Desarrollado por un grupo de investigadores australianos, este hormigón tiene como elemento central un cemento especial, producido con cenizas volantes y otros residuos industriales. De acuerdo a los profesionales responsables de este proyecto, el material producido posee la misma resistencia que el hormigón tradicional, pero con mucho menos huella de CO2.
Buscar nuevas “recetas” para la producción de hormigón, especialmente en el contexto actual de crisis climática, se hace necesario, especialmente cuando las metas a nivel de la industria del cemento y hormigón son el tránsito hacia la carbono neutralidad y la emisión cero.
Estos desarrollos implican, en la mayoría de los casos, el reemplazo de materias primas por otros materiales reciclados, los que disminuyen notoriamente el impacto ambiental de la producción de cemento -el elemento aglutinador del hormigón- y así, generar un hormigón de baja huella de CO2, al tiempo que se incorporan aspectos de economía circular en su producción.
En ese sentido, un equipo de investigadores de la Universidad de Murdoch, en Australia, desarrolló un nuevo tipo de hormigón que se produce con productos reciclados: “Colliecrete”, nombre que recibió ya que se genera en la localidad de Collie, ubicada en la región sudoeste de Australia Occidental.
Un hormigón especial desde el interior de Australia Occidental
“Colliecrete” tiene un ingrediente principal para su producción: cenizas volantes, que son un residuo que genera la combustión a carbón. Junto a estos, el nuevo tipo de hormigón también considera bauxita -residuo de la minería en aluminio- y otros áridos reciclados.
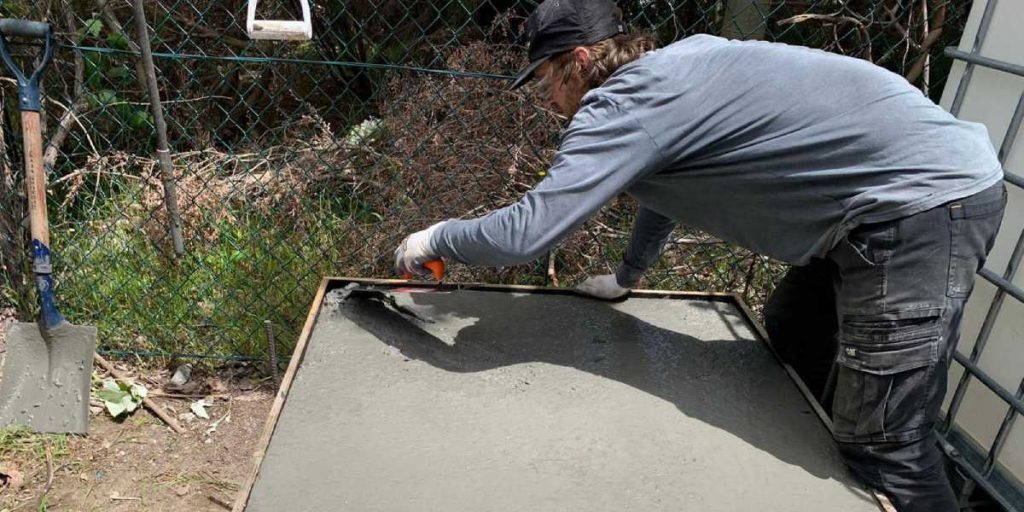
“El hormigón ‘Colliecrete’ puede utilizar entre un 80% y 90% de material reciclado en su componente de cemento”, precisó al medio australiano ABC Ramon Skane, ingeniero medioambiental y uno de los integrantes del equipo que dio vida a este nuevo producto.
¿Por qué cenizas volantes? Todo tiene que ver con Collie. Esta localidad australiana generó minas de carbón por décadas, especialmente para alimentar a las plantas de electricidad que dan energía al Sistema Interconectado del Sudoeste (SWIS, en sus siglas en inglés), la red principal del estado.
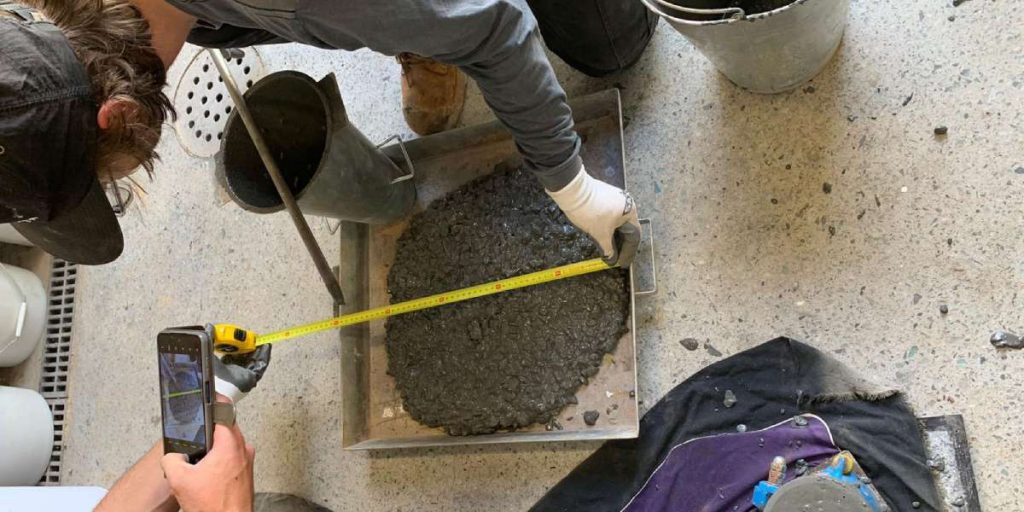
“Como resultado de esto, grandes cantidades de cenizas volantes se apilaban en Collie. Este material puede utilizarse como ingrediente activo para cementos geopoliméricos, que generan menor emisión que otros tipos de cementos”, dicen en el sitio web del proyecto. De hecho, en la misma entrevista a ABC, Skane aseguró que su cemento puede producirse “a temperatura ambiente y no calentando un horno a más de 1.000 grados Celsius para generar la caliza”.
¿Qué características tiene “Colliecrete”?
Dentro de las propiedades que destacan desde Colliecrete -además de la menor emisión de CO2- se encuentran aspectos interesantes. Por ejemplo, la resistencia a la compresión de este hormigón cuyo componente principal es el cemento geopolimérico es directamente proporcional a la ratio entre el metasilicato de sodio y las cenizas volantes. “Esto disminuye a medida que la ratio del árido se aproxima más a 0,5”, dicen en el sitio web del producto.
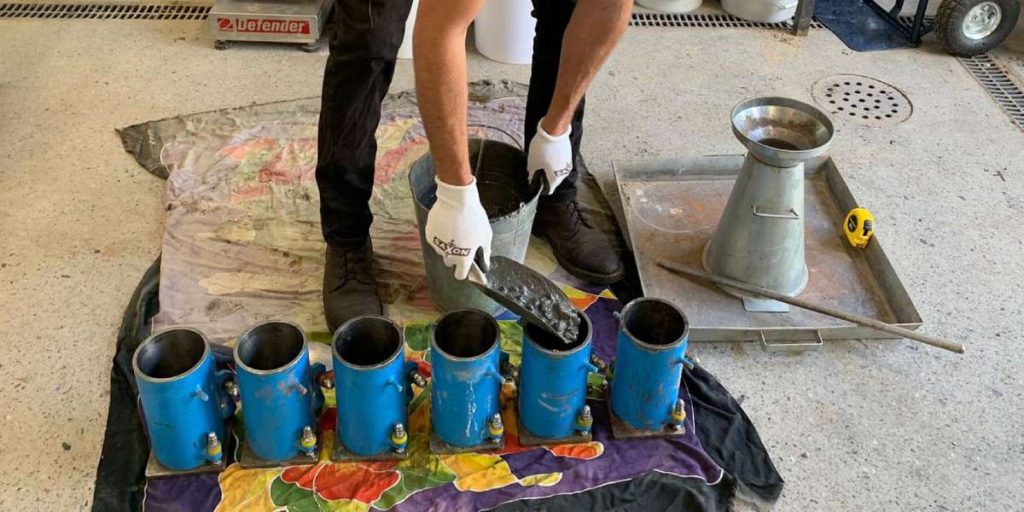
De acuerdo a esto, al aplicar estos hallazgos, se pudo generar un hormigón geopolimérico que logró una resistencia a la compresión de 100 MPa.
Otro aspecto que se destaca es que este hormigón tiene una menor contracción y calentamiento a la hidratación, en comparación con otro tipo de hormigones que en su conformación presenten cementos más tradicionales. Asimismo, la química de este hormigón le brinda una mejor resistencia al fuego y al ataque de cloruros, “haciéndolo especial para obras como anillos de fuego o estructuras en ambientes marinos”, subrayaron.
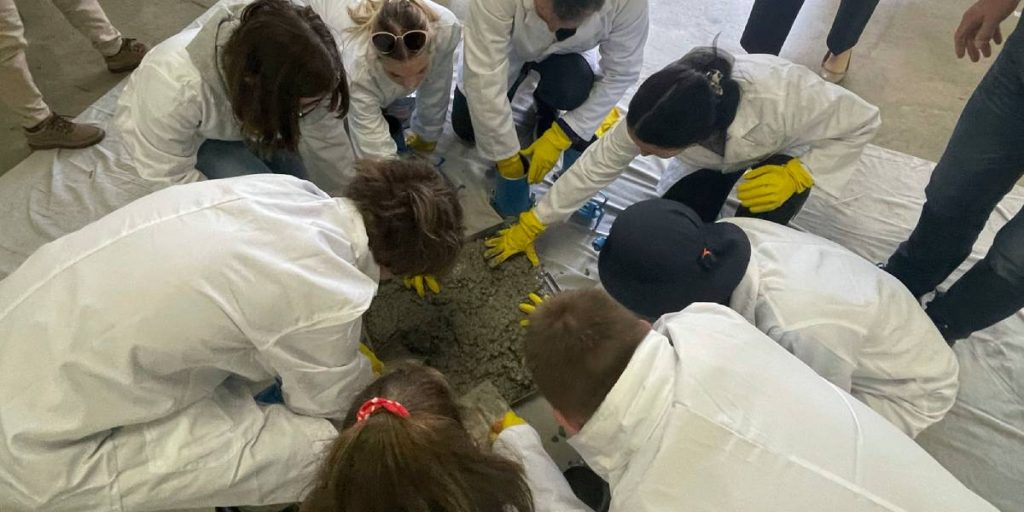
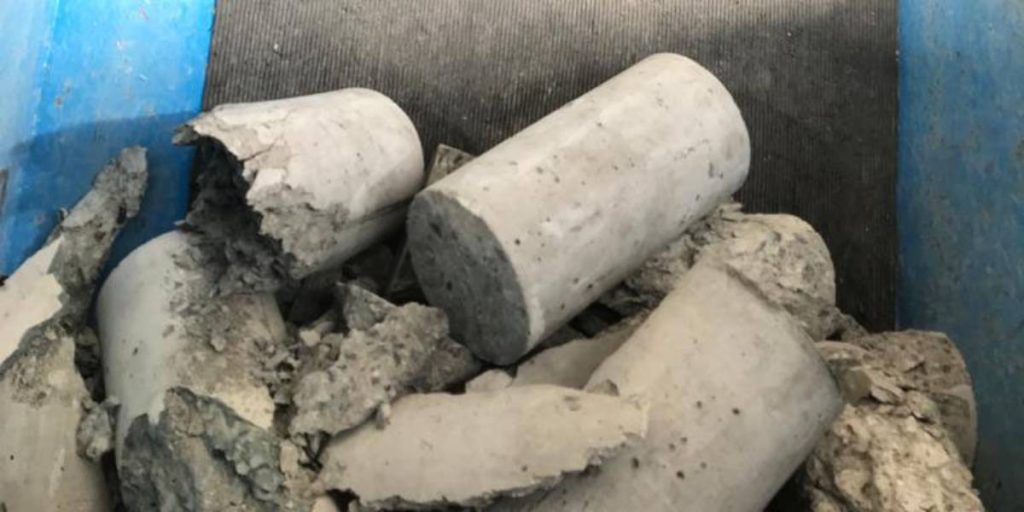
Aunque se encuentra en fase experimental y hasta el momento sólo se prueba en grandes bloques de hormigón, las aplicaciones que posee ‘Colliecrete’ son prácticamente las mismas que tiene un hormigón tradicional, ya que este nuevo tipo de hormigón se somete a ensayos de resistencia a la compresión, curado, resistencia a la tensión y contracción por secamiento, entre otros testeos. “Eventualmente, podemos utilizarlo en barreras para autopistas, incluso en edificaciones”, dijo Sarah Stanley, presidenta de Colliecrete.