Obra de conectividad vial de suma importancia para el desarrollo urbanístico de la Región Metropolitana, una de sus particularidades estuvo en la, en ese entonces, innovadora aplicación del hormigón proyectado o shotcrete para su construcción. Este reportaje, rescatado de nuestros archivos, entrega más detalles sobre este gran proyecto.
Desde sus inicios, en el año 2005, el proyecto Túnel San Cristóbal reunió ciertas particularidades que le permitieron contar con tiempo suficiente -cerca de dos meses- para realizar una serie de pruebas, tras lo cual se pudo aportar importantes cuotas de conocimiento en el manejo y uso del shotcrete.
Concretamente, se trató de aplicaciones con mezclas de materiales de distintos proveedores de cemento, arena, aditivos y fibras, las que finalmente convirtieron a este proyecto en uno de los diez primeros túneles del mundo en usar fibra de polipropileno para el refuerzo de sostenimiento estructural, a diferencia de la fibra de acero que se utiliza en la mayoría de este tipo de construcciones, según explicaron desde la constructora a cargo del proyecto.
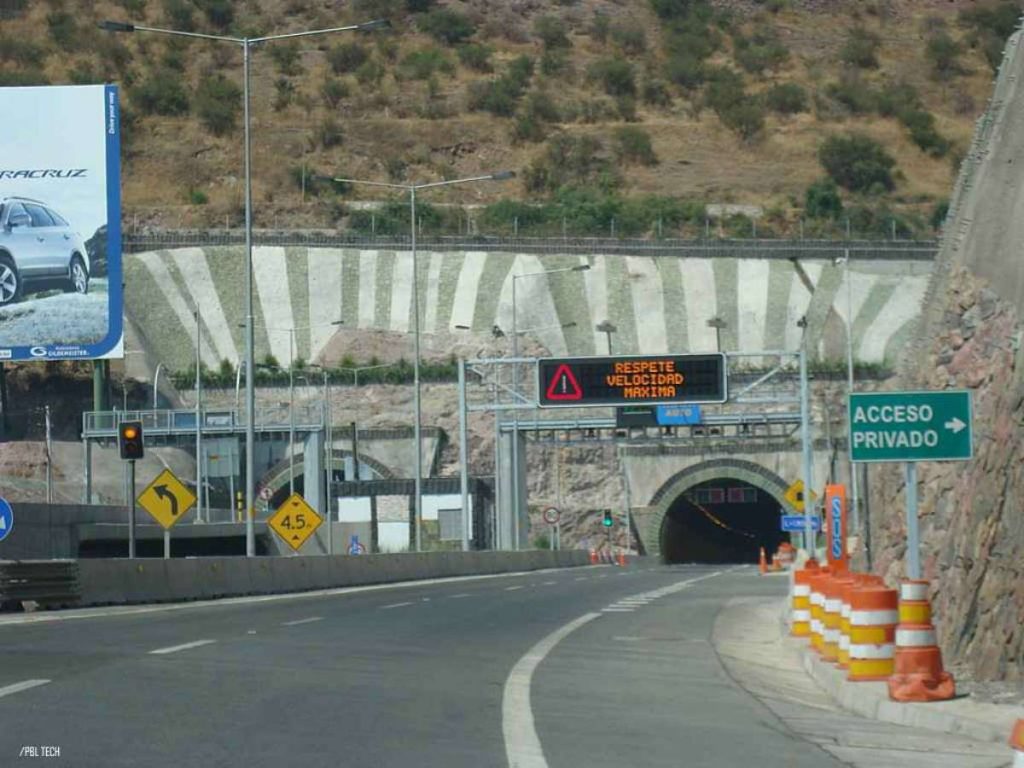
“El resultado de los ensayos -que evaluó el IDIEM de la Universidad de Chile- determinó que la malla que formaba esta fibra, sometida a flexión, se comportaba mucho mejor, con mejor resistencia y mayor durabilidad, por lo que nos atrevimos a usarla, marcando un verdadero precedente en Chile en este sentido”, comentaron.
A partir de esta experiencia, el proyecto se jugó por incorporar un gran nivel de innovación en su planteamiento y desarrollo, probando distintas opciones para cada caso. “Teníamos la posibilidad de innovar y aprovechamos esa gran oportunidad”.
Por otro lado, a nivel de diseño, otra innovación importante tuvo relación con los sistemas de evacuación temprana, que implicó temas como la detección y extinción de incendios y ventilación. En este contexto, lo más importante fue determinar salidas hacia lugares seguros, ubicadas en distancias adecuadas para ser recorridas por una persona en poco tiempo, esto es, cerca de 190 y 250 metros como máximo.
Enfocado también al tema de la seguridad, se utilizó un recubrimiento ignífugo, donde se utilizó una fibra que se consume y genera vacíos de aire al interior del hormigón, evitando que éste estalle frente a altas temperaturas.
El shotcrete
En este contexto de innovación y tecnología de punta, el uso y manejo del hormigón fue un factor fundamental del proyecto. En este sentido, la opción fue contratar a un técnico, con vasta experiencia en la colocación del shotcrete, para realizar pruebas con distintos materiales, a fin de conseguir la mezcla de hormigón más adecuada. “De esta forma -explicaron los encargados de la obra- hicimos una matriz con cemento y aditivos que arrojó cerca de 15 hormigones de prueba y, finalmente, en función de la resistencia y la absorción de energía, nos decidimos por el que se comportó de mejor manera”.
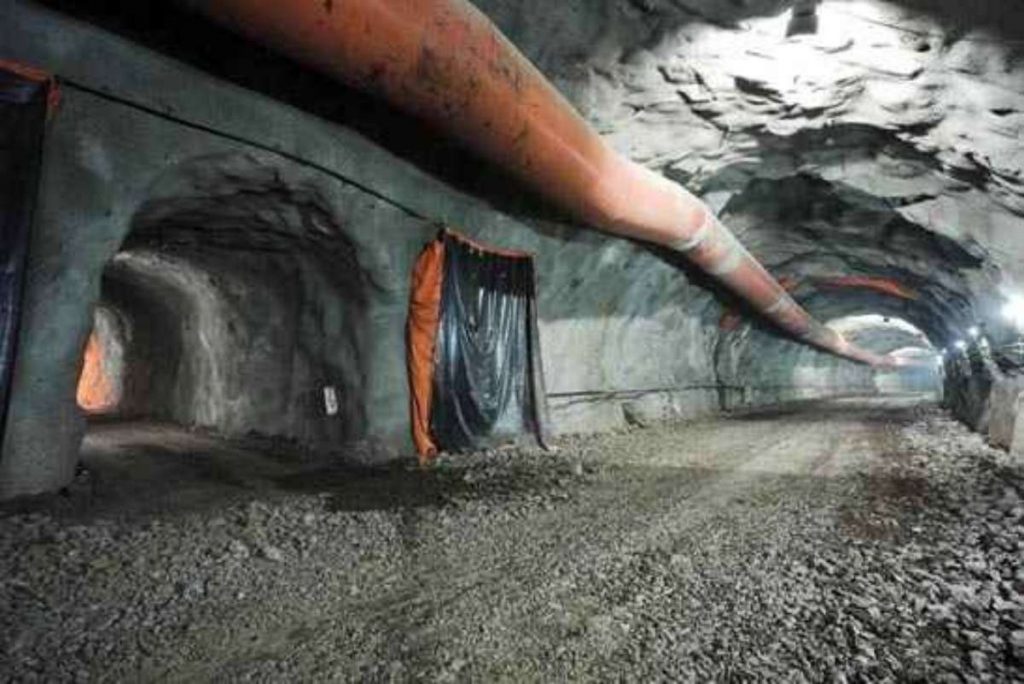
A nivel de shotcrete, la obra utilizó dos tipos de mezcla, una para sostenimiento y otra para revestimiento. En el caso de la primera, se debió enfrentar siete pasos de avance distinto, desde la roca de mejor calidad, que permitió avances de cuatro metros y medio; hasta la de menor calidad, donde sólo se pudo llegar a los 50 centímetros, antes de aplicar shotcrete de sostenimiento.
En relación a los espesores del shotcrete, éstos fueron variando en función de las condiciones del terreno, alcanzando espesores de hasta 30 centímetros como máximo.
En general, el recorrido del Túnel se caracterizó por presentar un muy buen terreno, pero con una serie de sectores con fallas intermedias, que fueron lo más complicado de tratar a nivel del shotcrete. En estos sectores de falla se aplicó un esqueleto de perfiles metálicos TH90, distanciados en espacios que van de los 50 centímetros al metro y medio como máximo, luego de lo cual se aplicó el shotcrete. Esta solución se utilizó eminentemente en el sector sur de la obra, donde se presentó material coluvial y donde el avance fue mucho más lento.
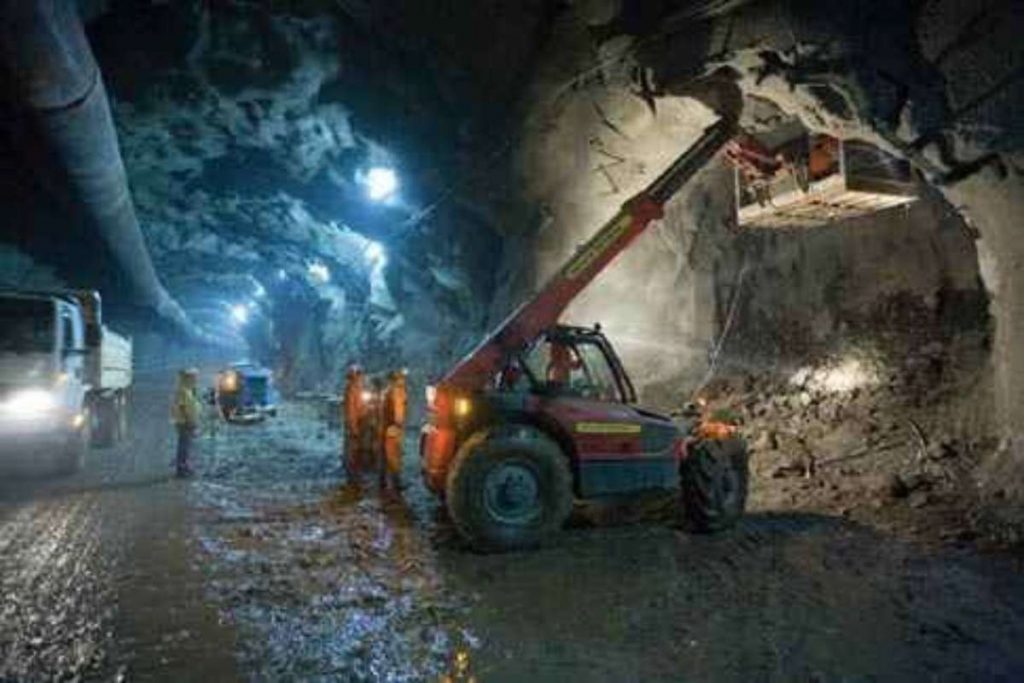
Para la mezcla del shotcrete de sostenimiento se utilizó cemento puzolánico, grado alta resistencia, de acuerdo a la norma NCh 148. Junto con ello, también se usaron dos tipos de áridos, uno con un tamaño máximo de 10 mm. y otro corrector fino, el cual se usó en una proporción de un 8.7%. El agua fue eminentemente potable y cumplió con los requisitos de la norma NCh 1498.
Sobre el plastificante, se utilizó un aditivo reductor de agua y retardante de fraguado, que mantiene la trabajabilidad de la mezcla hasta el momento de la proyección y en el caso del superplastificante, se utilizó un aditivo de alto rango, capaz de elevar la trabajabilidad del hormigón proyectado desde un cono de 4cm al deseado para una buena proyección (en torno a los 20 cm), que incorpora tecnología nanosílice y está diseñado para obtener hormigón de alta resistencia.
El acelerante de fraguado correspondió a un aditivo libre álcalis, que produce en el hormigón proyectado un rápido fraguado y una elevada velocidad de endurecimiento. Por último, como ya hemos mencionado, se usó una fibra de polipropileno de alto performance, con capacidad de reforzar el hormigón proyectado, otorgándole tenacidad y ductilidad.
Por su parte, para el caso del hormigón proyectado para revestimiento, la mezcla tuvo componentes similares a la anterior, pero en este caso la arena correctora fina se adicionó en una proporción de 3.1%; además, se utilizó microfibra de polipropileno, que corresponde a una fibra sintética multifilamento de polipropileno virgen de 12 mm. de largo, que reduce la fisuración por retracción y asentamiento plástico, y permite mitigar el efecto explosivo del hormigón proyectado producido durante un incendio.
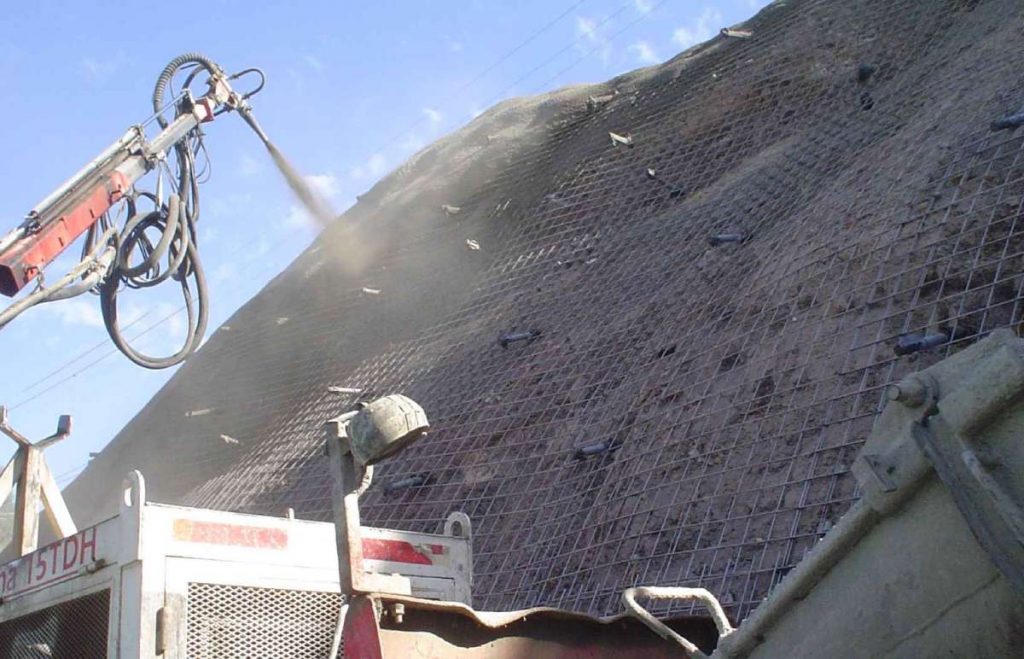
Para la provisión del shotcrete, se instalaron dos plantas de hormigonado, una en el sector de Providencia y otra en el sector de El Salto, que permitieron suministrar en obra el material que se necesitaba, con la regularidad requerida. “Esta opción de tener plantas propias –junto con nuestras propias bombas- nos permitió manejar los tiempos en función de las necesidades del proyecto y manejar también los ritmos de producción. Además de esto, para nosotros era fundamental contar con la mejor tecnología de los materiales al interior de la obra”, comentaron. Junto con esto, se utilizaron tres robots de colocación de shotcrete, uno por cada frente y otro en calidad de stand by en caso de fallas, que aplicaron el shotcrete por vía húmeda.
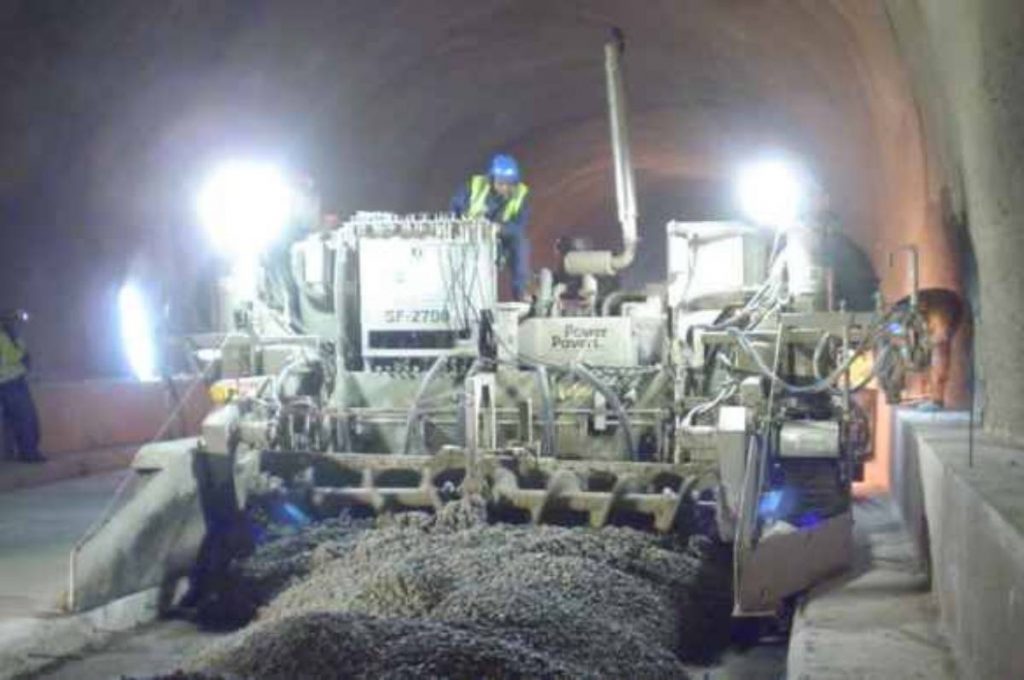
En términos de resistencia del shotcrete, ésta se fue controlando con muestras que se estudiaron en un laboratorio instalado en obra. En un principio, explicaron desde la constructora, se comenzó conservadoramente con un contenido de cemento de 410 kg/m3, lo que luego de unos siete meses de trabajo bajó a 390 kg/m3, los que mantuvieron perfectamente la resistencia que se esperaba, albanzando niveles promedio de cerca de 40 MPa, con índices que siempre estuvieron por sobre los 30 MPa.
Otros usos para el hormigón
Otra área importante donde se utilizó hormigón fue en la construcción de contrabóvedas, una especie de viga invertida, ubicada en la parte inferior del túnel, cuyo objetivo era apuntalar la abertura. Dichas contrabóvedas se construyeron continuamente en los sectores de roca de menor calidad, en zonas que fueron determinadas de acuerdo con la clasificación de rocas que constantemente realizaba el geólogo de la obra.
Para el caso del pavimento, se trabajó con un proveedor local de hormigón, con una alta resistencia (4,8 MPa a la flexotracción) y barras de amarre que fueron instaladas al término de cada jornada. Se utilizó además tren pavimentador, lo que permitió terminar en 10 días las dos pistas de un sentido del Túnel, con un intermedio de un mes para abordar la obra vial; para luego, en otros 10 días, las otras dos pistas del otro sentido. Por su parte, el espaciamiento de las losas fue de 3,5 cms.
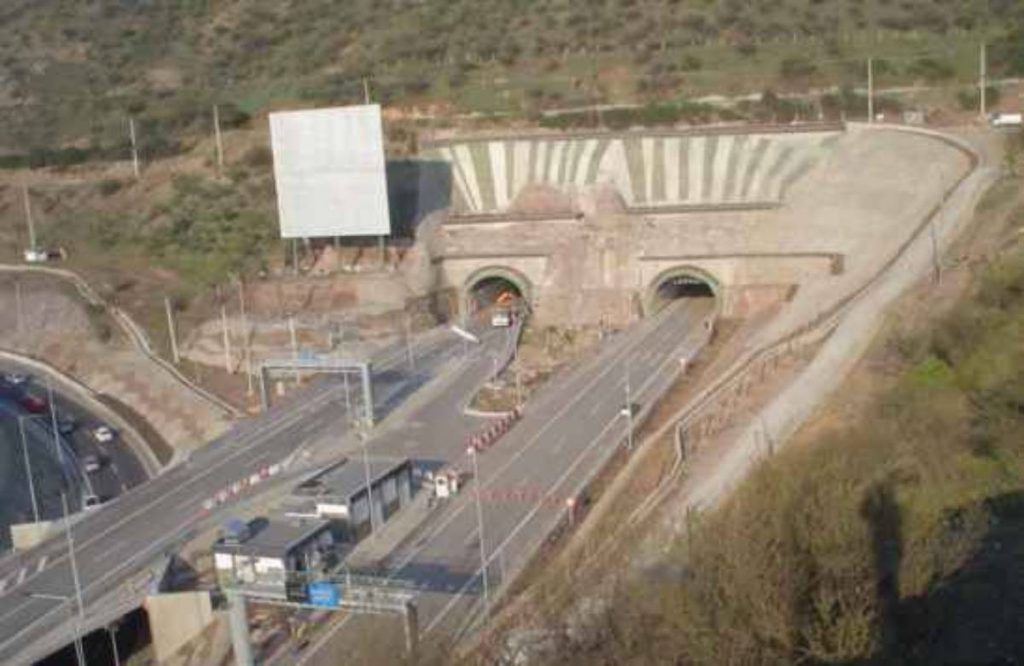
Inaugurado el año 2008, el Túnel San Cristóbal se encuentra en pleno funcionamiento, para todo horario y en ambos sentidos, generando beneficios que no sólo implican considerables disminuciones en los tiempos de traslado, sino también mejoras en la conectividad urbana, descongestión de la ciudad y ahorro de combustible; aportando a la descontaminación ambiental y la mejor calidad de vida de millones de personas.