Con miles de años de antigüedad, aún es posible observar e incluso utilizar, las grandes obras que el Imperio Romano dejó como legado a la humanidad. ¿Cómo se mantienen en pie? ¿Qué propiedades tiene el hormigón que se utilizó para su construcción? Un grupo internacional de investigadores analizó muestras y realizó un increíble hallazgo, que podría cambiar la manera en que se construye con el material en la actualidad.
Cuando se quiere destacar un aspecto positivo -de los muchos que posee- del hormigón, de inmediato la durabilidad es el primer atributo que se menciona. Para demostrar qué tan durable es el material, el ejemplo es siempre el mismo: las construcciones romanas.
Muchas de las obras de ingeniería que ejecutaron en la época del Imperio Romano, algunas de las cuales se mantienen en pie y en uso hasta nuestros días, se fabricaron con hormigón. Un ejemplo de ello es el Panteón Romano, que data de la época del emperador Augusto (24 a. de C. – 14 d. de C.), que en la actualidad es un importante sitio turístico y cuyo domo ostenta el título de ser la estructura de hormigón no armado más grande del mundo.
Al comparar esa edificación romana, o alguno de los acueductos que aún perduran hasta nuestros días (algunos incluso en uso) con otras estructuras más modernas que, luego de unas décadas, comienzan a desgastarse, los investigadores siempre se preguntaron cuál era la “receta” que hacía al hormigón producido por los romanos durar más.
Esta pregunta motivó a un grupo de investigadores del Massachusets Institute of Technology (MIT), la universidad de Harvard, junto con laboratorios de Italia y Suiza, a realizar una serie de estudios, los que finalmente, dieron con el “ingrediente secreto” que hace tan durable al hormigón producido durante el Imperio Romano.
Todo está en la cal
Durante muchos años, distintos académicos e investigadores asumieron que la clave de la durabilidad del hormigón de esa época se basaba en un componente: material puzolánico como la ceniza volcánica proveniente del área de Puzzuoli, en la bahía de Nápoles. Este tipo de ceniza específica se transportó vía marítima a distintos puntos del Imperio Romano para utilizarla en las construcciones.
Sin embargo, la investigación de este grupo internacional de académicos -publicada a comienzos del mes de enero en la revista Science Advances– demostró que al analizar detalladamente muestras del hormigón, no sólo se encontró puzolana. También, aparecieron pequeños elementos minerales blancos que siempre se habían categorizado como un componente extendido de los hormigones romanos.
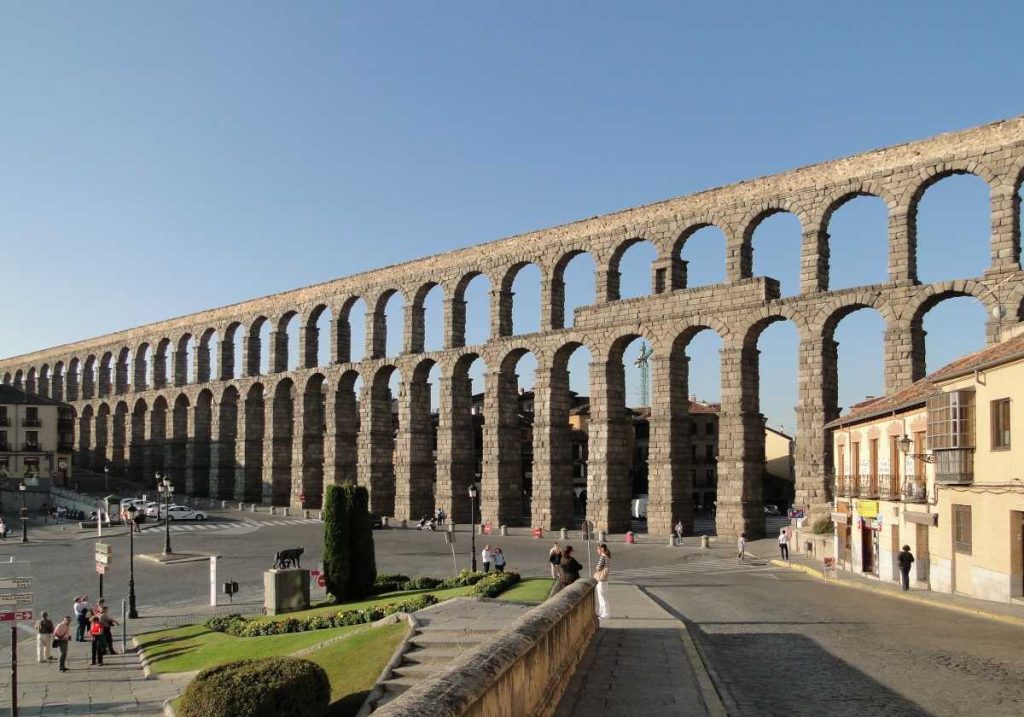
Estos elementos, denominados clastos de cal, siempre se asociaron a un pobre control de calidad del material. “Esa noción siempre me molestó”, comentó Admir Masic, académico del MIT y uno de los participantes de la investigación. “Si los romanos pusieron tanto esfuerzo en fabricar un material de construcción increíble, siguiendo todas las recetas al detalle sobre cómo optimizarlo, ¿por qué pondrían tan poco esfuerzo en asegurar que el producto final estuviese bien mezclado? Tenía que haber algo más”, comentó.
Mezcla caliente para hormigón autorreparable y más resistente
Al mapear estas partículas de cal -utilizando imágenes multiescala de alta resolución y técnicas de mapeo químico desarrolladas por el profesor Masic- los investigadores realizaron nuevos hallazgos sobre potenciales funcionalidades de los clastos.
Una de las principales dudas del estudio era qué sucedía cuando los romanos incorporaban la cal al hormigón. Históricamente, se asumía que ésta se mezclaba con agua para formar la pasta, pero eso no podía explicar la presencia de los clastos. Analizando las muestras, los investigadores encontraron que las partículas blancas también contenían carbonato de sílice. Asimismo, análisis espectroscópicos brindaron pruebas que esto se formó a temperaturas extremas, lo que se esperaría de una reacción exotérmica producida al utilizar cal viva en vez de, o junto con, cal apagada en la mezcla.
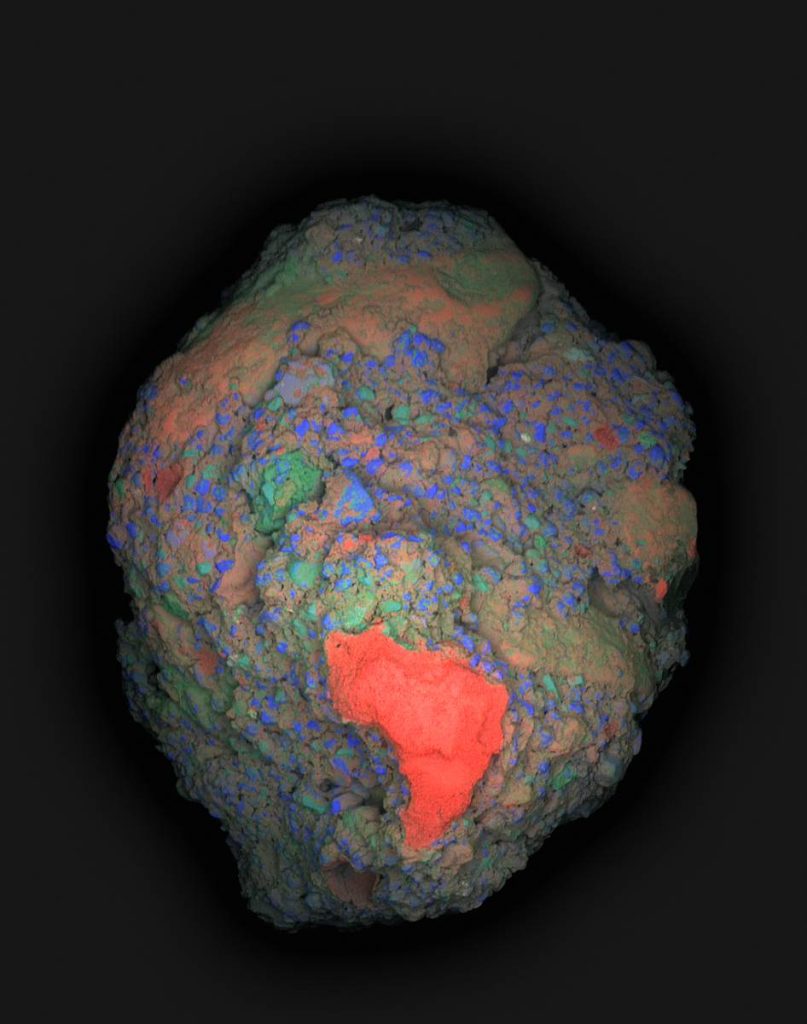
Así, el equipo llegó a la conclusión que la mezcla se realizaba en caliente. “Los beneficios de la mezcla caliente son dobles”, dijo Masic. “Primero, cuando el hormigón en general se calienta a altas temperaturas, permite procesos químicos que no son posibles si sólo se utiliza cal apagada, produciendo componentes asociados a esas altas temperaturas que de otro modo no se formarían. Segundo, esta temperatura aumentada reduce significativamente los tiempos de curado y fraguado ya que todas las reacciones se aceleran, permitiendo una construcción mucho más rápida”.
Hormigón que resiste el paso de la historia
Al estar en la mezcla en caliente, los clastos de cal desarrollan una arquitectura de nanopartículas característicamente frágil que crea una fuente de calcio reactiva que, como los investigadores propusieron, puede brindar propiedades autorreparantes. Así, al aparecer una fisura en el hormigón, estas nanopartículas llegaban al área a través de los clastos de cal de gran superficie. Este material, al reaccionar con agua, crea una solución saturada en calcio que puede recristalizarse en carbonato de calcio y reparar la fisura, o reaccionar con los materiales puzolánicos para brindar más resistencia al material.
Para probar que esto, efectivamente, es el responsable de la gran durabilidad del hormigón producido por los romanos, el equipo realizó muestras de hormigón con mezcla en caliente, las que incorporaron tanto formulaciones antiguas como actuales. Estas probetas se sometieron a ensayos para generar fisuras y así, pasar agua sobre estas. Los resultados evidenciaron que, a las dos semanas, las fisuras estaban completamente selladas.
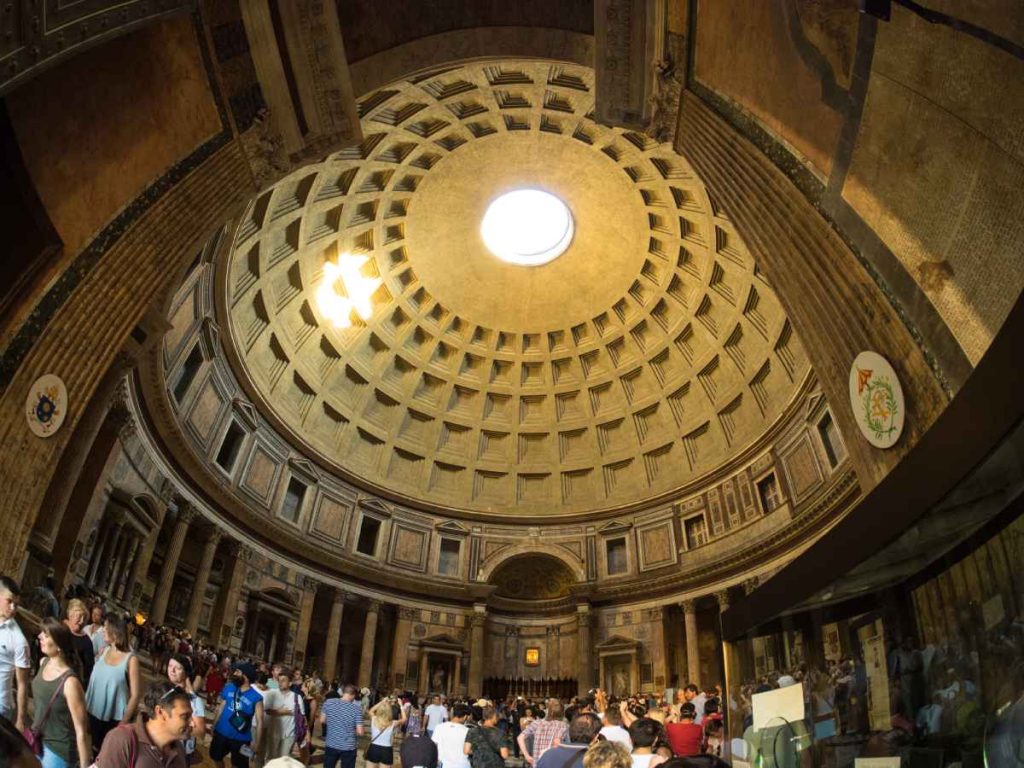
“Es emocionante pensar sobre cómo estas fórmulas para hormigones mucho más durables podrían expandir no sólo la vida útil de estos materiales, además, podrían mejorar la durabilidad de las formulaciones para hormigón impreso 3D”, comentó el académico.
El equipo, compuesto por Janille Maragh, PhD en Ingeniería Civil y Medioambiental del MIT; Paolo Sabatini, cofundador y CEO en DMAT, Italia; Michel Di Tommaso, del Instituto Meccanica dei Materiali, Suiza; y James Weaver, del Wyss Institute for Biologically Inspired Engineering, de la Universidad de Harvard, busca ahora generar pruebas a escala industrial de este tipo de hormigón, con el objetivo de ponerlo a disposición del público.