El hormigón con agregado reciclado contribuye al desarrollo de una industria del hormigón más ecoeficiente. Los agregados gruesos reciclados no afectan sensiblemente a la resistencia a compresión del hormigón, pero su mayor porosidad genera dudas sobre su capacidad para resistir la carbonatación. El presente artículo discute la resistencia a la carbonatación del hormigón con agregados reciclados. En este sentido, deben valorarse tanto la porosidad como la reserva alcalina del material. En ambos aspectos, el mortero adherido en las partículas del agregado juega un papel fundamental, modificando la velocidad de carbonatación.
Autores: Yuri Villagrán Zacardi (Doctor, Investigador FWOMSCA- SoE, Magnel-Vandepitte Laboratory for Structural Engineering and Construction Materials, Ghent University, Bélgica; e Investigador CONICET, Argentina. yury.villagranzaccardi@ugent.be), Carlos Pico Cortés (Ingeniero, Becario Doctoral del Consejo Nacional de Investigaciones Científicas y Técnicas, Laboratorio de Entrenamiento Multidisciplinario para la Investigación Tecnológica, Argentina. carlospicocortes@conicet.gov.ar), Claudio Zega (Doctor, Investigador del Consejo Nacional de Investigaciones Científicas y Técnicas, Laboratorio de Entrenamiento Multidisciplinario para la Investigación Tecnológica, Argentina. cj.zega@conicet.gov.ar).
Fuente: FICEM
Introducción
La economía circular emergente exige un uso extensivo del hormigón con agregado reciclado o simplemente hormigón reciclado (HR), para disminuir el consumo de recursos no renovables. En general, mejorar el reciclaje de residuos de construcción y demolición que puede representar hasta el 25-30% de toda la generación de residuos, es una medida esencial hacia una industria del hormigón ecoeficiente. Las condiciones geográficas juegan un papel importante en la justificación y competitividad de agregados reciclados (AR), siendo en muchos casos altamente prioritarios debido a la escasez de agregados naturales. Los efectos de los AR sobre la resistencia mecánica son relativamente menores y han sido resueltos tecnológicamente [1–3]. La normativa se encuentra en vías de adaptación, aceptando en muchos casos contenidos de hasta un 30 % de agregado grueso reciclado cuando no existen requerimientos significativos de durabilidad.
Sin embargo, el mero uso de agregados reciclados no es suficiente para conseguir una industria ecoeficiente. Las estructuras de hormigón sostenibles solo se pueden lograr combinando el reciclaje del hormigón de desecho con una vida útil extendida y con niveles aceptables de emisión de gases de efecto invernadero y de consumo de energía (Figura 1). La estrategia combinada de estas tres líneas de acción permite optimizar el ciclo de vida de las estructuras de hormigón y reduce el consumo de recursos vírgenes, así como el vertido de residuos e impacto ambiental.
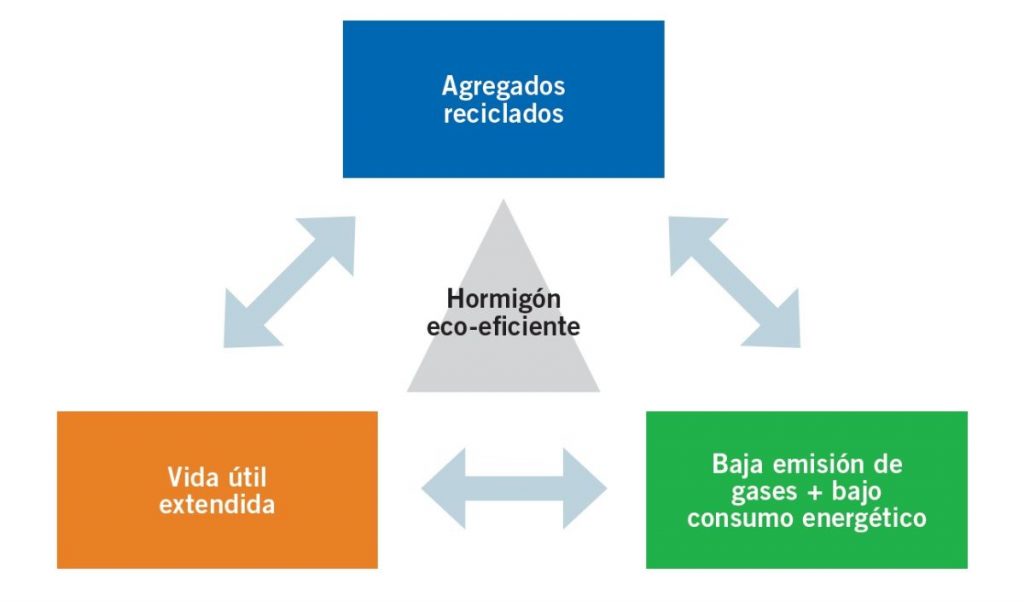
La predicción integrada de la durabilidad del HR es un tema sobresaliente que la investigación está abordando de manera inherente. Las brechas de conocimiento para el AR, como su procesamiento, mejora eficiente, secuestro de carbono, evolución de la microestructura y modelos de transporte, son aspectos que tendrán gran impacto en las estructuras venideras en el futuro cercano.
Un proceso que afecta el desempeño del hormigón con agregados reciclados en estos sentidos es la carbonatación. Los factores importantes por considerar son: la velocidad de carbonatación, caída del pH, la densificación de la estructura de poro y la captura de CO2 atmosférico (Figura 2). A pesar de las propiedades de transporte inferiores, la corrosión en las estructuras de HR aún podría prevenirse hasta por 100 años [4]. La confirmación precisa de la vida útil de estructuras elaboradas con AR solo puede provenir de modelos calibrados que incorporen los efectos del AR sobre la velocidad de carbonatación y la captura de carbono.
Investigaciones recientes han hecho avances en las tres líneas estratégicas. El objetivo principal de las mismas es el de asegurar y cuantificar la durabilidad y la ecoeficiencia de las estructuras.
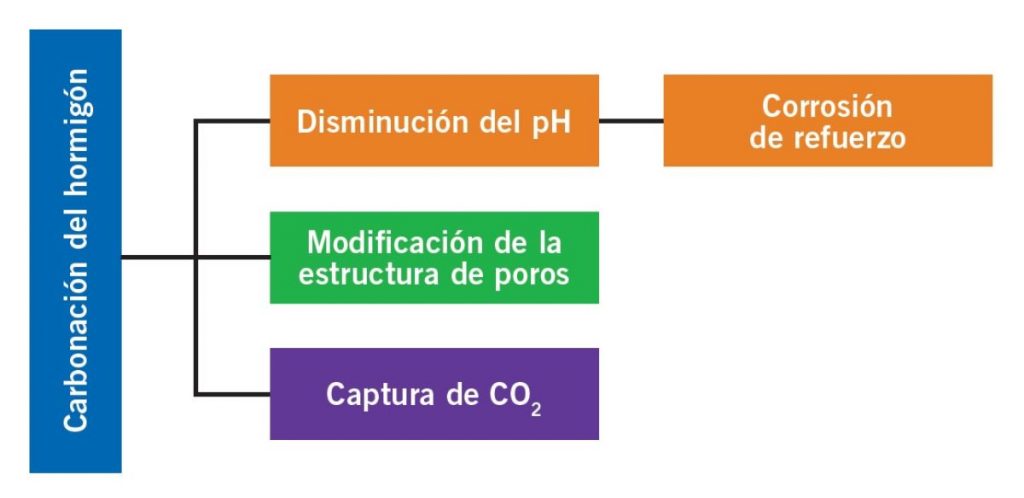
Consideraciones respecto a las propiedades del AR
La porosidad del HR dificulta su aplicación en ambientes urbanos e industriales debido a la velocidad de carbonatación más rápida que puede provocarse. Aunque el HR puede tener propiedades de transporte de agua suficientemente bajas con hasta un 75% de AR [5], se ha informado una mayor tasa de carbonatación [4,6-7]. La predicción de la velocidad de carbonatación a partir de las propiedades del HR no es, en general, suficientemente confiable por estas razones. Entre las propiedades del hormigón que mejor describen la tendencia a la carbonatación, la velocidad de succión capilar se presenta como una de las más adecuadas (Figura 3). Algunas investigaciones sugieren una capacidad compensatoria de la porosidad, mediante otras características del AR como su contenido de mortero adherido [8]. Este puede proveer una reserva alcalina adicional y aumentar la capacidad de captura de carbono en comparación con los agregados naturales.
Existen variaciones importantes en la literatura respecto al desempeño del agregado reciclado frente a la carbonatación. En general, se considera al AR como un material con características determinadas, mientras que pasa desapercibida la influencia de las propiedades del hormigón de desecho que le dio origen [10]. Más aún, el procesamiento avanzado y la gestión de los residuos de construcción y demolición pueden retener mayor o menor valor de los diversos tipos de flujo de desechos. Se ha demostrado que el proceso de trituración y clasificación tiene un impacto significativo en las propiedades de los agregados [11,12]. También el comportamiento por carbonatación de AR con trituración primaria versus AR con trituración secundaria es diferente, observándose una reducción de la velocidad de carbonatación de hasta 18% para el segundo grupo principalmente asociada a un menor contenido de mortero adherido en el AR [13]. Los marcadores de calidad importantes como la liberación de partículas (recuperación masiva de las fases más densas), la densidad, la distribución del tamaño y la forma pueden mejorarse mediante un procesamiento avanzado.
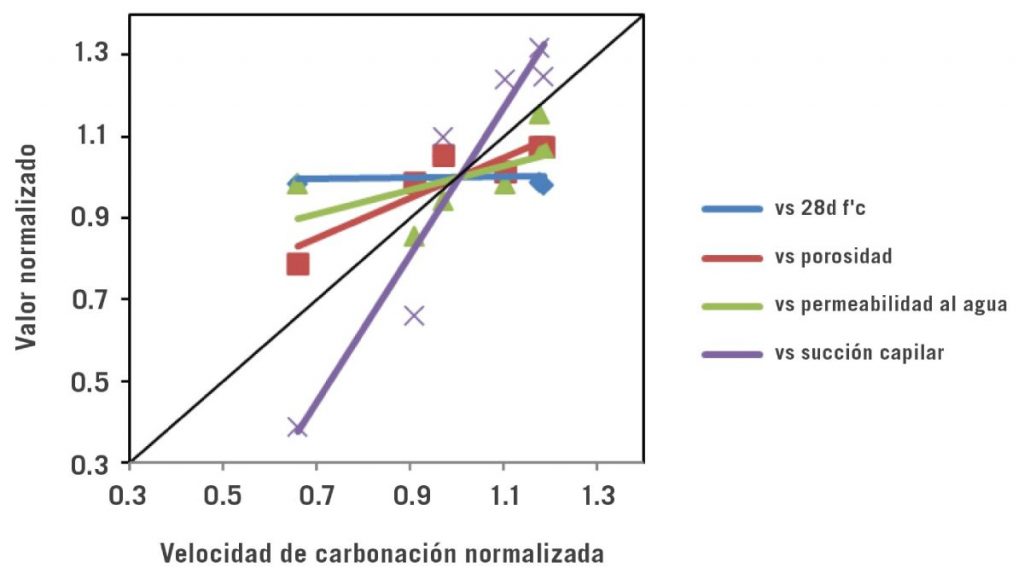
Zona de transición interfacial
Por otra parte, al ser el AR un material multifásico, introduce zonas de transición interfacial adicional (ZTI), que aumentan la sensibilidad en términos de propiedades de transporte. La ZTI en el HR ha sido principalmente descripta por nanoindentación y microscopía [14–16], pero aún no ha sido relacionada con el desempeño de durabilidad.
Esto implica una consideración importante del agregado reciclado en cuanto a su forma y textura. Ello debe ser analizado cuantitativamente cuando se lo compara con agregados naturales de trituración o con grava natural. En cuanto a la textura, la grava natural tiene una superficie externa más lisa y por lo tanto genera una ZTI con menos tortuosidad que el agregado reciclado. Ello es relevante porque el transporte de CO2 se facilita a través de esta zona [14]. Con la creación de superficies rugosas y con mayor tortuosidad, se mejora la transferencia mecánica, pero también se disminuye la velocidad de transporte en la ZTI. En cuanto a la forma, agregados reciclados tratados con un proceso secundario de trituración resultan en formas más redondeadas que contribuyen a la trabajabilidad de la mezcla en estado fresco. Ello permitiría disminuir el contenido unitario de agua en la mezcla y mejorar el desempeño frente a la carbonatación [2].
Otro aspecto importante de los agregados reciclados que afecta a la ZTI es la porosidad aportada por el mortero adherido. Cuando los agregados son utilizados en estado insaturado, los mismos absorben agua de la mezcla. Esto genera un transporte de agua y de finos hacia los poros del mortero adherido. De esta forma, la microestructura de la zona de interfase es prácticamente continua con la de la matriz (Figura 4). Esta práctica es habitual en la producción de hormigón, teniendo la precaución de incrementar el contenido de agua de la mezcla en una cantidad equivalente a la que absorberá el agregado. Si los agregados se incorporan en el hormigón ya en estado saturado, entonces esta situación no se produce y la ZTI entre mortero adherido y la nueva matriz puede ser más porosa que en el caso que los AR se incorporan secos.
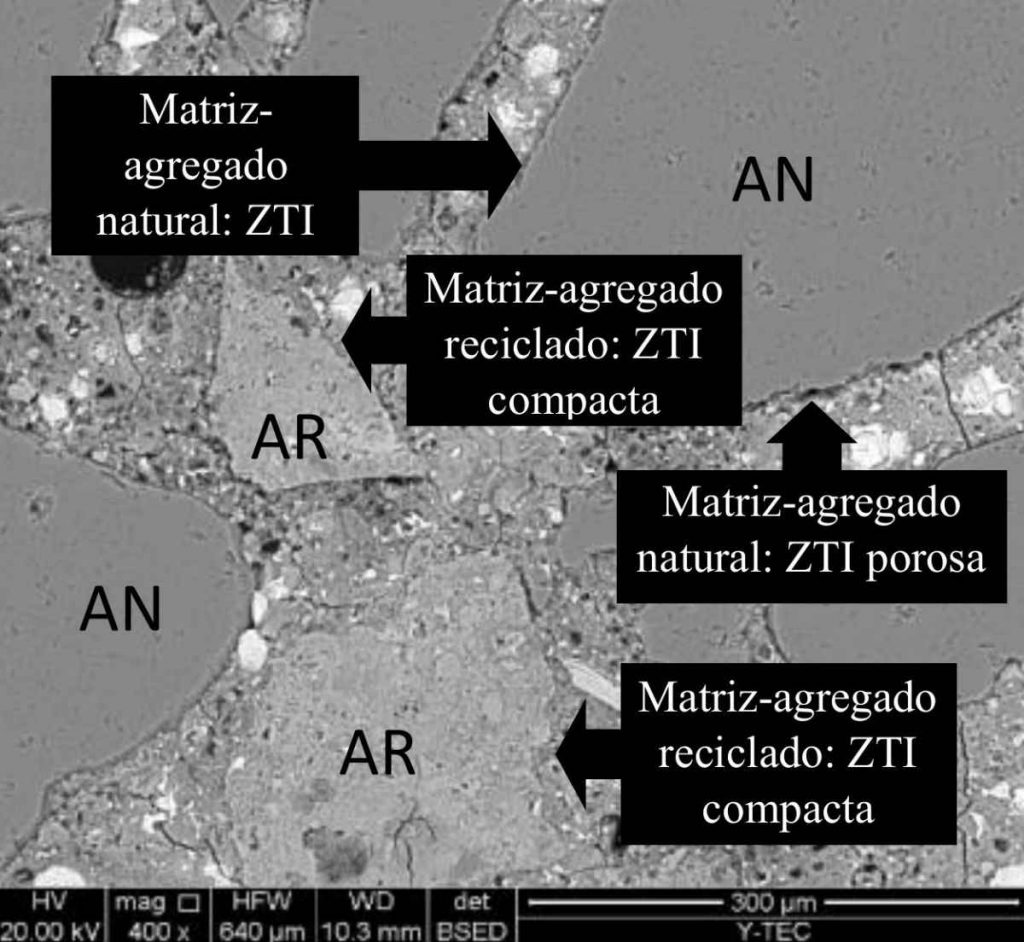
Captura de carbono y efectos sobre el análisis de ciclo de vida
El análisis de ciclo de vida (ACV) puede establecer el perfil ecológico de HR con un grado variable de complejidad. El ACV contempla como entrada todos los requerimientos de recursos y energía del producto y su proceso, para determinar el impacto ambiental mediante distintos indicadores de la unidad funcional. Naturalmente, el método es muy sensible a las condiciones locales. Aunque existen bases de datos disponibles que permiten hacer estimaciones, aún se necesitan inventarios más específicos y locales para una evaluación precisa. La contribución a la huella de carbono de las distancias y los modos de transporte es una de las condiciones locales más obvias que se pasan por alto. El agregado reciclado se encuentra en una zona más cercana a las zonas de consumo que la mayoría de los agregados naturales. La minería urbana puede contribuir a la ecoeficiencia cuando el transporte de agregados es limitado. Los aspectos logísticos ciertamente pueden pesar más que los impactos de los componentes del HR, como una ventaja potencial sobre el concreto convencional. Otras consideraciones para realizarse tienen que ver con la vida en servicio y el fin de vida del hormigón.
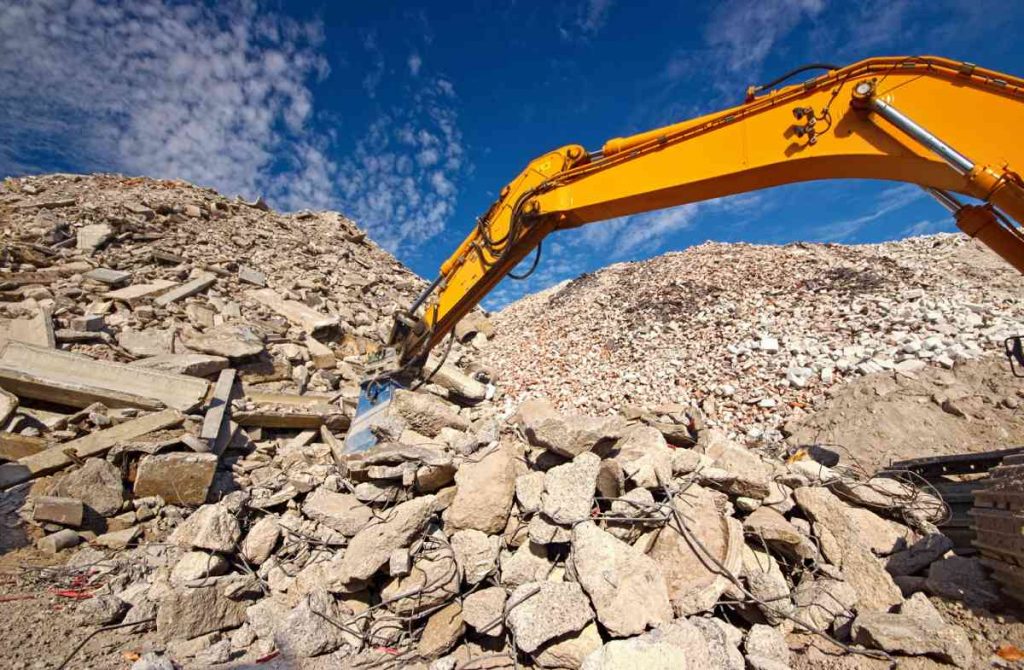
La carbonatación del hormigón como proceso natural, captura CO2 de la atmósfera. La cantidad de CO2 capturado nunca será mayor al CO2 emitido durante la producción, pero significa ciertamente un atenuante significativo del potencial de calentamiento global del hormigón. Estimaciones muestran que entre un 40 % y 70 % de la emisión química de CO2 durante la producción del cemento es recapturada durante la carbonatación [18-20]. Esta captura no es completa principalmente debido a que parte del óxido de calcio se encuentra retenido en el silicato de calcio hidratado y este no se carbonata con la misma facilidad que el hidróxido de calcio. El uso de adiciones minerales también consume parte de este hidróxido de calcio y disminuye la reserva alcalina que tiene el hormigón y por lo tanto su capacidad de captura de CO2.
Es importante diferenciar entre el grado de carbonatación y la velocidad de carbonatación. Ambos definen la capacidad de captura de CO2 del hormigón. Mientras que el grado de carbonatación depende de las condiciones químicas, la velocidad de carbonatación queda definida mayormente por la estructura de poro. Entonces, en hormigones sin armaduras de acero, resulta conveniente contar con una carbonatación rápida para disminuir el impacto ambiental del hormigón. Solamente en aquellos casos en que es importante proteger a las armaduras resulta beneficioso prevenir la carbonatación para que las armaduras se mantengan protegidas por el medio alcalino. El diseño de hormigones más carbonatables para estructuras sin armadura o en ambientes secos, es un factor a considerar en investigaciones futuras. Actualmente una mayor velocidad de carbonatación está asociad con un menor nivel resistente. El desacoplamiento entre estas dos propiedades supone un nuevo desafío en términos de sostenibilidad.
En términos de velocidad de carbonatación, los AR suponen una ventaja independientemente de su aprovechamiento en la fabricación de nuevos hormigones. La trituración del material supone un incremento de la superficie específica en contacto con el medio externo. A partir de ello, la captura de CO2 se acelera debido a esta mayor exposición (Figura 5). Tal contribución se produce desde el momento en que el AR es triturado y acopiado, produciéndose un beneficio con mayor captura de CO2 [21]. Una estimación genérica muestra que el volumen de hormigón carbonatado se duplica con la trituración. El ACV permite considerar tales contribuciones de las nuevas estructuras de hormigón incluso con procesos que suceden al fin de la vida de la estructura.
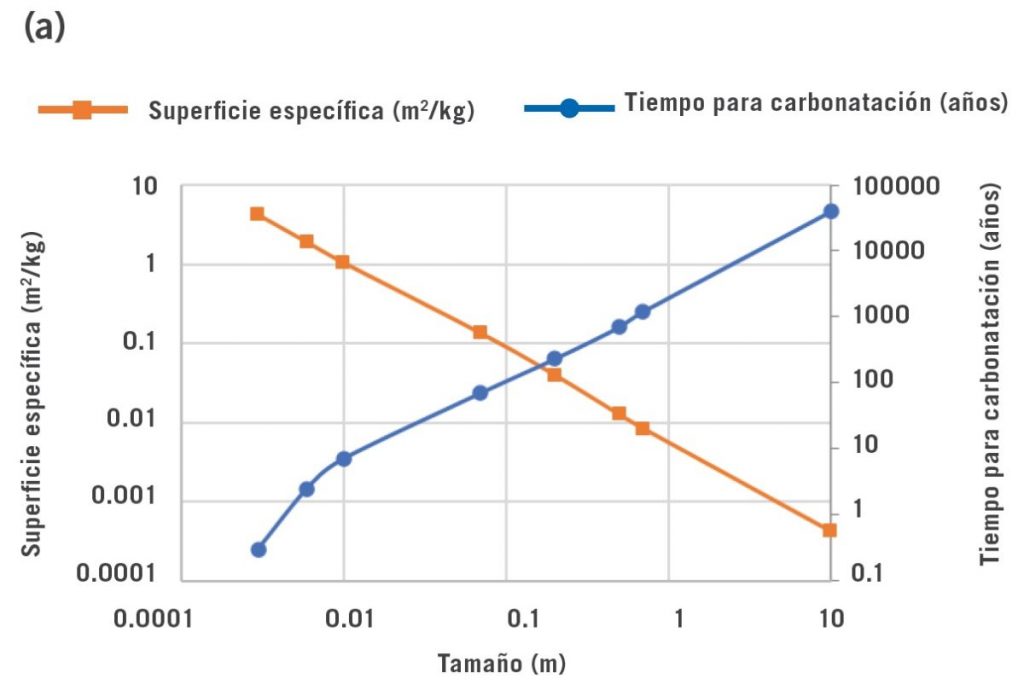
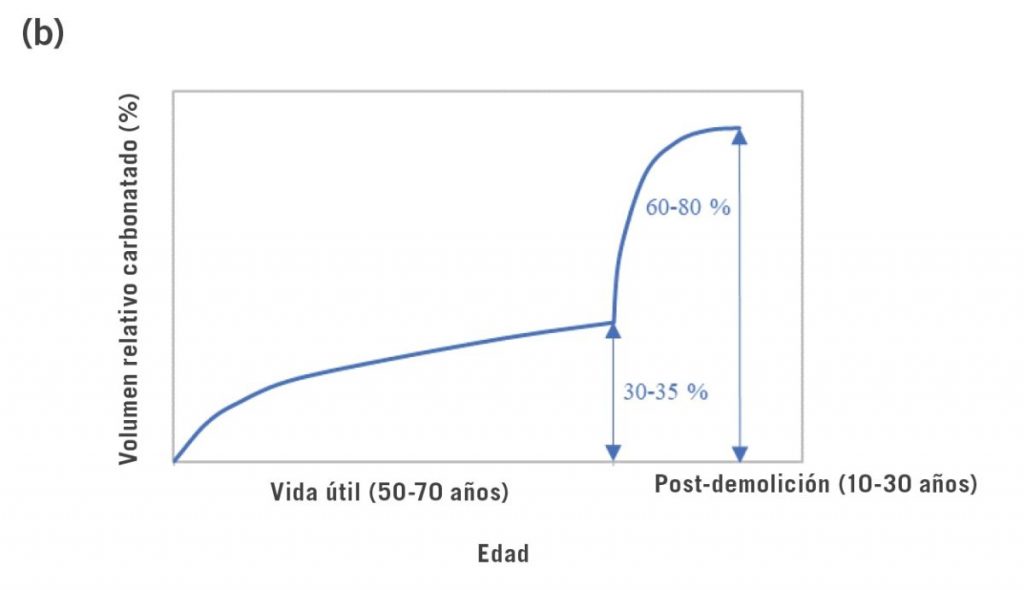
Conclusiones
La carbonatación del hormigón es un proceso con variadas implicancias. Es determinante de la durabilidad de estructuras de hormigón reciclado armado y de la ecoeficiencia de las construcciones a partir de la capacidad de captura de carbono.
Resulta necesario avanzar en el conocimiento del desempeño del hormigón reciclado frente a la carbonatación. Las investigaciones recientes describen un desempeño aceptable y en relación con los parámetros de diseño de las mezclas (principalmente la relación agua/cemento). Sin embargo, existen aspectos particulares relacionados con el mortero adherido en las partículas que implican características singulares de estos hormigones que deben ser abordadas.
La caracterización de las propiedades del agregado reciclado, principalmente en cuanto a su porosidad y contenido de mortero adherido, son fundamentales para la predicción de su desempeño frente a la carbonatación. No resultan necesarios métodos específicos, y los métodos de carbonatación acelerada ofrecen información equivalente a su aplicación en hormigón convencional. Es principalmente en la interpretación de resultados donde deben tenerse en cuenta los aspectos singulares relacionados con el mortero adherido y la zona de transición interfacial adicional.
La capacidad de captura de carbono es un aspecto aún poco investigado. Estas propiedades tienen la potencialidad de mostrar ventajas adicionales para la valorización del hormigón de desecho. De esta forma, puede tenerse en cuenta la parcial recaptura de carbono del material al final de su vida útil, como forma de cálculo más preciso de su real impacto ambiental.
Agradecimientos
Los autores agradecen el apoyo de ANPCyT a través del financiamiento PICT 2017-0091 Prest BID y PICT 2015-3339 Prest BID. Y. Villagrán-Zaccardi agradece el financiamiento recibido a Research Foundation Flanders (FWO, 12ZZD21N).
Referencias
1. Xiao J, Li J, Zhang C. Mechanical properties of recycled aggregate concrete under uniaxial loading. Cement and Concrete Research 2005; 35: 1187–94.
2. Pedro D, De Brito J, Evangelista L. Influence of the use of recycled concrete aggregates from different sources on structural concrete. Construction and Building Materials 2014; 71: 141–51.
3. Zega CJ, Di Maio AA. Comportamiento mecánico de hormigones reciclados elaborados con diferentes tipos de áridos gruesos naturales. In: UCLV, ed. Memorias Convención Científica Internacional UCLV. Varadero, Cuba, 2017.
4. Sáez del Bosque IF, Van den Heede P, De Belie N, Sánchez de Rojas MI, Medina C. Carbonation of concrete with construction and demolition waste based recycled aggregates and cement with recycled content. Construction and Building Materials 2020; 234: 117336.
5. Cantero B, Sáez del Bosque IF, Matías A, Sánchez de Rojas MI, Medina C. Water transport mechanisms in concretes bearing mixed recycled aggregates. Cement and Concrete Composites 2020; 107: 103486.
6. Silva R V., Neves R, De Brito J, Dhir RK. Carbonation behaviour of recycled aggregate concrete. Cement and Concrete Composites 2015; 62: 22-32.
7. Bravo M, De Brito J, Pontes J, Evangelista L. Durability performance of concrete with recycled aggregates from construction and demolition waste plants. Construction and Building Materials 2015; 77: 357-369.
8. Zega CJ, Santillán LR, Sosa ME, Villagrán Zaccardi YA. Durable Performance of Recycled Aggregate Concrete. Journal of Materials in Civil Engineering 2020; 32: 1014–23.
9. Zega CJ, Etcheverry JM, Villagrán-Zaccar. Natural carbonation of multiplely recycled aggregate concrete. In: Djerbi A, Omikrine-Metalssi O, Fen-Chong T, eds. International Workshop CO2 Storage in Concrete. Paris, 2019: 117–23.
10. Zega CJ, Villagrán-Zaccardi Y a., Di Maio a. a. Effect of natural coarse aggregate type on the physical and mechanical properties of recycled coarse aggregates. Materials and Structures 2010; 43: 195–202.
11. Ulsen C, Tseng E, Angulo SC et al. Concrete aggregates properties crushed by jaw and impact secondary crushing. Journal of Materials Research and Technology 2019; 8: 494–502.
12. Hoffmann Sampaio C, Cazacliu BG, Ambrós WM et al. Demolished concretes recycling by the use of pneumatic jigs. Waste Management and Research 2020; 38:392–9.
13. Silva R V., Neves R, De Brito J, Dhir RK. Carbonation behaviour of recycled aggregate concrete. Cement and Concrete Composites 2015; 62: 22–32.
14. 1Otsuki N, Miyazato SI, Yodsudjai W. Influence of recycled aggregate on interfacial transition zone, strength, chloride penetration and carbonation of concrete. Journal of Materials in Civil Engineering 2003; 15: 443–51.
15. Lee GC, Choi HB. Study on interfacial transition zone properties of recycled aggregate by micro-hardness test. Construction and Building Materials 2013; 40:455–60.
16. Xiao J, Li W, Sun Z, Lange DA, Shah SP. Properties of interfacial transition zones in recycled aggregate concrete tested by nanoindentation. Cement and Concrete Composites 2013; 37: 276–92.
17. Sosa ME, Zega CJ, Villagrán-Zaccardi Y. Contribución mecánica del agregado fino reciclado mediante la mejora de la microestructura en la zona de interfase. In: Zega C, Torrijos C, eds. Memorias IX Congreso Internacional y 23o Reunión Técnica de La AATH. La Plata (Argentina): AATH, 2020: 233–40.
18. Andrade C. Evaluation of the degree of carbonation of concretes in three environments. Construction and Building Materials 2020; 230: 116804.
19. Possan E., Felix E.F., Thomaz W.A. CO2 uptake by carbonation of concrete during life cycle of building structures. Journal of Building Pathology and Rehabilitation 2016; 1: 7.
20. Andersson R., Fridh K., Stripple H., Häglund M. Calculating CO2 uptake for existing concrete structures during and after service life. Environmental Science & Technology 2013; 47: 11625-11633. 21. Pade C, Guimaraes M. The CO2 uptake of concrete in a 100 year perspective. Cement and Concrete Research 2007; 37: 1348-1356.