En este artículo, publicado originalmente por la revista Shotcrete Magazine de la American Shotcrete Association, se entregan detalles técnicos de la construcción de un skatepark en la isla de Barbados con hormigón proyectado, destacando la logística del transporte de los distintos elementos para la obra y el diseño de mezcla del material, que debía adaptarse a las condiciones climáticas del lugar.
Autor: Andy Duck, presidente de Artisan Skateparks.
Fuente: Shotcrete Magazine
Dedicación y persistencia
Las personas han viajado a la pequeña isla de Barbados para practicar surf en las permanentes olas que llegan desde el Atlántico, desde el tiempo en que los seres humanos conocieron el arte de montar sobre las olas. Esto mismo se puede decir del skateboard ya que ahora, la parroquia de Christ Church cuenta con un skatepark regional de hormigón. Este fue un proceso largo y exhaustivo, guiado por un consorcio de empresas y asociaciones, todas trabajando para brindarle a los barbadenses un skatepark de hormigón moderno a través de una planificación y un proceso adecuados. Todo comenzó con una llamada telefónica de Paul Wilson, un impulsor del skateboard local cuya incansable pasión estuvo siempre en entregarles a los jóvenes (de todas las edades), instalaciones adecuadas en Barbados.
Luego de varios años de apoyo a nombre de Paul y su creciente número de asociados, pares y skaters locales, el y su grupo crearon la Asociación de Skateboard de Barbados y consiguiente el reconocimiento del Ministerio del Deporte. ¡Ahora estaba organizados!
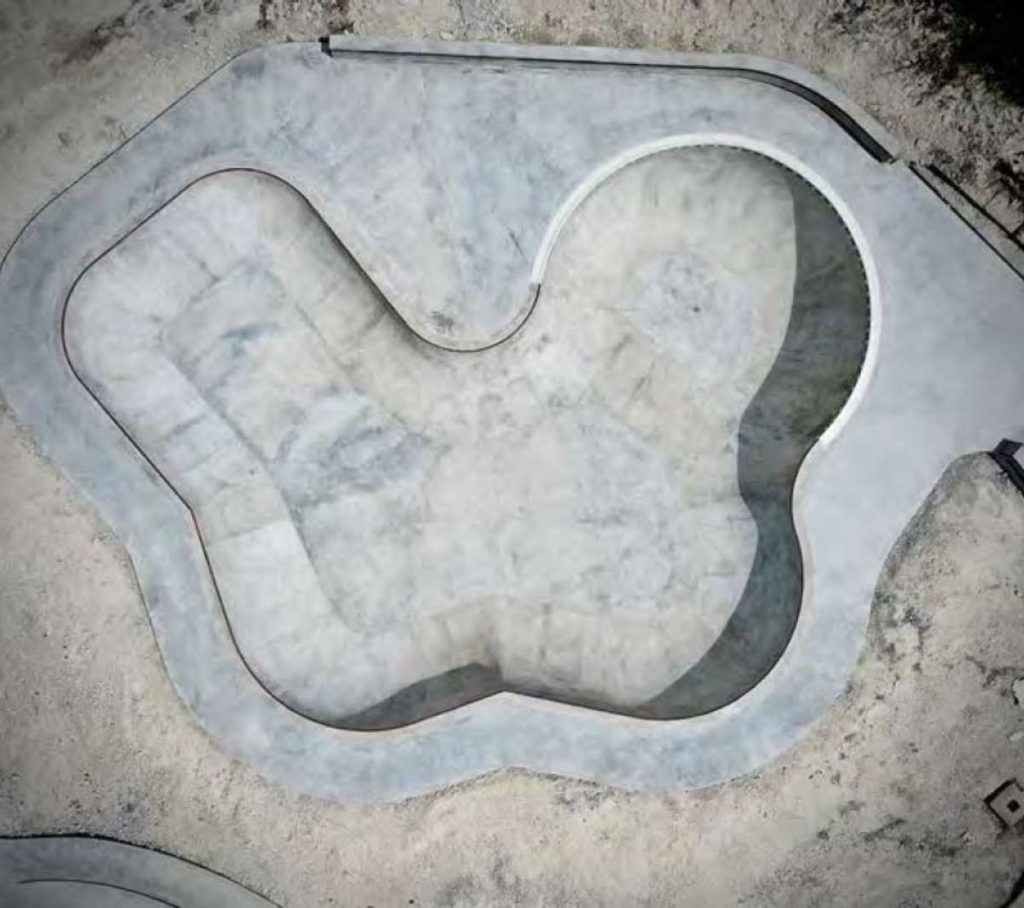
Con más años de dedicado trabajo, incluyendo un par de viajes para revisar sitios y los respectivos estudios de viabilidad, se conformó el equipo para el diseño y construcción del primer skatepark de Barbados. Para ello, se eligió a Pillar Design Studios, LLC, frecuente colaborador en el proceso de diseño y construcción, como el diseñador líder para los aspectos del skatepark que involucró al proyecto. Pillar desarrolló la documentación para la obra con la ayuda de una oficina de ingeniería estructural y civil local, Spencer Thorne. Una vez que Maria Holder Trust aseguró el financiamiento de la obra, la empresa Cooper Kaufman se encargó de la gestión del proyecto y la obtención de la oferta para la contratación general. Godson Builders se adjudicó el contrato y se eligió a Artisan Skateparks como el contratista, por su especialidad en la construcción de obras de este tipo.
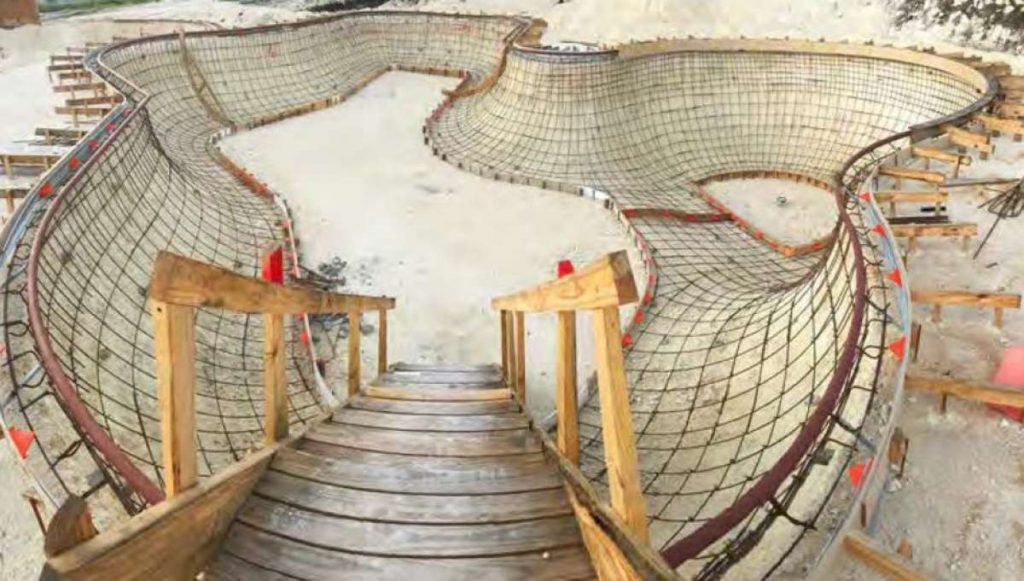
Como es la norma para la construcción de skateparks de hormigón, se especificó el uso de shotcrete como el método predilecto de colocación del hormigón para gran parte de este nuevo espacio. Cabe destacar que, por mucho tiempo, el hormigón proyectado es el método principal para la construcción de este tipo de obras. La habilidad para entregar una gran compactación y una completa encapsulación en armadura de refuerzo durante su colocación, entrega una gran adaptabilidad a las superficies onduladas típicas que presenta un skatepark moderno.
La planificación
En Estados Unidos, conseguir una gran experiencia de trabajo con el shotcrete toma un buen tiempo de planificación. Replicar esto en otro país, sin duda es llevar esa práctica a otro nivel. Aparte de la conversión métrica (de centímetros a pulgadas) y las potenciales interpretaciones tanto del lenguaje como de la idiosincrasia local, trabajar en otro país puede crear una serie de desafíos. Estos pueden abordarse a través de una extensa investigación de los materiales que estén disponibles en el mercado local, condiciones medioambientales (como temporadas de tormentas), procedimientos de los lotes, capacidades de plantas, volumen de transporte, los horarios relativos del tránsito y cuál es la mejor planta para proveer del shotcrete. Por suerte, este no fue el primer proyecto internacional de Artisan Skateparks.
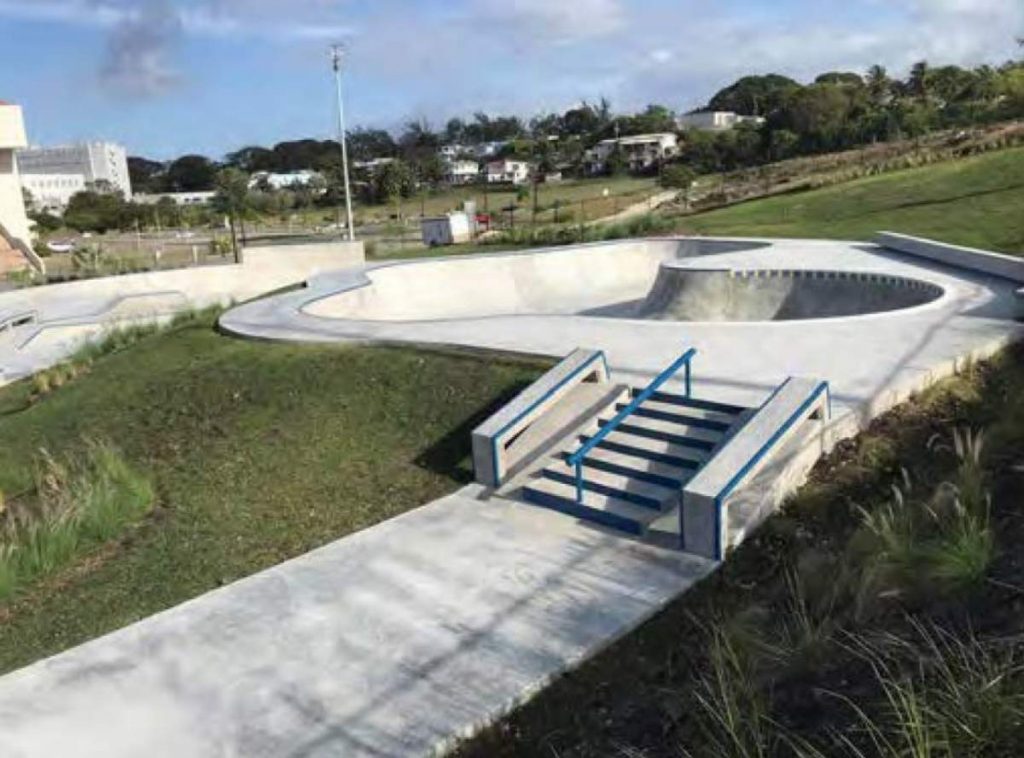
En primer lugar, se eligió a la empresa Ready Mix de Barbados como el proveedor principal de hormigón para el proyecto. Para el manejo de los múltiples elementos de la planificación se utilizó un buen número de correos electrónicos, llamadas telefónicas e incluso mensajes de texto (la forma de comunicación más popular en Barbados). La empresa a cargo de la construcción supo que la aplicación del shotcrete se realizaría bajo un clima cálido y por lo mismo, trabajó diligentemente junto con Ready Mix para encontrar un diseño de mezcla del hormigón que sirviese como base para la receta final del hormigón proyectado a utilizar en la obra. Las especificaciones arrojaron una mezcla de 4.000 lb/in2 (282,2 kgf/cm2) y 28 MPa de resistencia a la compresión a los 28 días, requerimiento que se logró con un aditivo reductor de agua y un estabilizador de la hidratación para facilitar las aplicaciones en climas cálidos.
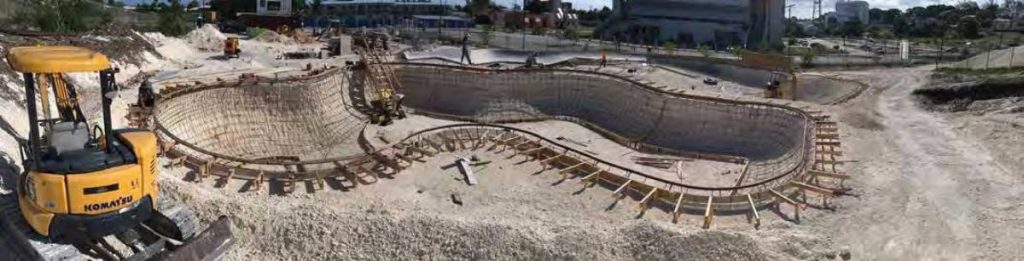
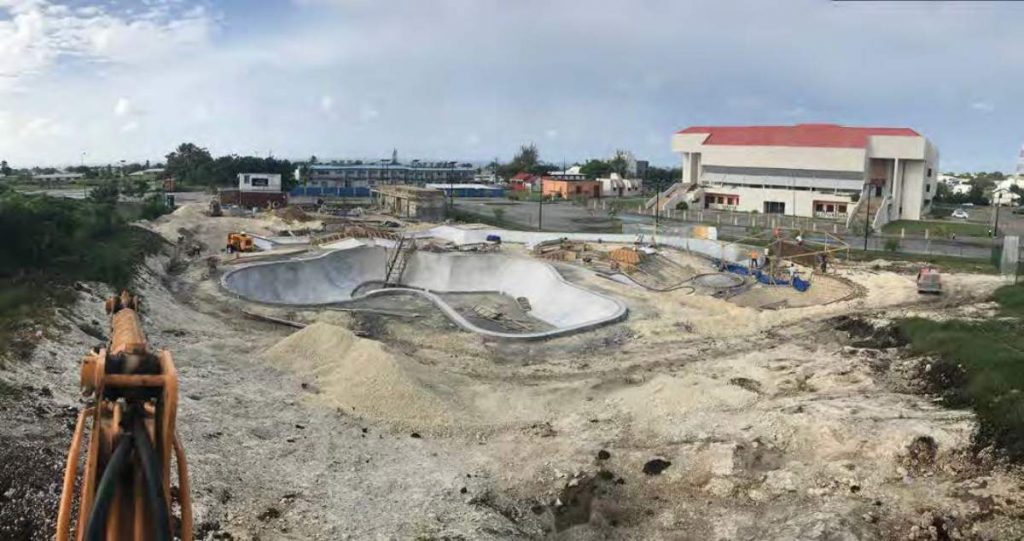
Las materias primas utilizadas fueron cemento Portland (según la empresa contratista, en los Estados Unidos, se usan puzolanas entre un 15% a un 20% para la mezcla) y todo el árido utilizado se encontró en forma de caliza chancada, lo que hizo que el contratista se preparara para un material con alta necesidad de hidratación y de fraguado rápido. A eso, durante el tiempo del trabajo en el proyecto se alcanzaron temperaturas históricas que iban de los 24,4°C en la mañana a los 32°C en la tarde, con humedad máxima todo el día.
Una vez analizadas las condiciones generales del viento en el sitio de la obra, junto con qué tan cerca se siente el sol cerca del ecuador, se buscó un proveedor de aditivos de experiencia comprobada para asegurar el éxito del proyecto. En ese sentido, explicó el contratista, se eligió a Sika por ya que existía un trabajo previo con el uso de aplicaciones para shotcrete en obras en Estados Unidos, además de tener una buena representación en la zona. Luego de varias discusiones sobre las condiciones de este proyecto, se eligieron las proporciones adecuadas para los aditivos y luego, se colocaron tambores de los productos junto con las herramientas para la obra y otros elementos en un container, para embarcarlas a Barbados.
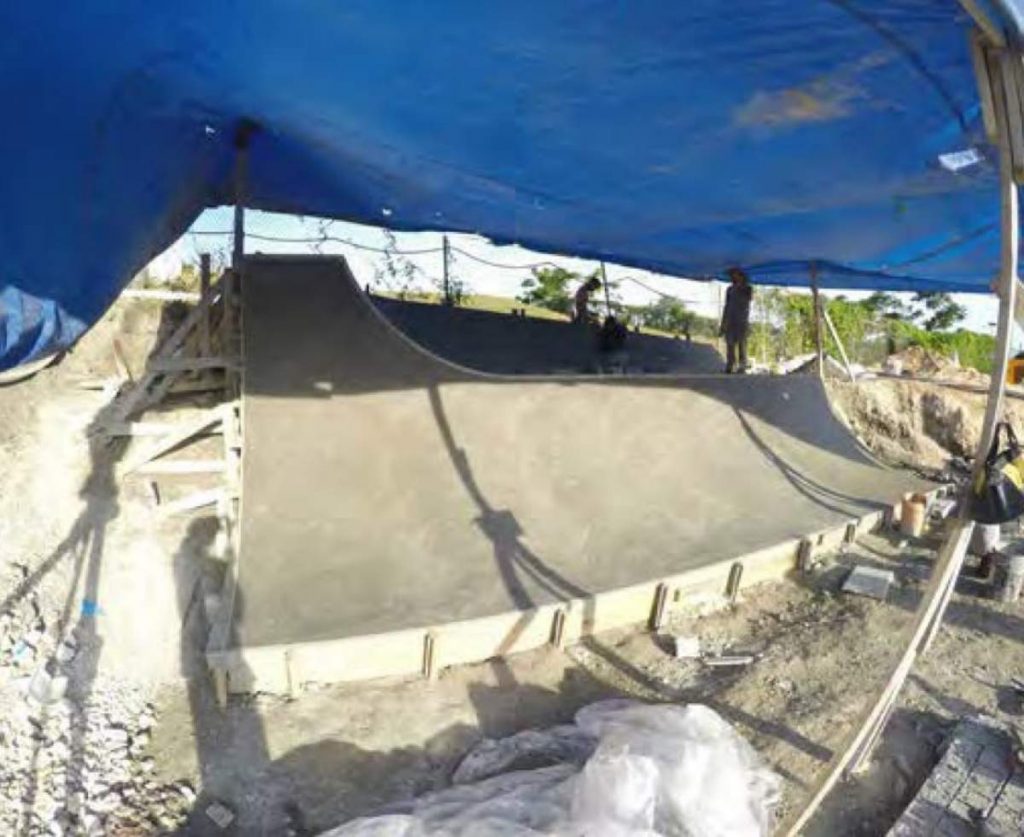
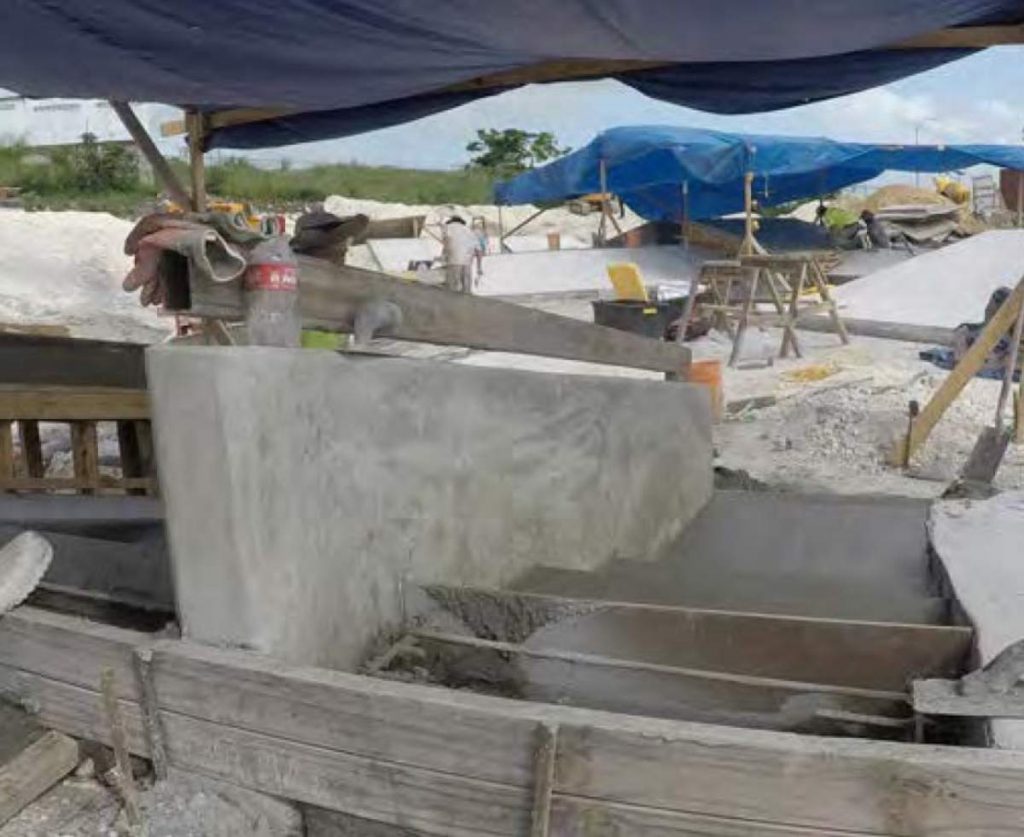
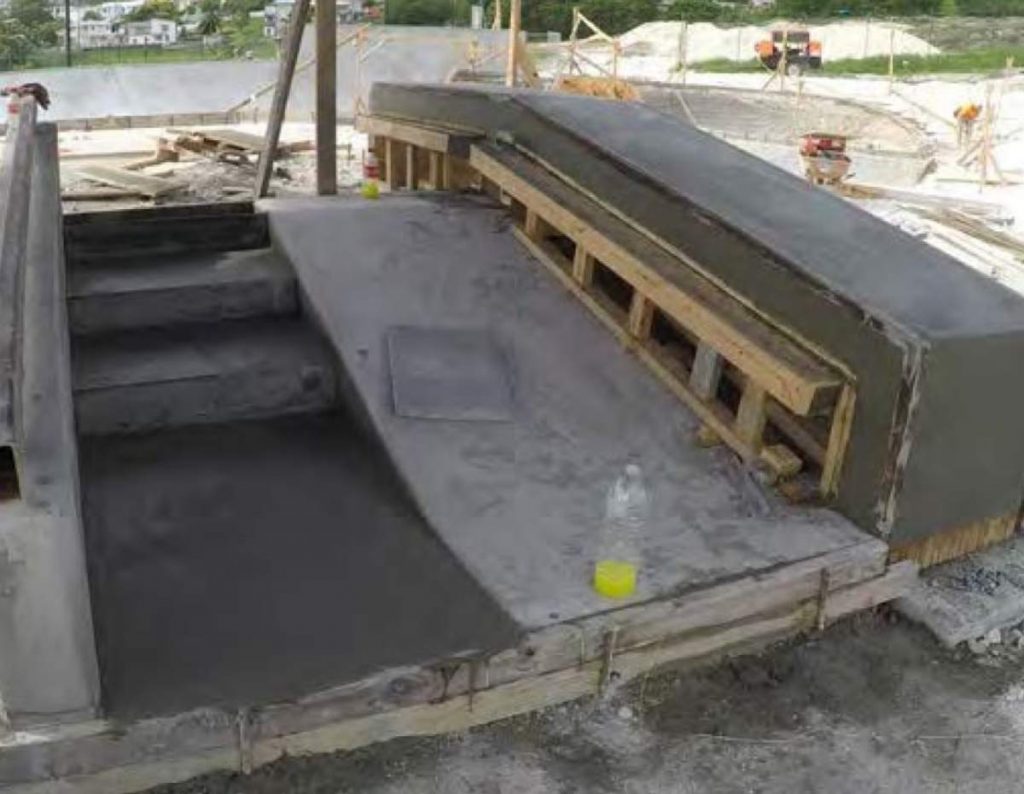
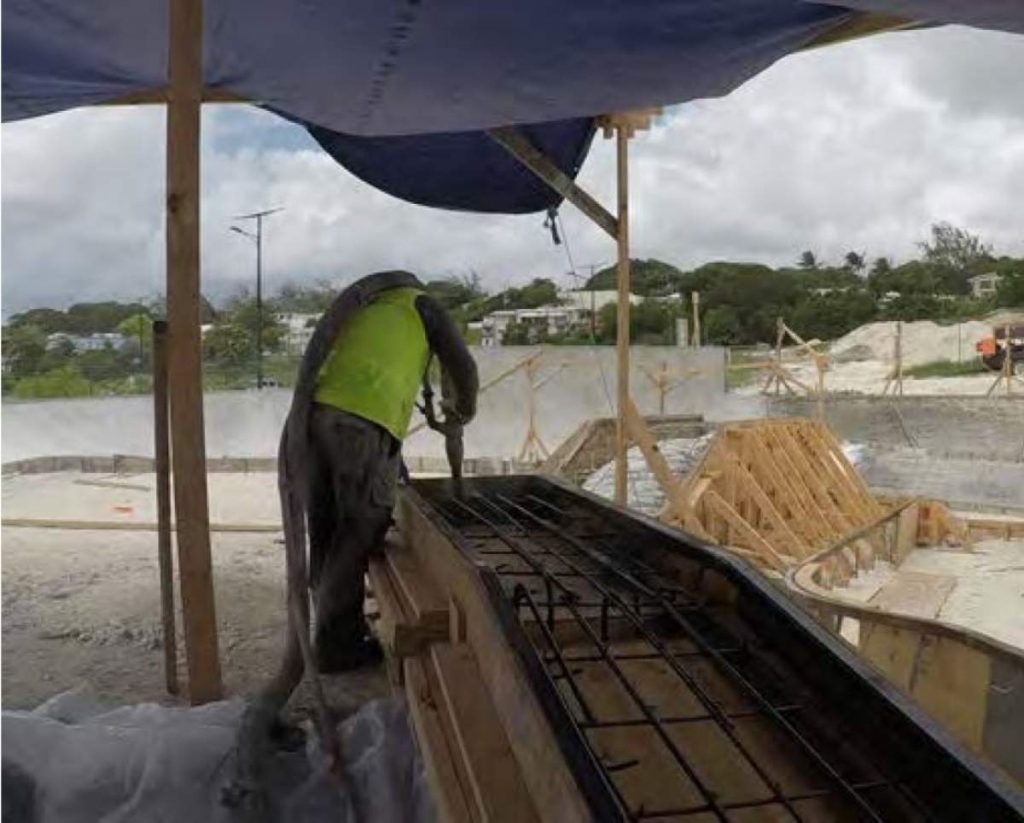
Antes de comenzar el proyecto, el contratista tuvo en consideración tres inconvenientes previos a la utilización de shotcrete en la isla. Desafortunadamente, nadie recordó qué tipo de proyectos o cuándo ocurrieron. Se estaban por embarcar alrededor de 260 m3 de shotcrete con una planta y un equipo que nunca habían experimentado esos inconvenientes. Para suerte del contratista, Godson Builders invirtió en una nueva bomba de hormigón REED A30 HP, equipo que la empresa utiliza desde hace una década. Esto permitió realizar una capacitación efectiva a nuestra cuadrilla sobre cómo operar la bomba y además, nos dio confianza en que el equipo de bombeo ejecutaría de forma correcta el trabajo.
El ambiente
La humedad se hizo sentir al instante en que el equipo de Artisan Skateparks llegó a Barbados. Asimismo, también se puedo apreciar cómo serían las condiciones de viento en la obra gracias al movimiento de éste en los árboles. También, el equipo notó que hubo una lluvia reciente, lo que se agregó a la alta humedad existente en el lugar.
Durante la visita al lugar de la obra, se conoció al equipo de trabajadores local y se tomaron nota de las condiciones climáticas específicas del sitio del proyecto. Se removieron todos los materiales orgánicos del espacio antes de la llegada del equipo y se acopiaron en una suerte de estante. Desde ahí, los contornos que forman la gradiente aproximada del plano se formaron con marga chancada. Se colocaron por capas, se humedecieron, compactaron y se dejaron en el sitio hasta que la obra comenzara.
Una vez trasladado el equipo humano y mecánico desde Estados Unidos, uno de los aspectos se estudió fue la marga como árido. Lo primero, es que ésta tiene una compactación tan densa que el equipo tuvo que realizar forados en el suelo para colocar ya sea fijaciones, estacas e incluso, clavos. En segundo lugar, el secado de la marga es muy rápido, lo que se puede considerar como bueno, teniendo en cuenta que en Barbados llueve casi todos los días. Sin embargo, y teniendo en consideración lo rápido que la marga iba a absorber el agua de la mezcla de hormigón, eso se transformó en un inconveniente importante. El acabado de los skateparks fabricados con shotcrete se realiza con una pala (típicamente, con unas palas tipo maní de 250 mm) de acero Clase A. Este proceso se lleva a cabo después de dar forma, de manera manual, a los contornos finalizados y detalles en el shotcrete recién colocado. El tercer y más inesperado aspecto del trabajo con la marla se relacionó con la exposición al sol. Y es que, pese a todas las precauciones, el reflejo del sol sobre esta piedra provocó intensas quemaduras en el equipo de la empresa contratista.
Por una letanía de motivos, se decidió utilizar un área protegida con un toldo para cada colocación del shotcrete.
El trabajo
Al momento de completar la fase de excavaciones, se instaló el encofrado y la subsecuente armadura de acero a lo largo de todas las partes de hormigón proyectado del proyecto. Se seleccionó un orden secuencial para el shotcrete, que comenzó con una pequeña y simple colocación del material para resolver el proceso de la planta mezcladora y para poner a prueba el nuevo diseño de mezcla del hormigón. Se ordenó una carga de 5,4 m3, la que se calculó como necesaria para que el aditivo estabilizador de la hidratación brindara al equipo 2 horas para transportar, disparar y dar forma a la sección colocada. Se instaló esta estructura con un toldo con la madera disponible y se colocó una lona azul sobre el encofrado artesanal para dar la sombra necesaria.
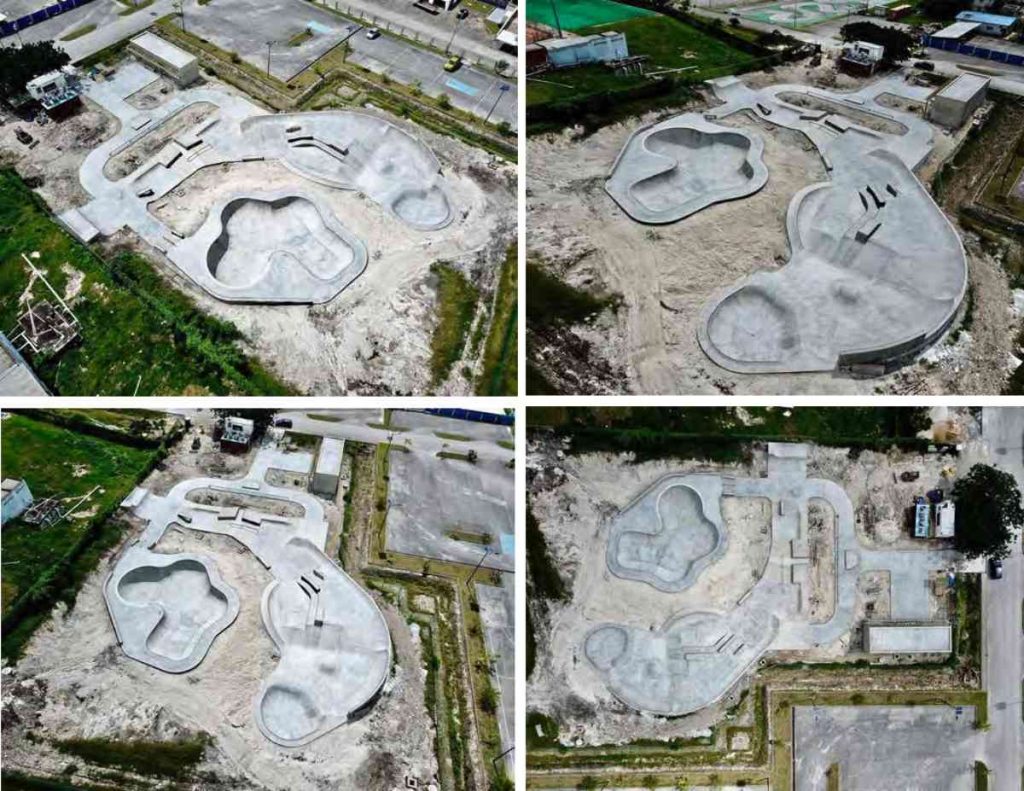
La aplicación del shotcrete se realizó según lo planificado. La bomba se entregó y el operador certificado por el ACI colocó el material mientras el equipo dio forma al hormigón colocado. Luego, se esperó algunas horas para que la aplicación final se endureciera lo suficiente para dar el acabado con las palas. Y si bien se utilizó una generosa cantidad de aditivo estabilizador de la hidratación, el equipo de la obra consideró que ese era el camino a seguir para responder a los desafíos impuestos por este proyecto.
Al finalizar cada colocación del shotcrete, se realizaron cortes de descarga con una Medusaw (una sierra de proceso húmedo con un disco de 184 mm con hojas de diamante). Los cortes de la sierra de completaron con mini molinillos, se humedecieron las losas, se cubrió con un plástico para sellar la hidratación por humedad y se colocó una lona sobre todo para asegurar al plástico de las condiciones del viento. Al día siguiente, se sacó esta capa, se aplicó un compuesto de curado y se recubrieron las losas con plástico para tratar de sellar la mayor cantidad de humedad posible en las losas par el curado.
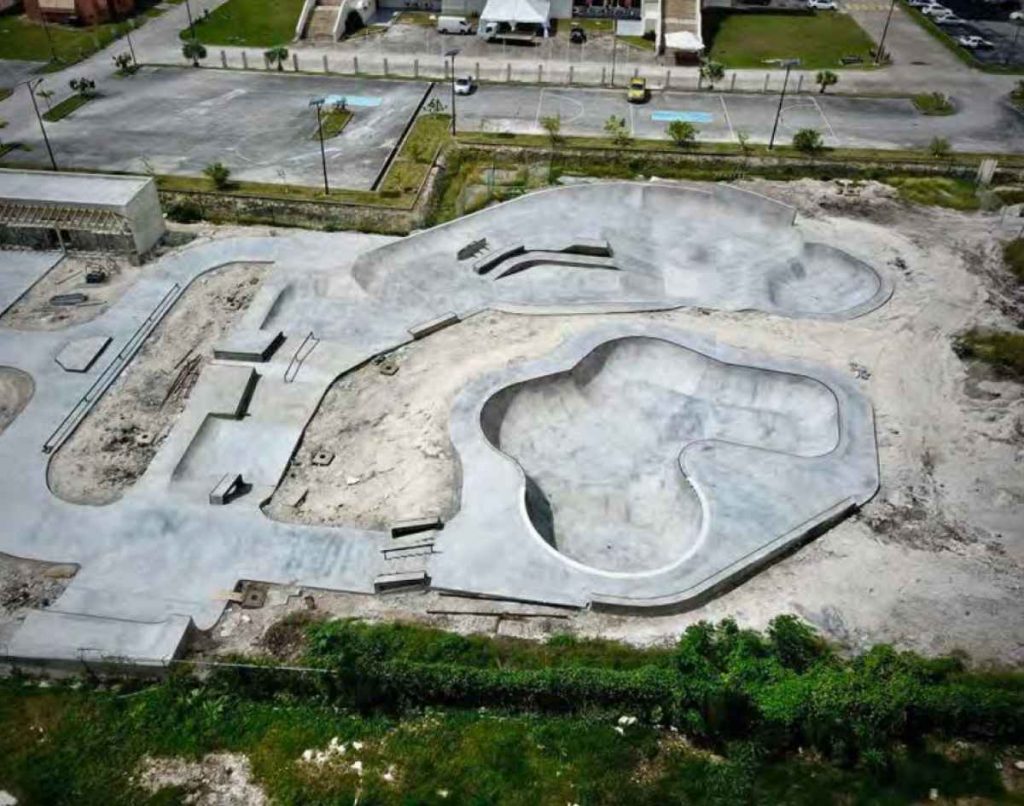
Los subsiguientes días, se incrementó la producción de material y, al mismo tiempo, se realizaron cambios significativos tanto el volumen como en el asentamiento de los aditivos. Ya al final de la primera semana, la cuadrilla de trabajo logró confianza con la mezcla, la planta dosificadora y con el nuevo equipo a cargo del shotcrete, formado por un operador local en capacitación y un ayudante a cargo de las terminaciones, también de la zona.
El cuenco del skatepark se completó en cuatro pasadas de shotcrete e incluyó una sección profunda (2,4 metros) que se diseñó pensando en la albardilla y la loseta de la piscina. Se creó una muesca en el hormigón proyectado de aproximadamente 150 mm desde la parte superior de la viga para así, colocar la siguiente loseta con la superficie terminada de shotcrete. Se colocaron baldosas Daltile, aprobadas para uso exterior, las que se enviaron en container por barco junto al equipo de Artisan Skateparks, al igual que el revestimiento Federal Stone y los materiales de instalación Laticrete. Se eligieron los colores azul y amarillo de la bandera de Barbados para la banda de azulejos bajo el borde blanco de la piscina.
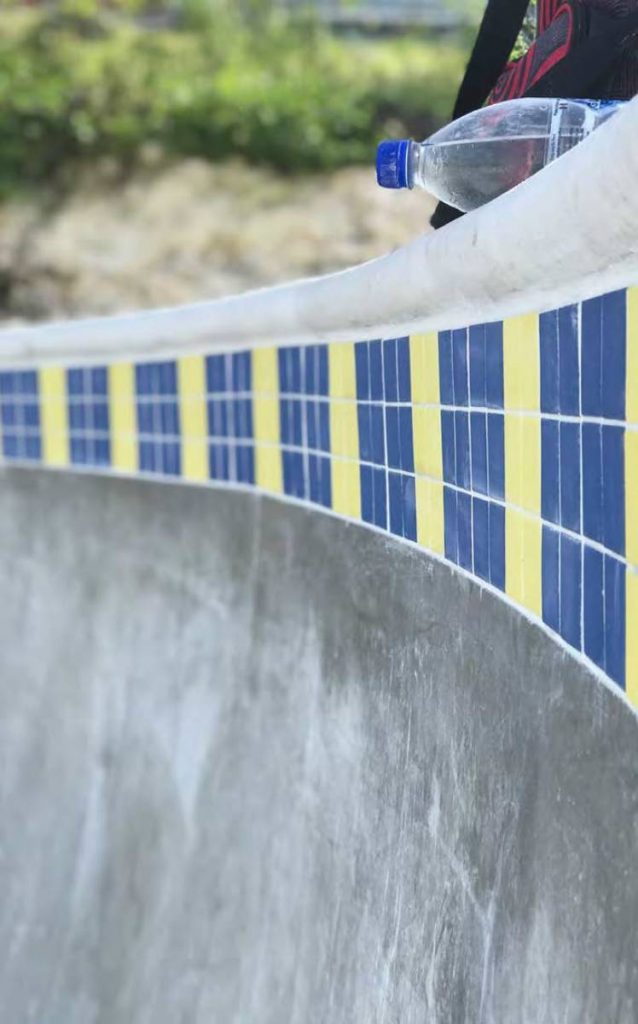
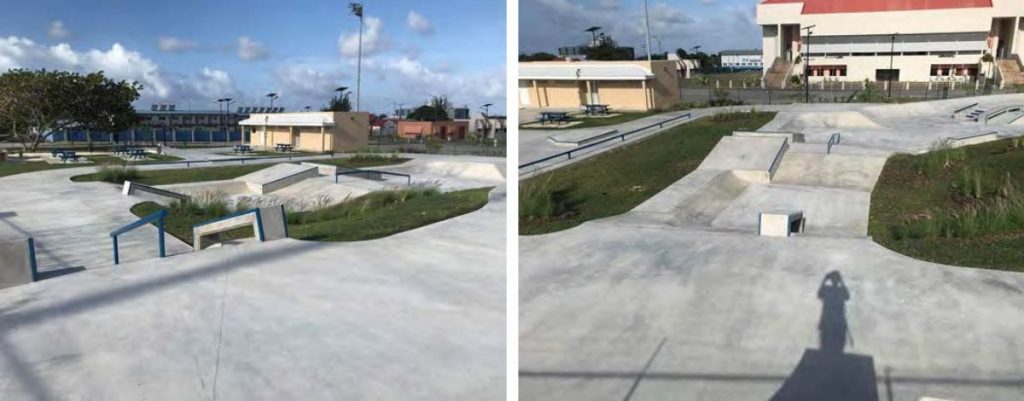
Finalización de la obra
El proyecto se completó en su totalidad en cuatro meses, una vez que arribó el planchado final y los subsecuentes sellos de juntas, entre otros elementos. El proceso del shotcrete tomó aproximadamente 5 semanas en se realizó de manera óptima desde el comienzo de la obra para ser uno, si no es que el único, proyecto con hormigón proyectado en Barbados. Si bien este no fue el primer trabajo de Artisan fuera de Estados Unidos, sí se tuvo que realizar una planificación logística detallada para embarcar los elementos necesarios para el proyecto.
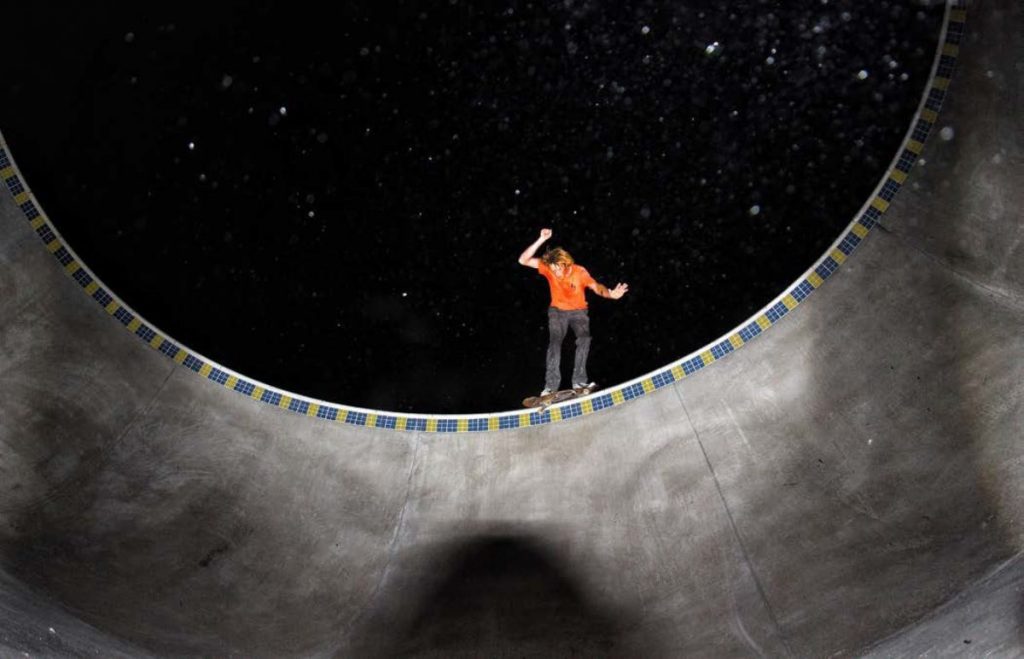
Además, hubo que adaptarse al ambiente del sitio del proyecto y resultó clave para el éxito del proyecto utilizar habilidades comunicacionales adecuadas para hablar con varios de los proveedores, los negocios y los trabajadores.