Presentado en la pasada bienal de arquitectura de Venecia, el proyecto “Striatus” -un puente de hormigón impreso en 3D- en el que confluye Zaha Hadid Architects, el Block Research Group del ETH Zúrich y otros asociados, revela una nueva forma de utilizar la tecnología de impresión 3D para construir con hormigón. Sobre esto, conversamos en exclusiva con Shajay Bhoshaan, íder del grupo de Diseño y Computación del prestigioso estudio, quien nos comentó más sobre este nuevo lenguaje.
En el mes de julio, durante la bienal de arquitectura de Venecia, el estudio de arquitectura Zaha Hadid Architects, ZHA, junto con el Block Research Group del ETH Zúrich, presentaron al mundo el puente peatonal “Striatus”, un elemento de hormigón impreso con tecnología 3D cuya principal característica es que su estabilidad estructural no está circunscrita al refuerzo con barras de acero.
Con 16 metros de largo, “Striatus” de inmediato se posicionó como un nuevo lenguaje constructivo. ¿De qué manera un elemento de estas características prescinde del acero? ¿Cómo podría comportarse, por ejemplo, ante un evento sísmico? Estas son sólo algunas de las preguntas que aparecen cuando se analiza a esta nueva propuesta de construcción con hormigón.
Shajay Bhooshan, actual director asociado del prestigioso estudio y líder del grupo de Diseño y Computación de ZHA (cuya sigla en inglés es ZHACODE), es arquitecto, doctor en arquitectura de la Universidad de Bath y uno de los responsables de este proyecto, del que compartió en exclusiva detalles respecto a su génesis y cómo, entre otras cosas, se apunta una construcción con hormigón más sostenible con este nuevo lenguaje.
Analizar los desarrollos de la construcción con hormigón con impresora 3D
Uno de los aspectos relevantes a la hora de pensar este proyecto, fue la manera en que se abordó el diseño. En efecto, Bhooshan ya llevaba trabajando en aspectos relacionados al diseño con la tecnología de impresión 3D de hormigón desde el año 2017, por lo que, aseguró, se encontraba desde antes “operando o investigando y aprendiendo acerca de todas las dificultades, oportunidades y restricciones, en general, del hormigón impreso en 3D y de cómo esta tecnología viene creciendo y evolucionando desde, quizás, 1995”.
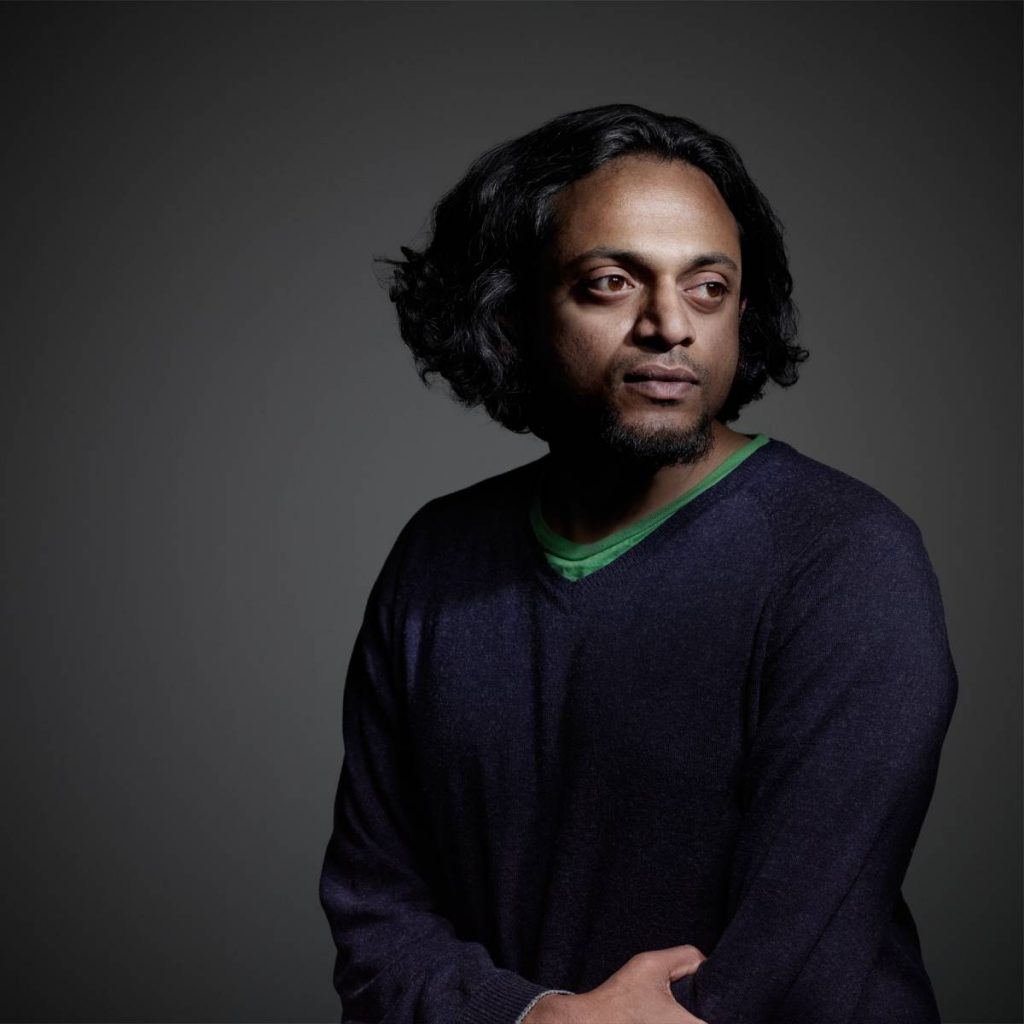
En ese sentido, el arquitecto y jefe del ZHACODE comentó la mayoría de las investigaciones que se llevan a cabo y que se relacionan al hormigón vertido con impresor 3D, se enfocan más en “la maquinaria o en la ‘receta’ del hormigón ara esta tecnología, además, en la actualidad existen empresas especializadas en este tema. Sin embargo, el aspecto del diseño arquitectónico de esta innovación se ha dejado de lado”, manifestó.
En ese contexto, el arquitecto y doctor en arquitectura explicó que, en base a su propia tesis doctoral, sentó la bases de lo que sería el sustento para “Striatus”. “Estaba haciendo investigación con herramientas de diseño y modelos de diseño arquitectónico, desarrollando una analogía de estos modelos de análisis con estructuras de mampostería”, dijo.
La analogía no es antojadiza. De acuerdo al profesional, el hormigón “puede verse como una piedra artificial y si se saca el componente acero de la ecuación, el hormigón armado, el material sin barras de refuerzo es básicamente una piedra artificial y se comporta materialmente como ésta. De esta manera, cualquier elemento que se pueda construir en piedra, es factible hacerlo en hormigón”.
Utilizar conocimiento del siglo XV con elementos tecnológicos actuales
Con ese sustento teórico definido, entró en juego el elemento tecnológico. Para ello, Bhooshan explicó que, en conjunto con el Block Research Group, se analizaron distintas estructuras en mampostería, como domos, arcos y muros. “Tomamos ese conocimiento histórico de diseño en mampostería y lo actualizamos”, subrayó.
Ese proceso, detalló, consideró el uso de elementos matemáticos y de tecnología computacional para analizar de mejor manera los aspectos de diseño y así, analizar con herramientas del siglo XXI construcciones centenarias.
“El otro aspecto de este proyecto tiene que ver con la impresión 3D de hormigón”, subrayó el experto. Esto, porque utilizar esta tecnología permite, a juicio del experto, “tomar ventaja de todos los beneficios que posee este material”.
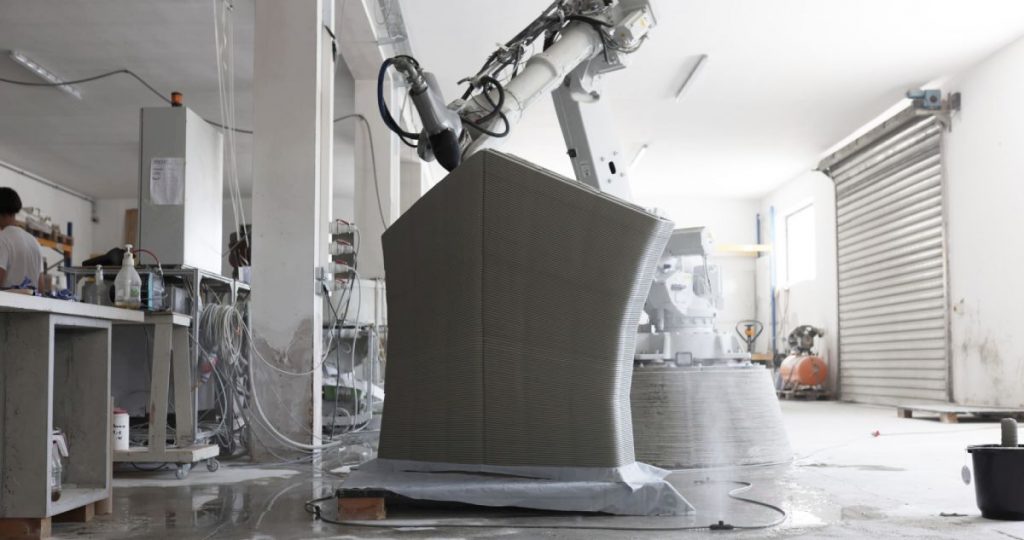
Deentro de estos, el líder de ZHACODE destacó que “permite colocar de forma precisa el material, donde se necesita. Entonces, volviendo a la analogía de la mampostería en piedra, se puede sacar un 40% o un 50% de ésta y el hormigón aún trabajará bien. Además, permite una variedad de diseños: por ejemplo, que sea hueco, algo complejo de hacer con roca verdadera porque se necesita tallarla”, explicó.
De esa forma, dijo el arquitecto, el proyecto “Striatus” se sustentó en esos pilares: “la maduración de la tecnología de impresión 3D de hormigón, pero que aún nadie sabe cómo diseñar con ésta; el hecho de que la impresión 3D permite colocar el hormigón de manera precisa y además, ahorrar material; y el hecho de que el hormigón está relacionado con la mampostería y la mampostería misma es como tener algo del Renacimiento en pleno siglo XXI, a través de varias investigaciones que se han realizado”, destacó el líder de ZHACODE.
¿Cuál es el mejor elemento de hormigón para testear este nuevo lenguaje?
Con esos conceptos, el desarrollo de este nuevo lenguaje constructivo -a partir de la tecnología de impresión 3D- comenzó a tomar forma. Un primer paso, detalló Shajay Bhooshan, fue definir qué tipo de elemento de hormigón sería el que demostrase los conceptos mencionados.
En ese sentido, el profesional comentó que “una obvia era construir una casa, pero muchas personas ya lo están y, además, lo que es interesante es que todas las capas que se colocan son paralelas y horizontales, y nosotros lo que queríamos mostrar es que el hormigón se puede utilizar para expandir espacios, no sólo para levantar muros. Es decir, partir desde el piso y terminar en el cielo. Eso significó que teníamos que imprimir en capas no horizontales ni paralelas”.
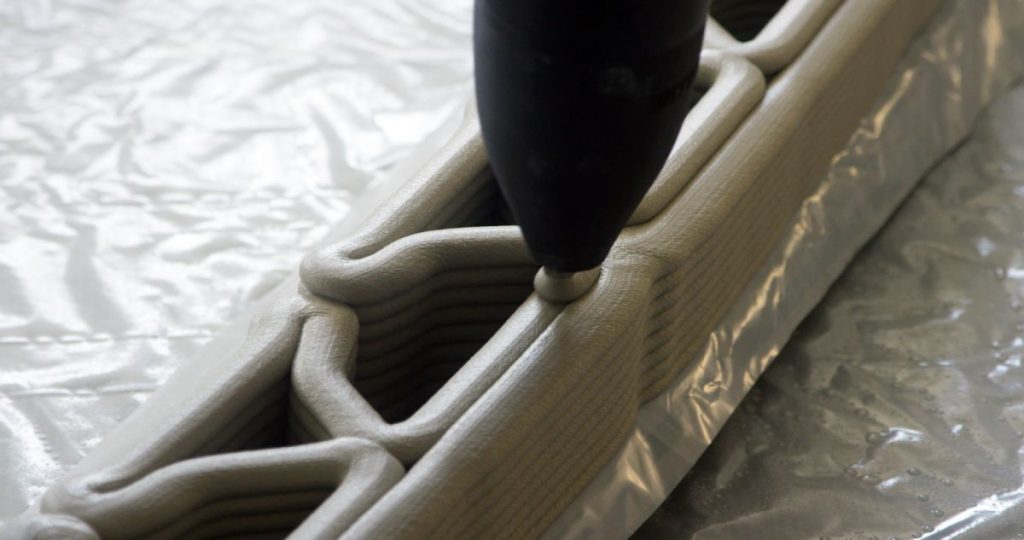
Para ello, se incorporó a Incremental3D en la impresión del hormigón, por su experiencia en el trabajo de capas no paralelas. En ese sentido, aseveró el experto, un beneficio extra de trabajar con capas no horizontales de hormigón impreso es que estas se pueden alinear de forma perpendicular a las fuerzas de carga. “Los arcos de piedra tienen ese corte, esa forma radial, porque es perpendicular a la fuerza de carga”, puntualizó.
“De esta manera, queríamos fabricar una estructura larga, queríamos imprimir en capas no horizontales, porque esa es la forma en que el hormigón ‘quiere’ ser utilizado, en compresión, aprovechando que el hormigón es excelente en compresión y que, al tener poca capacidad de tensión, lleva al uso de acero o fibras para su refuerzo. Por esos motivos, pensamos que un puente sería el tipo de elemento ideal para demostrar este lenguaje”, aseveró.
Además, explicó Bhooshan, si bien “Striatus” se presentó como un puente, también tiene elementos como arcos y muros, lo que permite analizar de mejor forma el comportamiento de este nuevo lenguaje.
Eficiencias en tiempo y transporte
Dentro de los aspectos más relevantes del proyecto “Striatus”, Shajay Bhooshan destacó los tiempos en que se desarrolló el puente: fueron 6 meses totales de trabajo, en los que la impresión de los bloques que forman el puente demoró 85 horas y el proceso de ensamblaje de estos, tomó poco más de un mes.
“Striatus” tiene un total de 53 bloques, los que van unidos entre sí, sin necesidad de algún mortero que las una. “Gracias a esto, se pueden levantar los bloques y colocarlos en otro lugar o también, separarlos, molerlos y reciclarlos”, dijo el arquitecto líder del ZHACODE.
El profesional destacó que varias áreas de conocimiento se integraron al proceso de fabricación de los bloques, tanto desde el diseño digital como en el proceso mismo de impresión de hormigón que, según el experto, asegura las condiciones ideales para que el hormigón maximice su desempeño a la compresión.
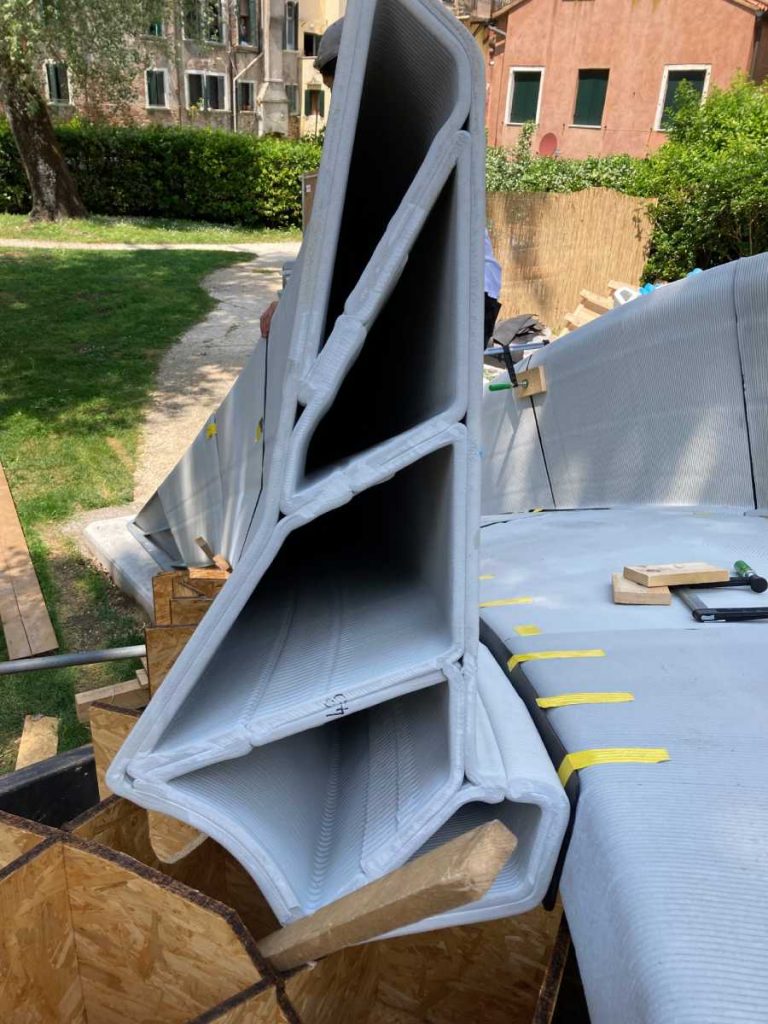
“Cada bloque de ‘Striatus’ tiene aproximadamente 500 capas de impresión. Asimismo, cada bloque tiene un patrón de impresión de 1,5 km y el puente completo, algo así como 60 kilómetros. Hubo que calcular todas las capas de hormigón extruido para cada uno de los 50 bloques y eso se debe hacer de forma precisa, además de coordinarlos con las otras especialidades”, explicó.
Asimismo, cada bloque tiene un peso que va entre los 200 y 700 kilogramos, lo que a juicio de Bhooshan, aseguran su transportabilidad. “Cuando comenzamos el proyecto, consideramos el hecho que se pudiesen transportar en un camión regular y que se pudiesen alzar en una grúa araña simple, con un equipo de 5 o 6 personas en el sitio de instalación y no de, por decir un número, 300 operarios”.
¿Sismoresistente? Una pregunta para análisis posteriores
Al no tener refuerzo ni de acero ni de fibras -debido a la traducción digital de las técnicas de mampostería en piedra- y al estar unido por juntas secas, sin necesidad de utilizar un mortero que una los bloques, una de las preguntas que surge es cómo se comportaría “Striatus” -y este nuevo lenguaje constructivo- ante una exigencia sísmica.
“Partiendo de la base que este puente se diseñó para zonas sísmicas europeas, si uno lo toma y lo traslada a Chile, por ejemplo, quizás se resienta por el movimiento, pero eso no significa que puedan utilizarlo los mismos principios en los que se sustenta este proyecto”, explicó el arquitecto.
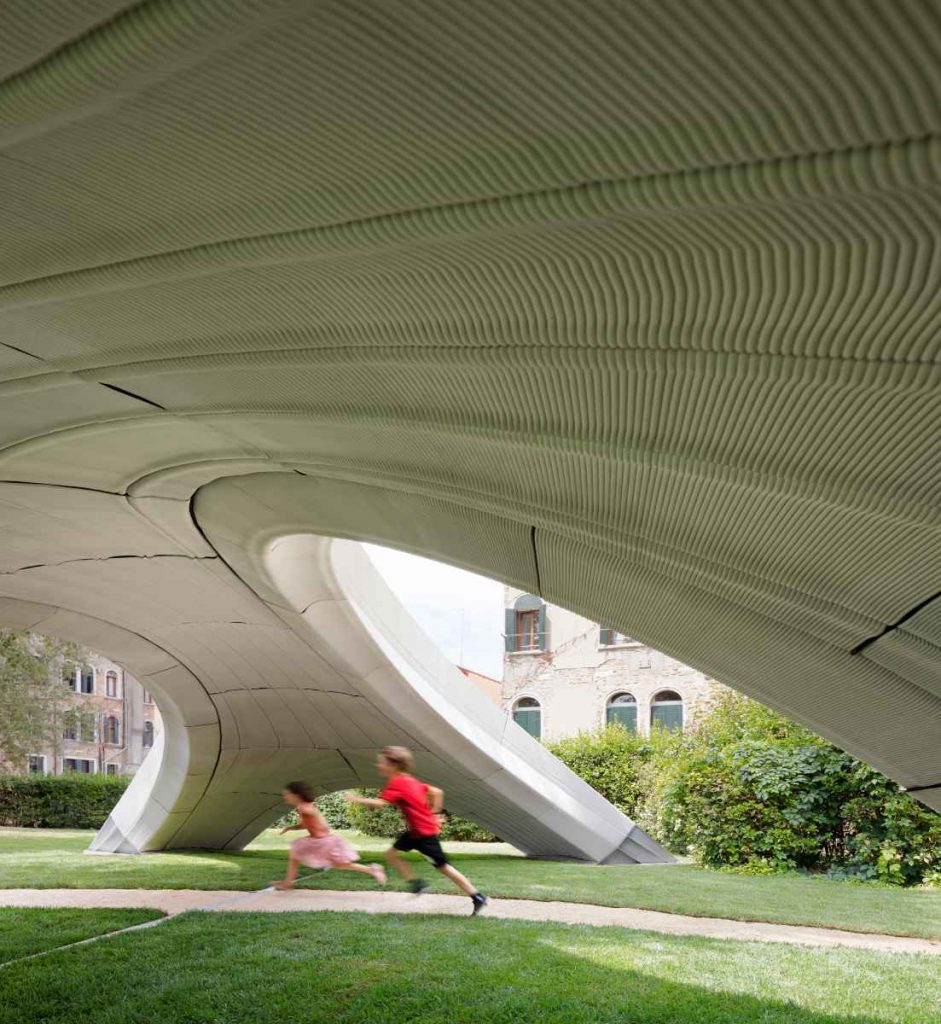
En ese sentido, Bhooshan comentó que si bien su campo de expertiz escapa al de la ingeniería estructural, por las características de “Striatus”, es posible que la estructura disipe la energía provocada por el sismo. “Podría no lucir como este proyecto, quizás tenga otros elementos visibles. Por ejemplo, las fundaciones podrían ser distintas”, dijo.
Asimismo, el hecho de que las juntas de “Striatus” sean secas –“debido a que el diseño de los bloques se realiza digitalmente y de forma milimétrica, de tal modo que no es necesario el uso de morteros para unirlos”, detalló el líder de ZHACODE- y que, sólo para evitar su fricción, el equipo detrás del proyecto consideró unas capas de neopreno, “potencialmente permite, si es que existe un sismo, que parte de la energía del movimiento se transfiera entre los bloques a través de estas capas”.
Sostenibilidad y economía circular: el gran aporte de este nuevo lenguaje
Otro de los aspectos que subrayan del proyecto “Striatus” y este nuevo lenguaje constructivo con hormigón impreso en 3D, dice relación con un aspecto que es completamente actual y que dice relación con el hormigón como material sostenible, además de contribuir con el desarrollo de la economía circular del sector.
Al respecto, Shajay Bhooshan subrayó que al reducir el acero en la estructura en un 90% –“sólo un par de cables para levantar al puente”, dijo- de inmediato se reduce la huella de CO2 que pueda tener este elemento. “A través de las técnicas de mampostería, no se necesita un hormigón de alta resistencia. Lo que requerimos es que sea un material con buena resistencia a la compresión y que las capas estén alineadas de forma perfecta para las cargas de fuerza, ya sea en un arco o en un muro”.
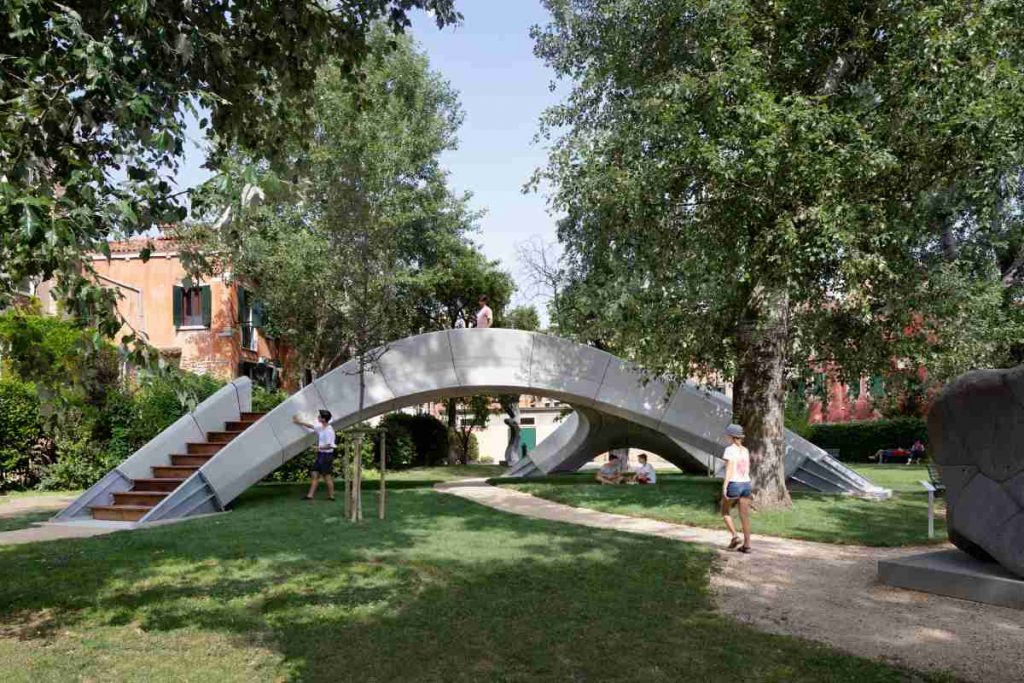
Si bien el arquitecto aclaró que, para “Striatus” se utilizó un hormigón de alta resistencia porque aún no existen hormigones adecuados para impresoras 3D que sean de menor desempeño, Holcim -otro de los involucrados en el proyecto- ya está desarrollando fórmulas que permitan utilizar hormigones de baja resistencia para este tipo de tecnología.
Siguiendo esa línea, Bhooshan destacó que los bloques, al ser reciclables, aportan a disminuir la huella de CO2 del hormigón, principalmente porque es posible molerlos y reciclarlos. “Incluso el poco acero que tiene el proyecto, que son los cables de tensión que sostienen al puente, se pueden separar fácilmente, por lo que también se pueden reciclar”, explicó el arquitecto.
Con esto, el líder de ZHACODE espera que “Striatus” sea un ejemplo de cómo utilizar hormigón de forma responsable. “Es cierto que el material tiene inconvenientes, pero estos pueden solucionarse con un buen diseño, con ingeniería, con desarrollo tecnológico. De esta forma, lidiamos con problemas que son del siglo XXI, como lo es el uso sostenible del hormigón y la solución está en utilizar conocimientos muy antiguos, como los de la mampostería del siglo XV, pero introduciendo tecnología, sea digital o ingeniería estructural, diseño digital y construcción con robots e impresión 3D”, subrayó.