Introducción
Los aditivos son productos químicos añadidos al cemento, mortero o concreto, para modificar una o más propiedades de las mezclas cementantes. Las dosis de los aditivos químicos normalmente varían entre el 0,05% y el 5% de la masa de ligante (cemento). Los aditivos químicos hoy son parte integral de mezclas cementadas debido a las diversas ventajas que proporcionan a sus propiedades de ingeniería en los estados fresco y endurecido. El incremento de dosis de los aditivos incrementa la fluidez de la mezcla, como lo ilustrado en la Figura 1.

El uso de aditivos químicos permite la producción de materiales cementantes para una amplia variedad de aplicaciones, desde mezclas con consistencia seca hasta concreto auto-compactante. Los aditivos químicos se clasifican de acuerdo con la función que ejercen, como: incorporadores de aire, reductores de agua, retardadores de fraguado, modificadores de comportamiento reológico, inhibidores de la corrosión, reductores de retracción, reductores de permeabilidad, inhibidores de la reacción de álcali-sílice, pigmentos, y otros de funciones variadas, tales como agentes de adhesión, agentes de formación de gas, agentes de cohesión, agentes de bombeo y agentes espumosos, entre otros.
Histórico
El empleo de aditivos en concretos y morteros es tan antiguo como el propio cemento u otros aglomerantes hidráulicos. Según COUTINHO (1997), los romanos añadían clara de huevo, sangre, manteca o leche a concretos y morteros rudimentarios para mejorar la trabajabilidad de las mezclas. Más recientemente, a finales del siglo XIX, con la invención del cemento Portland, la función de los aditivos químicos lentamente evolucionó debido a su beneficio a la trabajabilidad y durabilidad de mezclas cementadas. Actualmente, en muchos países, prácticamente todos los sistemas cementosos producidos industrialmente contienen algún tipo de aditivo químico.
El desarrollo de aditivos específicos para la modificación de las propiedades reológicas de las mezclas a base de cemento Portland data de principios de la década de 1930. La primera patente para el uso de un aditivo plastificante a base de lignosulfonato se obtuvo en Inglaterra a principios del siglo XX. La primera patente que contempló la fabricación y la utilización de superplastificantes a base de naftaleno sulfonato fue aprobada en los Estados Unidos en 1938 (AÏTCIN, 1998). El primer aditivo químico sintético fue utilizado en 1930 en los Estados Unidos, y consistió en un dispersante para negro de humo para aplicación de una pigmentación uniforme en un pavimento de concreto. Los aditivos incorporadores de aire comenzaron a ser desarrollados a partir de investigaciones en pavimentos de concreto en los Estados Unidos, donde existían problemas de durabilidad debidos a ciclos congelación-deshielo. El descubrimiento surgió a partir del uso de un agente de molienda que contenía surfactantes para la producción de cemento, que resulto en burbujas de aire en el concreto, como se muestra en la Figura 2.
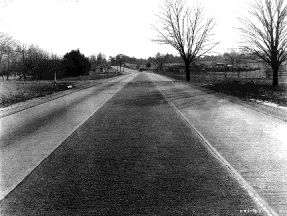
Los lignosulfonatos, que son un residuo industrial de la producción de pulpa de celulosa, fueron los primeros aditivos reductores de agua o plastificantes comerciales introducidos a principios de la década de 1960. En aquella época, esos aditivos contenían altos contenidos de azúcar en su composición, lo que generaba gran retardo de fraguado e incorporación de aire en los concretos. Actualmente, estos aditivos son sometidos a procesos de purificación para remoción de esos azúcares por medio de ultrafiltración, tratamiento térmico con pH controlado e incluso fermentación. Estos tratamientos reducen de forma significativa los efectos secundarios en los tiempos de fraguado, el modo de repulsión de los aditivos lignosulfonato es por acción electrostática, como se ve en la Figura 3.
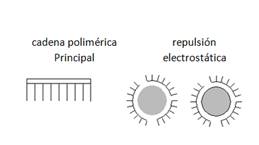
Los reductores de agua (WR) de eficiencia normal y alta (plastificantes y superplastificantes), que tienen requisitos de desempeño definidos, tienen otra clasificación comercial de plastificantes conocidos como reductores de agua de media eficiencia o polifuncionales (Mid Range Water Reducer – MRWR). Esta categoría de aditivos típicamente permite una reducción de agua entre 5% y 18% para una determinada consistencia del concreto. Tales aditivos son los más utilizados actualmente en centrales dosificadoras de concreto, pues las dosificaciones pueden ser alteradas sin impacto importante en los tiempos de fraguado de acuerdo con el revenimiento o reducción de agua requerida.
Las investigaciones realizadas a principios de la década de 1960 en Japón y Alemania llevaron al desarrollo de los superplastificantes, que pueden proporcionar una gran reducción de agua (hasta un 40%) o gran fluidez al concreto (baja tensión de fluencia y baja viscosidad plástica). En Japón, los aditivos a base de naftaleno sulfonato formaldehído condensado (NSFC) se comercializaron en 1964, resultando en una mayor reducción de agua y, por lo tanto, en concreto con mayor resistencia. Los aditivos a base de NSFC vienen, desde entonces, siendo utilizados en gran cantidad por la industria de concreto mundial (MALHOTRA, 1989). En la Figura 4 se ve los monómeros de melamina sulfonato y naftaleno sulfonato.
Los condensados de formaldehído-sulfonatos de naftaleno (NSFC) y melamina (MSFC) fueron los primeros tipos de aditivos superplastificantes, y resultaron en una mejora importante en la durabilidad del concreto por haber permitido la producción y el lanzamiento de concretos con baja relación agua / cemento menor que 0,40). Tales tecnologías fueron adoptadas por la industria del concreto con aceptación relativamente alta.
Figura 4: a) Monómero de la melamina sulfonato b) Monómero del naftaleno sulfonato (Rixan, 1999)
A finales de la década de 1980, una nueva familia de superplastificantes a base de poliéteres de policarboxilatopoliéteres (PCE) fue desarrollada en Japón. Los PCEs, por ser diseñados para aplicaciones específicas, se convirtieron en la tecnología dominante de superplastificantes para concreto. A partir de la década de 1990, los policarboxilatos-poliéteres se convirtieron en una importante tecnología de superplastificantes, a menudo sustituyendo el NSFC y el MSFC en muchas aplicaciones. La norma ABNT NBR 11768: 2011 clasifica estos aditivos en superplastificantes tipo II (SP II).
La estructura química genérica de los PCEs se muestra en la Figura 5. La diferencia de los polímeros NSFC y MSFC, es que la estructura del PCE puede presentarse de varias maneras diferentes dependiendo de la aplicación. Las propiedades de los PCEs se determinan por parámetros moleculares, tales como la longitud de la cadena molecular, y la frecuencia, tamaño y composición de las cadenas laterales anexadas a la cadena principal. Algunos PCEs contienen ambos grupos carboxilato y sulfonato (SO3). La dispersión y la defloculación de las partículas de cemento pueden ser controladas por el cambio de la longitud de esas cadenas y por el cambio de la longitud de la cadena central de estos polímeros.
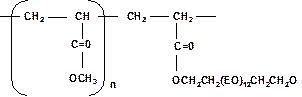
Los superplastificantes del tipo PCE son conocidos por proporcionar un mejor mantenimiento de la trabajabilidad y por ser más previsibles en cuanto al efecto sobre los tiempos de fraguado, en comparación con los aditivos de base NSFC y MSFC.
Las diferentes moléculas de aditivos dispersantes causan diferentes efectos de dispersión y dependen del tipo de cemento. Los aditivos basados en policarboxilatos son más eficientes que los basados en naftaleno sulfonatos, que a su vez son más eficientes que los aditivos basados en lignosulfonatos, como se muestra en la Figura 6, en una representación esquemática de pruebas de revenimiento.
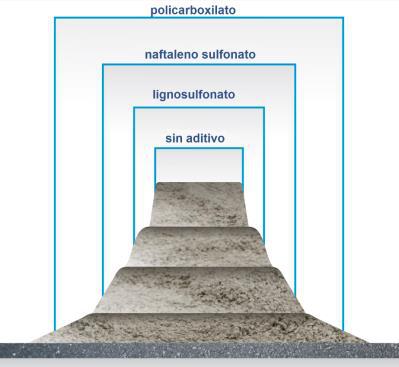
Las partículas de cemento tienen una tendencia natural a aglomerarse cuando se mezclan con agua debido a su polaridad y la fuerza de atracción de Van Der Waals entre estas partículas de cemento. El agua queda atrapada entre ellos, lo que reduce la fluidez/ tensión de fluencia del hormigón (Uchikawa, 1997). Los aditivos confieren varios efectos al concreto, la cadena principal del policarboxilato se deposita / adsorbe en la superficie de las partículas del cemento, mientras que las cadenas laterales se extienden desde la superficie, separando las partículas lo que reduce las fuerzas interparticulares responsables por la tensión de fluencia del concreto o de la pasta. El aditivo causa una repulsión estérica entre las partículas de cemento, una barrera física junto con un efecto de fuerzas repulsivas que resulta en la dispersión de las partículas y libera agua para fluidificar la mezcla, como se demuestra en la Figura 7 (Jolicoeur y Simard, 1998). Los superplastificantes interactúan en la superficie o se combinan químicamente con las fases de cemento o los componentes de cemento hidratado (Ramachadran, 1995).
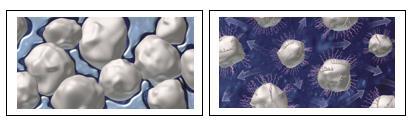
Otro de los grandes avances de la tecnología del concreto fue el desarrollo de aditivos incorporadores de aire a finales de la década de 1930. De acuerdo con la ABNT NBR 11768: 2011, los aditivos incorporadores de aire se clasifican como IA y se utilizan intencionalmente para introducir, en morteros y concretos, un sistema de burbujas de aire microscópico que sea estable y uniforme. Los materiales a base de cemento con una adecuada incorporación de aire presentan una resistencia mayor al deterioro causada por ciclos hielo-deshielo, en el estado fresco, los incorporadores de aire pueden mejorar el comportamiento reológico del concreto de forma significativa en mezclas con bajo consumo de cemento (menos de 300 kg / m³) o en diseños que contengan agregados de graduación pobre y falta de finos. Los incorporadores de aire, en estos casos, pueden mejorar la trabajabilidad del concreto en lo que se refiere al revenimiento y a la fluidez, pueden aumentar la cohesión de la mezcla y reducir la segregación, y pueden reducir la exudación. Además, otras propiedades del concreto se mejoran con la incorporación de aire, como el rendimiento térmico y acústico que se obtienen cuando se obtiene una incorporación de aire suficiente.
Todos los aditivos incorporadores de aire son agentes tensoactivos (o surfactantes), lo que significa que estos materiales poseen grupos hidrofóbicos (“hidrocarburo” no polar) e hidrofílicos (“aniónico” polar). Cuando se agregan a morteros y concretos durante el proceso de mezcla, estos agentes se concentran en la interfaz de agua y reducen la tensión superficial, promoviendo la formación y estabilización de burbujas de aire microscópicas por la formación de micelas (es una estructura globular formada por un agregado de moléculas anfipáticas, es decir, compuestos que tienen características polares y apolares simultáneamente, dispersas en un líquido que constituye una de las fases de un coloide) para formación de la burbuja de aire, como ilustrado en la Figura 8.
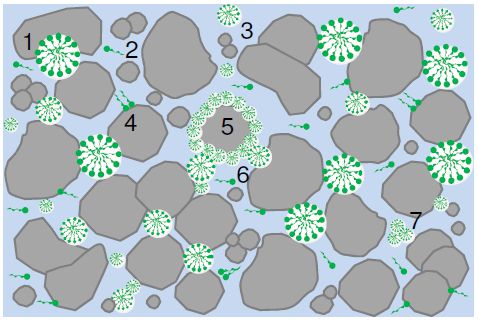
- Anclaje de las micelas de Incorporador de aire (IA) en las partículas de cemento en suspensión.
- IA libres, sin formarse micelas.
- Micelas libres en la pasta (sin anclaje).
- IA ancladas en la partícula de cemento
- Micelas alrededor de las partículas de cemento.
- Micelas ancladas.
- Micelas libres.
Figura 8: Ilustración del efecto del uso de incorporador de aire en la pasta de cemento (Romano, 2013)
En el año de 2018, después de más de 5 años de estudios, fue lanzado una nueva clase de aditivos para una nueva clase de concretos fluidos llamado de Concreto de Fluidez Controlada. Ese nuevo concreto utiliza diseños de mezcla de concreto convencional, con menor contenido de finos (que los concretos autocompactantes) y permite el uso de agregados más grandes, reduciendo aún más los costos de materiales. El aditivo especial para esos concretos, es un tipo de policarboxilato con efecto modificador de viscosidad que permite llevar el concreto convencional a concreto fluido sin presentar segregación como lo ilustrado en la Figura 9.
Figura 9: a) Concreto con diseño convencional con aditivo reductor de agua base lignosulfonato. b) Concreto con diseño convencional con el nuevo aditivo policarboxilato con efecto moderador de viscosidad desarrollado en 2018.
Además de los aditivos dispersantes y policarboxilatos modificadores de viscosidad, también se desarrolló recién una nueva familia de aditivos que son conocidos como lubricantes para agregados. Son polímeros que se adhieren en la superficie de los agregados (arena y piedra), de manera que al recubrir la superficie rugosa del agregado, se reduce la fricción interna del concreto durante el bombeo. Una representación de la lubricación de los agregados por los aditivos lubricantes se visualiza en la Figura 10.
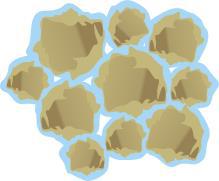
El uso de los lubricantes de agregados, permite que el concreto tenga una reducción de la presión de bombeo, sin afectar la viscosidad del agua, eso permite que la mezcla contenga mayor cantidad de finos con baja viscosidad durante el bombeo, además permite implementar el uso de agregados angulares sin cambiar o con poco cambio en el diseño de mezcla original. Los agregados ocupan el mayor volumen del concreto y, cuanto más angular es mayor la cantidad necesaria de pasta para lubricarlos, siendo así mayor el costo del concreto.
Referencias
(1) AÏTCIN, P. C. High performance concrete. London: E&FN SPON, 1998, 569p.
(2)COUTINHO, A. de S., Fabrico e propriedades do betão. Lisboa: LNEC editora. v.1. 1997. 610p.
(3) MALHOTRA V.M, Ed. International conference of superplasticizers nd other chemical admixtures in concrete.Proceedings. Ottawa, 1989. p.1-18.
(4)YAMADA, K., et al. Effects of the chemical structure on the properties of polycarboxylate-type superplasticizer. Cement and Concrete Research, v. 30, 2000, p. 197-207.
(5)ROMANO,R.C.O , Incorporação de ar em materiais cimentícios aplicados em Contrução Civil. Universidade de São Paulo, 2013. p. 44.
(6)Jolicoeur, C., Simard, M-A., Chemical admixture-cement interactions: Phenomenology and physico-chemical concepts. Cement and Concrete Research, 1998.
(7)Ramachadran,V.S.; Concrete. Admixtures Handbook, Properties, Science and Technology.Institute of Research in Construction National Research Council Canadá, Ottawa. 2nd edition.
(8)Uchikawa,H., Hanchara,S.; Sawaki,D.; The role of steric repulsive force in the dispersion of cement particles in fresh paste prepared with organic admixture. Cement and Concrete Research, Vol27,1997.
(9)Romano, R. C. O., Pileggi, R. G.; Use of rheological models for the evaluation of cement pastes with air-entraining agent in different temperatures. In: 26th Nordic Rheology Society, v. 25. p. 341-348. Copenhagen (2017).
(10)Rixon, R., Mailvaganam, N., Chemical admixtures for concrete. London: E&FN SPON, 3rd edition. 1999.
(11)Lyra, J.S., Romano R.C.O., Pillegi, R.G., Golvea,D.; Consolidação de pastas cimentícias contendo policarboxilatos um estudo calorimétrico e reológico. Associação Brasileira de Cerâmica, ano LVIII – vol. 58, 346 . 2012.