Este sistema estructural único combina al diseño de armazón con el de muro. Este artículo se publicó originalmente en la revista Structure Magazine, y detalló el diseño estructural de un pabellón construido con tecnología de hormigón impreso 3D.
Autora: Grace Melcher (Máster en Ingeniería Estructural del Massachussets Institute of Technology (MIT), Program Manager en ICON).
Frecuentemente en la industria de la construcción, la velocidad, asequibilidad y escalabilidad tienen como costo la belleza y funcionalidad. En marzo de 2023, la empresa tecnológica de construcción ICON se asoció con el Long Center for the Performing Arts, el estudio de arquitectura Bjarke Ingels Group (BIG) y Liz Lambert para construir el “Pabellón Cósmico” en Austin, Texas, el primer escenario para espectáculos que se fabrica con tecnología de impresión 3D.
Uno de los mayores beneficios de la tecnología de Impresión 3D es la velocidad. Los métodos de construcción tradicionales a menudo requieren de un diseño y abastecimiento que consume tiempo, pero con la tecnología de Impresión 3D, se pueden acelerar los procesos constructivos. Esto no sólo significa un ahorro en tiempo, sino también, permite controlar los costos asociados a la mano de obra y los materiales. Adicionalmente, la reducción de residuos de material es una ventaja importante en una industria cuyo foco hacia la sostenibilidad crece día a día.
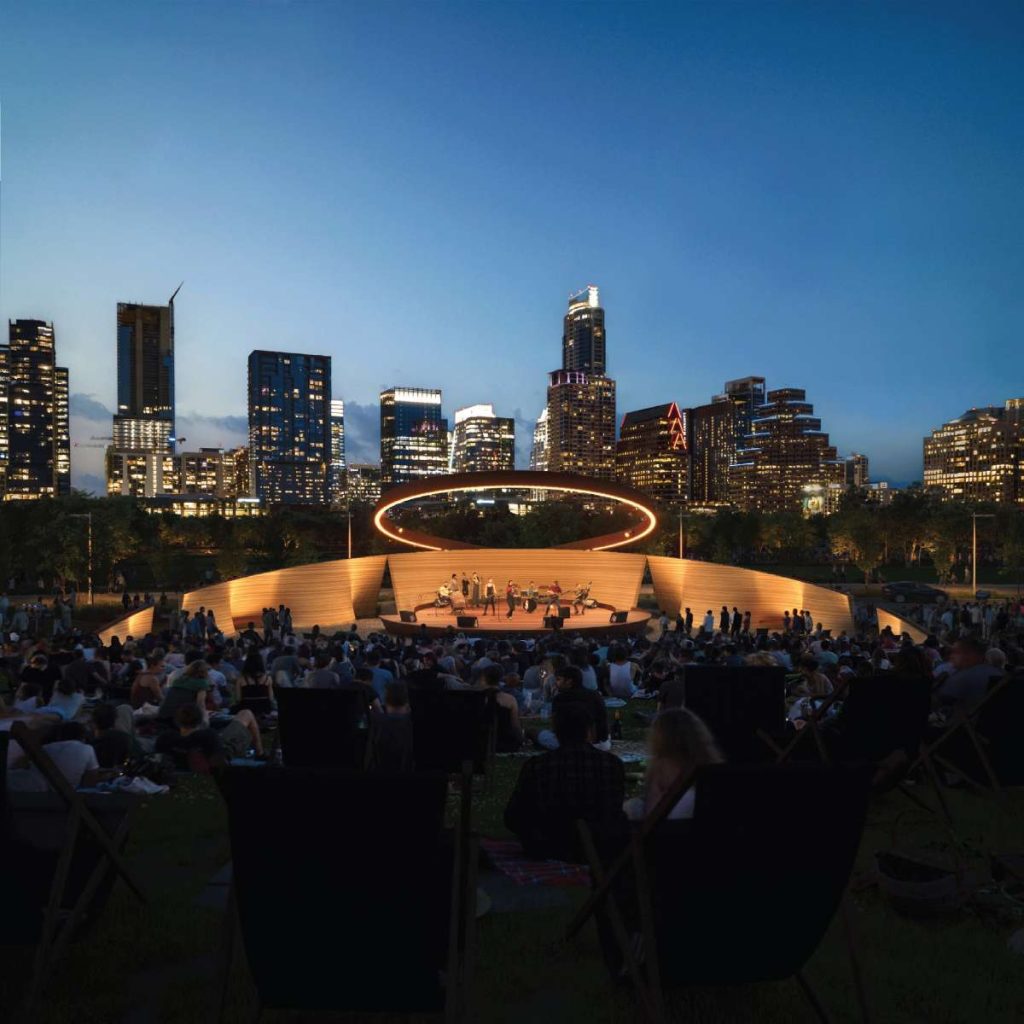
La personalización es otro de los grandes beneficios que tiene la tecnología de Impresión 3D. La habilidad de crear diseños complejos e intrincados abre un mundo de posibilidades tanto para los arquitectos como para los ingenieros diseñadores. Las estructuras pueden adaptarse para cumplir con solicitaciones específicas y preferencias estéticas, permitiendo una mayor creatividad y flexibilidad en el proceso constructivo sin alterar los costos.
Una implementación de la construcción con tecnología de Impresión 3D es utilizar un enfoque integrado verticalmente. ICON utiliza este método y combina la robótica (tanto en el diseño como en la producción), software, ciencia de los materiales y la arquitectura para proporcionar un flujo de trabajo continuo y una ejecución estructural precisa.
Para “imprimir” el pabellón, se utilizó el robot de deposición de materiales de ICON bautizado como “El Volcán”. Este robot de 4,5 x 14 x 40 metros opera en el plano cartesiano y viaja sobre sus rieles en el eje Y, permitiendo una deposición del material precisa. El material registrado que se utilizó en el proceso de impresión se denomina Lavacrete. Lavacrete es un grout cementoso de 2-3,5ksi que tiene una combinación específica de árido fino y cemento. Este material se entrega desde Magma, que es el sistema de manejo y dosificación de Lavacrete, equipado con un mixer y un mecanismo de entrega por bomba.
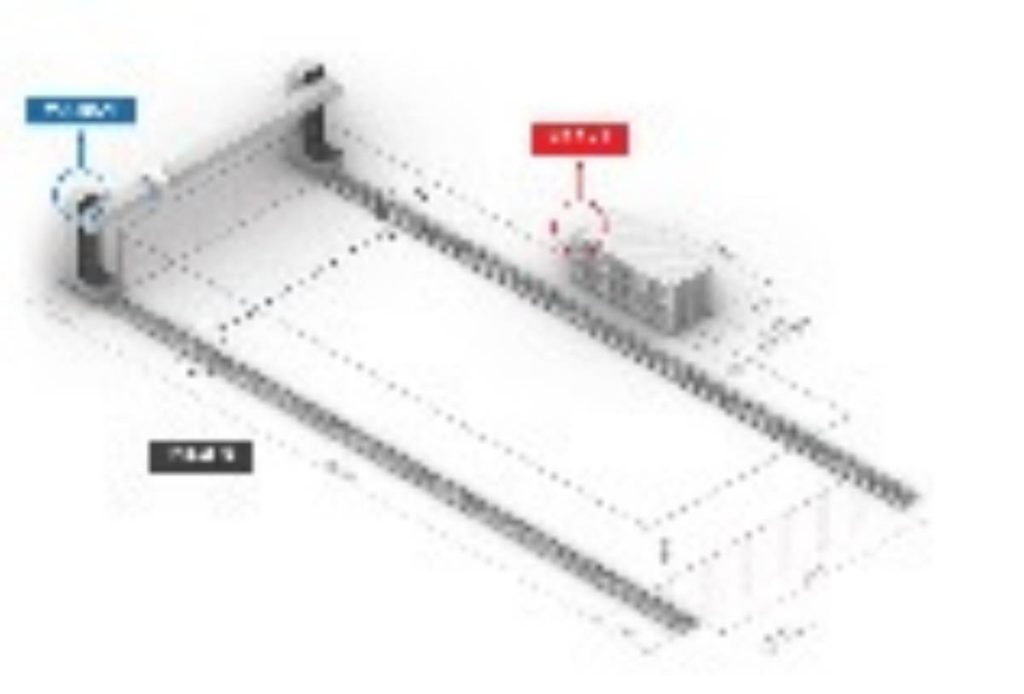
Diseño del “Pabellón Cósmico”
Diseñado en asociación con el estudio de arquitectura BIG, el “Pabellón Cósmico” se inspira en los temas de diseño arquitectónico planificados dentro de la futura expansión del desarrollo “El Cósmico”, ubicado en Marfa, Texas. El Pabellón es una superficie curva ondulada que actúa como punto de referencia, escenario y espacio de reunión para la cultura y la comunidad de Austin.
Uno de los aspectos más llamativos del “Pabellón Cósmico” es su geometría de forma libre. La estructura presenta múltiples capas de círculos y muros inclinados fuera del plano, creando un cautivador diseño visual que sería desafiante y costoso de lograr utilizando métodos constructivos tradicionales. La deposición natural del material crea naturalmente estrías en la impresión, lo que le da a la estructura una estética única de tierra compactada.
La impresión fue el elemento principal que permitió la expresión arquitectónica del “Pabellón Cósmico”. Desde la primera capa a la última, el proceso demoró sólo dos semanas, mientras que el diseño y la ingeniería para la obtención de los permisos, requirieron tres meses de preparación. Además, la confianza en los métodos constructivos automatizados y digitales guiaron soluciones ingenieriles creativas. El “doble digital” -o ruta de impresión- utilizado para dirigir a “El Volcán” hacia dónde depositar el material permitió la fabricación de barras de refuerzo geométricamente precisas.
También, posibilitó una transición sencilla hacia otras herramientas analíticas que ayudaron aún más al diseño estructural. La metodología de impresión aprovechó la ventaja de fabricar voladizos de punta a punta en tiempo real, evitando el uso de encofrados y reduciendo así costos, tiempo y disposición de residuos.
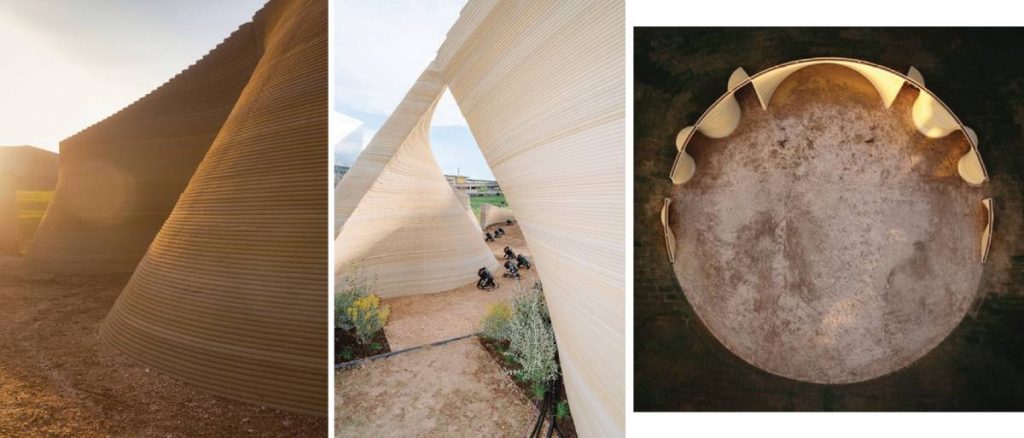
Desafíos
Hubo varios desafíos en la impresión de la geometría ondulada y elevada del Pabellón. El desafío del voladizo de cordón a cordón en tiempo real requirió de una serie de enfoques para superarlo.
Uno de los principales desafíos de la extrusión cementosa es esta limitación del ángulo en voladizo. A diferencia de la fabricación de aditivos polímeros a pequeña escala, la extrusión cementosa carece de capacidad de tensión entre los enlaces extruidos. Esta limitación se transforma en un obstáculo importante cuando se intentan realizar diseños elevados sin sistemas de soporte adicionales tales como el encofrado.
Para comprender la solución espacial del Pabellón, se utilizó la literatura existente sobre soluciones clásicas de mampostería. El ángulo interno de fricción y cohesión del material es lo que principalmente determina el ángulo máximo del voladizo en cualquier objeto cementoso impreso 3D. Normalmente, una limitación de ángulo común está alrededor de los 25 grados desde la vertical. Exceder este ángulo puede llevar a pandeo plástico, colapso plástico e inestabilidad estructural. Para conseguir el diseño del Pabellón sin encofrados costosos y poco productivos, se formuló una solución específica para mitigar las fallas comunes en voladizos.
El límite elástico de los morteros es distinto a cero, incluso en estados frescos y verdes. En su estado fresco, Lavacrete tiene suficiente resistencia elástica para apoyarse en sí mismo y resistir el colapso plástico en condición vertical. Sin embargo, la condición en voladizo provoca mayor esfuerzo en el material que si estuviese en una posición horizontal estándar.
Para superar esto en el Pabellón, se ejecutaron propiedades reológicas y una estrategia de operaciones que se basó en una coordinación precisa y coordinada. Esto permitió que el material ganara mayor límite elástico y de este modo, el ángulo interno de fricción de Lavacrete disminuyó previo a su deposición. Manipular estas propiedades del material permitió mejorar el ángulo máximo del voladizo y prevenir una falla por colapso plástico.
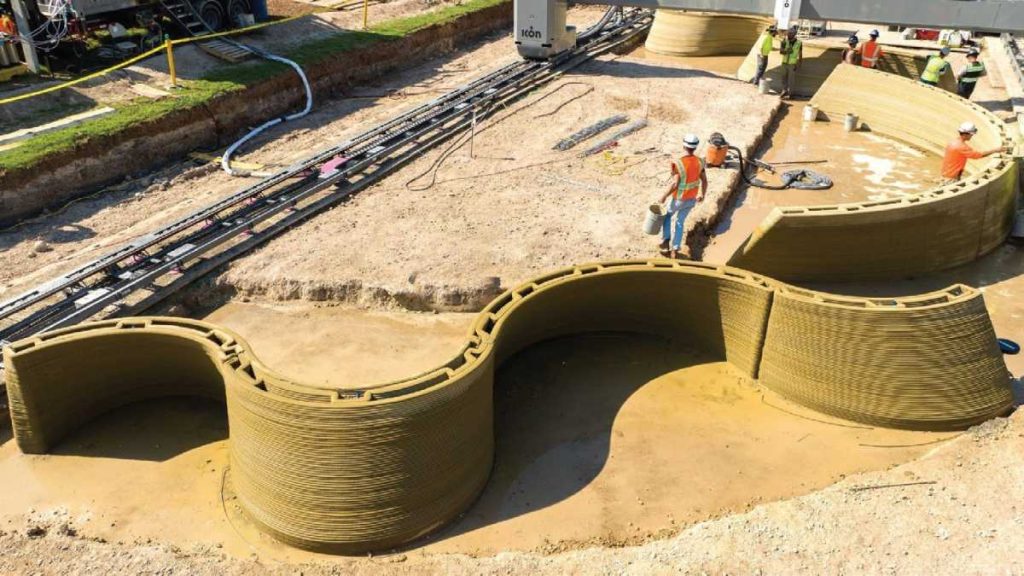
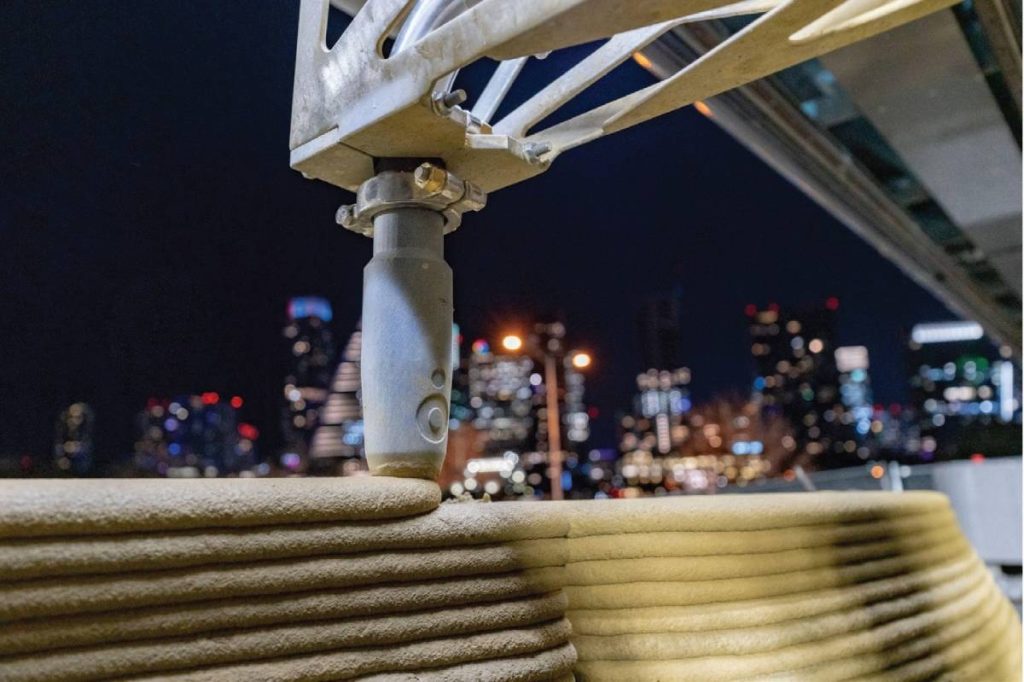
Adicionalmente, se empleó una estrategia de refuerzo utilizando alambre de acero. La tensión sobre la interfaz cordón a cordón y el corte global fuera del plano que provocó el voladizo crearon un mayor riesgo de pandeo elástico. El refuerzo con alambre (9 de espesor) se colocó entre los cordones en dirección longitudinal cada dos capas en áreas donde la estructura excediera el límite de falla vertical de 25 grados.
Esto reforzó el corte durante la fase verde del material y soportó a la estructura durante el proceso de curado. Al aumentar la resistencia de corte individual de los cordones, ICON pudo conseguir un ángulo de voladizo de 35 grados desde la vertical, sin alterar la forma de los cordones.
Otro aspecto que jugó un rol crucial para superar el desafío de la inestabilidad fue la tasa de construcción. La tasa de construcción es un factor significativo en cualquier proyecto de Impresión 3D, especialmente cuando se lidia con diseños en voladizo. La longitud de la ruta de impresión en una escala constructiva puede ser extensa y este hecho hace que sea más fácil superar la relación entre el peso propio de las capas adicionales y el desarrollo de resistencia elástica del material.
Estructura
El diseño estructural del “Pabellón Cósmico” combina elementos y principios de diseño tanto de armazón, muros y vigas. La estructura del “Pabellón Cósmico” evoluciona dinámicamente tanto horizontal como verticalmente, estéticas de alta calidad y funcionalidad. Los elementos clave del diseño estructural incluyen núcleos inclinados, una viga de unión escalonada y un diseño robusto de armadura y refuerzo.
El sistema estructural principal se compone de núcleos conectados a una viga de unión escalonada superior y una viga de unión plana inferior. Estos núcleos verticales se crearon por vacíos incluidos en el patrón de impresión dentro del muro hueco. Luego de imprimir, se colocaron las barras de refuerzo verticales en estos núcleos; luego, el ingeniero estructural los revisó para control de calidad. Finalmente, se rellenaron con Lavacrete utilizando a la impresora “El Volcán”. Estos núcleos siguen el perfil del Pabellón, el que ondula entre los -35 y 35 grados. Esto provocó que los núcleos se inclinasen en algunas zonas.
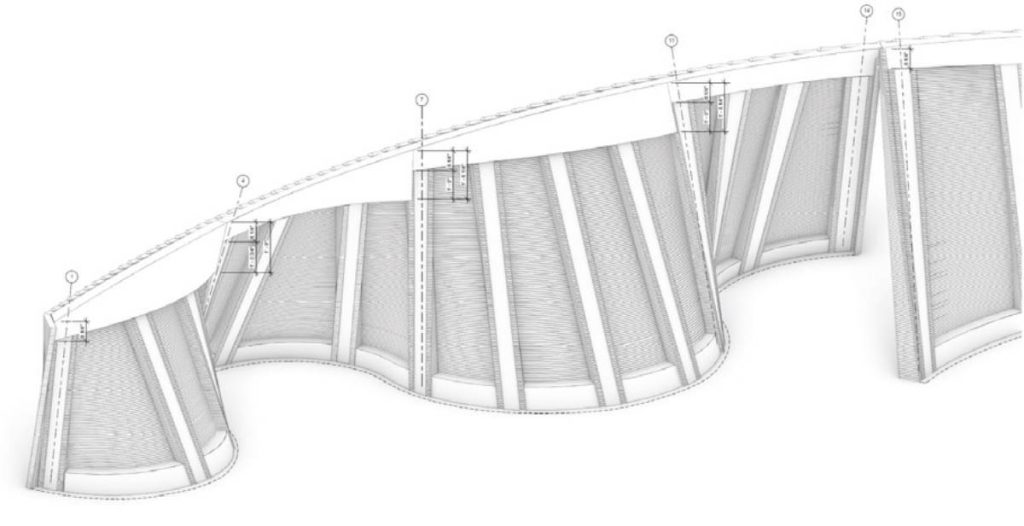
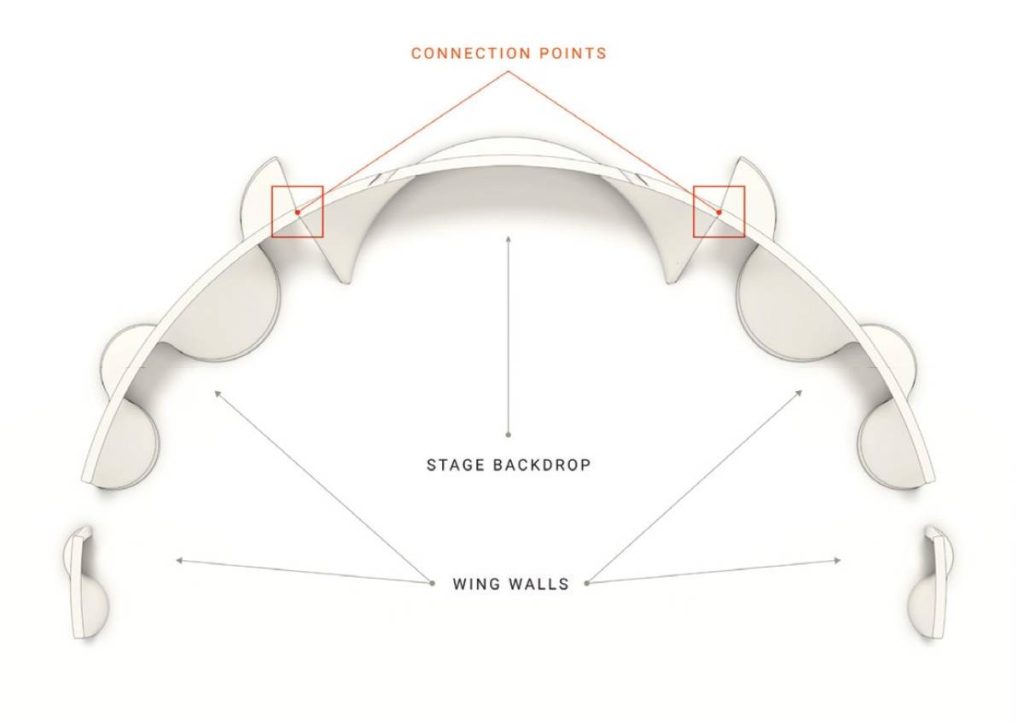
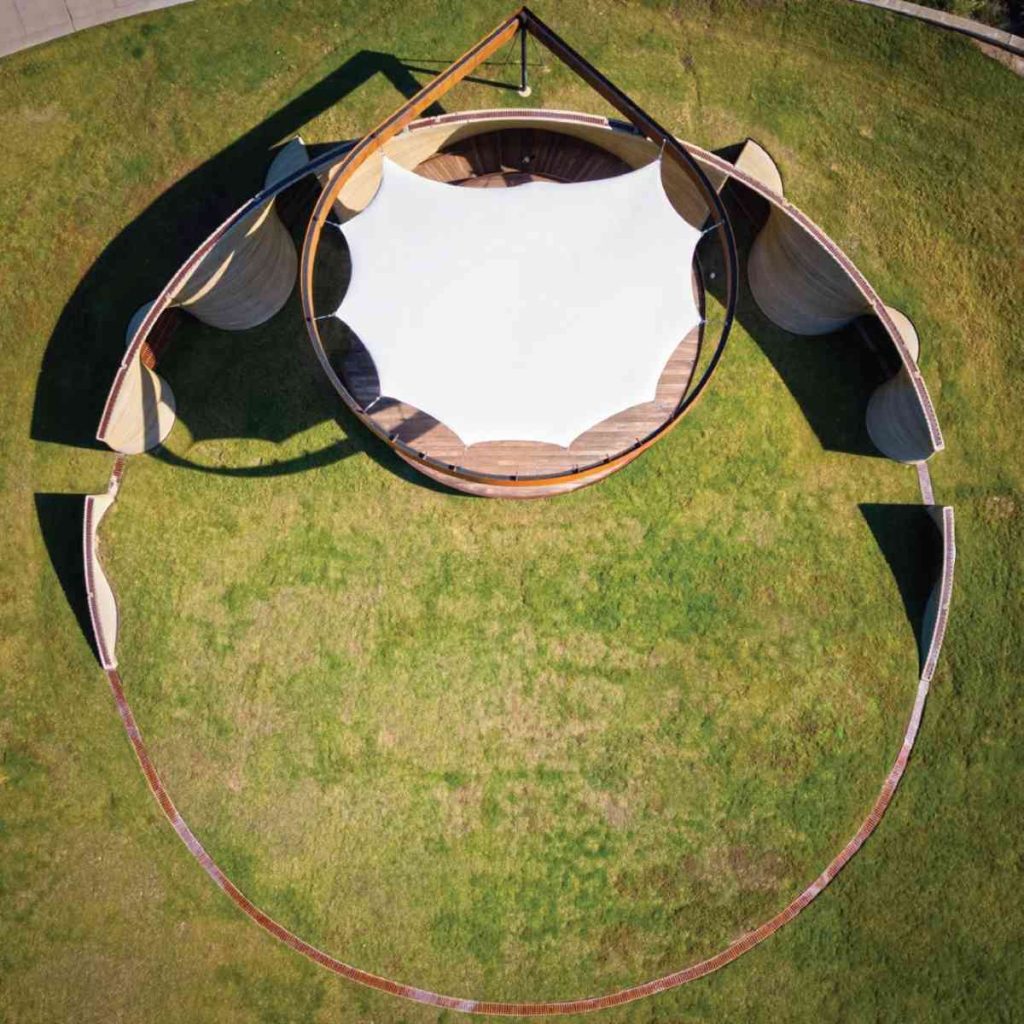
Debido a que la línea superior de la geometría desciende en la punta de las alas para abrazar a la tierra, la viga de unión superior está escalonada en secciones para apuntalar a la línea superior. El refuerzo consiste en largas barras en los núcleos y las vigas de unión superior e inferior, con barras más pequeñas colocadas de manera longitudinal entre los cordones durante el proceso de impresión.
El “doble digital” antes mencionado permitió prefabricar y doblar formas exactas de barras para hacerlas coincidir con la geometría impresa. Junto con el refuerzo de barras, un punto de unión de refuerzo se encuentra en la conexión entre el fondo del escenario y los muros laterales. Este punto de unión asegura estabilidad y continuidad estructural entre los tres muros. El Pabellón también incluye un anillo de halo alrededor de la parte superior de la geometría para iluminar y dar sombra al escenario en las presentaciones.
Para validar la integridad del Pabellón, como ocurre con cualquier estructura en la que el hormigón es el material principal, se llevó a cabo un plan de validación de ingeniería y control de calidad que se ejecutó durante toda la impresión. Se tomaron testigos y se ensayaron periódicamente para asegurar que la estructura alcanzó la resistencia a la compresión requerida. También se realizó un Análisis de Elementos Finitos (FEA, en sus siglas en inglés) en el diseño del Pabellón. Esta técnica computacional sirvió a múltiples propósitos, incluyendo:
- La validación de las mecánicas estructurales: FEA se utilizó para asegurar que la estructura cumpliese con los estándares de seguridad.
- Investigación del Punto de Conexión: Un foco específico del modelo FEA fue una investigación en el punto de conexión. Esta junta crítica requirió de un análisis cuidadoso para asegurar que podía resistir las cargas de manera efectiva.
- Análisis de Secuencia de Construcción: FEA jugó un papel protagónico en el análisis de la secuencia de construcción del Pabellón. Esto aseguró que la estabilidad se mantuviese durante el proceso constructivo, minimizando el riesgo de temas inconvenientes estructurales durante el ensamblaje.
FEA se llevó a cabo utilizando tanto elementos sólidos como huecos, permitiendo así una evaluación completa del sistema estructural del Pabellón. Al comparar varios enfoques, se creó un diseño estructural resiliente que puede resistir las fuerzas dinámicas en juego.
Conclusión
El Pabellón impreso 3D se alza como un símbolo de las posibilidades infinitas que la tecnología de Impresión 3D ofrece al mundo de la construcción y la arquitectura. Desafía las limitaciones tradicionales, une estética y funcionalidad y exhibe el inmenso potencial de las prácticas avanzadas de construcción robótica.
El “Pabellón Cósmico” desafía a la industria estructural a empujar las barreras, abrazar metodologías avanzadas y reimaginar lo que es posible. Es un símbolo del ingenio humano y la promesa de un extraordinario futuro en la construcción.