La industria de la construcción tiene distintos desafíos a los que responder, que van desde el aspecto medioambiental a la productividad. Los desarrollos en shotcrete -especialmente, los que se refieren al desarrollo de resistencia temprana en esta tecnología- podrían ser la respuesta a esos retos.
Autora: Christine Poulin, ingeniera civil, Máster en Hormigón Proyectado de la Universidad Laval.
Fuente: Shotcrete Magazine
Traducción: Felipe Kraljevich M.
A medida que la industria de la construcción enfrenta nuevas necesidades y desafíos, el shotcrete experimenta una constante evolución a través de la investigación y el desarrollo en materiales, equipos y métodos constructivos.
Ampliamente utilizado en reparaciones de hormigón y aplicaciones subterráneas, el shotcrete ofrece numerosas ventajas sobre el hormigón convencional encofrado y vertido. Su distintiva técnica de colocación neumática emplea pulverización de alta velocidad para colocar el hormigón transportado en una manguera a la boquilla sobre una superficie receptora.
Reconocido por su conveniencia y eficiencia económica, el shotcrete a menudo reduce o elimina la necesidad de encofrados, permite el acceso a áreas de trabajo complejas y permite espesores y acabados dentro de tolerancias estrechas. Debido a su alto efecto de compactación, el shotcrete alcanza una excelente adhesión a la superficie receptora y encapsula eficazmente a las barras de refuerzo, ambas consideraciones de diseño cruciales para los proyectos (ACI PRC-506-22, 2022).
1.- Procesos del shotcrete
Existen dos procesos distintivos para el shotcrete u hormigón proyectado: el shotcrete húmedo (o de mezcla húmeda) y el seco (mezcla seca). En el proceso húmedo o de mezcla húmeda, la mezcla de hormigón, mezclada cuidadosamente con agua, se introduce a una bomba de hormigón y se transporta por una manguera hacia una boquilla. A continuación, se añade aire comprimido a la boquilla para alcanzar una alta velocidad y asegurar una compactación adecuada del hormigón en la superficie receptora. La Figura 1 ilustra la aplicación del shotcrete húmedo o de mezcla húmeda.
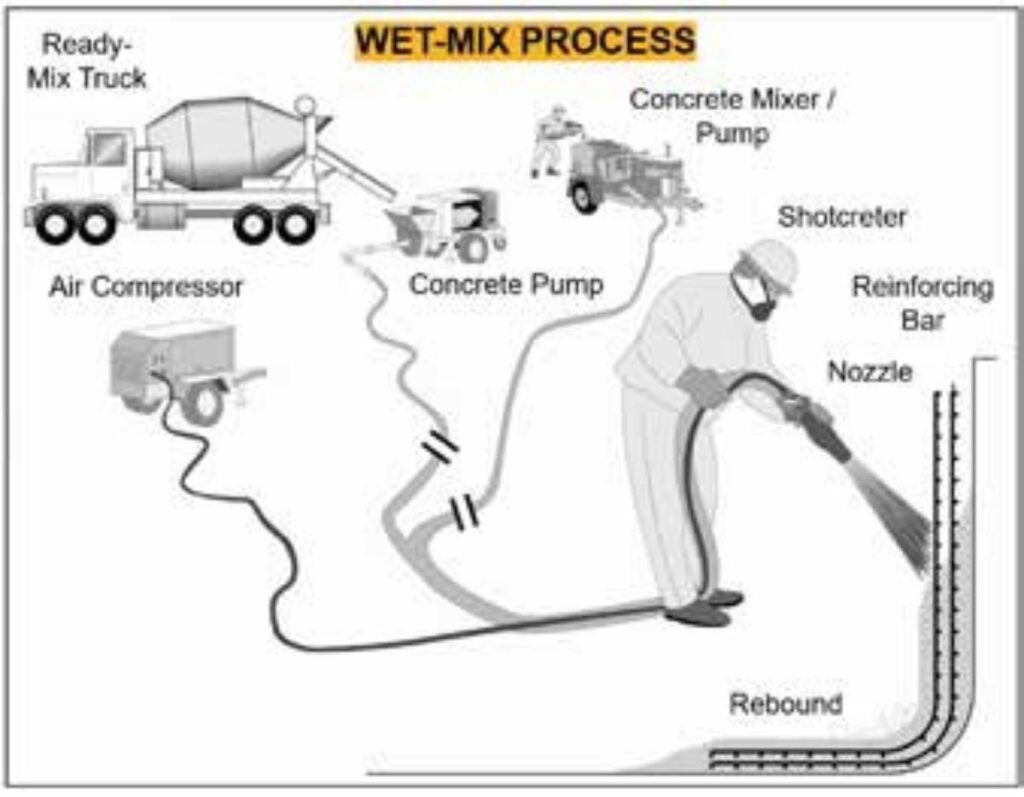
En el proceso seco o de mezcla seca, sólo se utilizan componentes premezclados, sin agua, para alimentar a la pistola de shotcrete. El aire comprimido se utiliza para transportar los materiales de hormigón secos (o ligeramente húmedos si se usa un prehumidificador) a través de la manguera hasta el cuerpo de una boquilla. El cuerpo de una boquilla incluye un aro de agua por el que se introduce agua presurizada para que se mezcle de manera uniforme con los materiales de hormigón. De forma simultánea, el hormigón se proyecta a través de la boquilla a alta velocidad sobre la superficie receptora.
Existen muchas variantes reconocidas por la industria para asegurar la mezcla homogénea y reducir la emisión de polvo con el shotcrete seco o de mezcla seca, tales como el uso de un prehumidificador o la colocación del anillo de agua en la manguera de suministro hasta 3 metros antes de la boquilla, también conocido como boquilla hydromix. Estas dos variantes se distinguen por el punto por el cual se introduce el agua a través del cuerpo de la boquilla antes de proyectar el hormigón. La Figura 2 ilustra la aplicación de shotcrete seco o de mezcla seca con el uso de un prehumidificador.
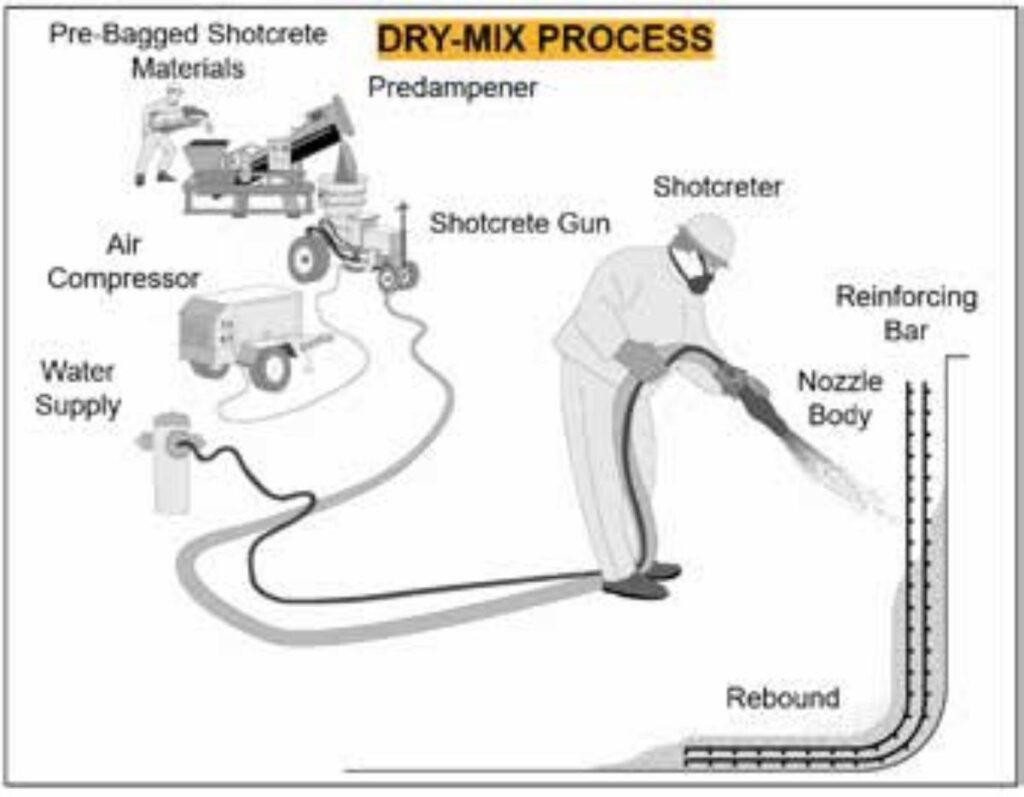
Cualquiera de estos dos procesos puede ser el adecuado para diversos requisitos de construcción Sus características distintivas hacen que el proceso de mezcla húmeda o seca sea más el adecuado para una aplicación específica debido a las diferencias en el equipo, las características operativas, disponibilidad de los materiales de hormigón y características de la colocación. De acuerdo con la Guía para Shotcrete del Comité 506 del American Concrete Institute, ACI, (ACI PRC-506-22, 2022), la Tabla 1 ilustra las diferencias y características principales que ofrecen ambos procesos de shotcrete.
Proceso húmedo o de mezcla húmeda | Proceso seco o de mezcla seca |
El agua de la mezcla se controla en el equipo de mezcla y se puede medir con precisión | Control instantáneo sobre el agua de la mezcla y la consistencia de la mezcla en la boquilla para cumplir con las condiciones variables del campo |
Mayor garantía de que la mezcla de agua está completamente mezclada con los otros ingredientes | Más adecuado para colocar mezclas que contengan áridos ligeros o materiales refractarios |
Menor polvo y pérdida de material cementoso durante la operación de disparo | Las mangueras de suministro son más fáciles de manejar |
Normalmente tiene menos rebote, resultando en menor pérdida | Muy adecuado para condiciones en las que no se puede predecir el tiempo de colocación del shotcrete o este es intermitente |
Mayor volumen por tamaño de manguera | Menor volumen por tamaño de manguera |
Como se ilustra, los procesos de shotcrete de mezcla húmeda o seca se complementan entre sí, ofreciendo a los diseñadores y contratistas gran versatilidad para su uso en diversas aplicaciones, las que van desde reparaciones en el hormigón hasta construcciones subterráneas como túneles y minería.
Mientras que el proceso de mezcla húmeda brinda una mayor capacidad de volumen y un nivel de residuo de material relativamente más bajo debido a un menor rebote, el proceso de mezcla seca utiliza equipos más livianos y pequeños, lo que lo hace más adecuado para aplicaciones específicas. El proceso de mezcla seca también ofrece un control de consistencia instantáneo para adaptarse a las condiciones del terreno.
Normalmente, los profesionales con más experiencia en la industria, como los contratistas de shotcrete, son los más indicados para determinar cuál proceso es el más adecuado para cada aplicación en específico y son excelentes asesores para garantizar el éxito de las obras con shotcrete.
En la industria de la construcción actual, existe una creciente demanda por una mayor eficiencia y velocidad para cumplir con plazos ajustados y, al mismo tiempo, garantizar un acceso seguro. Como resultado, la industria está mejorando continuamente las mezclas de shotcrete ya sea integrando aglutinantes o fibras alternativos, junto con diversos aditivos. Estos esfuerzos continuos de investigación y desarrollo permiten a la industria cumplir con rigurosos estándares de calidad, transformando al shotcrete en una de las principales técnicas constructivas para garantizar tanto seguridad como rendimiento.
Trabajar bajo tierra conlleva sus propios desafíos, desde condiciones exigentes hasta acceso limitado a equipos. En estos entornos, donde contratistas y proveedores deben cumplir con estrictos estándares y plazos ajustados, se suele necesitar shotcrete de resistencias tempranas aceleradas.
La necesidad por una rápida movilización de equipos, disponibilidad inmediata del hormigón y la posibilidad de situaciones de paradas y arranques durante la aplicación exigen soluciones eficaces. Por este motivo, Sika Canadá lleva desarrollando de manera constante varias tecnologías en shotcrete seco o de mezcla seca para mejorar sus prestaciones y cumplir con las demandas de estas complejas aplicaciones.
2.- Tecnologías del Cemento
Existe una amplia variedad de opciones de cemento para producir mezclas de shotcrete de alta calidad según las necesidades de los proyectos. Uno de los más comunes que se utilizan en la industria es el cemento Portland tradicional (OPC, en sus siglas en inglés). Cuando se combina con un acelerante de fraguado de alto nivel, el shotcrete a base de este cemento logra un fraguado y un desarrollo de resistencia a edad temprana más rápidos.
El hormigón a base de cemento Portland tradicional comprende cuatro fases principales: silicatos de calcio (C2S y C3S), aluminato tricálcico (C3A) y aluminoferrita tetracálcica (C4AF). El producto principal de la hidratación del cemento Portland tradicional, que resulta de la reacción de C2S y C3S en la solución, es el hidrato de silicato de calcio (CSH), lo que contribuye a la gran rigidez del sistema.
En la producción de cemento, se agrega yeso, que se utiliza como una fuente de sulfato de calcio para inducir un período de baja actividad química, denominado la fase latente (un paso necesario para evitar el fraguado instantáneo). La fase latente asegura el requisito de trabajabilidad para la colocación adecuada del hormigón en sitio y generalmente, puede durar hasta 4 horas, dependiendo de la temperatura y las condiciones del ambiente. Una vez que los sulfatos de calcio se agotan y la solución se satura con iones, se inicia el fraguado inicial del shotcrete a base de cemento Portland tradicional, seguido por una ganancia de resistencia de alrededor de 15 MPa a las 24 horas.
Los acelerantes de fraguado se utilizan ampliamente en el shotcrete para acelerar rápidamente la velocidad de reacción de los sistemas estándar de cemento Portland tradicional. Sika Canadá promueve sólo acelerantes de fraguado sin álcalis, comúnmente utilizados en la actualidad para mejoras el desempeño y durabilidad del shotcrete, a diferencias de los acelerantes altamente alcalinos que se utilizaban antiguamente en la industria.
Estos acelerantes sin álcalis, que se componen principalmente de sulfatos de aluminio, impactan a la hidratación cinética al reducir el tiempo de fraguado del shotcrete a base de cemento Portland tradicional entre 5 a 10 minutos. Ellos contribuyen al desarrollo de resistencia temprana con un alza de aproximadamente 1 MPa por hora, permitiendo al shotcrete alcanzar resistencias de alrededor de 21 MPa dentro de las 24 horas cuando se utiliza un acelerante de fraguado de alto nivel.
Sin embargo, esta solución tiene limitaciones en términos de alcanzar ganancias de resistencia temprana en este sistema estándar. El uso excesivo de acelerante de fraguado durante la colocación del shotcrete también puede impactar de forma negativa en la calidad, resistencia y durabilidad del hormigón in situ (Moran & Jolin, 2022). Como resultado, existen cementos alternativos, como los cementos de sulfoaluminato de calcio (CSA), que se encuentran disponibles comercialmente y sirven como una excelente alternativa para alcanzar resistencias iniciales muy altas.
El hormigón a base de cemento de sulfoaluminato de calcio consiste en una fase predominante, la ye’elimita (C4A3S), la que desempeña un rol fundamental en la hidratación general del sistema. Esta reacción se ve influenciada por las proporciones de los sulfatos de calcio (generalmente semihidratados y anhidros) y cal hidratada.
Al disolverse, la reacción química es casi instantánea debido a la formación de etringita, el principal producto de hidratación del cemento CSA. Este hidrato reacciona rápidamente debido a su mineralogía, permitiendo alcanzar resistencias tempranas iniciales muy altas. Comparado con el cemento Portland tradicional, el shotcrete a base de cemento CSA exhibe una ganancia de resistencia de alrededor de 21 MPa a las 3 horas, con un tiempo de fraguado final prácticamente instantáneo.
La Figura 3 ilustra la correlación entre el desarrollo de resistencia a la compresión a edad temprana para mezclas de shotcrete basadas en cemento Portland tradicional, con y sin un alto nivel de acelerante de fraguado, y cemento CSA.
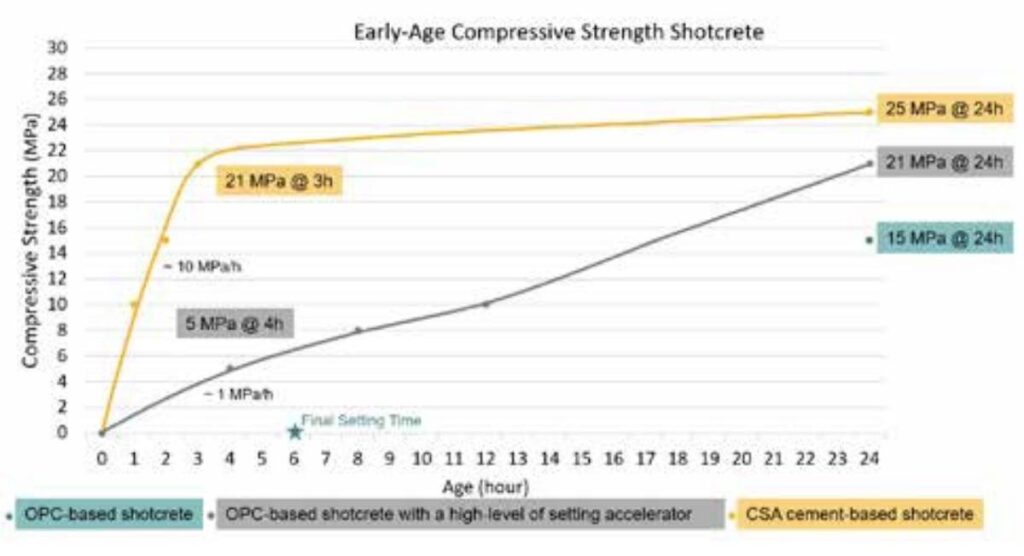
El shotcrete a base de cementos tipo CSA exhibe un desempeño extraordinario en comparación al hormigón proyectado a base de cemento Portland tradicional, ya sea sin o con un alto nivel de acelerante de fraguado. Si bien el shotcrete a base de cemento Portland Tracicional sin acelerante de fraguado aún no alcanza su fraguado final, el desarrollo de resistencia del shotcrete a base de cemento CSA es cuatro veces más alto que el hormigón proyectado a base de cemento Portland tradicional con un alto nivel de acelerante de fraguado.
Como referencia, el resultado de la resistencia a la compresión del shotcrete a base de cemento Portland tradicional sin acelerante de fraguado sólo se muestra a las 24 horas. El sistema de este cemento no está diseñado para lograr un desarrollo de resistencia a temprana edad y su resistencia es insuficiente para realizar ensayos poco después de su colocación. Necesita cerca de 6 horas para alcanzar su tiempo final de fraguado, mientras que el shotcrete a base de cemento Portland tradicional con un alto nivel de acelerante de fraguado toma lugar en los primeros minutos después de su proyección, y el shotcrete a base de cemento tipo CSA fragua casi de forma instantánea.
Además de sus ventajas en cuanto a resistencia rápida, el proceso de hidratación único del cemento tipo CSA ofrece propiedades de compensación a la retracción. Existen alternativas a las mezclas de shotcrete a base de cemento Portland tradicional que también entregan estabilidad volumétrica junto con un rápido desarrollo de resistencia.
Esto se demostró con un proyecto de investigación en la Universidad Laval (Lemay, 2013), en el que se utilizaron mezclas ternarias compuestas por cemento Portland tradicional, cemento de aluminato de calcio (CAC) y sulfato de calcio. Sin embargo, la dosificación adecuada del sulfato de calcio es fundamental para asegurar la estabilidad volumétrica del sistema; de otra forma, puede ocurrir una expansión incontrolada. Esta cinética compleja se ilustró eficazmente en la Figura 4, destacando la interacción entre estos componentes luego de la adición del sulfato de calcio.

Este umbral expansivo observado en sistemas principalmente compuestos de cemento Portland tradicional y cemento tipo CAC demuestra cómo una dosis excesiva de sulfato de calcio puede llevar a una expansión no deseada del hormigón. El límite exacto de expansión entre cada sistema aún no está lo suficientemente claro debido a la variabilidad en las fuentes de estos componentes, por lo que se requiere mayor investigación para comprender mejor a estos sistemas ternarios (Lemay, Jolin & Gagné, 2014).
Por lo tanto, el uso de cemento tipo CSA proveniente de la industria, ya premezclado, asegura un hormigón estable al emplear esta tecnología, beneficiándose así de un rápido desarrollo de resistencia temprana y propiedades de compensación a la retracción. De hecho, el cemento tipo CSA, normalmente posicionado a la izquierda del diagrama, que contiene fases de aluminato de calcio, permanece por debajo del umbral de expansión descontrolada.
Desde un punto de vista ecológico, es relevante mencionar que el cemento tipo CSA es ambientalmente más amigable. Su eficiencia de producción es mayor que la del cemento Portland tradicional, lo que se traduce en emisiones de CO2 más bajas por tonelada de cemento. Estas ventajas son particularmente valiosas considerando los actuales desafíos que enfrenta la industria (Juenger et al., 2011).
En el hormigón tradicional de encofrado y vertido, se suelen utilizar retardantes de fraguado para asegurar la necesaria trabajabilidad del hormigón a base de cemento tipo CSA. Sin embargo, con shotcrete seco o de mezcla seca, no se requieren retardantes de fraguado ya que la mezcla se realiza en la boquilla justo antes de proyectar el hormigón. Esta excepcional combinación permite el desarrollo de una tecnología de alto rendimiento que ningún otro método de hormigón puede igualar.
3.- Caso de estudio
Un excelente caso de estudio que muestra la efectividad del shotcrete seco o de mezcla seca a base de cemento tipo CSA es la construcción de túneles y estructuras subterráneas dento del proyecto Eglinton Crosstown en Toronto, Canadá.
El proyecto Eglinton Crosstown se erige como la mayor obra de infraestructura de Canadá, inicialmente estimada en $8,4 billones de dólares canadienses en 2011, pero en la actualidad valorada en $12,5 billones de dólares canadienses (USD $8,7 billones). Este proyecto implica la construcción de un sistema de tren liviano (LRT) diseñado para transportar a viajeros de este a oeste dentro de la ciudad de Toronto.
El proyecto, que comenzó en 2011, estaba previsto originalmente que se completara en 2021, pero encontró retrasos, lo que llevó a una nueva meta de finalización revisada para finales de 2024. Extendiéndose por un corredor de 19 km, el proyecto incluye una sección subterránea de 10 km e incorpora 25 estaciones junto con 2 conexiones a la línea de metro Toronto Transit Commission ya existente, ilustrada en las estrellas de la Figura 5 (KPMB, 2024). La estación Cedarvale se ubica en la intersección Eglinton West y la estación Yonge, en la intersección Eglinton.

Los desafíos técnicos que se plantearon en estas intersecciones de las líneas de metro existentes y la futura línea LRT, donde era necesario construir un nuevo túnel debajo del túnel de metro en servicio operativo, requirieron el uso de técnicas de apuntalamiento. Mientras el contratista utilizó shotcrete seco o de mezcla seca con un alto nivel de acelerante de fraguado en la estación Cedarvale, se uso shotcrete de mezcla seca a base de cemento tipo CSA en la estación Yonge, como muestran las Figuras 6 y 7.
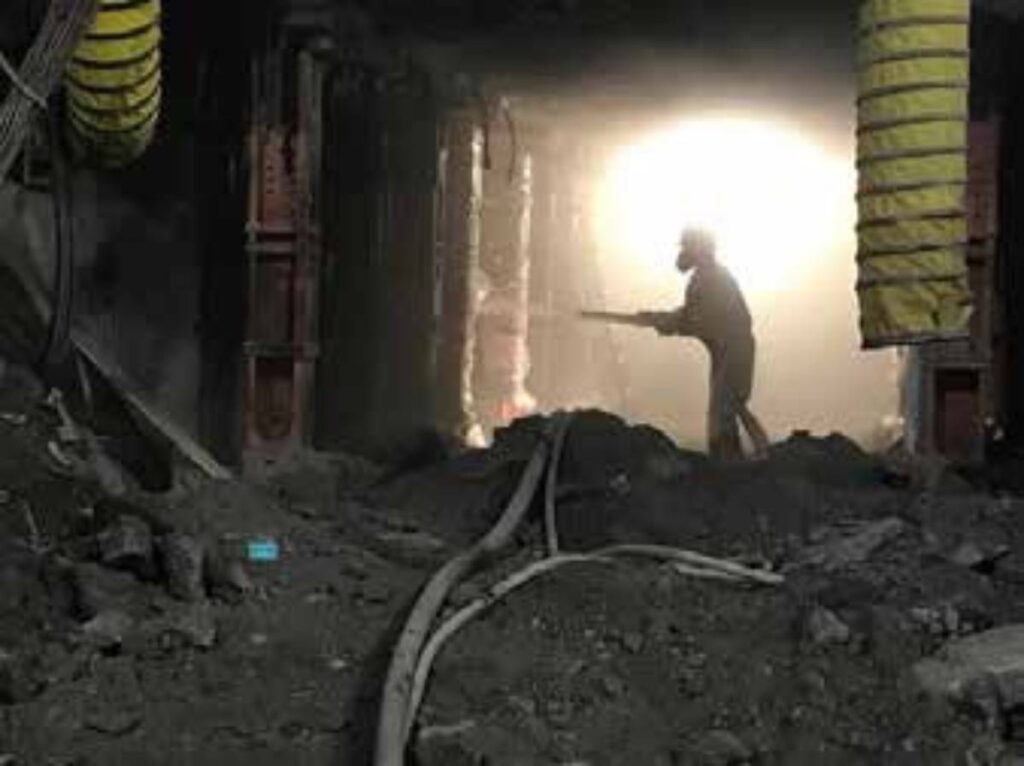
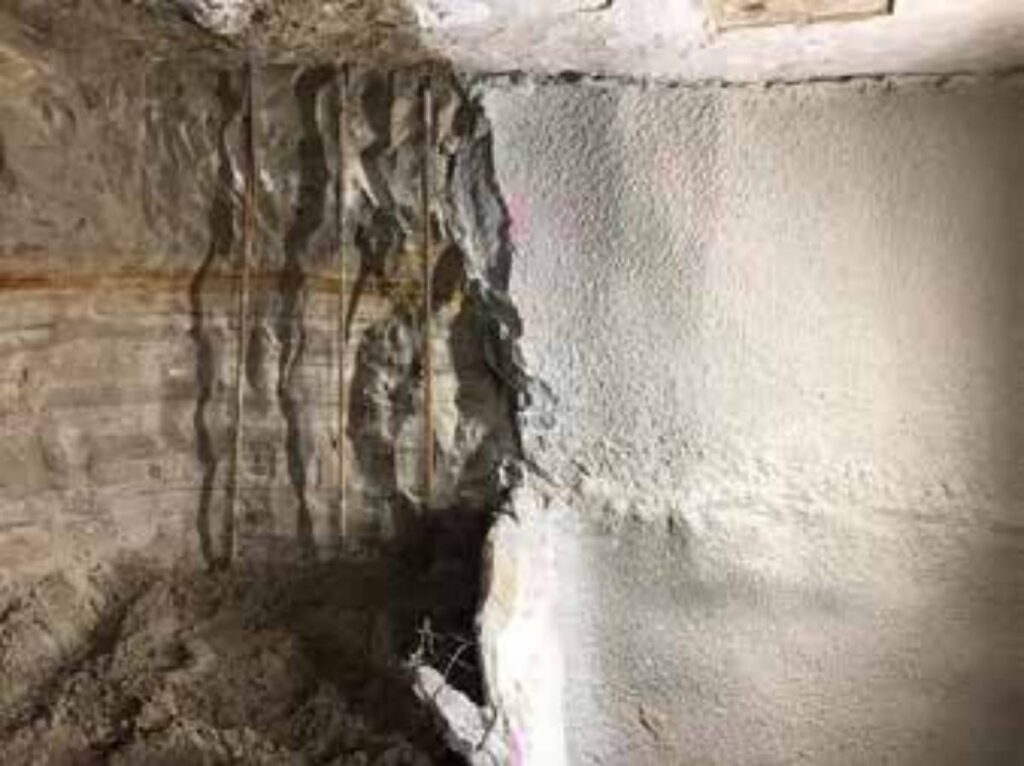
El shotcrete de mezcla seca a base de cemento tipo CSA jugó un rol importante en la estación Yonge ya que aseguró una excavación rápida y segura. El proyecto demandaba el desarrollo de una resistencia temprana específica que un shotcrete con acelerante de alto nivel no podía alcanzar.
El contratista cumplió con estos requerimientos con una mezcla de shotcrete basada en cemento tipo CSA, garantizando la finalización oportuna y duradera de los revestimientos y estructuras de soporte del túnel. Además, la versatilidad del shotcrete de mezcla seca resultó ventajosa para transitar por el complejo terreno subterráneo y cumplir con los estrictos requisitos del proyecto. Los resultados obtenidos con el shotcrete de mezcla seca a base de cemento tipo CSA en el proyecto fueron de alrededor de 10 MPa en una hora y de 20 MPa a las 2 horas. Las resistencias se midieron in situ en el tiempo requerido para cumplir con los requisitos del proyecto.
Para los ensayos a tan temprana edad, las mediciones de resistencia se llevaron a cabo utilizando el método de ensayo de viga con una bomba hidráulica manual y un manómetro calibrado, siguiendo el ensayo estándar ASTM C116 (retirada) (ASTM, 1999), como se muestra en la Figura 8.
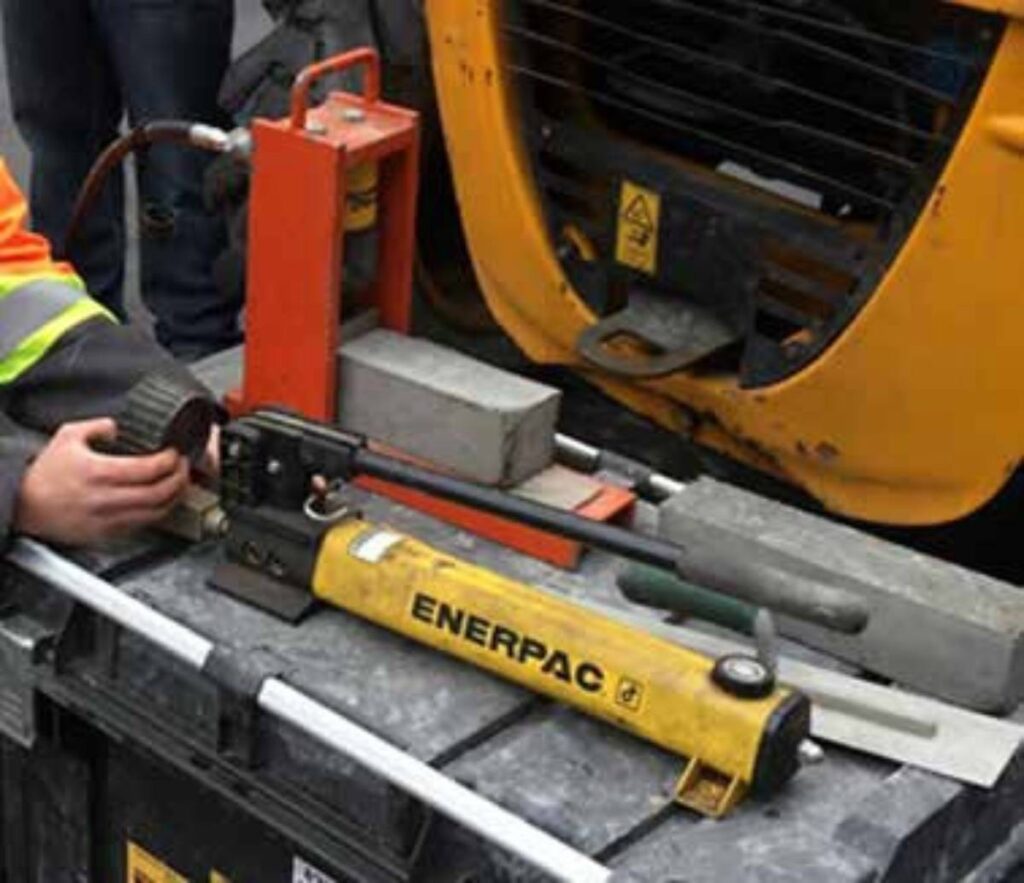
Como explicaron Heere & Morgan (2002), aproximadamente 24 horas después de la proyección inicial, la resistencia a la compresión del shotcrete generalmente suele ser insuficiente para utilizar la extracción de testigos u otros procedimientos de ensayo convencionales.
Por lo mismo, se desarrolló el método de ensayo de viga, donde cada lado de la viga a flexión funciona como cubos modificados para la carga. Este método de ensayo se considera el más adecuado para ensayar el shotcrete a edad temprana y tiene la ventaja sobre otros métodos indirectos de ensayo de shotcrete a edad temprana (como las sondas o pasadores penetrantes, y los ensayos por extracción) de medir directamente la resistencia a la compresión.
Las características específicas del shotcrete seco o de mezcla seca a base de cemento tipo CSA seleccionado, además de los métodos ensayos empleados, ofrecieron información valiosa respecto a las propiedades y el desempeño del shotcrete de mezcla seca en esta aplicación crítica. Este caso de estudio destaca como Sika Canadá, con su tecnología, contribuyó al éxito del proyecto Eglinton Crosstwon, subrayando su efectividad en desarrollos de infraestructura a gran escala.
4.- Conclusiones
La industria de la construcción debe adoptar nuevas tecnologías e innovaciones que le permitan enfrentar los desafíos actuales. Gracias a sus propiedades únicas, el shotcrete resalta como una solución de colocación, cumpliendo con los estándares de proyecto más estrictos y ofreciendo beneficios inigualables en comparación con el hormigón vertido tradicional.
Al combinar las ventajas del shotcrete con cementos alternativos, el shotcrete seco o de mezcla seca a base de cemento tipo CSA ofrece resultados de alto desempeño bajo condiciones de obra complejas. Esta solución única logra una resistencia a la compresión cercana a los 21 MPa dentro de 3 horas, mientras que el shotcrete a base de cemento Portland tradicional con un acelerante de fraguado requiere de 24 horas para alcanzar un resultado similar. Como resultado, el shotcrete de mezcla seca a base de cemento tipo CSA permite una mayor eficiencia y rapidez para cumplir con los plazos de los proyectos.
El proyecto Eginton Crosstown es un excelente ejemplo de cómo Sika Canadá, en estrecha colaboración con los contratistas y diseñadores, aborda de manera exitosa estos desafíos al implementar soluciones de vanguardia en túneles y la industria minera
Referencias
1. ACI PRC-506-22. (2022). Shotcrete – Guide. Farmington Hills, MI: American Concrete Institute Committee 506.
2. Morgan, D. R., & Jolin, M. (2022). Shotcrete Materials, Performance and Use. Taylor & Francis Group, UK, 500 p.
3. Lemay, Jean-Daniel. (2013). Développement de béton projeté à ultra-haute résistance initiale. Département de Génie Civil. Québec, Université Laval. M.Sc., p. 127.
4. Lemay, J.-D., Jolin, M., & Gagné, R. (2014). Ultra Rapid Strength Development in Dry-Mix Shotcrete for Ultra Rapid Support in Challenging Mining Conditions. American Shotcrete Association magazine, Fall 2014, p. 14-19.
5. Juenger, M. C. G., F. Winnefeld, J. L. Provis et J. H. Ideker (2011). Advances in alternative cementitious binders. Cement and Concrete Research, Vol.41, No.12, p. 1232-1243.
6. KPMB. (2024). Eglinton Crosstown makes infrastructure exciting again: Marianne McKenna sitting on Metrolinx board. Retrieved from https://www.kpmb.com/news/eglinton-crosstown-makesinfrastructure-exciting-again-marianne-mckenna-sitting-on-metrolinxboard/
7. ASTM. (1999). ASTM C116-90 (withdrawn): Standard Test Method for Compressive Strength of Concrete using Portions of Beams Broken in Flexure. ASTM, West Conshohocken, PA: ASTM International.
8. Heere, R. & Morgan, D.R. (2002). Determination of Early‐Age Compressive Strength of Shotcrete, American Shotcrete Association magazine, Vol.4, No.2, p. 28-31.