Se menciona a la carbonatación como un elemento clave para la industria en su desafío de alcanzar la carbono neutralidad. Sin embargo, se conoce poco sobre este proceso, que es inherente del material, y los avances que se están realizando en esta materia para producir cementos y hormigones más sustentables. En este artículo, se aborda este proceso natural del cemento y el hormigón, destacando los nuevos desarrollos para mejorarlo.
Fuente: ECRA
Introducción
El cemento es uno de los materiales de construcción más utilizados en el mundo, pero su producción es responsable de una cantidad significativa de emisiones de CO2. Sin embargo, existe un proceso natural que permite que el hormigón reabsorba parte de este CO2 a lo largo de su vida útil: la carbonatación. En los últimos años, la industria del cemento ha comenzado a explorar formas de aprovechar y acelerar este proceso para reducir su huella de carbono. Este artículo explora el fenómeno de la carbonatación, sus implicaciones para la industria del cemento y las nuevas tecnologías que buscan optimizar este proceso.
¿Qué es la carbonatación?
La carbonatación es un proceso químico natural que ocurre en el concreto endurecido. Durante este proceso, el dióxido de carbono (CO2) presente en el aire reacciona con los componentes del cemento hidratado, principalmente el hidróxido de calcio (Ca(OH)2), también conocido como portlandita, y los silicatos de calcio hidratados (CSH). Esta reacción forma carbonato de calcio (CaCO3), efectivamente “secuestrando” el CO2 en la estructura del hormigón.
El proceso químico
La reacción química principal de la carbonatación se puede representar de la siguiente manera:
Ca(OH)2 + CO2 → CaCO3 + H2O
Esta reacción ocurre en presencia de humedad, con condiciones óptimas alrededor del 50% de humedad relativa. El proceso es gradual y comienza en la superficie del hormigón, avanzando lentamente hacia el interior a medida que el CO2 se difunde a través de los poros del material.
Efectos en el hormigón
La carbonatación tiene varios efectos en las propiedades del hormigón:
1. Densificación: La formación de carbonato de calcio lleva a un aumento de volumen de aproximadamente 11%, lo que resulta en una disminución del volumen de poros de hasta un 25%.
2. Aumento de resistencia: La carbonatación puede aumentar la resistencia del cemento endurecido hasta en un 50%.
3. Cambio en el pH: El proceso reduce el pH de la solución de poros del hormigón de aproximadamente 13.5 a menos de 9.
4. Contracción: Aunque la carbonatación del hidróxido de calcio resulta en un aumento de volumen, la carbonatación de las fases CSH está asociada con una disminución de volumen, lo que puede llevar a una contracción general del cemento endurecido.
Es importante notar que mientras la carbonatación puede mejorar algunas propiedades del concreto, también puede tener efectos negativos. En particular, la reducción del pH puede comprometer la capa de pasivación que protege el acero de refuerzo en el hormigón armado, lo que podría llevar a la corrosión del refuerzo si la carbonatación alcanza esa profundidad.
La carbonatación natural como sumidero de carbono
En 2021, el Panel Intergubernamental sobre Cambio Climático (IPCC) reconoció por primera vez la carbonatación de materiales de construcción basados en cemento como un “sumidero de carbono”. Según estudios citados en el informe del IPCC, se estima que la carbonatación de materiales cementosos compensa emisiones de CO2 equivalentes a aproximadamente el 43% de las emisiones de proceso de la producción de cemento.
Cuantificación de la carbonatación natural
Para cuantificar la carbonatación natural, se han propuesto diferentes enfoques. Uno de ellos, desarrollado por Andersson et al., propone tres niveles de cálculo con diferentes grados de precisión:
Nivel 3: Determina la absorción anual de CO2 del stock de edificios existente utilizando un conocimiento extenso del uso histórico del cemento en sus diversas aplicaciones.
Nivel 2: Tiene una precisión menor y se puede aplicar si los datos sobre el uso de cemento y concreto solo están disponibles para algunos años.
Nivel 1: Es un procedimiento simplificado que estima la absorción anual de CO2 de los materiales de construcción basados en cemento de un país en la fase de uso en un 20% de las emisiones de proceso de CO2 de la calcinación en el año respectivo. Además, se estima una absorción anual de CO2 del 2% al final de la vida útil (durante y después de la demolición del edificio) y un 1% en uso secundario.
Estos métodos permiten a los países y regiones estimar la cantidad de CO2 que sus estructuras de hormigón están absorbiendo naturalmente, lo que puede ser útil para los cálculos de emisiones netas y la planificación de estrategias de mitigación del cambio climático.
Estimación de la absorción de CO2 en elementos de hormigón
Para evaluaciones del ciclo de vida, es importante poder estimar cuánto CO2 pueden absorber los componentes individuales de hormigón en función del tiempo. El Anexo BB de la norma EN 16757 proporciona información para estimar la absorción de CO2 de los elementos de construcción basados en cemento.
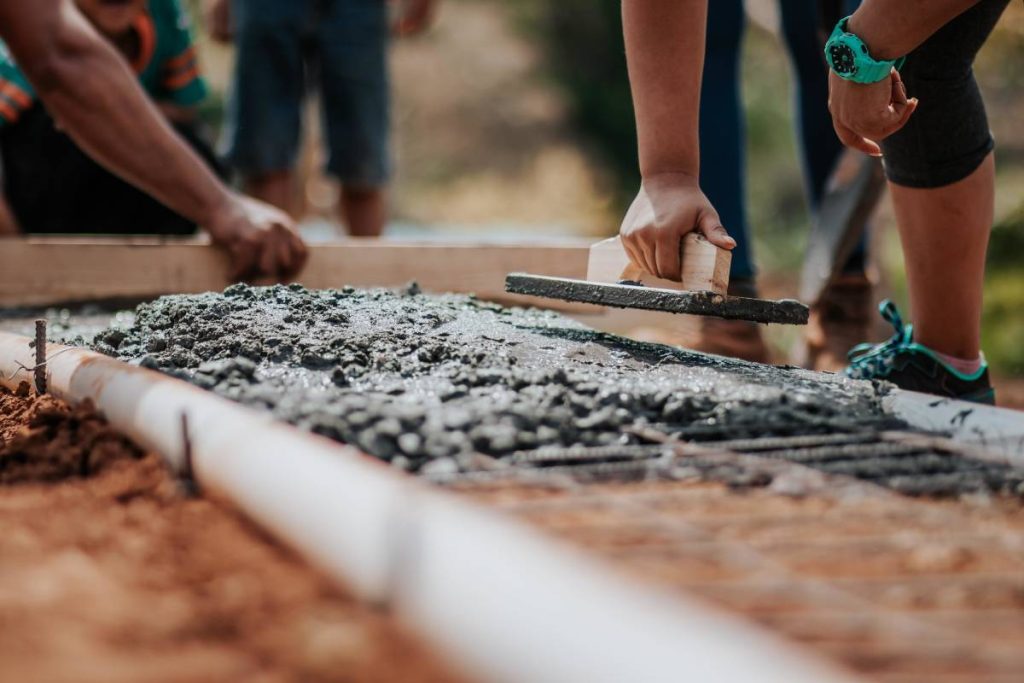
Según la norma, la absorción de CO2 en kg por m2 de superficie de hormigón durante t años se puede calcular con la siguiente fórmula:
CO2 absorbido = Utcc * C * k * √t * Dc / 1000
Donde:
– Utcc es la absorción teórica máxima en kg CO2/kg de cemento
– C es el contenido de cemento en kg/m3 de hormigón
– k es un factor que describe la tasa de carbonatación [mm/año0.5]
– Dc es el grado de carbonatación [%]
Por ejemplo, para una estructura de ingeniería civil (clase de resistencia del hormigón C40/50, 400 kg de CEM I por m³) con superficies expuestas a la lluvia, se calcula una absorción de CO2 de 1,8 kg/m2 durante una vida útil de 100 años.
Para hormigón expuesto a un clima interior seco y cubierto con pintura o papel tapiz (clase de resistencia C25/30, 280 kg de CEM I por m3), la absorción de CO2 se calcula en 2,5 kg/m2 durante una vida útil de 100 años.
Además, el anexo BB de la norma EN 16757 aborda el potencial de la carbonatación luego de la fase de uso: la absorción de CO2 durante la fase “fin de la vida útil” (es decir, demolición, trituración y almacenamiento) del hormigón depende en gran medida en cómo se manejen y almacenen los residuos de hormigón ya triturado. Ya sea que el hormigón machacado se deposite en vertederos o se recicle y reemplace materias primas, también tendrá una influencia decisiva en el potencial de carbonatación. En la norma se proporcionan estimaciones sobre la carbonatación potencial durante estas etapas en el ciclo de vida.
Las fracciones de calcio carbonatables que provienen de puzolanas como cenizas volantes o de materiales hidráulicos latentes como la escoria granulada de alto horno molida en el cemento son ignoradas [2] cuando se determina el potencial de carbonatación. Como enfoque conservador, sólo se considera para la carbonatación al calcio reactivo del clínker en el cemento Portland.
Carbonatación forzada: acelerando el proceso
Mientras que la carbonatación natural es un proceso lento que puede tomar décadas, la industria del cemento está explorando formas de acelerar este proceso a través de la carbonatación forzada o mineralización. Esta técnica busca incorporar CO2 en la pasta de cemento endurecido mucho más rápidamente que el proceso natural.
Se estima que alrededor del 80% de la pasta de cemento endurecido en los elementos de hormigón no está carbonatada al final de su vida útil. Esto representa un potencial significativo para la reincorporación de CO2. En principio, se puede reincorporar una cantidad de CO2 equivalente a la liberada durante la calcinación de la piedra caliza en la producción de clínker.
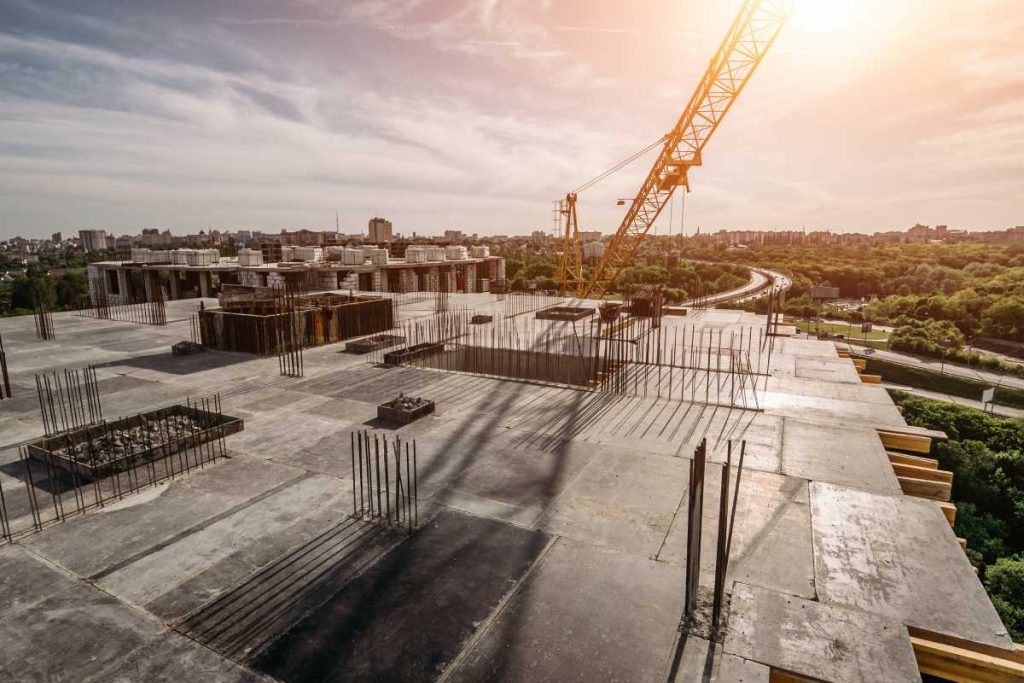
Además, existe un potencial de unión de CO2 de fases del silicato cálcico hidratado que no están basadas en el clínker o de fracciones carbonatables sin reaccionar de materiales hidráulicos o puzolánicos latentes como escoria granulada de alto horno o cenizas volantes. Cuanto más fina sea la pasta de cemento endurecida, más rápido podrá absorber CO2 en condiciones de humedad adecuadas.
En la actualidad, la industria evalúa varios métodos de procesamiento para separar la pasta fina de cemento endurecido del residuo de hormigón (por ejemplo, la fragmentación electrodinámica en combinación con varias etapas de chancado). En el caso del almacenamiento y acopio de la pasta de cemento endurecida ya separada, normalmente se carbonatan los centímetros exteriores del acopio, de modo que el potencial de carbonatación del material debería permanecer intacto un periodo de tiempo más largo.
Proceso de carbonatación forzada
El proceso de carbonatación forzada implica el tratamiento de la pasta de cemento endurecido con CO2 y humedad en condiciones controladas. Las tecnologías actuales están siendo desarrolladas para permitir una carbonatación muy rápida de la fracción de pasta de cemento endurecido.
Dependiendo del tamaño del grano de la pasta y la porosidad de la pasta de cemento endurecida reciclada, las condiciones para una carbonatación rápida incluyen:
– Contenidos de humedad de alrededor del 5 al 10% en masa.
– Temperaturas entre 40 y 60°C.
– Presión para acelerar aún más el proceso.
Temperaturas más altas reducen significativamente la solubilidad del Ca(OH)2 y por consiguiente, el progreso de la carbonatación.
Con las condiciones adecuadas de humedad y CO2, la pasta de cemento finamente molida puede carbonatarse hasta en un 80% después de aproximadamente 15 minutos y casi completamente después de 2 horas. También se pueden conseguir altas tasas de carbonatación con las composiciones de gases de combustión que son habituales en las plantas de cemento (aproximadamente, 20% de CO2).
Luego de la carbonatación de la Portlandita, el calcio de las fases de CSH reacciona con el CO2 para formar carbonato de calcio y un gel amorfo de silicato de aluminio, el que puede tener propiedades puzolánicas.
Aplicaciones y beneficios
La pasta de cemento carbonatada y finamente molida puede utilizarse como un componente principal del cemento con propiedades al menos comparables a compuestos cementosos que contengan piedra caliza o cenizas volantes. Esto puede llevar a mejoras en la resistencia a la compresión del cemento, incluso en edades tempranas.
En principio, los sistemas industriales para la carbonatación del hormigón molido o de la pasta de cemento endurecida y para el tratamiento de productos de hormigón ya existen, por ejemplo, cámaras de curado con vapor y/o CO2. Sin embargo, la carbonatación forzada del hormigón triturado o de la pasta de cemento endurecida aún no se aplica a escala industrial. Existen proyectos piloto y es necesario realizar trabajos de desarrollo para adaptar los sistemas existentes de carbonatación forzada.
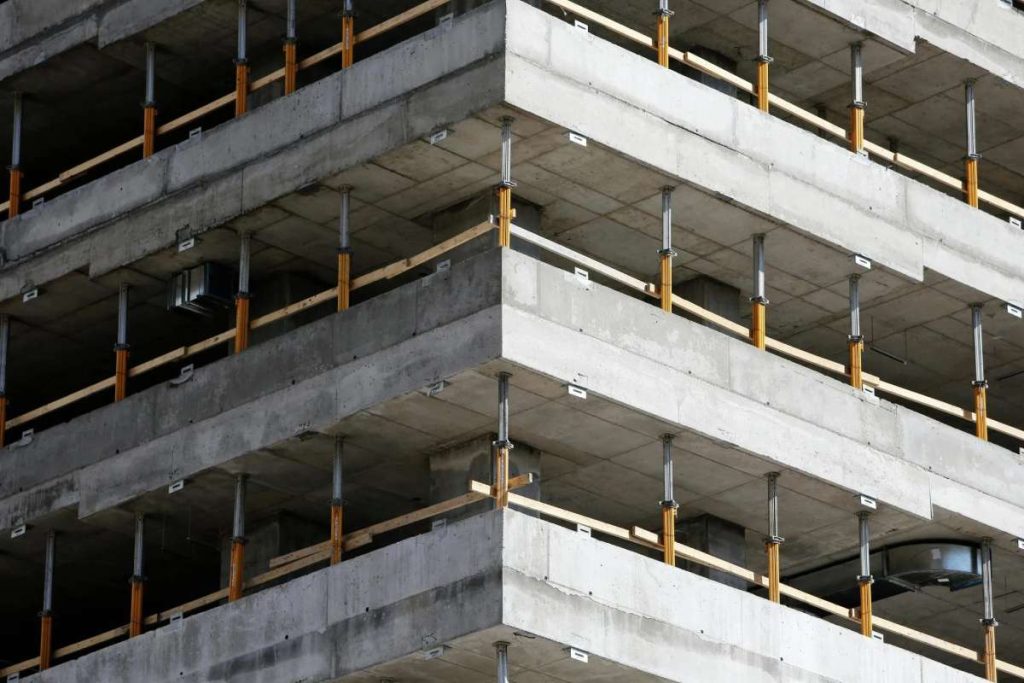
No obstante, la carbonatación forzada tiene el potencial de ser una tecnología prometedora de Captura y Utilización de Carbono (CCU) para la industria del cemento y podría ser un elemento clave adicional en el camino hacia la economía circular del cemento y el concreto.
Por una parte, el CO2 puede incorporarse y en segundo lugar, se produce un material (posiblemente puzolánico) que puede utilizarse como un componente del cemento para reducir el factor clínker.
Desafíos y oportunidades
A pesar de su potencial, la implementación a gran escala de la carbonatación forzada enfrenta varios desafíos:
1. Manejo de grandes cantidades de material: Para una tonelada de pasta de cemento endurecido (puro), teóricamente se deben procesar alrededor de 5 toneladas de hormigón triturado.
2. Separación y transporte: La separación del hormigón triturado durante la demolición y la separación de la pasta de cemento endurecido del agregado deben garantizarse. Se necesitan áreas para el procesamiento y el almacenamiento provisional lo más cerca posible del sitio de demolición o de la planta de cemento.
3. Diseño del proceso: El proceso de tratamiento con CO2 debe diseñarse para un alto rendimiento (alta absorción de CO2 con los tiempos de retención más cortos posibles), similar a un horno de cemento.
4. Proximidad a las plantas de cemento: Para un uso directo de los gases de combustión de los hornos de cemento para el tratamiento con CO2, la proximidad local entre el procesamiento del residuo de hormigón (demolición) y la planta de cemento sería de gran ventaja.
5. Nuevos flujos de fuentes: En comparación con la práctica de reciclaje de hormigón existente, se deben iniciar nuevos flujos de fuentes que tengan en cuenta la reutilización completa de los materiales utilizados en el hormigón triturado para la producción de nuevo hormigón fresco (áridos reciclados), así como para la producción de clínker y cemento (pasta de cemento reciclada).
Además de la carbonatación completa de la pasta de cemento endurecido del concreto triturado, existen otros enfoques que utilizan la carbonatación parcial de la pasta de cemento endurecido en hormigón fresco o joven para mejorar la resistencia y almacenar CO2.
Uso de CO2 para mineralizar cristalitos de CaCO3 en concreto fresco
En este proceso, se inyecta aproximadamente 0,1 – 0,3% en masa de CO2 (en relación con el peso del cemento) en el hormigón fresco durante el mezclado. El CO2 reacciona con los iones de calcio en el hormigón fresco y forma “semillas” de carbonato de calcio, que pueden mejorar el proceso de hidratación posterior hasta cierto punto, como una especie de aditivo.
La incorporación efectiva de CO2 para un hormigón promedio con 300 kg de cemento por metro cúbico es entre 0,3 y 0,9 kg de CO2 por metro cúbico. Además, se pueden lograr ahorros adicionales de CO2 indirectamente al reducir el contenido de cemento en el hormigón, aprovechando la mejora de la hidratación a través de la “siembra”. Las reducciones típicas de cemento son aproximadamente del 5% en masa.
Uso de CO2 para carbonatar elementos de hormigón
En este proceso, los elementos prefabricados sin refuerzo o productos de hormigón como bloques de mampostería o adoquines de hormigón (adocretos) se tratan con vapor y CO2 para aumentar la resistencia temprana e incorporar CO2. Esto generalmente se hace después del desmolde y luego de unas horas de secado.
Dependiendo de las dimensiones del elemento de hormigón, la duración del tratamiento (varias horas) y la concentración y presión de CO2, se reporta una absorción de CO2 de hasta el 35% en su masa en relación con la masa de cemento. La carbonatación forzada puede llevar a un aumento en la resistencia temprana del hormigón. El desarrollo de resistencia posterior resulta de la hidratación continua del aglutinante.
Es importante notar que existe poco conocimiento sobre los efectos de tales tratamientos con CO2 en la hidratación posterior o en las influencias en los aspectos de durabilidad. Además, se asume que el potencial de carbonatación natural se agota ampliamente mediante la carbonatación forzada. Una carbonatación adicional solo ocurrirá después de la trituración. Este tipo de carbonatación forzada se utiliza en algunos países en una medida muy limitada, por ejemplo, en China e India.
Más común en la producción de elementos no armados de hormigón, tales como adoquines, es el uso de cámaras de tratamiento de CO2. Generalmente, sólo los milímetros superiores de la superficie de hormigón se carbonatan rápidamente mediante un tratamiento de CO2 breve, para reducir eficazmente la tendencia a la eflorescencia de los productos de hormigón.
Para todos los sistemas de tratamiento de CO2, debe tenerse en cuenta el alto efecto corrosivo del ácido carbónico resultante sobre los elementos metálicos.
Conclusiones
La carbonatación, tanto natural como forzada, representa una oportunidad significativa para la industria del cemento en su búsqueda de reducir su huella de carbono. El reconocimiento de la carbonatación natural como un sumidero de carbono por parte del IPCC es un paso importante en la comprensión del ciclo de vida completo de los materiales basados en cemento.
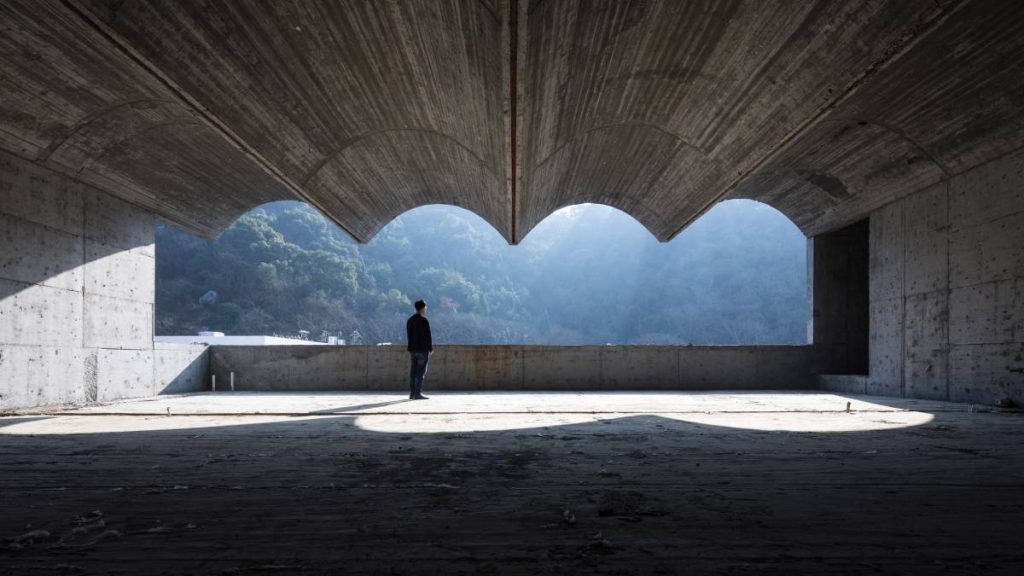
Las tecnologías de carbonatación forzada, aunque todavía en desarrollo, ofrecen el potencial de acelerar significativamente este proceso natural, permitiendo una mayor absorción de CO2 en tiempos mucho más cortos. Esto no solo podría ayudar a compensar las emisiones de la producción de cemento, sino que también podría llevar a la producción de nuevos materiales con propiedades mejoradas.
Sin embargo, la implementación a gran escala de estas tecnologías enfrenta varios desafíos, desde el manejo de grandes cantidades de material hasta la necesidad de nuevas infraestructuras y flujos de fuentes. Superar estos desafíos requerirá innovación continua, inversión y posiblemente cambios en las prácticas de la industria de la construcción y la demolición.
A medida que la industria del cemento continúa buscando formas de reducir su impacto ambiental, la carbonatación, tanto natural como forzada, probablemente jugará un papel cada vez más importante. La investigación continua y el desarrollo en esta área podrían llevar a avances significativos en la sostenibilidad de uno de los materiales de construcción más utilizados en el mundo.