En este artículo, publicado originalmente por la revista Shotcrete Magazine de la American Shotcrete Association, se entregan detalles técnicos de la reparación y puesta en funcionamiento de un túnel con 150 años de antigüedad. Para realizar el trabajo, el uso de shotcrete tanto en el sostenimiento como en el acabado del proyecto fue fundamental.
Autora: Ashley Cruz, ingeniera de operaciones, es directora de Operaciones de Cruz Concrete y fue la gerente de proyecto y la operadora de la mezcla de hormigón para el túnel de Park Avenue.
Fuente: Shotcrete Magazine
El túnel Park Avenue, conocido antiguamente como el túnel Murray Hill, es una vía pública de 425 metros de largo, 5 metros de ancho y tres de alto, que cruza seis cuadras de la ciudad de Nueva York. El túnel se construyó originalmente en 1837 con un corte de roca abierto, sobre el cual se construyó un arco de ladrillo el año 1854 para crear el perfil del túnel. En los siguientes 150 años, el túnel estaría plagado con inconveniencias que van desde fallas mecánicas a filtraciones en el muro de revestimiento debido al volumen del suelo sobre éste, precisamente el lugar se introdujo la idea de una estabilización de shotcrete dentro del alcance del proyecto.
El alcance estructural utilizando hormigón proyectado como revestimiento del techo, se discutió primero al inicio de la fase de diseño debido a la imperfección de las curvas del arco de ladrillo original. El mandante trajo a la empresa Cruz Concrete una vez que el proyecto se hizo público y trabajó de cerca con el equipo de diseño. En este esfuerzo, el equipo dedicado de Cruz desarrolló la secuencia de la instalación de shotcrete y ayudó con el desarrollo del diseño de mezcla final del hormigón.
Finalmente, Cruz Concrete se adjudicó el sub-contrato para ejecutar las reparaciones con shotcrete en los muros de parapeto de piedras originales y para proveer e instalar el revestimiento de hormigón proyectado de 300 mm de espesor, que abarca todo el arco del techo del túnel. Estos elementos de alcance utilizaron 31 m3 para la reparación del hormigón y 1.200 m3 para el revestimiento finalizado de shotcrete.
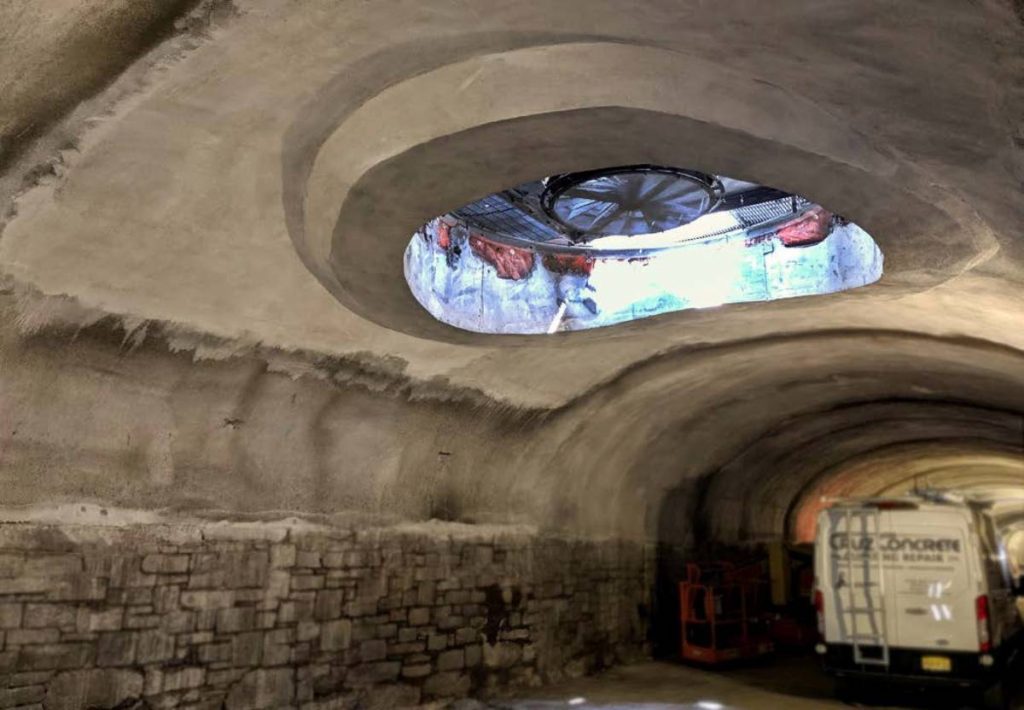
Un histórico arco-techo en los tiempos modernos
La especificación del diseño requirió el uso de 6.000 lb/in2 -422 kgf/cm2- (41 MPa) de único componente premezclado, especialmente formulado para la mezcla con cemento Portland que además contiene aditivos retardantes a la retracción, fibras, humo de sílice y áridos cuidadosamente catalogados. Esta mezcla de hormigón produjo un mortero para aplicación vía mecánica de alta constructabilidad y baja absorción. Además, se especificó para el diseño de mezcla un aditivo reductor de la permeabilidad para disminuirla en el producto final. Todos los ensayos realizados con esta mezcla mostraron resultados que sobrepasaron los requerimientos especificados para este material.
El diseño estructural del nuevo revestimiento del cielo requirió construir por fuera del ladrillo existente, utilizando una sábana impermeabilizante fijada al ladrillo y un refuerzo estructural de acero: vigas de celosía, compuestas de dos barras de refuerzo #11 (#36M) y una barra de #13 (#44M), colocadas a 0,6 metros en el centro y que descansan en el borde de la saliente del muro de piedra existente. Además, se instalaron mallas de alambre como soporte adicional para la colocación del shotcrete.
La progresión típica de este proyecto se basó tanto en la técnica de hormigón proyectado como también en la aprobación del inspector. Cada día, el equipo aplicó el shotcrete al arco superior en dos ascensores, progresando 8 metros a lo largo del corredor. El ascensor de base se ubicó aproximadamente entre los 150 a 225 mm de profundidad, lo suficiente para rellenar las vigas de celosía. El grosor remanente se aplicó durante los días de trabajo previos. Esto sirvió como el acabado de levantamiento, permitiendo el uso de un aditivo para menor aceleración de fraguado, lo que significó que el equipo tuviese más tiempo para perfeccionar el acabado de esponja flotante. Cruz mezcló, aplicó y finalizó aproximadamente de 19 a 23 m3 de hormigón de asentamiento de 75 mm por día.
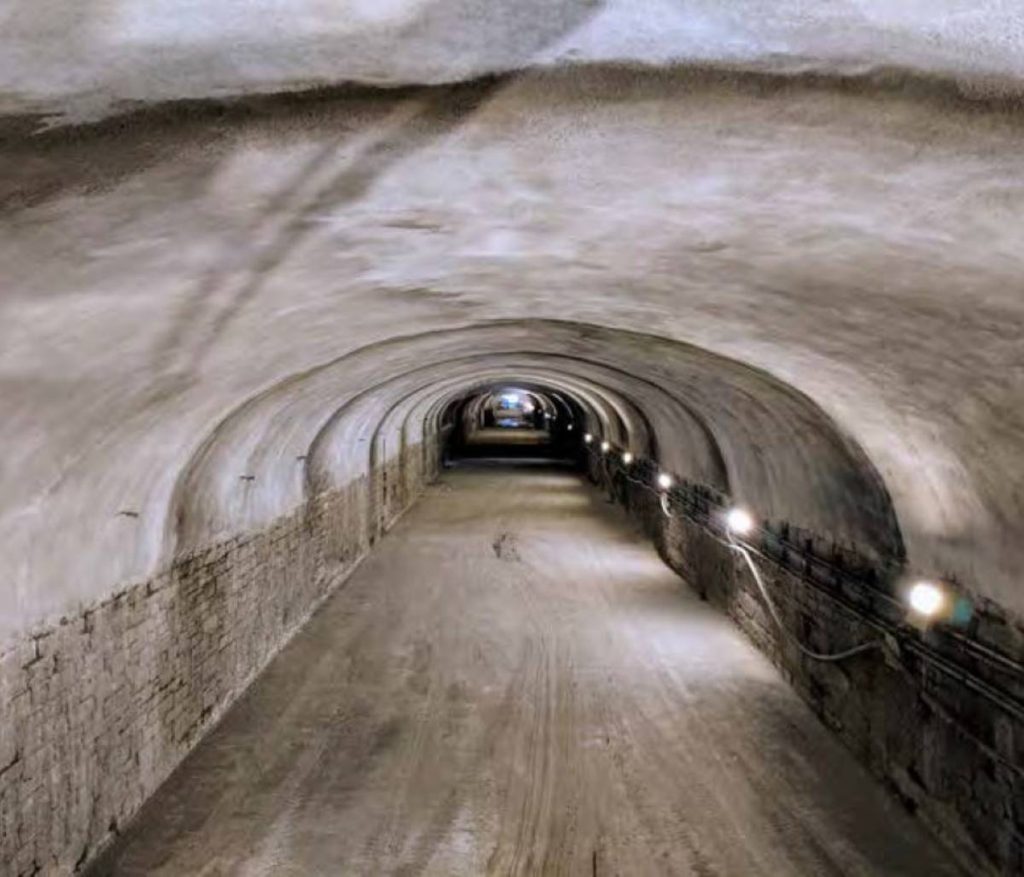
Dadas las restricciones de espacio dentro de un túnel de 5 metros de ancho, Cruz pudo utilizar un sistema de tres equipos: uno encargado de la boquilla, otro a cargo del rasgado y acabado, y un equipo para el bombeo y el mantenimiento de la manguera.
Mezclando el shotcrete en sitio
El shotcrete fue el elemento estructural más importante y determinó el camino crítico del proyecto. Los otros tres elementos principales fueron la superficie del camino, rejuntar los históricos muros de piedra y la instalación de un nuevo equipamiento eléctrico y de protección contra incendios, que aunó a estos tres elementos esenciales.
Para brindar de forma exitosa la mezcla especificada de shotcrete, la que eliminó el uso de camiones mixer para la entrega del material, se le solicitó a la empresa que la mezcla del hormigón se realizara en el sitio de la obra. Para lograr ese desafío, Cruz utilizó una mezcladora continua, la que se llevó a la obra en un remolque y una camioneta, montada sobre un antideslizante para una fácil movilidad a través de un montacargas. Esto permitió al equipo mover el equipo a lo largo del corredor en cada turno. El hormigón seco se entregó preenvasado en forma de sacos, con pesos de 1.400 kilogramos, los que se colocaron sobre la tolva seca de la mezcladora. Tractores-remolques entregaron y descargaron los 30 pallets del material cada semana por la entrada sur del túnel, la que tenía un espacio libre marginalmente más alto. Estas entregas se colocaron estratégicamente dentro del túnel para mitigar cualquier interferencia con otras operaciones de la construcción.
Cuando se trabaja con hormigón proyectado, es imperativo que la relación agua/cemento del material sea mantenida de manera apropiada. Al lanzar el shotcrete al techo, la precisión de esta relación se transforma en una prioridad aún mayor. El operador e inspector de la mezcla de hormigón realizada en el sitio, estuvo constantemente monitoreando la cantidad de agua utilizada para cada tanda de hormigón. El asentamiento de cono se mantuvo más menos en los 25 mm, cada 76 mm de asentamiento. A medida que se progresó en el corredor, la presión del agua cayó ya que la principal fuente agua presurizada provenía de un grifo ubicado a nivel de calle, a unas seis cuadras de distancia. Para aliviar este inconveniente, se reemplazaron todas las mangueras a líneas de agua de 50 mm, a excepción de las de 19 mm, cuyo largo es de 30 metros, y sólo se autorizaron otros trabajos con esta fuente de agua cuando no se realizaba la mezcla del hormigón. A lo largo de todo el proyecto, se añadió también un aditivo acelerante de fraguado rápido a la boquilla para asegurar la adhesión del hormigón una vez aplicado.
El desafío del diseño
Otro factor que agregó complejidad al proyecto fue la inclusión del trabajo alrededor de 8 ventiladores extractores de techo. Los ventiladores tenían un diámetro que iba de los 2,5 a los 3 metros. Durante la construcción, este sistema de extracción requirió de una actualización, y con ello, un rediseño del perfil del cielo en estos puntos. Los documentos del contrato mostraron un diseño de techo con un anillo de compresión integrado dentro de cada pozo del ventilador. Se emitió una orden de cambio para construir el anillo de compresión colgado por fuera del ventilador. Esto agregó material al diseño original con un anillo de compresión que sobresaldría hacia abajo desde el techo aproximadamente 350 mm y 600 mm de ancho.
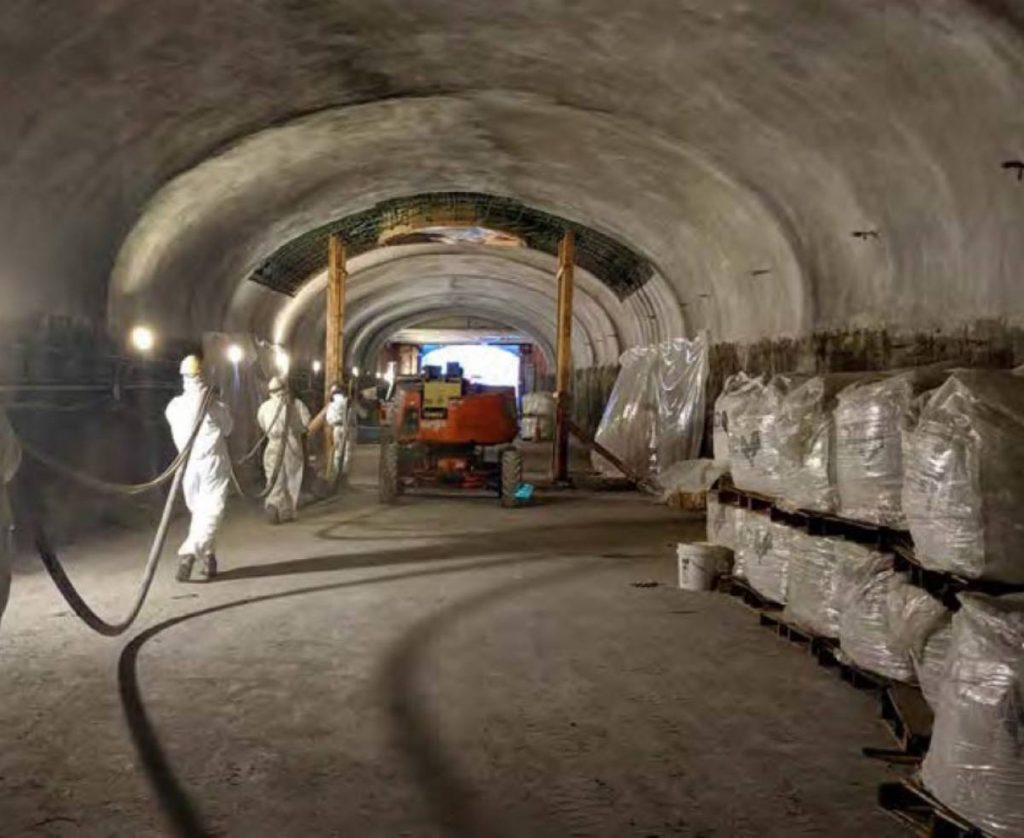
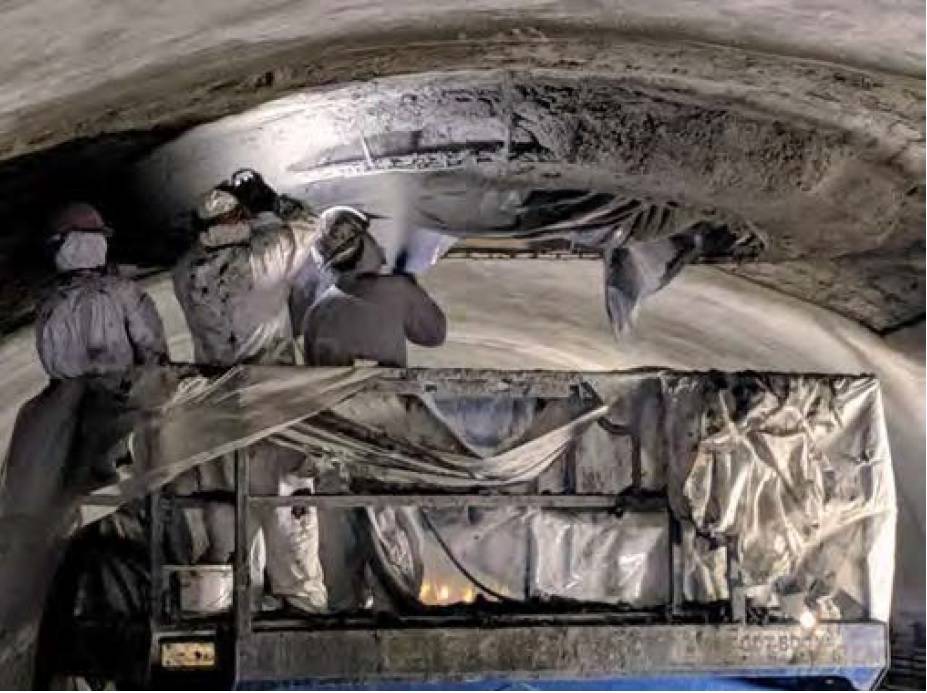
Durante el proceso del rediseño de los ventiladores, el contratista continuó instalando el shotcrete, forzando al equipo a dejar espacios en el arco alrededor de los extractores, los que debían estar completamente operacionales durante la construcción. El shotcrete probó ser invaluable para el éxito del trabajo en el anillo de compresión, ya que el hormigón proyectado no requiere juntas de construcción formadas, lo que finalmente permite dejar los espacios con facilidad. La aprobación final de este rediseño llegó cuando el contratista (Cruz Concrete) ya estaba llegando al final del túnel. El mandante general construyó una mampara de un solo lado en el diámetro interior de cada extractor, la que actuó como el límite del shotcrete. Esto permitió al equipo continuar con la instalación sistemática de las elevaciones de shotcrete. Este proceso se añadió al cronograma del proyecto, sin embargo, éste se completó antes del tiempo originalmente previsto por el equipo.
El shotcrete resultó de enorme importante para la estética general del producto terminado ya que tanto el arquitecto como el ingeniero solicitaron que la superficie de hormigón terminada siguiera el perfil de la obra de ladrillos existente, la que estaba lejos de un nivelado perfecto. Los ladrillos se instalaron en 1857 y, en ese aspecto, Cruz Concrete se esforzó por conservar la mayor parte de la apariencia histórica del lugar para que la experimentaran las futuras generaciones.
Sustentabilidad medioambiental y económica
Dada la eficiente del método de colocación del shotcrete, el equipo de Cruz determinó que el shotcrete sería entre un 35% a un 50% más eficiente en términos de tiempo, en comparación a la metodología tradicional de verter y dar forma al hormigón. En ese sentido, desde que el método de colocación del shotcrete eliminó la necesidad de levantamientos y removió a los complejos encofrados, el mandante disfrutó de ahorros significativos dada la reducción tanto de mano de obra como de materiales. Adicionalmente, la eliminación del encofrado redujo el consumo total de los carbonos emitidos durante la duración del proyecto.
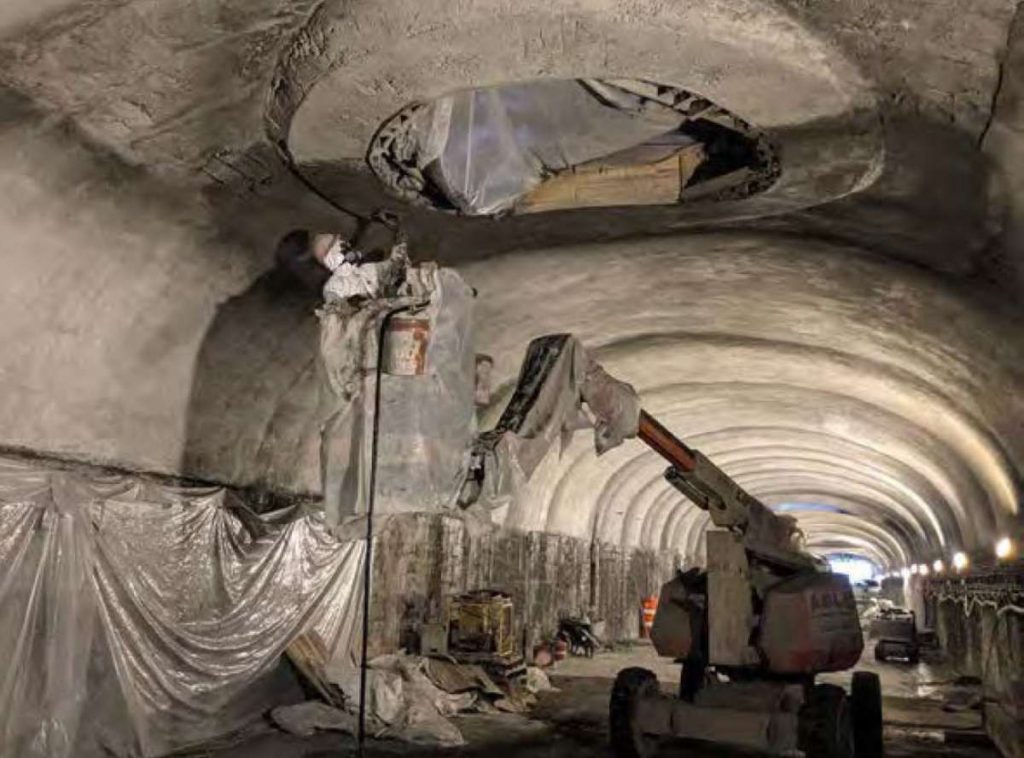
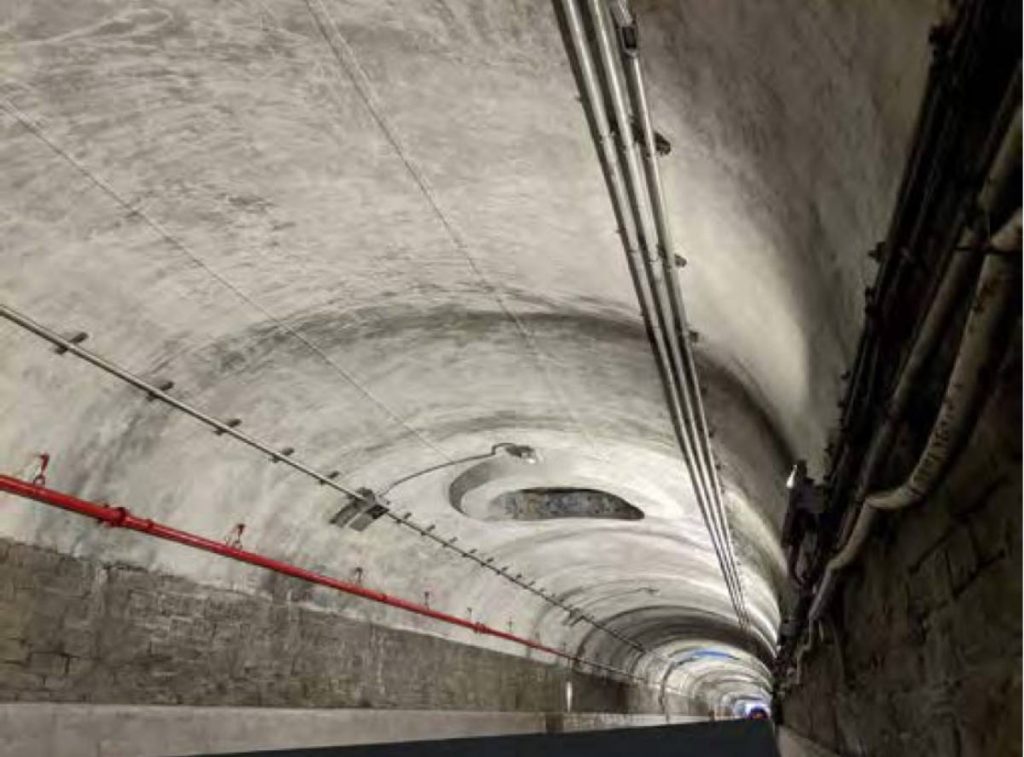
Utilizando la dosificadora en el sitio -requerida por el proyecto- Cruz pudo reducir la huella de carbono de la mezcla del hormigón y del transporte en más del 50%, con el uso de un motor diesel de 29 HP con 430 horas de funcionamiento y 100 entregas de material, a diferencia de las operaciones de una planta de hormigón y los camiones mixer que entregan el material en el tráfico de Manhattan. Todos los desagües para las aguas lluvias en el túnel se cubrieron con medias filtrantes para prevenir el sedimento y disminuir la entrada de lodo al sistema de alcantarillado, de este modo reduciendo la carga de contaminantes en la infraestructura de aguas pluviales del sitio.
Finalmente, Cruz Concrete completó el proyecto, transformando aproximadamente 1.220 metros cúbicos de hormigón seco preenvasado en la mezcla húmeda de shotcrete que fue colocada, finalizada y curada, en 70 días de trabajo. Las filtraciones de agua se bajaron y el arco aún mantiene gran parte de sus características de 1.800.