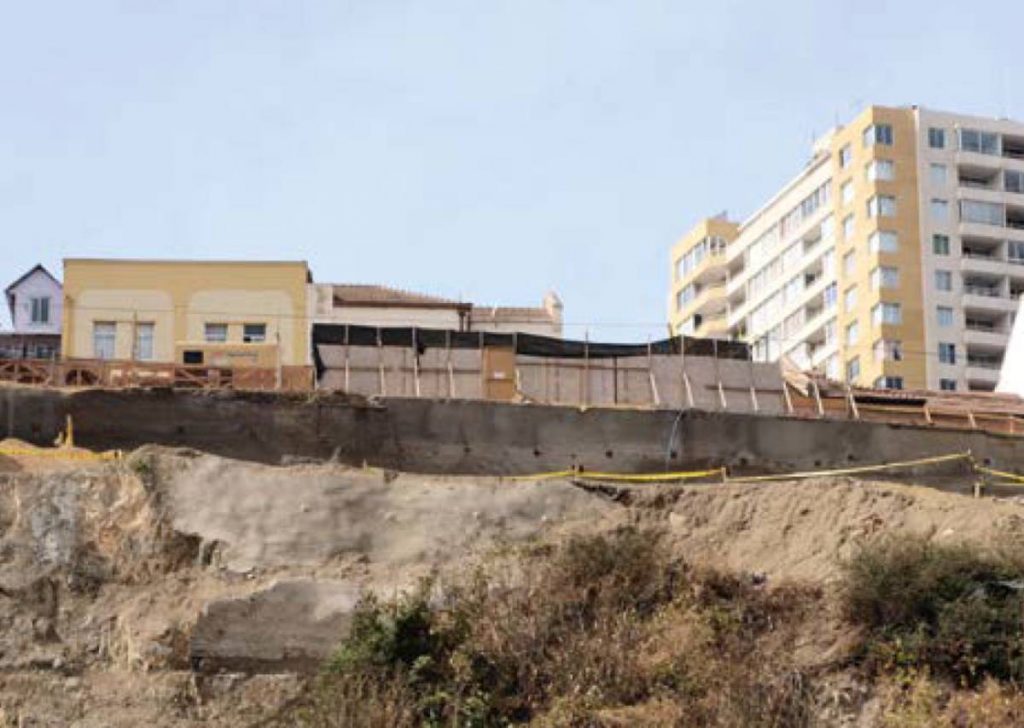
En cuanto a la colocación de armaduras en la estructura, se recomienda que normalmente se utilicen fijaciones de mallas que se pueden denominar como ligeras. En los casos de obras de ingeniería civil, como túneles, muros y taludes se hace necesario la fijación por medio de sistemas pesados, como son bulones, barras, anclajes, entre otras. En caso de que dos o más capas de armadura vayan a ser proyectadas, la capa externa no debe ser asegurada directamente con la interna, sino que tiene que ser escalonada de manera que permita a la cara interna ser proyectada sin interferencia.
En tanto, Vicencio cuenta que “los pernos o cables de anclaje, las mallas tejidas o soldadas de acero y las fibras de acero y sintéticas hacen, en conjunto con el shotcrete, una placa que es capaz de tomar y transmitir los esfuerzos o la deformación del talud”.
Proyección
Una vez determinada la máquina a utilizar, se debe:
- Comprobar que las mangueras de proyección estén limpias, para ello se conectan a un compresor que disponga de un manómetro, si éste muestra una presión superior a la normal, significa que las mangueras están sucias. En este caso, deben limpiarse doblándolas, torciéndolas o golpeándolas suavemente con un martillo, volviendo a dar aire y expulsando así el material alojado en los conductos.
- Conectar las mangueras formando el menor número posible de curvas y, de ser posible, sin ningún rizo.
- Comprobar la salida del agua y/o del aditivo, para los casos de vía seca o húmeda respectivamente, así como el funcionamiento de las bombas.
- Estando en funcionamiento la bomba de agua y/o aditivo, se deberá dar entrada al aire comprimido, con lo cual, se examinará el abanico que forma la pistola, viendo inmediatamente si existe algún fallo de suministro en los eyectores, para lo cual, visto éste, se deberá solucionar limpiando o cambiando la boquilla. Si el abanico es débil quiere decir que no hay suficiente presión de aire, en este caso, se deberá incrementar la misma. La manguera debe estar conectada con la boquilla y la bomba, para comenzar con la proyección. El pitonero deberá mantener la boquilla (pistola) hacia abajo, en espera del suministro de la mezcla.
Consejos técnicos
Según lo que recomienda Carlos Sánchez, experto en temáticas de Shotcrete, el hormigón proyectado debe ser adecuadamente proporcionado en sus componentes de tal forma que sea transportado y expulsado con facilidad por medio de la bomba y compresor. Asimismo, debe realizarse una calibración rigurosa de caudales, con la finalidad de aplicar la dosis precisa de aditivo acelerante, evitando dosis menores, que se traducen de desprendimientos o sobredosis que generan pérdidas de resistencia. “En general, un buen diseño de mezcla en conjunto con los equipos adecuados y personal calificado en proyección, garantiza buenos resultados finales”.
Por otro lado, Gerardo Staforelli, actual gerente general de Euclid Chemical Cave, afirma que el principal cuidado se refiere a los procesos de curado del material en taludes, considerando que es un tipo de shotcrete diferente al de túnel, al estar mucho más expuesto a las condiciones ambientales, con un alto potencial de fisuración.
Asimismo, afirma que, considerando la geometría y la ubicación de muchos de estos taludes, el viento y el sol genera altas tazas de evaporación, por lo que se recomienda utilizar sistemas de protección iniciales tipo alcohol alifático.
También, se recomienda que al terminar el trabajo se debe limpiar adecuadamente las mangueras y las máquinas, para lo cual se cortará el suministro de la mezcla y se dejará el aire comprimido salir libremente por la manguera, doblando ésta antes de la boquilla, disparando de vez en cuando la cantidad de aire para que se limpie totalmente, tanto la máquina como mangueras en todo su recorrido.
Otra recomendación es la preparación de la superficie del talud para asegurar la adherencia y la estabilidad.
Además, Vicencio aconseja que el equipo de proyección debe ser el adecuado para alcanzar los requerimientos técnicos y de calidad determinados por el diseño y la ingeniería. Por ejemplo, adherencia, estabilidad, durabilidad, seguridad operacional u otros. A esto, el experto del ICH agrega que el volumen y caudal de aire comprimido tiene que ser el adecuado para lograr los requerimientos técnicos. Según la recomendación europea EFNARC, por ejemplo, es de 12 m3/min y 7 bares de presión.
Asimismo, se recomienda tener un personal idóneo y capacitado técnicamente para ejecutar todo el proceso de proyección de shotcrete. En lo posible, esta actividad debe ser ejecutada por personal certificado.
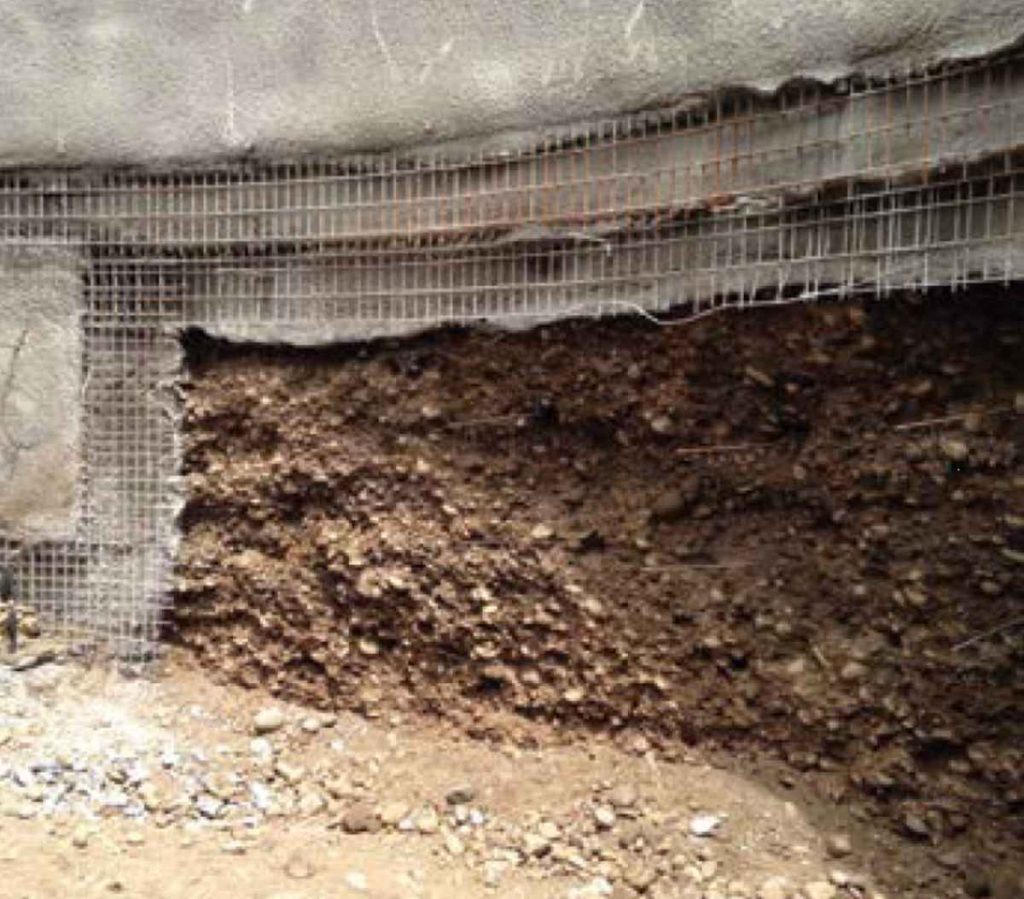
De acuerdo a los expertos, uno de los errores de aplicación de este sistema, se relaciona con la sobrecarga del talud, lo que genera asentamientos y desprendimientos del mortero de proyección. De igual forma, al proyectar sobre terrenos inestables, se aumenta la presión del aire de proyección, generando el mismo efecto.
La regulación de la dosis de acelerante, tampoco está exenta de ocurrencia, generando pérdidas de resistencia mecánica a 7 y 28 días, además de una alta probabilidad de oquedades en la zona de armaduras.
Otro error tiene que ver con la mezcla de mortero gruesas que perjudican la adherencia y aumentan el porcentaje de rechazo (pérdidas), además de dificultar el traslado del mortero al interior de las tuberías generando una proyección ineficiente.
Los expertos también coinciden en que uno de los errores más comunes provendría de los que se cometen por parte del personal a cargo de la proyección, generalmente, por falta de un adecuado entrenamiento y capacitación en los conceptos fundamentales que determinan la calidad y la durabilidad del shotcrete.
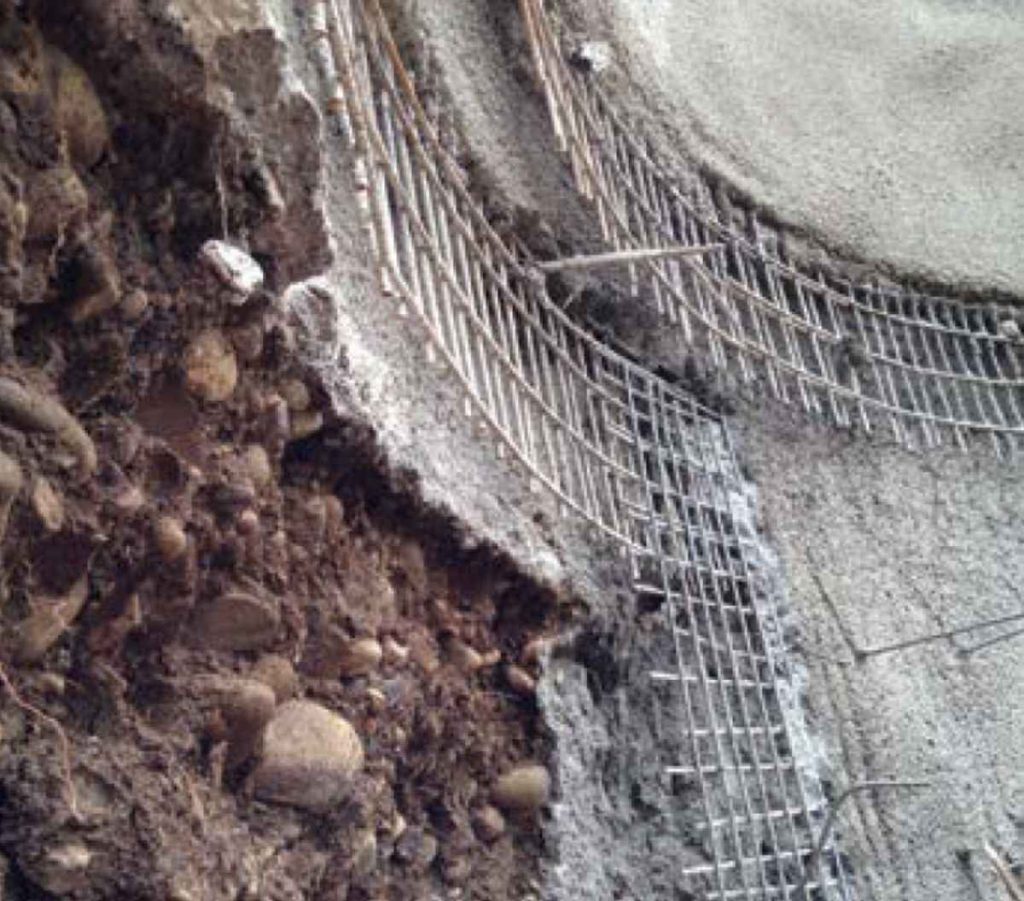
Por lo general, toda obra de carácter estructural está sometida a fiscalización. La construcción de taludes no es la excepción, aunque suele ser menos exigente que los requisitos indicados para la minería o construcción de túneles. Lo normal es la verificación de la resistencia mecánica del mortero proyectado, la cual se realiza mediante la extracción y ensayo de testigos endurecidos, siguiendo los procedimientos establecidos en la Normativa Chilena. Dependiendo de la especificación, podría agregarse la certificación de permeabilidad, como también, la resistencia a edades tempranas.
En síntesis, Gian Franco Compagnoni, gerente general de Robocon, concluye que “para realizar un trabajo de estabilización de un talud, debemos contar con un estudio de ingeniería que considere todos los aspectos técnicos ya comentados, la condición de terreno y el requerimiento geomecánico. Además del diseño de la ejecución, exigencias y ensayos, se tiene que cumplir con el contratista”. Asimismo, Compagnoni, recomienda que “una vez finalizado los trabajos de fortificación, se deben hacer mantenciones en los próximos días, para garantizar el buen curado del hormigón y de los detalles de las terminaciones”.