La nueva estructura, bautizada como “Phoenix”, es un desarrollo conjunto entre Zaha Hadid Architects, Holcim y el Block Research Group del ETH Zúrich y Holcim, y su particularidad es que para su construcción, se utilizó un hormigón desarrollado especialmente con las piezas de “Striatus”, el anterior puente sin refuerzo que fabricó el estudio de arquitectura.
El año 2021, Zaha Hadid Architects presentó en la Bienal de Arquitectura de Venecia su puente “Striatus”, una estructura construida con hormigón impreso 3D cuya principal característica fue que no utilizaba barras de acero de refuerzo en la fabricación de sus elementos, 53 en total, quedando la resistencia del puente supeditada a la geometría del diseño de éste.
Con el uso de herramientas de diseño digital, “Striatus” logró traducir el lenguaje de la antigua mampostería de piedra a la construcción con hormigón impreso 3D sólo con uniones secas. Esta estructura, como comentó a Hormigón al Día en su momento Shajay Bhoosan, director asociado en Zaha Hadid Architects y líder del área de Diseño y Computación del estudio, aprovecha al máximo la resistencia a la compresión del hormigón, gracias a las herramientas digitales presentes tanto en su fase de diseño como de fabricación.
El proyecto recibió varios premios y sirvió de base para continuar la investigación sobre esta nueva metodología constructiva basada en el hormigón impreso 3D. Así, el estudio presentó recientemente a “Phoenix”, un nuevo puente fabricado con hormigón impreso 3D sin refuerzos, sólo que esta vez, el material utilizado corresponde al hormigón reciclado de “Striatus”, incluyendo áridos reciclados de ese hormigón, lo que lo transforma en el primer puente de hormigón impreso 3D con áridos reciclados del mundo.
Un puente de hormigón impreso 3D reciclado y sin refuerzos
Para la construcción de “Phoenix”, el estudio de arquitectura forjó una alianza con Holcim que desarrolló una particular tecnología basada en la Economía Circular que incorporó las 10 toneladas de material reciclado provenientes del anterior puente, “Striatus”.
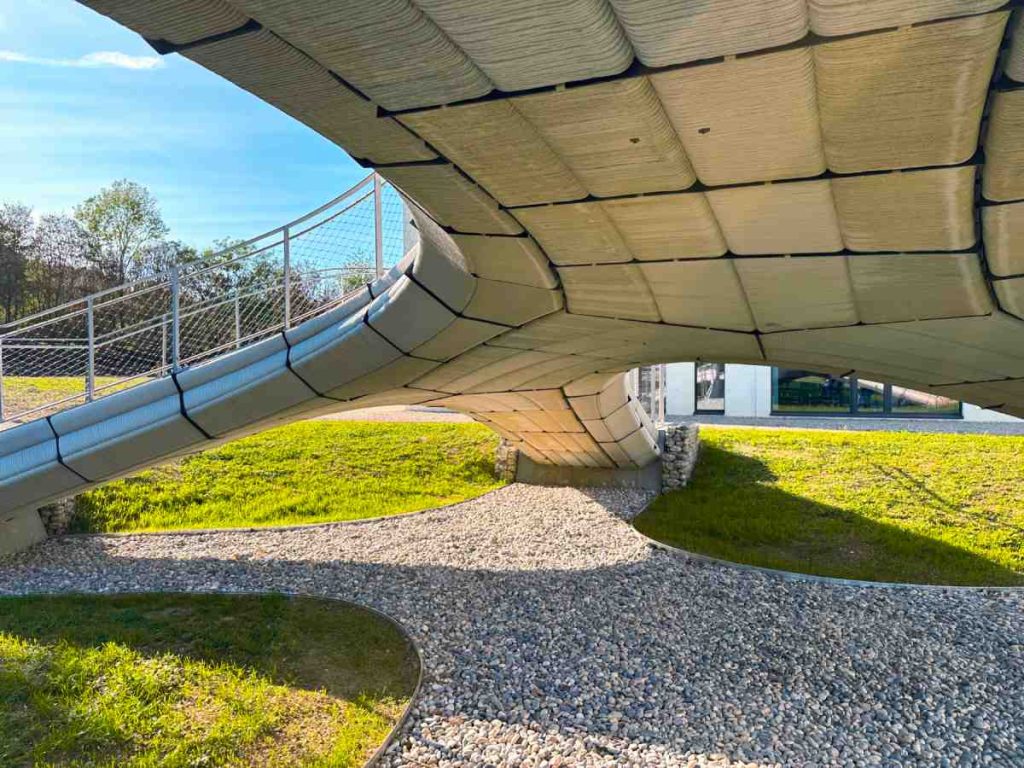
El nuevo hormigón que se desarrolló para la tecnología de impresión 3D de “Phoenix” posee una fórmula que posee un 40% menos de CO2 comparado con el que se utilizó para la construcción de “Striatus” y una huella de carbono que, en promedio, es un 25% menor que la del puente original, informó Zaha Hadid Architects en el comunicado de prensa que anunció a “Phoenix”.
También se informó que la “construcción circular, utilizando softwares de diseño computacional y tecnología de hormigón impreso 3D, permite la reducción de hasta un 50% de los materiales utilizados, sin afectar el desempeño de la estructura”. De esta forma, y tal como su predecesor, “Phoenix” se sostiene exclusivamente a través de su resistencia a la compresión sin utilizar barras de refuerzo para sus elementos, lo que permite desarmar y reciclar de manera fácil y eficiente.
Las posibilidades que presenta “Phoenix” para la construcción del futuro
Para Shajay Bhooshan, líder del área de Diseño y Computación en Zaha Hadid Architects, el puente “Phoenix” representa un “hito en lo que respecta a la rapidez tecnológica. Muestra la maduración del diseño integrado a las tecnologías de construcción que se iniciaron con el proyecto ‘Striatus’. Existen mejoras en la robustez de las herramientas de diseño digital, más cercana y alineada con las numerosas mejoras en el diseño estructural y en aspectos de la circularidad del proyecto, una impresión del hormigón más precisa y una amplia calibración para mejorar la eficiencia de producción del número de bloques, que son casi el doble, en un menor tiempo de impresión”.
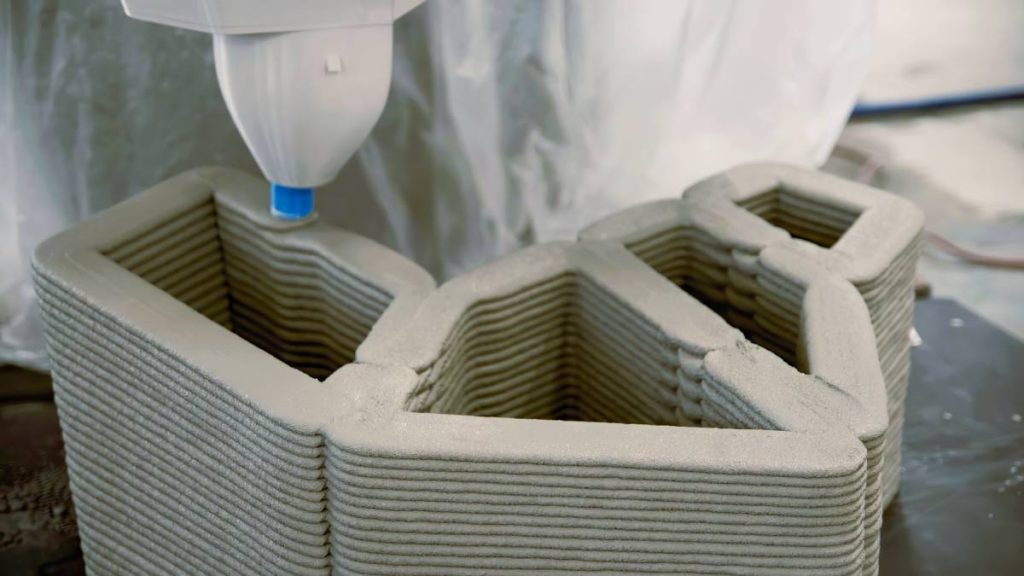
Por su parte, Philippe Block, codirector del Block Research Group del ETH Zúrich, manifestó que “el hormigón es una piedra artificial y como cualquier piedra, no quiere estar en una viga recta, quiere estar en un arco de mampostería. Seguir estos principios históricos nos permite mantener a los materiales separados para reciclarlos de manera más fácil y ensamblar la estructura en seco para un desmontaje más eficiente”. En esa línea, Edelio Bermejo, líder global de I+D de Holcim, agregó que “este proyecto muestra que, hoy por hoy, infraestructura esencial puede diseñarse y construirse de una forma que es circular y tiene una baja huella de carbono”.
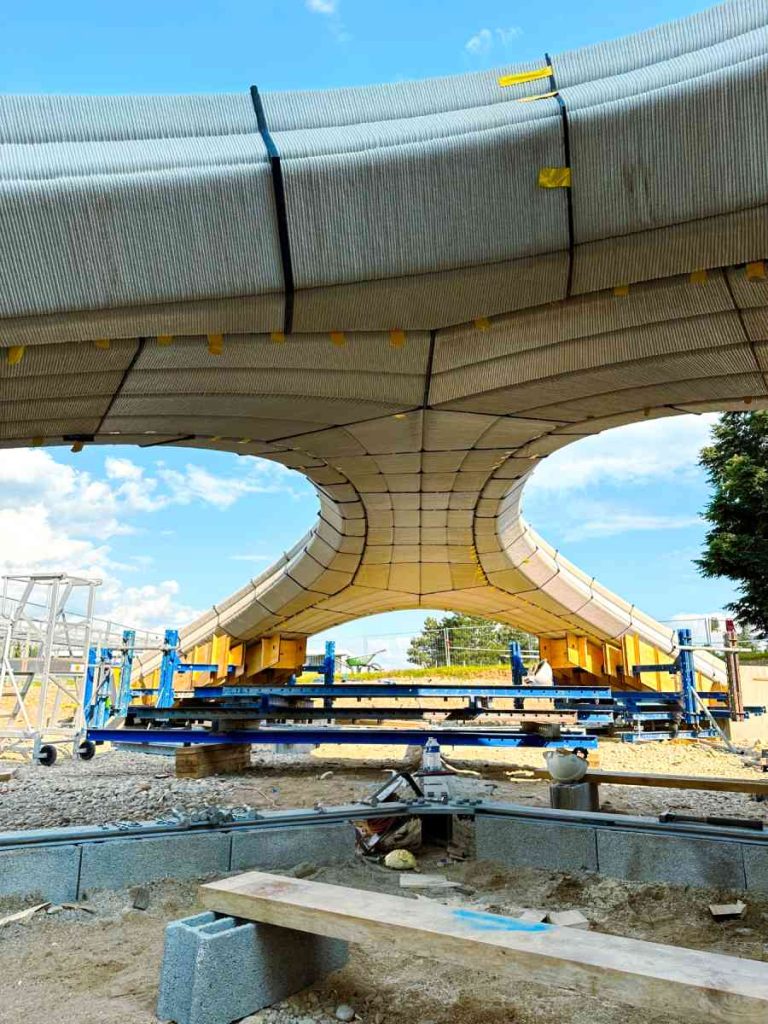
El puente “Phoenix” se fabricó en el Centro de Innovación de Holcim y en su desarrollo también participó el Block Research Group de la Escuela Politécnica de Zúrich (ETH Zurich). Con esta estructura, el grupo busca demostrar que la tecnología de impresión 3D aplicada a la construcción con hormigón, junto con elementos de la Economía Circular, brinda importantes reducciones en cuanto a huella de carbono y es posible aplicarla a cualquier escala.