Un equipo de la Universidad Estatal de Washington, WSU, liderado por el candidato a doctorado Zhipeng Li, incorporó biocarbón en la mezcla del cemento para producir hormigón. El resultado fue no sólo un material con una resistencia a la compresión similar al hormigón tradicional, sino también, uno con una mayor capacidad de absorber CO2 del medio ambiente.
Reducir la emisión de CO2 en la producción de cemento es uno de los principales desafíos que tiene la industria a nivel global. Prueba de ello es, por ejemplo, la Hoja de Ruta de la Global Cement and Concrete Association, GCCA, entidad no gubernamental que reúne a varios actores del sector y que, en ese documento, fija la emisión cero como meta al año 2050. Bajo esta premisa, otros organismos de países desarrollados se alinearon a este desafío.
Uno de los aspectos que más contribuyen a la emisión de CO2 es la producción del clinker, materia prima esencial para la producción del cemento, el que se obtiene al desintegrar piedra caliza en hornos a altas temperaturas. Este proceso genera CO2 tanto por el uso de combustibles -algo de lo que la industria ya se está haciendo cargo, al cambiar paulatinamente la matriz energética ya sea por fuentes renovables o, como en el caso chileno, la revalorización energética de residuos- como por el mismo proceso químico que se genera al calentar la piedra caliza.
Para disminuir esas emisiones en particular, los nuevos estudios se enfocan en sustituir la piedra caliza por otros elementos como, por ejemplo, bicarbonato de sodio. En esa línea, investigadores de la Universidad Estatal de Washington (WSU) liderados por Zhipeng Li (candidato a Doctor) y el profesor Xiaming Shi, desarrollaron una nueva fórmula que considera el uso de biocarbón para la producción de cemento, con resultados bastante positivos.
Biocarbón como aditivo especial para la producción de cemento
El biocarbón se obtiene de restos de carbón vegetal que son procesados vía pirolisis para uso agrícola. Vale decir, es una biomasa, pero de origen vegetal. Este subproducto ya se había utilizado antes en otras investigaciones relacionadas con la producción del cemento y la reducción de su huella de carbono. Sin embargo, con sólo un 3% de adición de biocarbón al cemento, la resistencia del hormigón se reducía de forma alarmante.
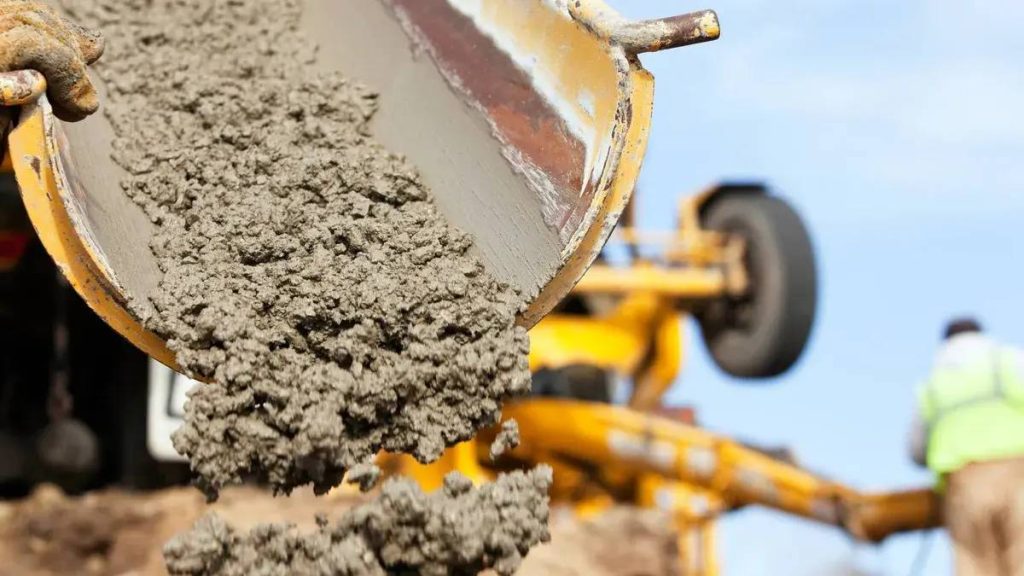
¿Qué hizo el equipo de la WSU? Trató al biocarbón con las aguas residuales del lavado del hormigón. Al hacer esto, los investigadores lograron añadir más de un 30% de biocarbón a la mezcla del cemento. La pasta cementicia resultante logró alcanzar una resistencia a la compresión a los 28 días comparable a la de un cemento tradicional.
“Nos comprometimos a encontrar nuevas formas para diversificar el uso de subproductos en la industria del hormigón. Una vez que identificamos a esos subproductos, el próximo paso es ver cómo podemos agitar la varita mágica de la química para transformarlo en un recurso”, dijo el profesor Xianming Shi.
En ese sentido, el académico destacó que las aguas residuales del lavado del hormigón, pese a que se trata de un ambiente muy alcalino, son también una valiosa fuente de calcio. Los investigadores utilizaron ese elemento para inducir la formación de calcita, beneficiando al biocarbón y, finalmente, al hormigón que incorpora ese producto.
Un hormigón que absorbe más CO2
Junto con el incremento en la resistencia, la adición de biocarbón trajo otro efecto, gracias a la sinergia entre el alto ambiente alcalino de las aguas residuales, las que contienen un alto porcentaje de calcio, y el biocarbón, de naturaleza porosa: el carbonato de calcio precipitó sobre y dentro del biocarbón, generando como resultado esa mayor resistencia y, además, permitiendo la captura del dióxido de carbono del aire.
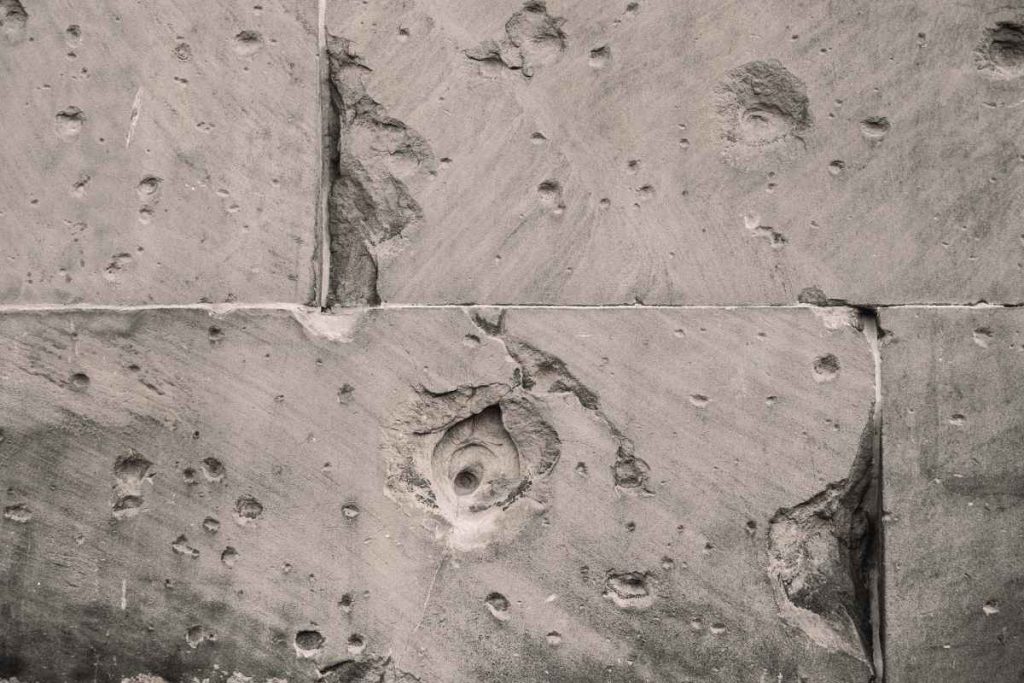
Como resultado, el biocarbón logró absorber hasta un 23% de su peso en dióxido de carbono desde el aire. Es decir, que un hormigón fabricado con esta pasta de cemento y biocarbón, podría continuar secuestrando CO2 durante toda la vida útil del concreto, la que en promedio es de 30 años para pavimentos y 75 años para puentes, a no ser que se especifique mayor durabilidad para el hormigón.
“Estamos muy entusiasmados con que esto contribuya a la misión de generar ambientes constructivos con emisión cero”, resaltó Shi. Y si bien los investigadores puntualizaron que este nuevo desarrollo se realizó en laboratorio, esperan escalarlo pronto a nivel industrial para realizar ensayos de campo a escala real con este nuevo producto.