Desde hace algunas décadas, la mezcla húmeda de shotcrete se usa cada vez más para aplicaciones estructurales. Recientemente, se utilizó una mezcla húmeda de shotcrete para construir un muro estructural masivo con refuerzo congestionado y dimensiones mínimas de 1,0 m en una planta de tratamiento sanitario. Para la aplicación del hormigón proyectado, se propuso una mezcla de bajo calor que incluyó hasta un 40% de escoria en la mezcla. Se realizó un ensayo previo en una maqueta, a la que se disparó el shotcrete para establecer procedimientos de trabajo adecuados y calificar tanto la mezcla del material como a los lanzadores del material. Desde el modelo, se extrajeron testigos y ventanas de corte, los que confirmaron la consolidación apropiada alrededor del refuerzo congestionado. Se desarrolló un plan de control térmico que incluyó requerimientos de ensayos tanto en laboratorio como in-situ, modelos de análisis térmico con un elemento finito de tres dimensiones y requerimientos de control térmico, incluyendo la instalación de tubería de enfriamiento y mantas térmicas.
El shotcrete probó ser un medio eficiente para la construcción de elementos estructurales masivos. Se estudió el control térmico para construcción con shotcrete masivo y se probó el plan propuesto para el control térmico para su correcto funcionamiento. Finalmente, se entregó una guía general para la construcción con shotcrete masivo.
Autores: Lihe Zhang, Dudley R. Morgan, Iain Kirk, Anastasia Rolland y Robert Karchewski.
Fuente: Shotcrete Magazine
Introducción
El shotcrete es un transporte neumático de materiales de hormigón a una alta velocidad hacia una superficie receptora, para conseguir una compactación in-situ (1). Mientras que el shotcrete lleva utilizándose por más de un siglo, el uso de este material en reemplazo del hormigón tradicional colocado in-situ para nuevas construcciones se incrementó hace algunas décadas. El shotcrete estructural se refiere a la aplicación de hormigón proyectado para elementos estructurales, los que incluyen muros estructurales, columnas y otros componentes estructurales. El shotcrete estructural posee una serie de ventajas sobre el hormigón colocado in-situ, incluyendo un menor requerimiento de encofrados. En toda América del Norte, cada vez se aplica más y más el shotcrete estructural. Para determinar si el shotcrete es adecuado para aplicaciones estructurales, se deben considerar las configuraciones del refuerzo y las dimensiones estructurales. Además de la configuración del refuerzo, una aplicación de shotcrete estructural exitosa requiere que los materiales del hormigón proyectado sean:
- Bombeables (esto es, buena trabajabilidad para la entrega/transporte y bombeo).
- Disparables (esto es, compatibilidad de trabajo con la bomba de shotcrete, manguera y boquilla. Además, que el operador pueda manejarlo de eficiente y controlada).
- Apilable (esto es, que el shotcrete aplicado a una superficie debe mostrar propiedades adhesivas y de cohesión que le permita apilarse y acumularse en todo su espesor y altura son caerse ni desmoronarse); y
- Terminable (esto es, debe ser apto para cortes, nivelados y acabados apropiados).
Con el uso de los materiales y equipos adecuados, además de las técnicas de disparo recomendadas por el ACI 506 (1) y ACI C660 (2), el hormigón proyectado puede consolidarse completamente alrededor de la armadura y de otras incrustaciones.
El uso de mezclas húmedas de shotcrete para estructuras de hormigón con dimensiones mínimas que van desde los 200 mm de grosor a los 500 mm, se incrementó de manera exponencial. Recientemente, se fabricaron con éxito estructuras con mayor grosor, es decir, que van desde los 500 mm hasta los 1,5 m, utilizando mezclas húmedas de shotcrete.
Este artículo entrega detalles respecto al uso de una mezcla húmeda de hormigón proyectado, utilizada para la construcción de un muro estructural de 1,0 m de grosor con dos capas de barras de refuerzo de 25M (#8), perteneciente a una planta de tratamiento de alcantarillado. Debido a las restricciones del sitio, construir el muro utilizando una metodología tradicional -es decir, verter y colocar el hormigón de manera normal- habría sido muy difícil. Se propuso utilizar el método de shotcrete y el muro se construyó de manera exitosa, práctica y rentable. Las características de la construcción del muro de shotcrete masivo utilizando esta metodología, fueron las siguientes:
Primero, se utilizó de manera exitosa una mezcla para el hormigón proyectado compuesta por un 40% de escoria, la que reemplazó al cemento portland. Esta mezcla probó cumplir satisfactoriamente con todos los requerimientos de este shotcrete en cuanto a bombeo, disparo, su forma de apilarse y sus requisitos de acabado.
Un operador certificado por ACI construyó el muro estructural utilizando el método de aplicación manual. Se fabricó además una maqueta con la sección más congestionada de las barras de refuerzo para disparar y calificar a la mezcla, al operador y a la aplicación del shotcrete.
Segundo, se categorizaron las estructuras cuyas dimensiones mínimas era más de 0,9 m como hormigón masivo y se requirió de un plan de control térmico (TCP, en sus siglas en inglés) para minimizar el potencial de fisuración térmica. Se testeó la mezcla de shotcrete y también, se registró el calor provocado por el proceso de hidratación. Se utilizó también un modelo de elemento finito tridimensional para modelar el desarrollo del calor y el comportamiento térmico de la estructura. Basados en la planificación de control térmico, se seleccionó la instalación de unas tuberías de enfriamiento para cumplir con los requerimientos del plan. Así, se instaló una capa de tuberías de enfriamiento, espaciadas en intervalos de 1,0 m, para cumplir con los requerimientos de la obra.
“Se utilizó exitosamente una mezcla húmeda de shotcrete para construir un muro masivo con armadura congestionada”.
Importancia de la investigación
Aunque en la actualidad, se utiliza más al hormigón proyectado shotcrete para construcción estructural, son relativamente pocos los proyectos que reportan ser estructuras masivas de hormigón con dimensiones mínimas de 0,9 m. El comportamiento térmico para la construcción con hormigón masivo debe controlarse de forma adecuada; sin embargo, existe poca información en la literatura publicada que se refiera a medidas de control térmico para construcción con hormigón masivo. Este articulo presenta información relacionada con una mezcla húmeda de shotcrete que considera un 40% de escoria en su diseño, el que se utilizó para la construcción de un muro masivo de shotcrete de 1,0 m de grosor con dos capas de barras de refuerzo de 25M. Además, entrega detalles respecto al análisis y modelado térmico, y el desarrollo de un plan de control térmico para esta construcción de un muro con shotcrete masivo. El plan de control térmico debe ejecutarse controlando la temperatura de colocación del hormigón proyectado, instalando tubería de enfriamiento para disipar el calor que genera la hidratación del shotcrete y aplicando mantas térmicas para protección termal. Las temperaturas registradas durante el monitoreo de la construcción estuvieron muy cercanas al desarrollo de temperatura modelado. La inspección posterior a la obra no encontró fisuras térmicas en el muro estructural de shotcrete.
Este artículo entrega una guía general para la construcción con shotcrete masivo, que incluye:
- Se prefiere el uso de una mezcla de bajo calor para el shotcrete por lotes, bombeo, disparo y acabado.
- La construcción con shotcrete masivo debe conseguir una consolidación adecuada alrededor de la armadura; y
- El plan de control térmico del shotcrete masivo debe minimizar el potencial para fisuras térmicas.
Estudio de viabilidad
Un gran contratista civil en el oeste de Canadá construyó una planta de tratamiento para desechos de alcantarillado. Las dimensiones del muro estructural de interés aparecen en la Fig. 1.
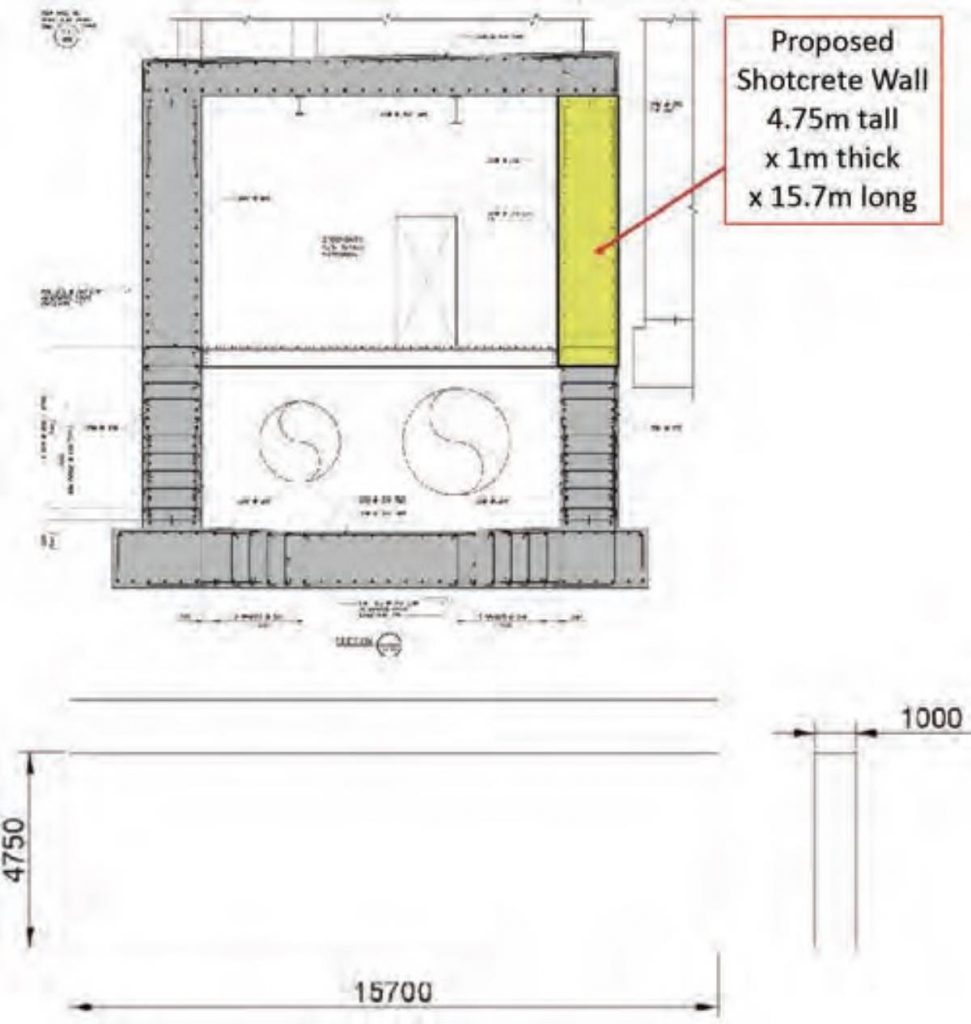
Para la construcción del elemento, se propuso una metodología que involucra el uso de una mezcla de shotcrete con un alto volumen de escoria y la instalación de tubería de enfriamiento en el muro estructural. Sin embargo, debido a la falta de experiencia previa en proyectos que involucren el uso de shotcrete masivo para la construcción de muros que consideren medidas apropiadas para cumplir con los requerimientos de control térmico, tanto el mandante como el ingeniero diseñador y el contratista levantaron las siguientes interrogantes:
- ¿Puede el shotcrete aplicarse de forma exitosa en un muro de 1,0 m de espesor con dos capas de barras de refuerzo de 25M, espaciadas por 300 mm?
- ¿El proceso dañará a los tubos de refuerzo durante la aplicación, al involucrar hormigón proyectado a altas velocidades?
- Debido a que las mezclas de shotcrete tienen, usualmente, un contenido de cemento más alto que las del hormigón colocado in-situ, usualmente de al menos 400 kg/m3 de material cementicio, esto puede resultar en temperaturas muy elevadas. ¿El calor de la hidratación aumentará el potencial de fisuras térmicamente inducidas?
- ¿Qué medidas se pueden implementar para mitigar el potencial de fisuraciones térmicas?
Para responder a esas preguntas y probar que el shotcrete sí era apropiado para la construcción de un muro estructural de 1,0 m de grosor con una consolidación satisfactoria alrededor de la armadura de barras de refuerzo de 25M y, además, probar un desempeño térmico satisfactorio, se construyó una maqueta para realizar los ensayos pertinentes. Se evaluó a la maqueta y la encapsulación de las barras de refuerzo se inspeccionó de forma visual, con la extracción de testigos y ventanas de corte desde la maqueta. El contratista procedería a utilizar shotcrete para construcción del muro, siempre y cuando la maqueta demostrase que el hormigón proyectado podía aplicarse de forma satisfactoria para encapsular a las barras de refuerzo. Al mismo tiempo, se realizó un ensayo de caja caliente para obtener la curva adiabática del alza de temperatura de la mezcla, base que se utilizaría para el desarrollo de una planificación de control térmico para la construcción del muro de hormigón masivo.
Diseño de mezcla
El contratista de hormigón propuso un diseño de mezcla para el shotcrete con una resistencia a la compresión de 35 MPa a los 28 días. Esto satisfizo los requerimientos de resistencia a la compresión para un elemento estructural bajo esta exposición al ambiente. La mezcla se diseñó con 60% de cemento tipo GUL (tipo 1L) y un 40% de escoria, que reemplazó al cemento portland. El cemento tipo GUL tiene aproximadamente un 15% de caliza y tiene un menor calentamiento producto de la hidratación, comparado con un cemento tipo GU. Con el 40% de reemplazo de escoria, el calor generado durante el proceso de hidratación del cemento se reduce aún más. Aumentar el reemplazo del cemento con alto contenido de escorias reducirá el calor provocado por la hidratación del shotcrete. Sin embargo, aumentar en demasía el reemplazo con escoria puede provocar dificultades para el proceso del shotcrete que incluyen el bombeo, aplicación y en particular, el apilamiento del hormigón proyectado sin desprendimientos. Previo a este proyecto, generalmente se añadía a la mezcla húmeda del shotcrete un 25% de escoria de reemplazo. Por lo mismo, aumentar el contenido de escoria a un 40% requirió de ensayos que probasen que el shotcrete podía ser bombeable, disparable y que no se desprendería del elemento.
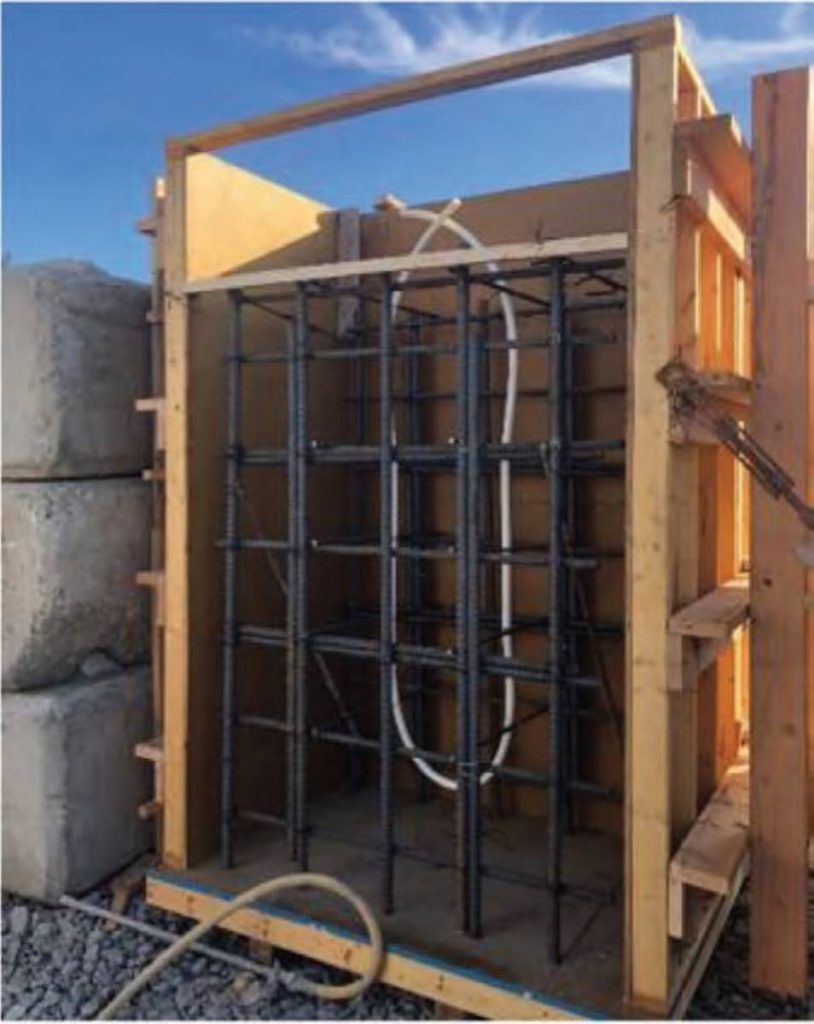
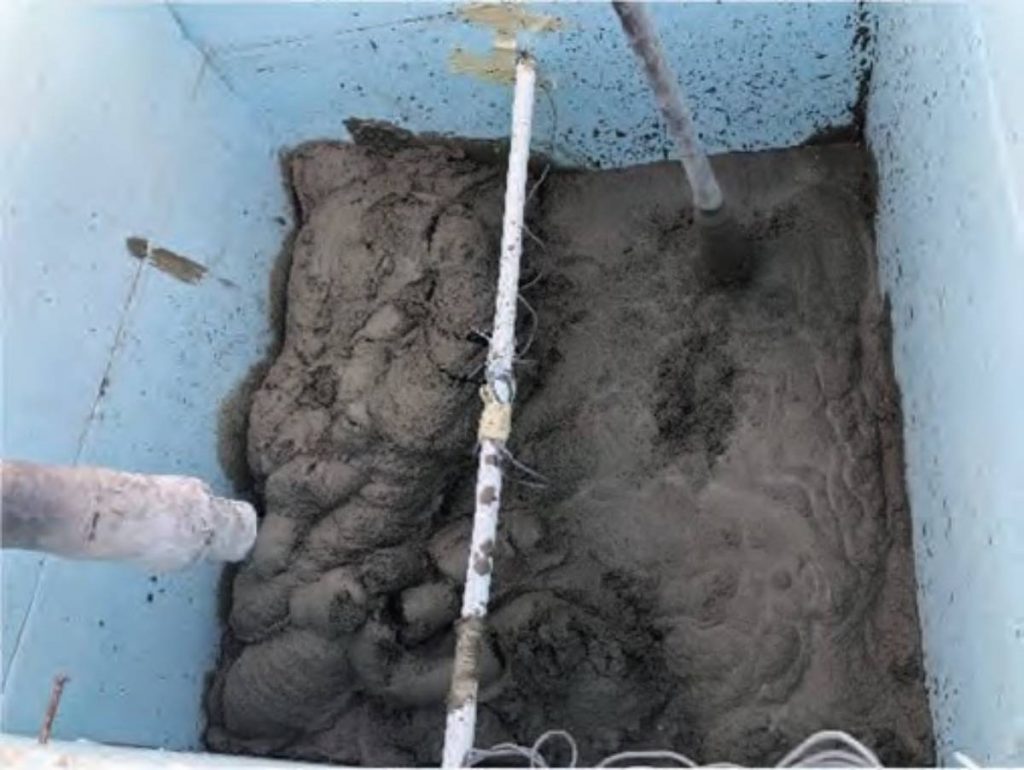
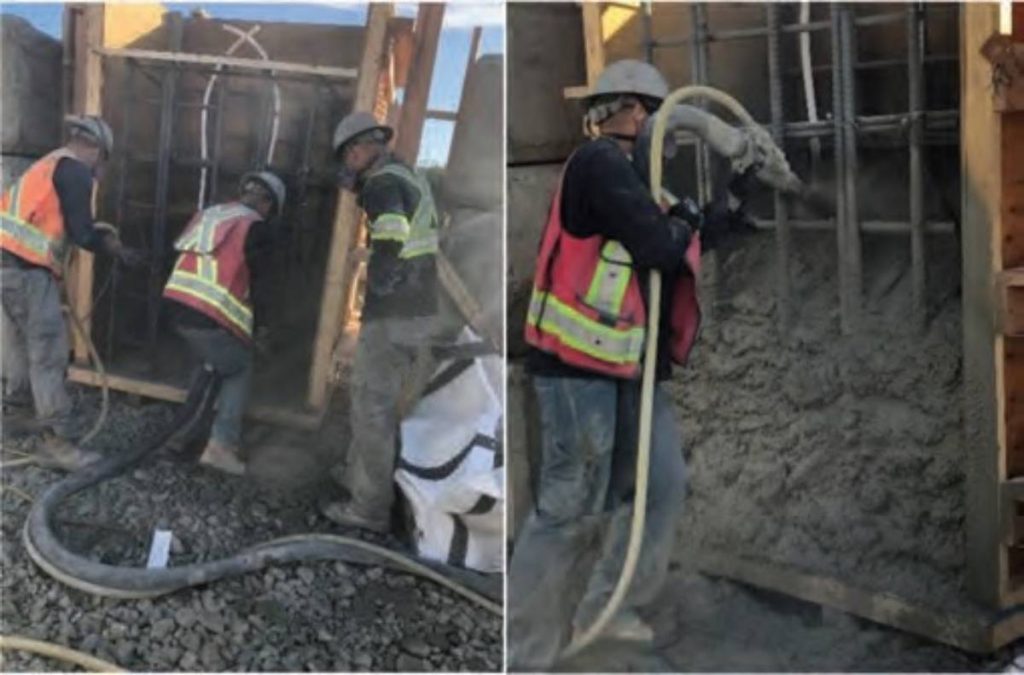
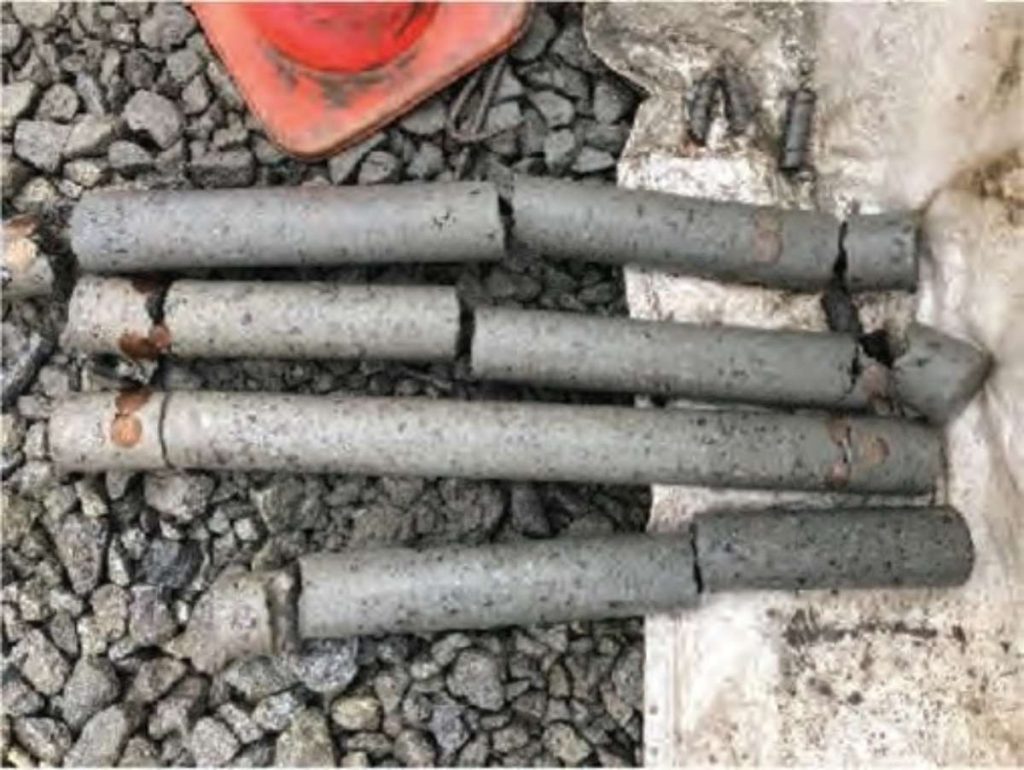
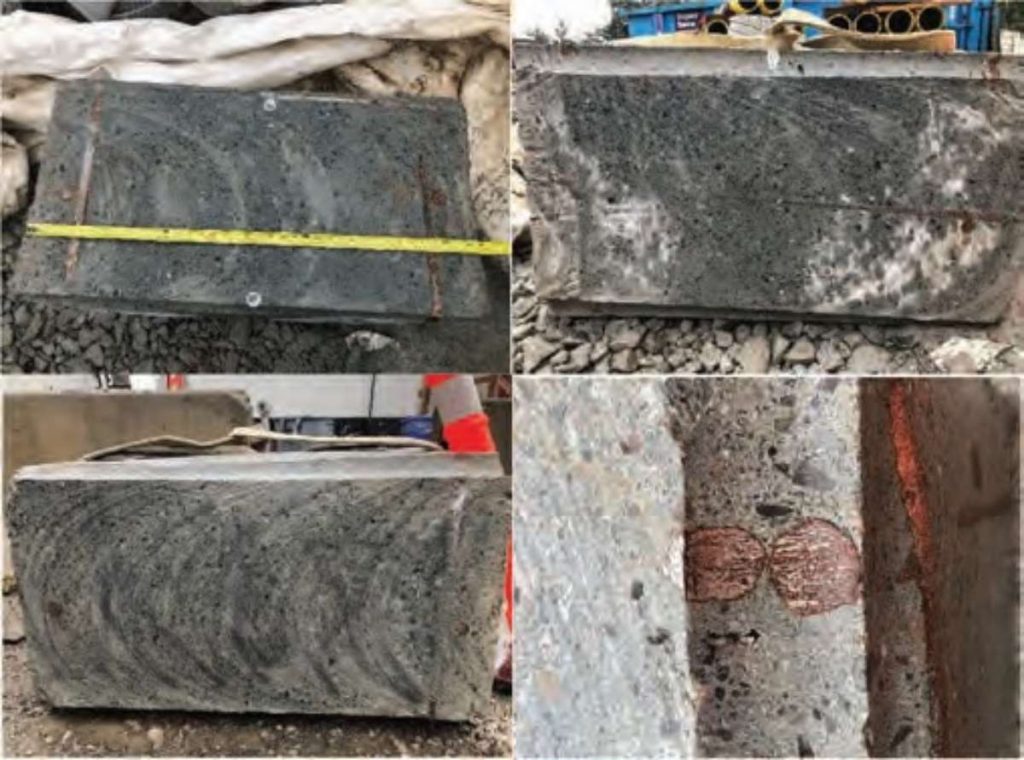
El uso de áridos gruesos (de un tamaño máximo de 10 mm) y finos para el diseño de mezcla del shotcrete cumplió con los requisitos de gradación No. 2 de ACI 506R.
La relación (peso/cm) entre los materiales cementicios y el agua tuvo un máximo de 0,40.
El diseño del asentamiento fue de 70 ± 20 mm para aplicación de shotcrete estructural. Este tamaño se testeó y cumplió de manera adecuada con el bombeo y proyección para aplicaciones de shotcrete estructural. El asentamiento es crítico para que el lanzador aplique de forma exitosa el hormigón proyectado en elementos estructurales. Un asentamiento más bajo ayuda a que el shotcrete se apile en secciones más gruesas a mayor altura sin desmoronarse. Sin embargo, si el asentamiento es demasiado bajo, el hormigón proyectado no fluirá apropiadamente alrededor y encapsulará a las barras de refuerzo y a los empotramientos. Con un 40% de escoria de reemplazo, la mezcla húmeda del shotcrete tiende a desmoronarse a un mayor asentamiento. Por ello, se debe tener una especial consideración, además de técnicas de disparo adecuadas, cuando se trabaje con un volumen alto de material cementicio suplementario; el shotcrete y los lanzadores prefieren trabajar con asentamientos bajos para aplicaciones estructurales. Se utilizó un reductor de agua de alto rango para alcanzar el asentamiento requerido. No se requirió de retardante u otro aditivo para el control de la hidratación. Se diseñó la mezcla para colocarla dentro de 90 minutos ya que más de ese tiempo provocó que la mezcla comenzara a endurecerse y no pudiese bombearse de forma correcta. El asentamiento, en el rango de 70 ± 20 mm, resultó adecuado para esta mezcla.
Se incorporó aire a la mezcla del shotcrete con un contenido de 5 a 8% de aire en lotes, en satisfacción con el requisito de durabilidad de congelación y deshielo del CSA C-1 Exposure Class. La adición de aire al shotcrete ayuda al material a ser bombeable y facilitar su proyección luego de su salida de la boquilla. Un hormigón proyectado con aire incorporado tendrá un contenido de aire en lote más alto y reducirá, por lo tanto, el contenido de aire del shotcrete al momento de su proyección. Un contenido de aire incorporado más alto facilita el proceso de bombeo mientras que un el aire más bajo al momento de proyectar el material ayudara a su apilamiento. Este es un beneficio único del aire incorporado en el shotcrete, referido como el “efecto que mata al desmoronamiento” (1, 3, 4).
Se realizó un análisis preliminar térmico basado en valores térmicos supuestos y se consideró aceptable la construcción del muro con shotcrete, sujeto a la implementación de las siguientes medidas:
- Utilizar una mezcla con 40% de escoria, con tubos de enfriamiento y la instalación de mantas térmicas para el control térmico.
- Utilizar a un contratista con experiencia en shotcrete estructural, con una rigurosa inspección y ensayos de control de calidad para asegurar la conformidad de las especificaciones del proyecto.
Maqueta de tiro
Se condujo una maqueta de tiro con los siguientes detalles:
- Se instaló la armadura tal y como aparece en los planos del muro estructura (Fig. 1).
- Durante la construcción de la maqueta, se instaló una capa de tubos de enfriamiento (tubo de cloruro de polivinilo [PVC] con un diámetro de 25 mm) con un espaciado de 1m para testear si pudiese causar algún tema de consolidación (Fig. 2).
- Las muestras se colocaron para testear el calor de la hidratación requerida por los modelos finitos en tres dimensiones.
- Se construyó un bloque con aislamiento de placa de poliestireno extruido (EPS) de 1 x 1 x 1 metro con 150 mm de grosor en cada uno de los seis lados. Se utilizó el desarrollo de la temperatura tanto para un cilindro de 150 mm de diámetro como para un bloque de 1 m3 para calcular el aumento de la temperatura adiabática para la mezcla del shotcrete (Fig. 3).
La aplicación del shotcrete en la maqueta del muro estructural se realizó con éxito. Un experimentado lanzador (con certificado ACI en proceso de mezcla húmeda) logró un disparo de alta precisión exitoso al muro en su altura completa, en combinación con el uso de un vibrador y un tubo de soplado (Fig. 4).
La figura 5 muestra los testigos que se extrajeron de la maqueta de muro y la figura 6, el bloque recortado. Ambos muestran claramente que tanto la barra de refuerzo de 25M como los tubos de enfriamiento de 25 mm de diámetros, fueron debidamente envueltos por el hormigón proyectado y que la maqueta está libre de vacíos o de otros defectos.
Los resultados de los ensayos de disparo en la maqueta se consideraron satisfactorios y cumplieron con las mejores prácticas industriales (1). Tanto el mandante como los ingenieros diseñadores acordaron que podría utilizarse una mezcla húmeda de shotcrete para construir el muro estructural con una adecuada consolidación alrededor de la armadura y con tubería de enfriamiento.
Los resultados del ensayo con mezcla húmeda de shotcrete en la maqueta fueron los siguientes:
- Asentamiento: 55 mm.
- Temperatura: 17,8 °C
- Contenido de aire por lote: 6,2%
- Contenido de aire por disparo: 2,5%
Los testigos se extrajeron desde un panel de pruebas del shotcrete y se ensayaron para resistencia a la compresión a 7 y 28 días, y para absorción de la ebullición y volumen de vacíos permeables a 7 días. Los resultados de estos ensayos fueron los siguientes:
- Resistencia a la compresión a los 7 días: 23,6 MPa
- Resistencia a la compresión a los 28 días: 36,1 MPa
- Absorción de la ebullición: 5,4%
- Volumen de vacíos permeables: 12,0%
La aplicación de shotcrete en la maqueta demostró que el hormigón proyectado puede aplicarse de forma exitosa para consolidar barras de refuerzo de gran diámetro y armadura de múltiples capas. En particular, demostró que en la sección con mayor congestión de las barras de refuerzo se consolidó de manera adecuada, con el lanzamiento adecuado. Además, el shotcrete también logró consolidarse de manera completa alrededor de la tubería de enfriamiento sin dañarla. Los resultados de la resistencia a la compresión de los testigos de shotcrete alcanzaron los 35 MPa especificados a 28 días. La absorción de la ebullición fue menor al 17%, lo que cumplió con los requerimientos de desempeño e indica una buena calidad del shotcrete (3). El comportamiento térmico de la mezcla de hormigón proyectado se obtuvo tanto en ensayo de laboratorio como en prueba de campo.
Modelado térmico y efecto de la tubería de enfriamiento en el desarrollo de la temperatura
El incremento de la temperatura adiabática (Fig. 7) se desarrolló en ensayo de laboratorio con cilindros de 150 mm de diámetro y en pruebas in-situ con un bloque de 1 x 1 x 1 m aislado con un tablero de EPS de 150 mm (R = 15).
Se utilizó un programa computacional de elemento finito 3-D para modelar el desarrollo de la temperatura para el muro estructural. Se estudió el efecto de la tubería de enfriamiento y se modeló el bloque de hormigón con y sin estos tubos. Los resultados se muestran en la Fig. 7. La temperatura de colocación del hormigón fue de 15°C para ambos escenarios. Cuando se utilizó la tubería de enfriamiento, la temperatura más alta se redujo de 58 a 53°C. También se redujo el tiempo en alcanzar dicha temperatura de 48 a 50 horas, a 35 a 38 horas.
Luego de alcanzar la temperatura más alta, la tubería de enfriamiento resultó muy efectiva para disminuir la temperatura del centro durante la parte descendiente de ésta. Esto resultó en un menor diferencial de temperatura entre el centro y la superficie. Sin los tubos de enfriamiento, el diferencial de temperatura era, aproximadamente, de unos 15°C cuando se dejaron en su lugar las mantas térmicas y luego superó los 20°C después de 168 horas o 7 días, cuando se sacaron las mantas. Con los tubos de enfriamiento, el diferencial de la temperatura fue de 10°C y menos con las mantas térmicas colocadas, permaneciendo bajo los 10°C luego de 168 horas o 7 días, cuando estas se sacaron.
Esto demostró que la tubería de enfriamiento puede reducir de forma efectiva la temperatura más alta, como también, los diferenciales de temperatura entre el centro y la superficie.
La tubería de enfriamiento también entregó gran flexibilidad para el calendario de construcción. Durante las obras, es común que el calendario cambie debido a varias razones. Los tubos de enfriamientos brindaron una opción alternativa para acomodarse a los desafíos impuestos por la obra, por ejemplo, una temperatura de colocación del hormigón más alta o repentinos cambios en la temperatura ambiente.
Plan de control térmico
Se preparó un plan de control térmico (TCP, en sus siglas en inglés) para que la construcción del muro cumpliese con los requisitos especificados para el hormigón masivo, los que son:
- La temperatura más alta debe ser menor o igual a 60°C para evitar la formación de etringita tardía (DEF)
- El diferencial de temperatura entre el centro y la superficie debe ser menor o igual a 20°C
- En una situación donde el diferencial de temperatura exceda los 20°C, se debe realizar un análisis de esfuerzo y el esfuerzo térmico calculado versus la ratio de resistencia a la tensión no debería exceder el 75%.
Los resultados del modelado térmico se incluyeron en la Tabla 1 con los escenarios 1 y 2, que son los siguientes:
-Escenario 1: La temperatura de colocación del shotcrete es de 15°C, sin tubería de enfriamiento, las mantas térmicas cubren la superficie acabada del shotcrete desde el tiempo su colocación por 10 días. Este escenario controló la temperatura de colocación, la que puede ser la forma más efectiva para reducir la temperatura peak. Sin embargo, esto puede resultar un desafío para la preparación por lotes de hormigón masivo durante días cálidos en el verano o a principios de otoño.
-Escenario 2: La temperatura de colocación del shotcrete es de 20°C, con una capa de tubería de enfriamiento espaciada por 1 metro, con una temperatura de 13,7°C de agua, la manta térmica cubre la superficie acabada del shotcrete desde el tiempo de su colocación por 7 días. Este escenario requiere de menor esfuerzo en el control de la temperatura de colocación, pero mayor en el control de la temperatura durante la construcción, es decir, instalando y manteniendo el agua fría durante el periodo de curado.
Los resultados del modelo en ambos escenarios se diagramaron en la Fig. 8, con el hormigón colocado a 15°C.
La selección del escenario dependerá del programa de construcción y el esfuerzo para controlar la temperatura de colocación, instalación y mantenimiento del tubo de enfriamiento, lo que requiere de la coordinación entre los ingenieros diseñadores y los equipos de construcción.
La construcción del muro con shotcrete se programó para principios de septiembre, sin embargo, se descubrió que controlar la temperatura del hormigón proyectado a 15°C resultaba complejo. Por ello, se eligió el escenario 2 y se instaló la tubería de enfriamiento con un espaciado de 1 metro, como se muestra en la figura 9.
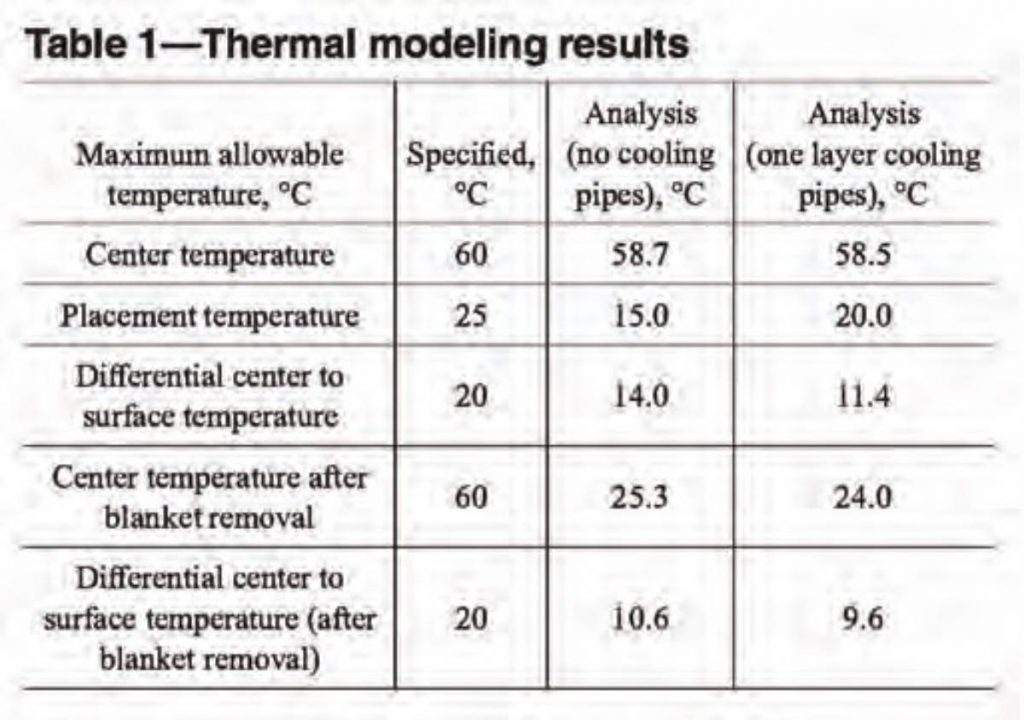


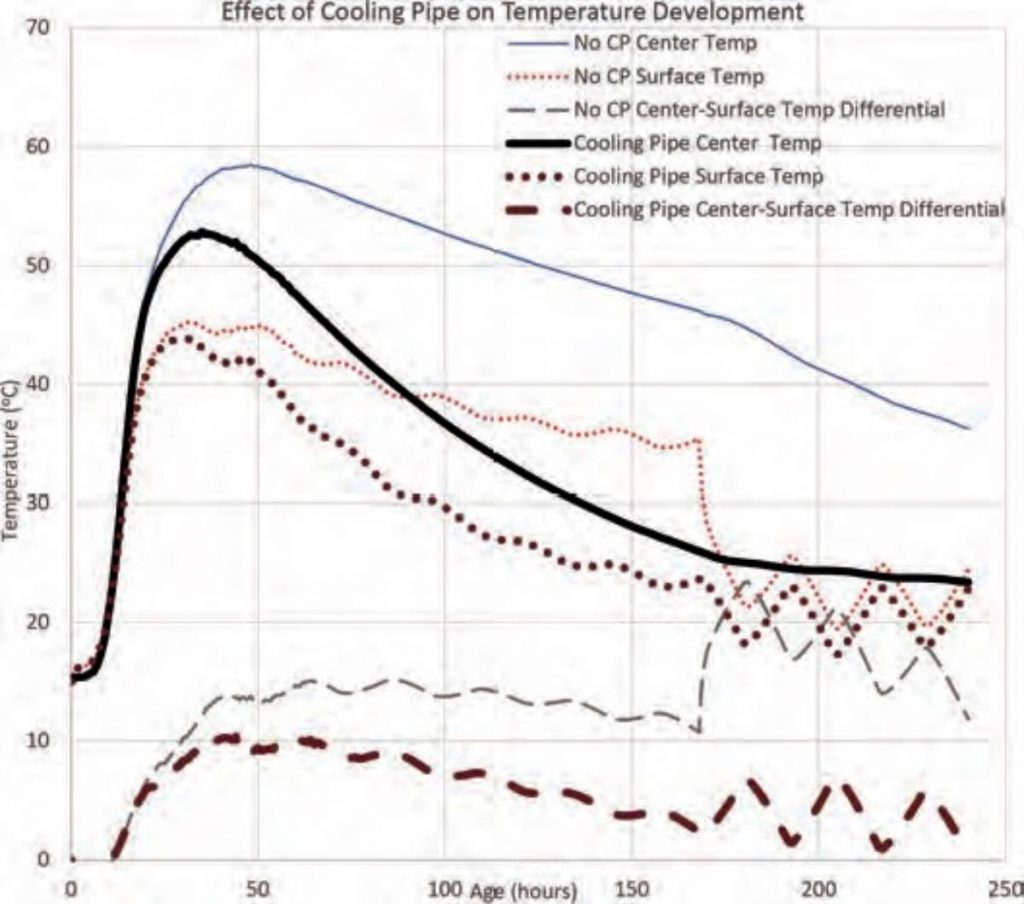
Construcción del muro estructural
A comienzos de septiembre, se construyó el muro estructural utilizando una metodología de aplicación de mezcla húmeda de hormigón proyectado. El autor realizó un monitoreo e inspección rigurosos, a la vez que llevó a cabo ensayos de control de calidad, durante todo el proceso de aplicación. Los resultados de dichos controles se incluyeron en la Tabla 2. La aplicación del shotcrete comenzó a las 7:00 y terminó a las 16:30. En resumen, este gran muro estructural se construyó sólo en 9,5 horas, utilizando una mezcla húmeda de shotcrete premezclado. Se aplicó un total de más de 70 m3 de hormigón proyectado utilizando la metodología de disparo de alta precisión. Los detalles de la aplicación del shotcrete se encuentran en la figura 10 hasta la 21.
Resultados de los ensayos de control de calidad del shotcrete
- Resistencia a la compresión a los 9 días: 38,5 a 46,6 MPa; lo que supera los 35 MPa especificados a los 28 días
- Absorción de la ebullición: 6,5 a 7%, lo que cumple con el máximo especificado de 8%
- Volumen de vacíos permeables: 14,5 a 15,4%, lo que cumple con máximo especificado de 17%
Productividad de la construcción del muro de shotcrete masivo
Previo a la construcción del muro, el ingeniero instaló e inspeccionó un encofrado trasero y la armadura. Durante la construcción del muro de shotcrete masivo, se aplicó un total de nueve camiones de carga con 8 m3 de hormigón proyectado, para un total de 72 m3 de shotcrete. La aplicación del shotcrete comenzó a las 7:00 con disparo continuo durante el día. La colocación del hormigón proyectado terminó a las 15:55 y el acabado del hormigón proyectado se completó a eso de las 17:30. Por ello, tomó un total de 9 horas completar la aplicación y 10,5 horas terminar todo el trabajo con el shotcrete, incluyendo su acabado. Esto resultó en un promedio de producción de construcción del muro de shotcrete masivo de una carga de camión de 8m3 de hormigón proyectado, con un total de 72 m3 aplicados en un turno de 10,5 horas. Esta tasa de producción es típica para aplicaciones de shotcrete estructural, con un equipo de dos a tres lanzadores, cuatro finalizadores y cuatro ayudantes.
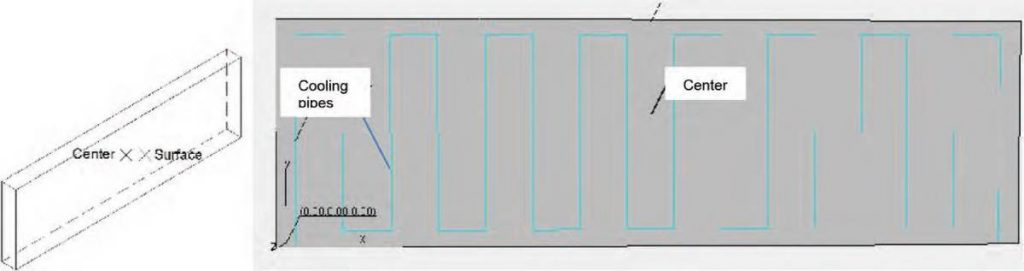
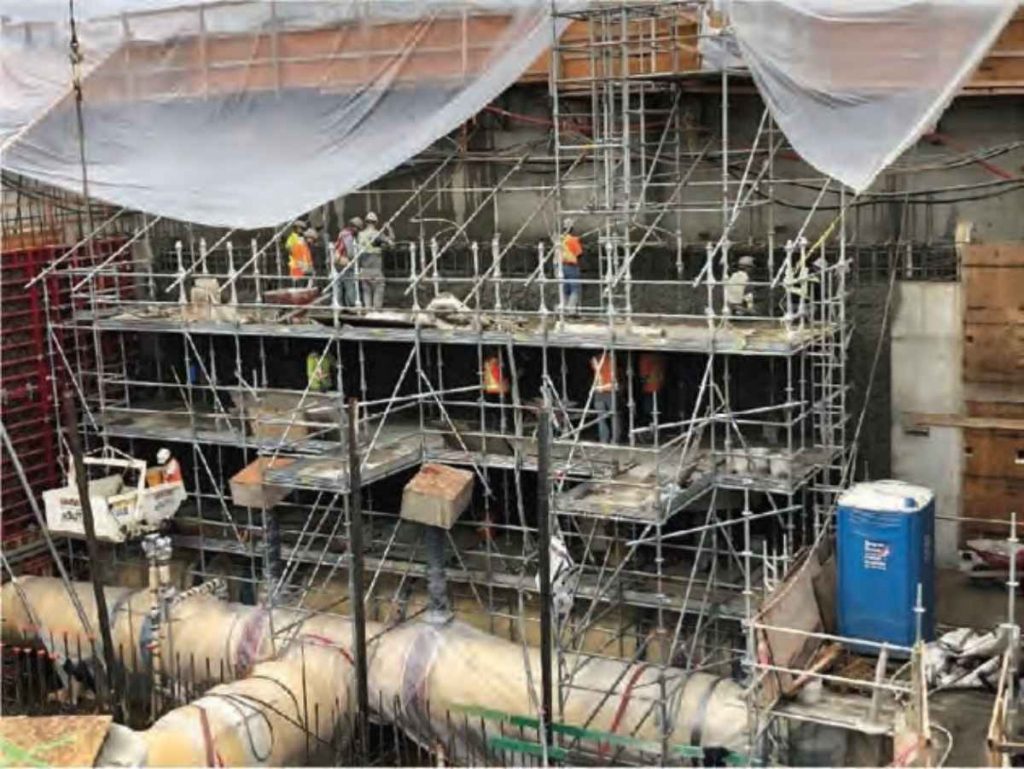
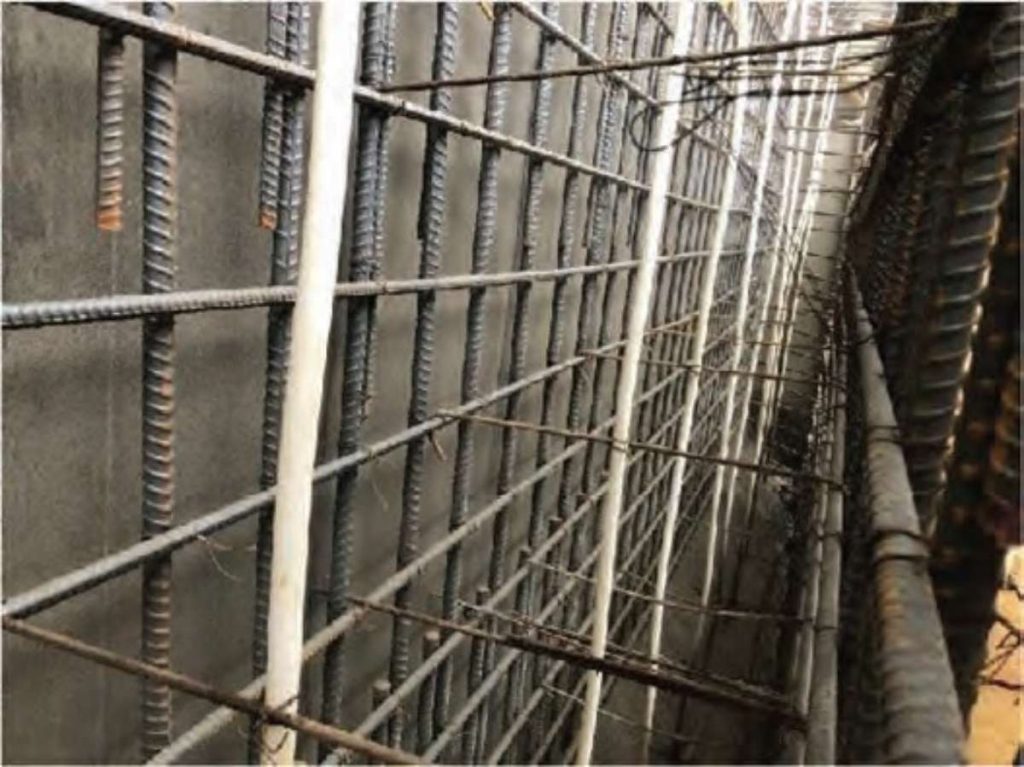
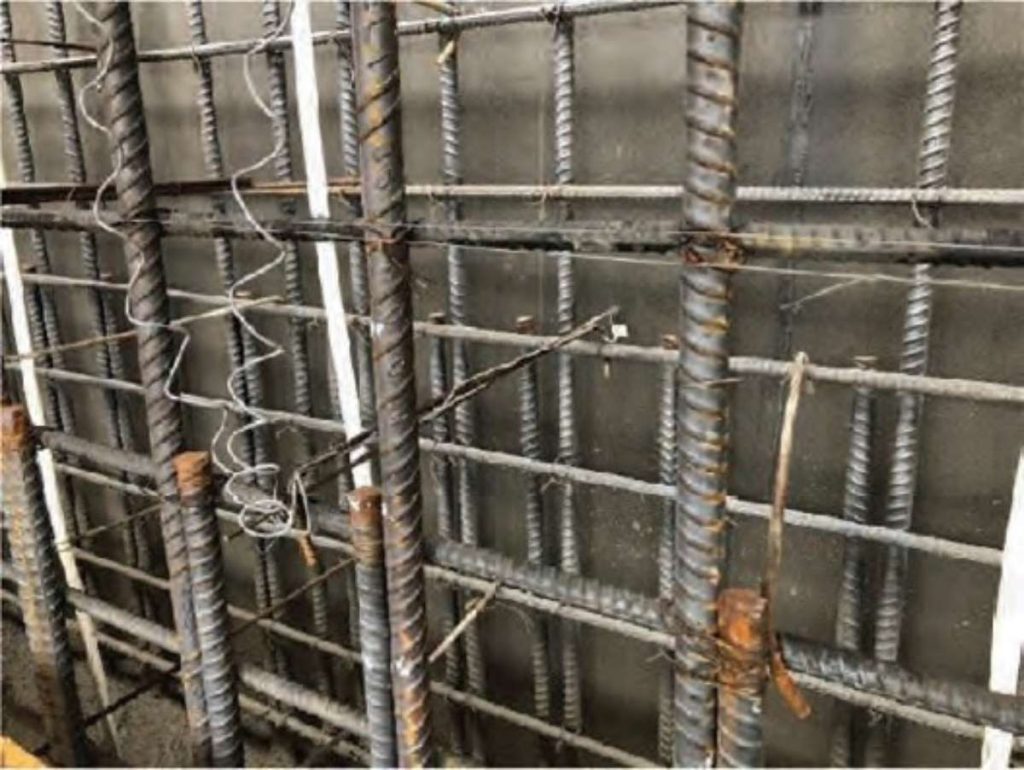
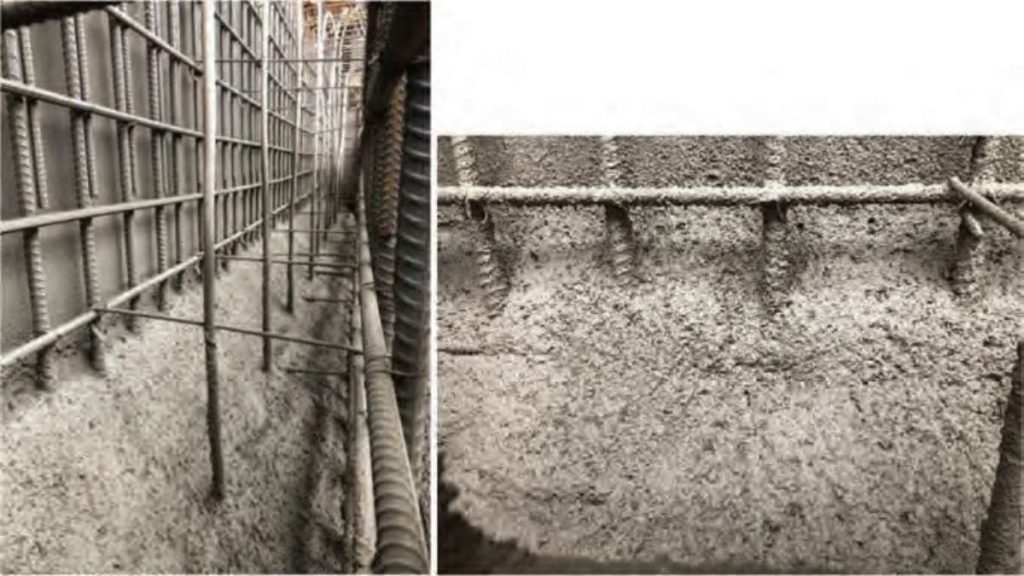
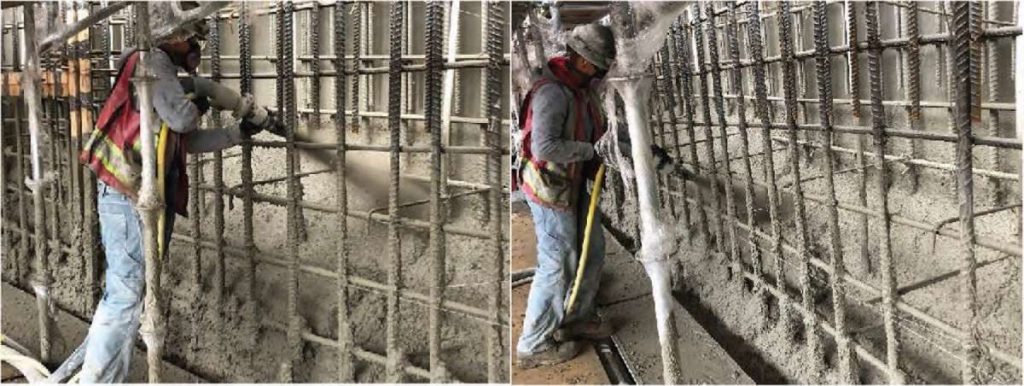
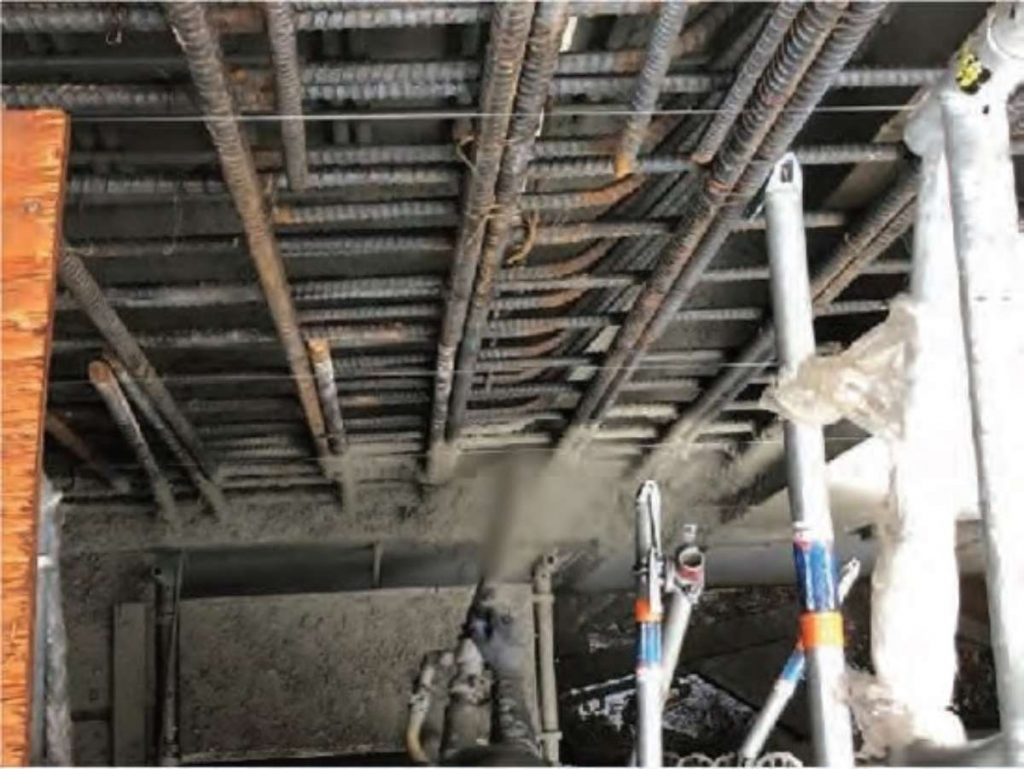
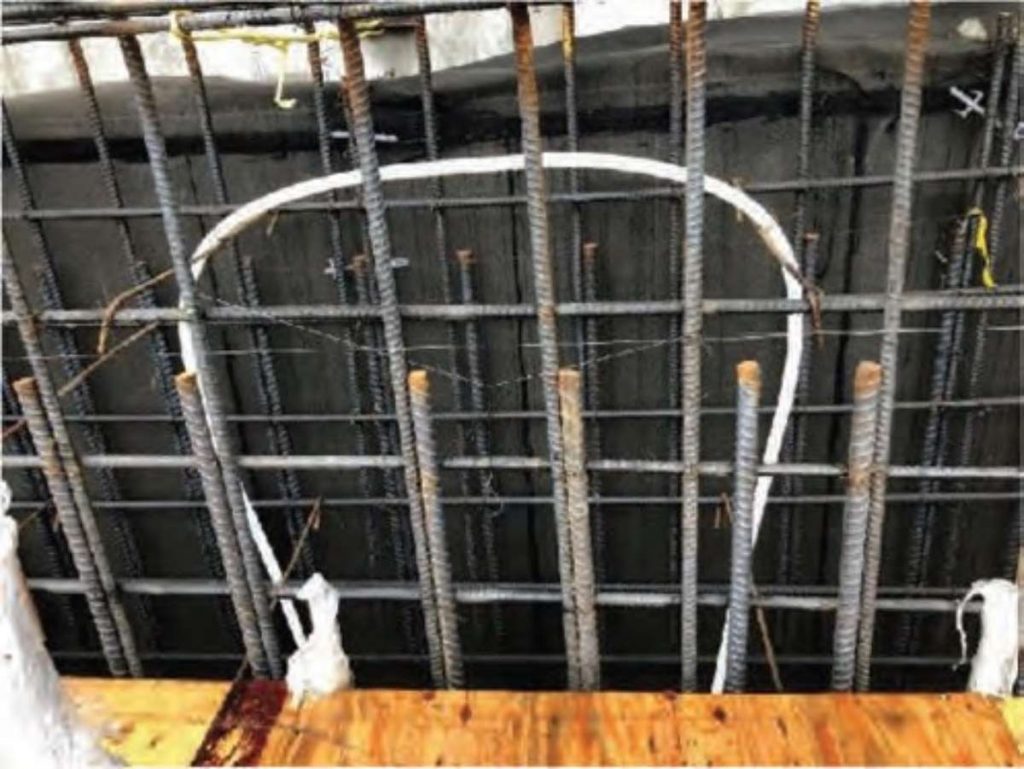
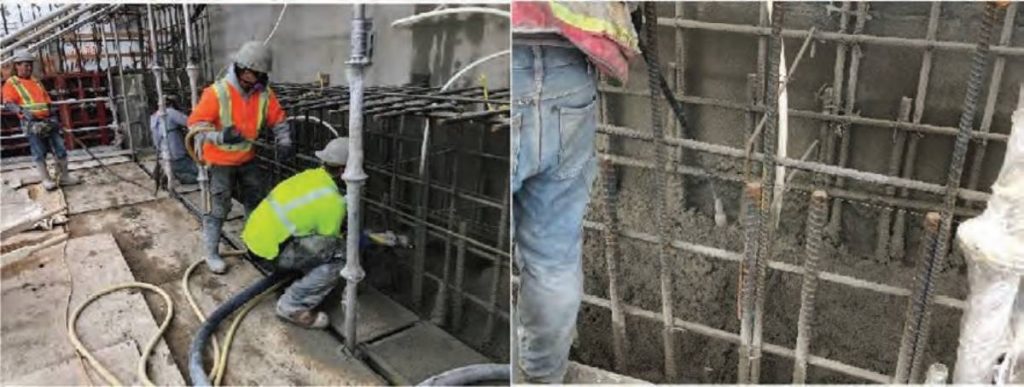
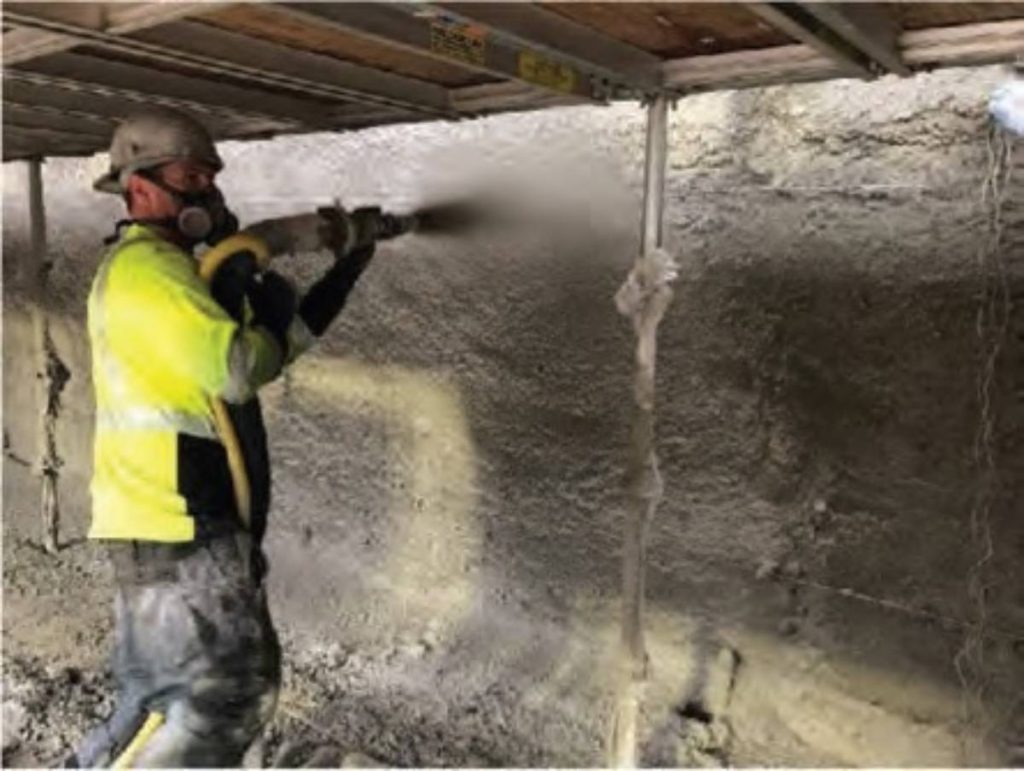
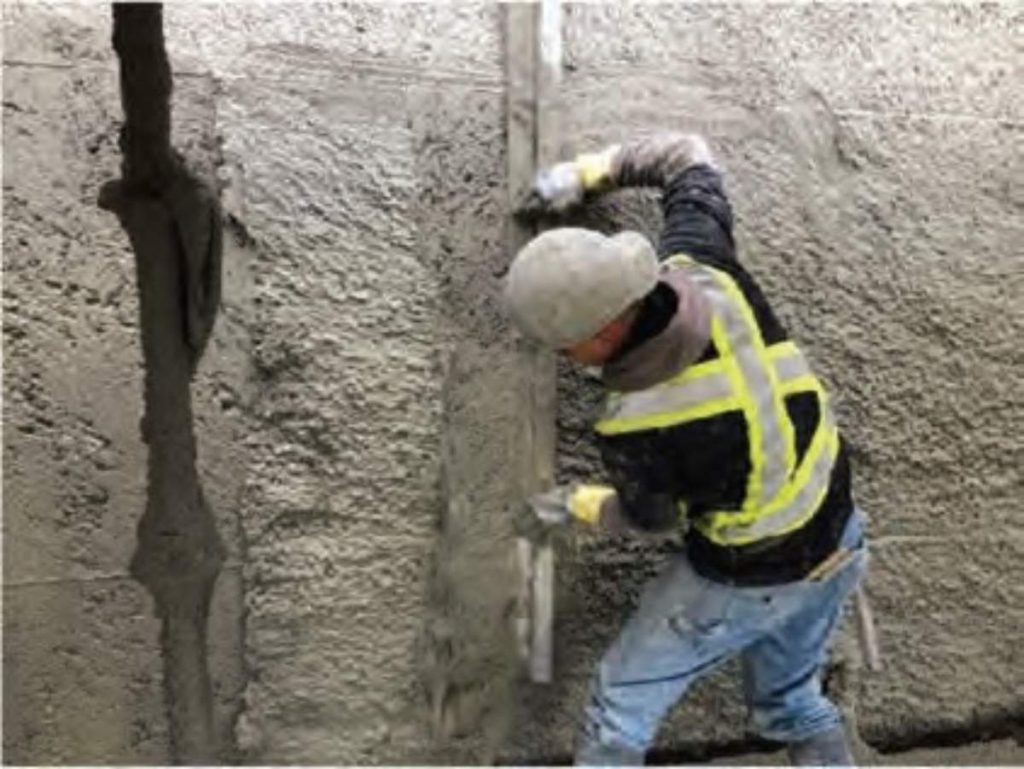
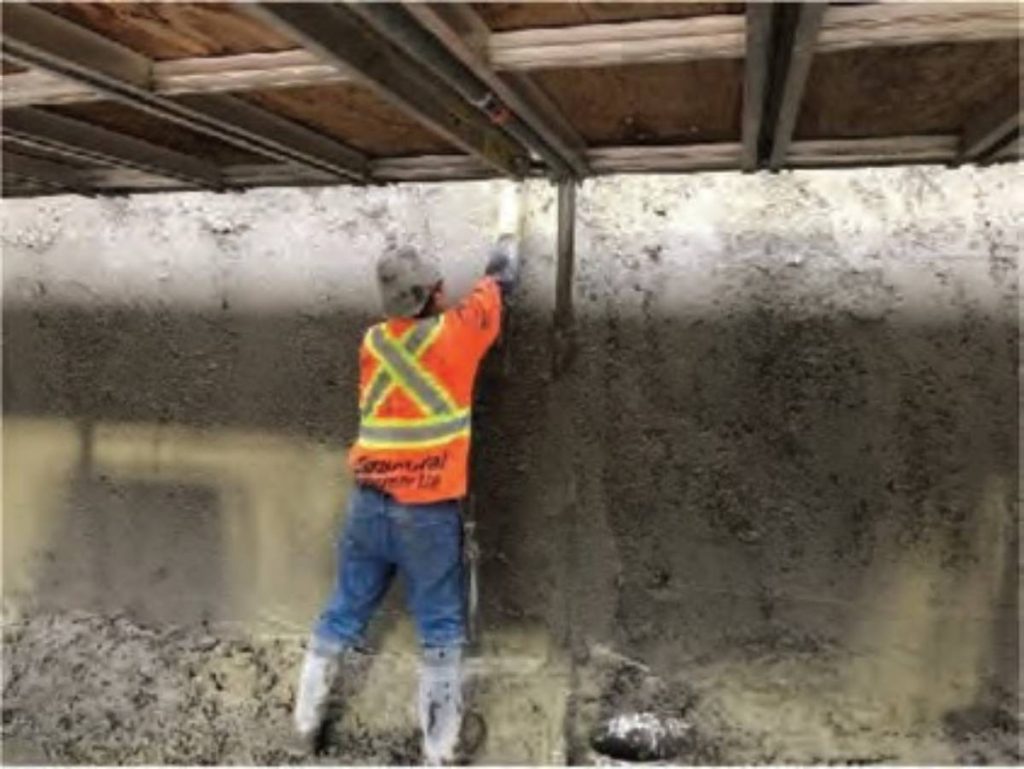
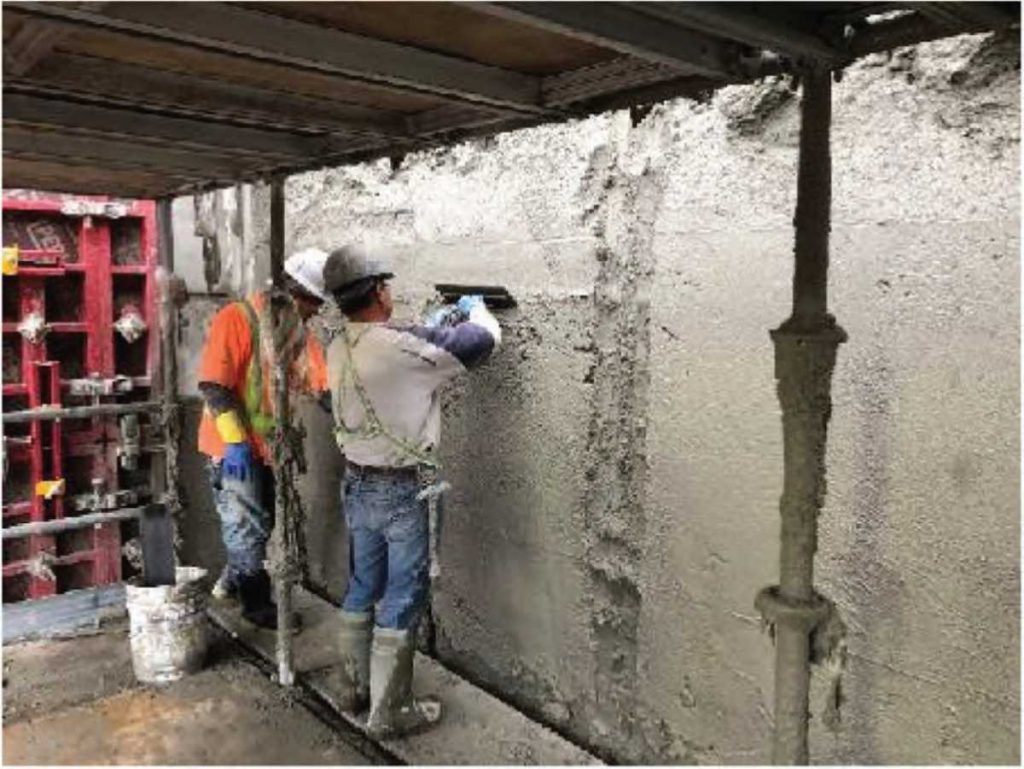
Desarrollo de la temperatura del muro de shotcrete masivo
Justo después de que se completó la instalación del hormigón proyectado, se pasó agua fría a través de la tubería de enfriamiento por aproximadamente 10 días. Sin embargo, las mantas térmicas no se instalaron hasta 53 horas más tarde debido a temas con la planificación del sitio de construcción. Los datos de la temperatura se descargaron en aproximadamente cuatro días (90 horas), luego de las cuales, el aparato que registró la temperatura se dañó.
La información detallada del desarrollo de la temperatura para el muro de shotcrere se incluyó en la figura 22.
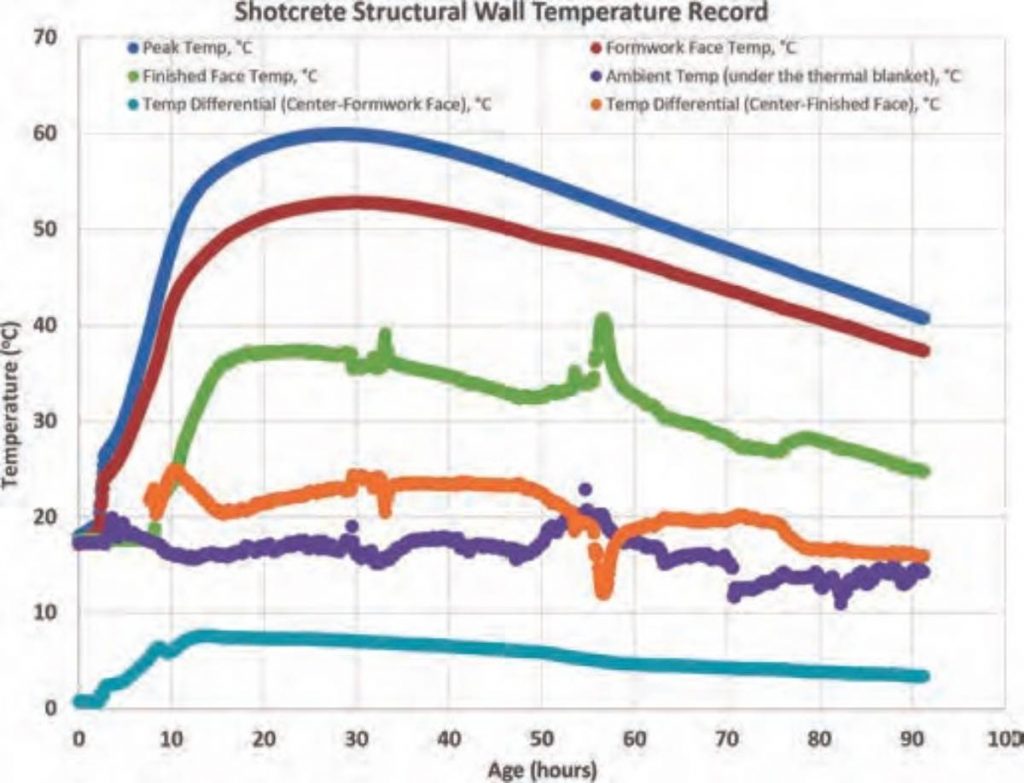
La temperatura más alta en el centro del muro fue de 60°C y cumplió con la temperatura máxima especificada permitida, también de 60°C. El diferencial de temperatura entre el centro y la cara del encofrado fue menor a los 20°C. La temperatura ambiente osciló entre los 15° y los 20°C durante las primeras 50 horas. Sin embargo, el diferencial de temperatura entre el centro y la cara acabada del muro tuvo rangos que oscilaron entre los 20° y 25°C en las primeras 50 horas, para luego caer bajo los 20°C. Esto se atribuyó al hecho de que las mantas térmicas no se colocaron hasta después de las 53 horas, contraviniendo el plan de control térmico. Típicamente, cuando el diferencial de temperatura excede los 20°C, se requiere de un análisis de esfuerzo para determinar si el esfuerzo térmico sobrepasa el 75% de la resistencia a la tensión.
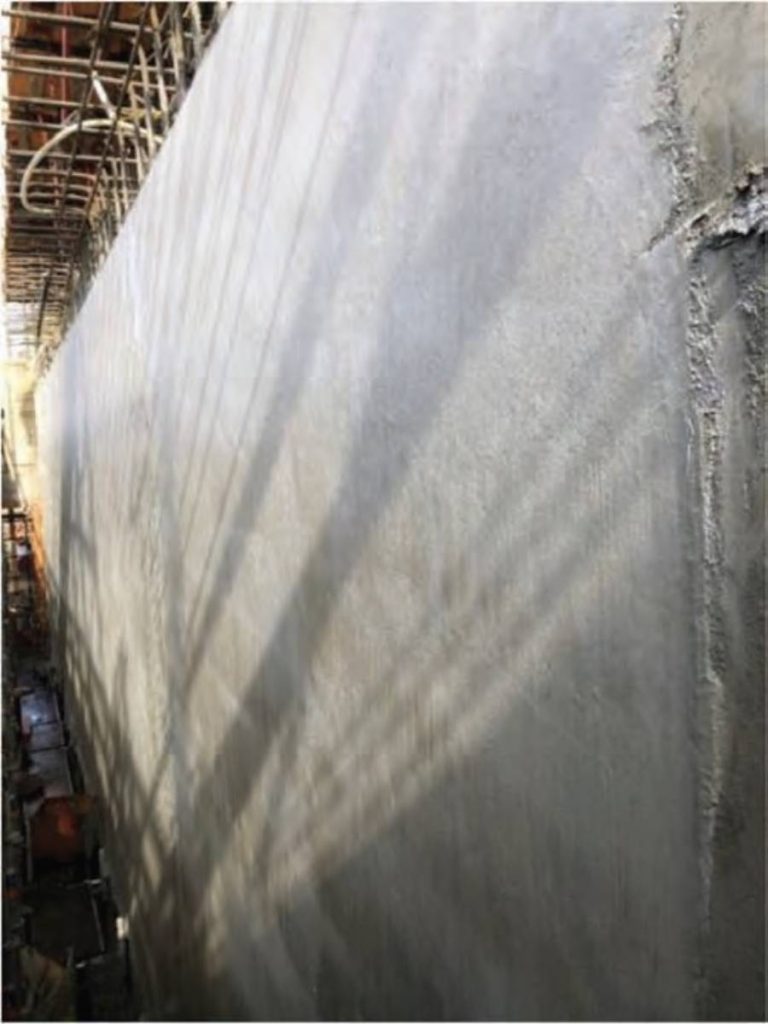
El remodelado post vertido y el análisis de esfuerzo se realizaron con un modelo finito 3-D y los resultados se incluyeron en la Tabla 3.
Se hizo presente que, debido a la planificación de obra, los ensayos para resistencia a la tensión y a la deformación por fluencia lenta no se condujeron para obtener los parámetros para el análisis de esfuerzo. Se utilizaron parámetros de una mezcla con resistencia a la compresión, módulo de elasticidad y deformación por fluencia lenta similares para el análisis del esfuerzo térmico. Los resultados del análisis de tensión mostraron que el esfuerzo térmico versus la ratio de resistencia a la tensión es de 59%, lo que es menos que 75%, al que se considera como un alto potencial para fisuraciones térmicas.
Si bien no hubo datos de temperatura registrados después de las 90 horas, la tendencia de la temperatura en su punto más alto, cara del encofrado y cara del acabado, todas descendieron bajo los 20°C después de las 90 horas. Con una temperatura ambiente de 10° a 25°C, el diferencial de temperatura estuvo dentro de los 20°C hasta 10 días después de la instalación de las mantas térmicas, cuando finalizó el Plan de Control Térmico.
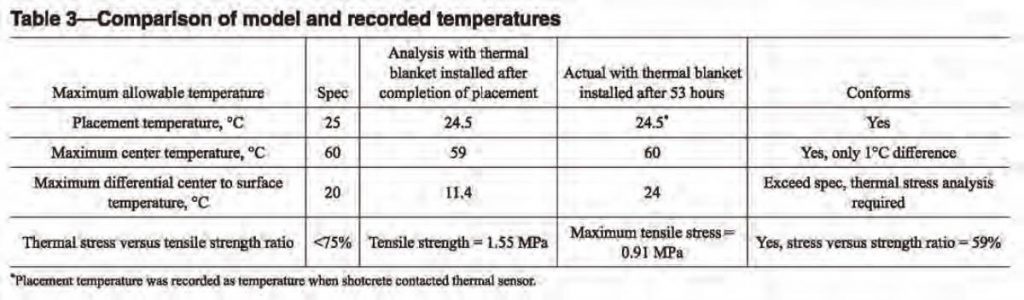

Se realizó una inspección posterior a la construcción del muro, una vez que se sacaron las mantas térmicas. La condición de la superficie de la cara acabada se muestra en las figuras 23 y 24. No se observaron fisuraciones térmicas.
Conclusiones
- La mezcla húmeda de shotcrete con 40% de escoria se aplicó de manera exitosa para la construcción de un muro de shotrete masivo armado de 1 metro de grosor, utilizando el método de disparo de alta precisión. Se logró una encapsulación apropiada del refuerzo, de tamaño hasta 25M y empalmado paralelo.
- El shotcrete recubrió los tubos de enfriamiento sin provocarles daños.
- El hormigón proyectado resultó ser eficiente para construir el muro estructural masivo.
- Se implementó un Plan de Control Térmico. La temperatura peak cumplió con el requerimiento especificado para una estructura de hormigón masivo. El diferencial de temperatura entre el centro y la superficie acabada sobrepasó los requisitos especificados hasta en 50 horas, pero una inspección posterior al vertido confirmó que no se observó fisuración térmica.
- La temperatura registrada y la temperatura modelada, ajustada con las condiciones de construcción actuales, estuvieron muy cercanas, con menos de 1°C de diferencia en la temperatura más alta. Esto muestra que el modelo con elemento finito en 3-D utilizado en el proyecto es capaz de modelar, de forma precisa, el desarrollo de la temperatura de la mezcla y el proceso de construcción con hormigón proyectado.
En síntesis, el shotcrete resultó un éxito en su aplicación al muro estructural, cumplió con los requisitos de desempeño especificados para el proyecto en cuanto a resistencia a la compresión, absorción de la ebullición y volumen de permeabilidad de los vacíos, y la calidad del muro de hormigón proyectado masivo resultó satisfactoria, sin fisuras térmicas a la vista.
Recomendaciones
Pensando a futuro, el shotcrete se utiliza cada vez más para la construcción de complejas estructuras de hormigón con complicados detalles en su armadura. Esto incluye a gruesos muros, vigas, columnas y otros componentes estructurales que pueden clasificarse como hormigón masivo. Recientemente, el ACI 308 incluyó al hormigón proyectado dentro del código de construcción (6). La implementación de planes de control térmico para estas estructuras de shotcrete masivo será crítica para cumplir con los requisitos de diseño estructural y de vida útil de dichos elementos. Este documento entrega principios generales una metodología detallada para ingenieros diseñadores que consideran la construcción de componentes estructurales de shotcrete masivo. Involucra diseño estructural, diseño de mezcla, un plan de control térmico, maqueta y calificación, prueba de control de calidad e inspección de la obra y una inspección post vertido. Con los esfuerzos apropiados de los ingenieros diseñadores, ingenieros de hormigón/shotcrete, contratistas y hormigoneras, los componentes de shotcrete masivo estructural podrán construirse de manera adecuada para cumplir con los requisitos de vida útil y las especificaciones propias del proyecto (5). Los autores continúan realizando más investigación en esta materia, incluyendo ensayo de comportamiento térmico de los materiales del shotcrete y modelado de estructuras de shotcrete masivo con medidas de control térmico optimizadas.
Para diseñar estructuras de shotcrete masivo, se recomienda seguir los siguientes principios:
- Especificar las propiedades mecánicas del shotcrete, incluyendo la resistencia a la compresión, módulo de eslasticidad, resistencia a la flexión, resistencia al corte y con fibras, resistencia a la tensión residual.
- Constructabilidad con shotcrete. Un diseño de mezcla apropiado del hormigón proyectado debe someterse a pruebas y ensayos. El alza de la temperatura adiabática debería desarrollarse basada en los ensayos de la mezcla.
- El modelado térmico debiese conducirse de acuerdo con lo que se desarrolló en el Plan de Control Térmico. El Plan de Control Térmico debería especificar la máxima temperatura que se puede permitir en la estructura, la que normalmente es menor a los 60°C, y con un diferencial de temperatura entre el centro y la superficie máximo permitido de menos de 20°C. Si el diferencial de temperatura excede los 20°C, debe realizarse un análisis de esfuerzo térmico para determinar si el esfuerzo versus la ratio de resistencia supera el 75%. Si lo hace, existe un alto potencial para el desarrollo de fisuras térmicas. Los medios y metodologías para medidas adecuadas que disminuyan el riesgo de fisuración térmica incluyen, pero no se limitan, a la reducción de la temperatura de aplicación del shotcrete y el uso de mantas térmicas con un periodo de instalación más extendido, de ser necesario. Utilizar encofrados aislados, tuberías de enfriamiento y otras medidas, en caso de ser necesario. El especialista en shotcrete, el contratista y el ingeniero diseñador deben trabajar juntos para llegar con las opciones más eficientes y rentables para implementar el plan de control térmico.
- Deben testearse previo a la construcción el equipamiento para el shotcrete, la mezcla y la calificación del lanzador. El operador a cargo de proyectar el shotcrete debe tener la certificación de ACI para lanzadores. Durante los ensayos en la maqueta, debe seleccionarse el componente estructural con la sección más congestionada de las barras de refuerzo. Los testigos y/o ventanas de corte deben inspeccionarse de manera visual por un especialista con experiencia en hormigón proyectado tal y como lo plantean los requisitos de ACI y la especificación del proyecto. Al mismo tiempo, deben implementarse medidas de control térmico durante la etapa de maqueta. El propósito es calibrar los modelos térmicos y ajustar el plan de control térmico, de ser necesario.
- Luego de una inspección y ensayo satisfactorios de la maqueta del componente estructural, la estructura de shotcrete masivo puede construirse con los mismos materiales, equipamiento, lanzadores y equipo. El plan de control térmico debe ejecutarse instalando los suficientes sensores térmicos para monitorear el desarrollo de la temperatura de la estructura. El ingeniero debe revisar y registrar las temperaturas de forma oportuna y si lo requiere, implementar medidas de control térmico extras tales como la instalación de mantas térmicas adicionales, bajar la temperatura del agua, aumentar el flujo del agua en las tuberías de enfriamiento, entre otras medidas posibles.
- La inspección posterior al vertido debe conducirse por un especialista en hormigón para establecer si existe alguna fisura térmica. En caso de evidencias de fisuración térmica, el plan de control térmico debe revisarse y reformularse, basado en el curado actual y las condiciones de protección de la estructura. Se recomienda realizar una comparación entre la temperatura registrada posterior al vertido versus la temperatura modelada.
Referencias
- (1) Comité ACI 506, “Guía de Shotcrete (ACI 506R-I 6)”, American Concrete Institute, Farmington Hills, MI, 2016, 8 pp.
- (2) Comité ACI C660, “CP-60 Libro del trabajador para la Certificación ACI del lanzador de shotcrete”, American Concrete Institute, Farmington Hills, MI, 2015, 120 pp.
- (3) Zhang, L.; Morgan, D. R; y Mindess S., “Evaluación comparativa de las propiedades de transporte del shotcrete comparado con el hormigón colocado in-situ”, AC/ Materials Journal, V. 113, No. 3, May-June 2016, pp. 373-384.
- (4) Zhang, L., “Contenido de aire en el shotcrete: proyectado vs. apilado”, Shotcrete, Winter 2012, pp. 50-54.
- (5) Zhang, L., “President’s Memo”, Shotcrete, Winter 2019, pp. 4-5.
- (6) Hanskat, C.; Holland, T. C.; y Suprenant, B. A., “Shotcrete incorporado dentro del código de construcción ACI 318-19”, Concrete International, V. 41, No. 12, Dec. 2019, pp 31-35.