Esta startup, cuya base se encuentra en Finlandia, está en el foco por su interesante aproximación al uso de la tecnología de construcción con hormigón impreso 3D, aportando elementos de infraestructura al área de bienes y servicios, fuera del ámbito de la edificación, que es donde más se conocen estos desarrollos. Para conocer más sobre sus proyectos y también, tener una imagen más clara sobre los caminos que sigue esta tecnología, conversamos con Fernando De Los Ríos, CEO de Hyperion Robotics.
En los últimos años, el avance que presenta la tecnología de impresión 3D aplicada a la construcción con hormigón resulta evidente. El tránsito desde columnas ornamentales a edificaciones completas da cuenta de cómo esta nueva metodología constructiva puede transformar las técnicas de la construcción con hormigón, aportando una serie de beneficios, entre los que destacan la productividad y la sostenibilidad.
Pese a ello, la adopción del hormigón impreso 3D para distintos proyectos ha sido más bien lenta y acotada principalmente al ámbito habitacional, donde las obras más recientes suelen ser casas o edificaciones de una o dos plantas. En Europa, por ejemplo, dentro de sus estrategias de descarbonización del sector se encuentra la promoción de proyectos que incorporen esta tecnología en su desarrollo, lo que muestra la relevancia que se le da a esta tecnología para hacer de la industria una más sostenible.
En Estados Unidos, por otra parte, se está completando un barrio completo formado por 8 modelos distintos de casas, de un total de 100 unidades, que forman parte de un desarrollo habitacional de 2.500 viviendas, subrayando la tendencia en el uso de la tecnología de construcción con hormigón impreso 3D hacia el sector habitacional.
Otra de las principales características de la construcción con hormigón impreso 3D es la adaptabilidad que posee esta tecnología. Aunque gran parte de lo que se conoce en la actualidad se vincula a la edificación, existen iniciativas que, fabricando elementos para sectores como el sanitario, eléctrico o de infraestructura civil, van incorporando esta nueva tecnología a estas áreas.
Elementos de infraestructura para el sector de bienes y servicios
Hyperion Robotics, startup de Finlandia, se encuentra dentro de esas iniciativas que buscan desarrollar la construcción con hormigón impreso 3D en áreas distintas a las del sector habitacional. Actualmente, aporta con elementos fabricados con hormigón impreso 3D a la empresa sanitaria de Yorkshire, en el Reino Unido y uno de sus primeros proyectos, con el que concitó la atención de varios medios especializados, fue el de fundaciones para subestaciones para una compañía eléctrica, en Finlandia.
“Nosotros nos enfocamos principalmente en la industria de bienes públicos o utilities, que son básicamente el sector de electricidad, agua e infraestructura en general, esa es nuestra área de experticia”, dice Fernando De Los Ríos, CEO de la startup.
¿Qué los llevó a tomar la decisión de enfocarse en este tipo de industrias y no en el área de vivienda, que es lo que suele verse para el desarrollo de la construcción con hormigón impreso 3D?
-Empezó un poco con ese proyecto inicial que tuvimos hace un par de años con Iberdrola, una de las empresas más grandes de energía, que tiene presencia también en Latinoamérica, donde les ayudamos a optimizar las fundaciones, las cimentaciones que tienen en sus proyectos eléctricos. Por un lado, desarrollamos y, de alguna manera, también descubrimos, que este tipo de estructuras tienen una mayor capacidad para optimización.
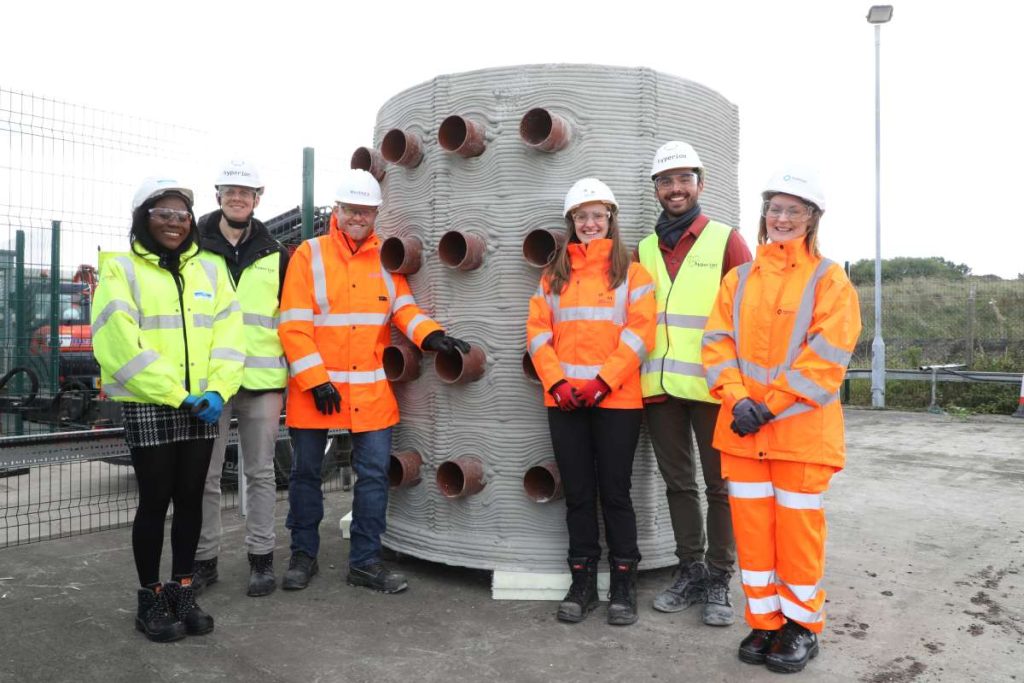
Por ejemplo, en el caso del proyecto para la empresa sanitaria de Yorkshire, los ingenieros de Hyperieon identificaron que las cajas de conducción de cables eléctricos (“drawpit”, en inglés) podían desarrollarse bajo esta tecnología constructiva y “generar un impacto importante en tiempo, costo, ahorro de material y algo muy importante, la reducción de CO2”, explica De Los Ríos.
¿De qué manera abordan ustedes el diseño estructural de este tipo de elementos?
-Muy buena pregunta. Esta es, tal vez, una de las principales diferenciales que tenemos nosotros. Tenemos un equipo de ingenieros estructurales en la empresa que se encargan de desarrollar estos diseños siempre pensando en los códigos de construcción, en el caso de Europa, es el Eurocode, el Eurocódigo.
“Sabemos, por ejemplo, que en Chile se sigue el ACI, el ASTM, pero siempre con el apéndice local, que sabemos que es un lugar sísmico, así que es mucho más estricto, entonces siempre tratamos de entender cuáles son los requerimientos desde el punto de vista del código y luego, a partir de eso, hacemos el diseño y la ingeniería y esto siempre, obviamente, considerando la forma óptima para producirlo con nuestra tecnología, generando modelos de software listos para la producción”, agrega.
Ingeniería integral y desarrollo optimizado
Pese a algunos desarrollos con hormigón impreso 3D en el Reino Unido -como en el que participó Hyperion Robotics- vinculados al área de la infraestructura, en Europa y en otras partes del mundo esta tecnología se vincula más con la construcción de edificaciones y viviendas. “En Alemania, por ejemplo, hay casos muy interesantes en el desarrollo de casas y edificios grandes, pero no mucho en este tipo de infraestructura”, comenta Fernando De Los Ríos.
En ese sentido, el CEO de Hyperion Robotics cree que la versatilidad que ofrece esta tecnología, la que permite optimizar el diseño para el desarrollo de este tipo de elementos, es una ventaja comparativa al momento de incorporar esta tecnología al desarrollo de esta clase de proyectos.
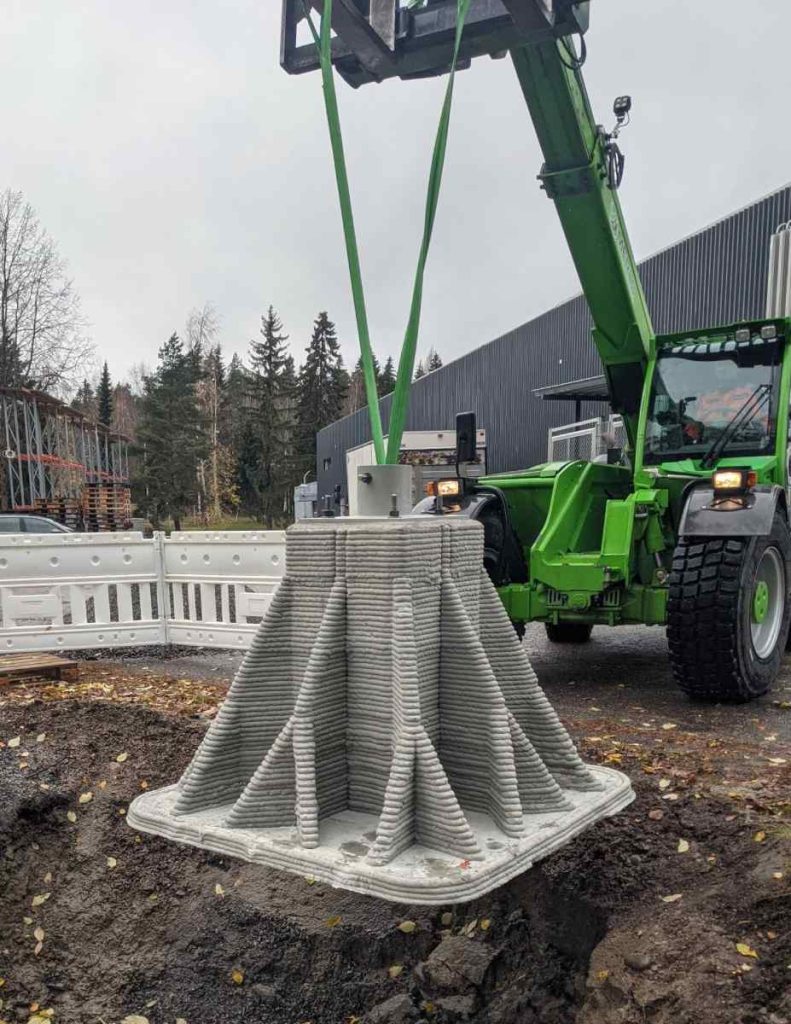
“Por ejemplo, en nuestro catálogo también tenemos tanques de agua, distintos tipos de estructuras que pueden existir en estas mismas plantas sanitaria. Si pensamos, por ejemplo, en fundaciones o cimentaciones, son muchos tipos distintos de cimentaciones y otro elemento interesante son los muros de retención, o las barreras acústicas, que se tienen en las carreteras. Existen muchos tipos de muros o barreras que podemos hacer de forma más eficiente”, puntualiza.
En ese sentido, ¿consideran ustedes el desarrollo o la ingeniería del material en estas aplicaciones?
-Hace un par de años, decidimos incorporar el desarrollo de los materiales porque al final, todo está conectado y dijimos ‘si queremos tener un desarrollo tecnológico avanzado, ágil, debemos tener un mayor control del desarrollo de estas recetas de materiales’ y por eso, tenemos un equipo de ingenieros de materiales, de hormigón, en el equipo, donde hemos desarrollado un número de recetas, de mezclas.
Dentro de esas investigaciones, Fernando De Los Ríos revela que poseen un diseño de mezcla a base de cemento -“más tradicional”, dice- que equivaldría a un hormigón de alto desempeño. “También, algo interesante para Chile, es nuestra experiencia utilizando residuos de la minería y residuos industriales donde al final, creemos que ese es el camino por seguir: cómo utilizar los materiales locales, ya sea residuos industriales, residuos de demolición, otro tipo de residuos, para reducir el impacto en materias primas y tener un producto más sostenible”, agrega.
Dentro de estos desarrollos del material, ¿también incorporan el uso de aditivos para, por ejemplo, una mejor fluidez del hormigón impreso 3D?
-Así es. Y, si lo conectamos un poquito con los requerimientos del Eurocode, hay que entender qué es lo que el código nos dice, por ejemplo, de la ratio entre agua y cemento, este tipo de requerimientos que, si es que los seguimos, y complementando con distintas pruebas, por ejemplo, pruebas mecánicas de compresión, de tensión, de durabilidad, tendremos una mejor mezcla para los elementos que desarrollemos.
“Por ejemplo, acá en Finlandia es muy frío, como tú sabrás. Entonces, tenemos que hacer pruebas de congelamiento y asegurarnos de que va a pasar todas las pruebas de durabilidad y eso es algo que tenemos: todas nuestras pruebas están certificadas y se las ofrecemos y presentamos a las empresas con las que trabajamos en los distintos proyectos”, destaca.
Relativo al avance de la construcción con hormigón impreso 3D en Europa y a escala global, ¿cómo ven el desarrollo que está teniendo esta tecnología?
-A nivel europeo es muy interesante porque poco a poco está creciendo y ha tenido un mayor impulso en el último par de años, diría yo. Existen muchas universidades que tienen presupuestos muy altos para desarrollar tecnologías y en algunos países, por ejemplo, en Holanda, hay mucho impulso de impresión 3D y de tecnologías sostenibles, ambos por el lado de la producción robótica y también, en la parte de materiales, el desarrollo de materiales sostenibles.
“Si pensamos un poco en la industria en general, vivienda es donde existe un número mayor de desarrollos, no sólo en Europa y bueno. Estamos viendo ejemplos de este desarrollo en Centroamérica, algunos en Sudamérica, en Estados Unidos, también”, subraya.
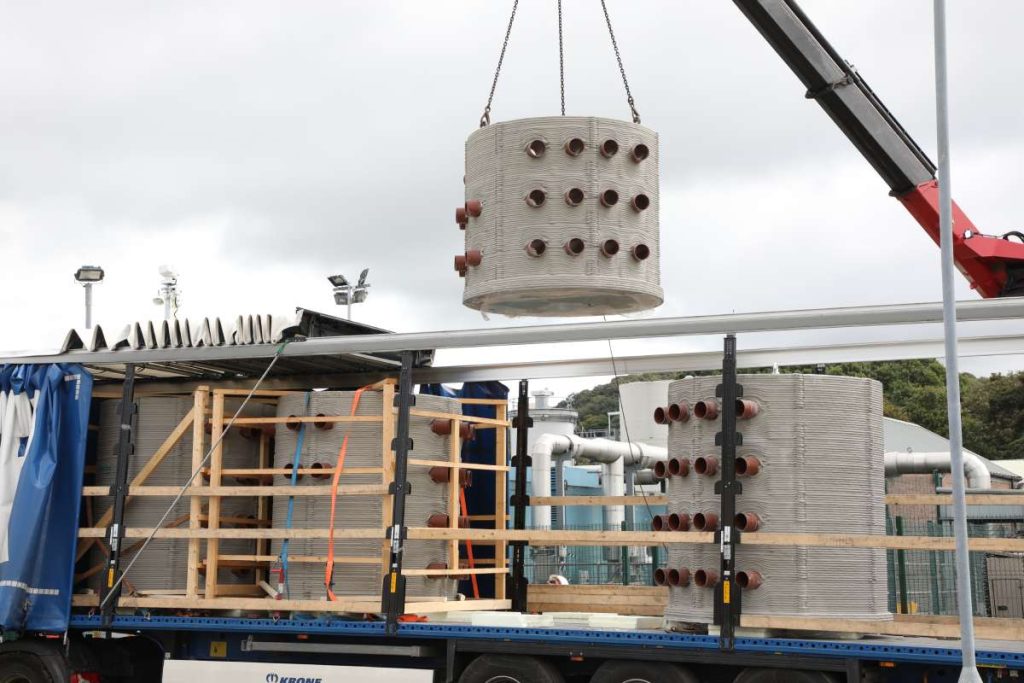
En ese sentido, el CEO de Hyperion Robotics asegura que, dadas las metas de reducción que la industria del cemento y hormigón europea se planteó para el año 2030, la incorporación de la tecnología del hormigón impreso 3D dentro de los distintos proyectos -en especial, en el desarrollo de infraestructura para el sector de bienes y servicios- será cada vez más necesaria.
“Si bien las compañías eléctricas y sanitarias son más bien conservadoras en cuanto a sus metodologías constructivas, pero por nuestra parte, estamos tratando de empujar la adopción de esta tecnología y lo hacemos con evidencia: mostramos datos que revelen beneficios directos en cuanto a su incorporación a las obras, tanto en eficiencia costo/tiempo, como también, la sostenibilidad de su adopción. Si no se dan estas evidencias, la sostenibilidad no es justificada si queremos impulsar esta tecnología a volúmenes mayores”, explica.
Dado que el sector de la construcción aún es algo conservador en ese aspecto, ¿cómo logran ustedes validarse a la hora de incorporar esta tecnología a un proyecto? ¿Exhiben las cifras de sus experiencias anteriores?
-Por un lado, está la parte técnica y es algo que nos ha tomado años de desarrollo, de I+D. Por otra parte, está el desarrollo en materiales: cómo podemos demostrar y asegurar que los materiales tendrán, como se dice en inglés, el service life, que van a durar entre 50 y 100 años porque tenemos que asegurarnos de que estas plantas industriales van a durar por muchos, muchos años y lo que hacemos por ese lado es desarrollar las pruebas de laboratorio o pruebas de escala real que nos dicen que, al tener todas estas propiedades de durabilidad, propiedades mecánicas, esto equivale a este tipo de service life. Esta es la parte técnica. Luego, tenemos el diseño. Hay que demostrar que el diseño cumple con los códigos, que tiene todos los requerimientos, que estamos haciendo estructuras reforzadas.
“También, tenemos que demostrar que es más eficiente en cuanto a costo y tiempo. Puede ser, como te decía, más sostenible, podemos ahorrar el 100% de CO2, pero es muy importante demostrar que traemos otros beneficios, empezando por la reducción de costo, pero no sólo en el costo del producto mismo, sino de toda la cadena de valor”, enfatiza.
Asimismo, resalta que en algunos países del denominado “Viejo Continente”, la legislación es algo a tener en cuenta a la hora de implementar la tecnología del hormigón impreso 3D dentro de proyectos de infraestructura. “Al tener estas leyes de sostenibilidad, por denominarlas de alguna forma, que impulsan o incentivan a las empresas a ser más sostenibles, entonces se debe considerar dentro la cadena de valor a estas nuevas tecnologías”, puntualiza.
Proyectos actuales y futuros de Hyperion Robotics
La gran recepción de las cámaras para instalaciones eléctricas que la startup finlandesa fabricó para Yorkshire Water con la tecnología de hormigón impreso 3D da evidencias de la versatilidad de esta metodología.
En el caso de la sanitaria británica, el proyecto consistió en la construcción de cuatro cámaras de inspección cuya función es “conectar cables eléctricos bajo tierra, desde distintas direcciones, dentro de una planta de tratamiento de agua”, explica Fernando De Los Ríos.
Antes de comentar sobre el proyecto en sí, ¿cómo se construyen generalmente este tipo de elementos?
-La tecnología o el método más utilizado es cast in situ, la producción in situ. Obviamente, una alternativa es utilizar prefabricados, pero bueno, uno de los desafíos principales de los prefabricados es que todos estos elementos son, de alguna manera, personalizados o customizados, todos son distintos, hay un volumen importante, pero todos son distintos dependiendo del proyecto, dependiendo de dónde se encuentren dentro de la planta de agua y normalmente, por la manera en que se fabrican, tienen la forma de una caja.
“Con nuestra tecnología -dice De Los Ríos- y nuestra experiencia en diseño, dijimos let’s think outside of the box y cambiamos la caja por un cilindro y al cambiar esa geometría, pudimos ahorrar un 50% en volumen de hormigón”.
Cada unidad, especificó el CEO de Hyperion Robotics, cuenta con un número de espacios que va entre los 16 y 30 orificios donde posteriormente, se instalan los tubos donde pasan los cables. “Si piensas en el método tradicional -explica- que es muy manual, necesitas o un molde que tenga todos estos huecos ya prearmados o se tiene que, primero, hacer la estructura y luego hacer este core drilling, forma manual, y tiene que ser en el ángulo correcto, en el lugar correcto y obviamente tienes el error humano. Entonces, la precisión robótica es algo también único que trae nuestra tecnología”.
Hablábamos antes, que uno de los beneficios de la tecnología de hormigón impreso 3D era la optimización de las estructuras, lo que llevaba a utilizar menos material. En el caso de este proyecto en específico, ¿tienen una cifra de cuánto material se ahorró?
-Al transformar ese cubo, esa caja, en un cilindro, automáticamente ahorramos un 50% de material. Principalmente, viene por la reducción del hormigón y yo diría también del acero de refuerzo, porque al optimizar la estructura misma, tenemos una reducción, de alguna manera proporcional, a la reducción de materiales, así es que ahorramos por ambas partes.
Esto significó que los ahora “cilindros”, de 2,2 metros por 2 metros de diámetro, pesaran menos, facilitando su transporte e instalación. “Si tienes una estructura que pesa, por ejemplo, más de 5 toneladas, necesitas una grúa más grande y eso es poco eficiente. Entonces, se puede hacer la instalación con la misma grúa que ya se tiene en el sitio, entonces, se ahorra mucho en términos de la complejidad logística que se tiene en el proyecto”.
Asimismo, el desarrollo completo de estos elementos, considerando las etapas de diseño, fabricación e instalación, tomó dos meses. “El cliente había estimado 6 meses para la producción de forma tradicional, incluyendo diseño, ingeniería, producción, hasta tener los elementos ya bajo tierra. Fue tan rápido el proceso que el cliente no estaba listo para recibirlos y los tuvimos que almacenar por un mes hasta poder enviarlos”, enfatiza De Los Ríos.
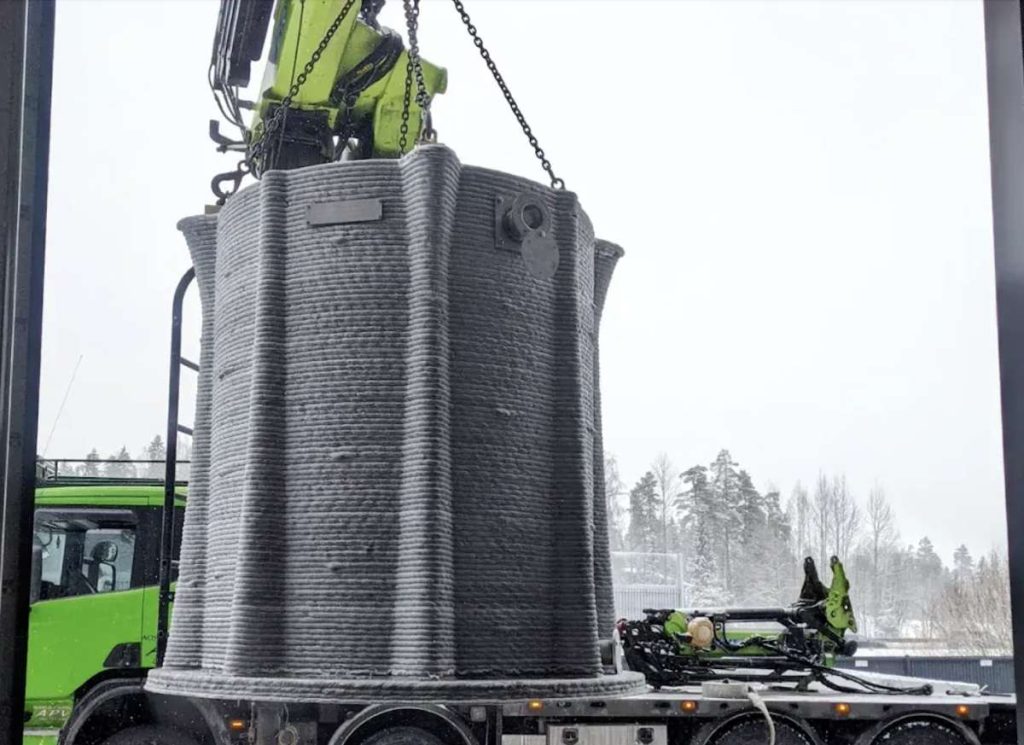
Con esto, para el CEO de Hyperion, también es posible dar evidencias de los beneficios de la tecnología de construcción con hormigón impreso 3D en cuanto a velocidad del proyecto, ya que es posible disminuir drásticamente los tiempos de construcción e incluso, revela el profesional, implementar requerimientos de última hora, como en este caso, incorporar mayor cantidad de espacios para los tubos en uno de los elementos.
“En la forma tradicional, esto tendría que hacerse de manera manual luego de tener la estructura y después, la ingeniería: el diseño hubiera tenido que esperar tal vez entre una semana o diez días para ser aprobado por el cliente. A nosotros, nos tomó menos de 5 minutos cambiarlo en nuestro modelo de software”, subraya.
¿Cuáles son los futuros desarrollos que tienen en carpeta?
-Como te comentaba, estamos trabajando con el gobierno local de una ciudad en Finlandia para la instalación de muros de retención para carreteras. Obviamente, el tipo de proyecto es distinto, pero el proceso es el mismo, diría yo, en cuanto al diseño, producción y en general, el desarrollo de los productos.
“En este proyecto en el Reino Unido -añade- desarrollamos un número pequeño de cámaras de inspección, pero la idea es empezar a tomar un mayor número de elementos dentro de estas plantas de agua, pensando en la industria sanitaria, hasta poder construir todos los elementos de hormigón donde nuestra tecnología pueda traer beneficios”.
Finalmente, el CEO de Hyperion Robotics revela acercamientos para traer su tecnología a este lado del planeta. “Estamos trabajando con algunos clientes en Latinoamérica también, cerca de Chile, así es que algo ya se debe venir. Existe una necesidad de infraestructura gigantesca, mucho más que en Europa, así es que, si podemos hacerlo de manera más eficiente y esto conectado donde vemos el crecimiento, que es en el sector energético y en cimentaciones, por qué no hacerlo”, dice el profesional.