Este artículo, publicado originalmente en la revista Shotcrete Magazine de la American Shotcrete Association, da cuenta de la evolución y los avances que tiene la construcción con esta metodología constructiva tanto en Estados Unidos y Canadá, ya sea en túneles para uso civil como en minería, además de los últimos avances respecto a la construcción con shotcrete para elementos estructurales masivos.
Autores: Lihe (John) Zang, Ph.D., P.Eng., F.ACI y Dudley (Rusty) Morgan, Ph.D., F.ACI.
Nota: Este paper se presentó en octubre de 2021, durante la conferencia de la Asociación de Túneles de Canadá en Toronto.
Abstract
En años recientes, el shotcrete se ha utilizado de manera amplia para el sostenimiento del terreno en túneles civiles y minas de Norteamérica. Las tecnologías del hormigón proyectado han avanzado ya sea con robustos robots pulverizadores, diseños de mezcla para shotcrete de alto desempeño y refuerzo con fibras de alto desempeño, en combinación con una rigurosa certificación para operadores de boquilla de shotcrete e inspecciones de control de calidad y programas de ensayo. Los ingenieros diseñadores y contratistas están utilizando cada vez más a menudo el shotcrete para diversas aplicaciones subterráneas, incluyendo el sostenimiento del terreno y los revestimientos finales en túneles en terreno suave y roca dura, como también en proyectos de reparación y rehabilitación de túneles ferroviarios y otras aperturas subterráneas. Grandes cavernas subterráneas se construyeron utilizando shotcrete como revestimiento inicial en San Francisco y Los Ángeles, y tanto para el revestimiento inicial como final en New York y Washington D.C.. Este artículo se enfoca en desarrollos tecnológicos recientes para el shotcrete a utilizar en proyectos subterráneos, los que nacen desde la experiencia de los mismos proyectos y entregan importantes lecciones aprendidas. También, demuestra que un adecuado control de calidad y programas de certificación del shotcrete son críticos para el éxito de proyectos con shotcrete.
Introducción
El shotcrete es un proceso para el transporte neumático de materiales de hormigón a altas velocidades hacia una superficie receptora para conseguir la compactación in situ. Si bien el shotcrete se ha utilizado por cerca de un siglo, el uso de esta metodología para el soporte del terreno en túneles, minas, postes y otras estructuras subterráneas se volvió cada vez más popular durante la pasada década (Ref. 1-9). Los avances en la tecnología del shotcrete incluyen el uso de mezclas para el alto desempeño del material, pulverizadores robóticos avanzados, los que se operan a través de control remoto, aceleradores libres de alcalinos y fibras de alto desempeño, incluyendo macrofibras sintéticas y fibras de acero.
Características que requieren los materiales del shotcrete para una exitosa aplicación subterránea:
- Trabajabilidad, esto es, que sea cohesionado
- Poseer un asentamiento y consistencia adecuados, sin segregación durante el transporte o bombeado
- Bombeable, esto es, tener buena trabajabilidad para su bombeo
- Disparable, esto es, que su trabajo sea compatible con una bomba, manga y boquilla de shotcrete y que sea manejada/controlada de manera eficiente por un operador de boquilla
- Construible, esto es, la mezcla de shotcrete, tal como se dosifica, suministra y transporta, debe aplicarse tal cual se diseñó y planificó, y no provocar retrasos en el cronograma de la obra
- Incidentes, tales como una pérdida excesiva de asentamiento o aumento de temperatura, endurecimiento rápido, tapones en la manguera y caída del shotcrete deben minimizarse durante la construcción
Durante la década pasada, los autores trabajaron en un importante número de proyectos de túneles civiles y mineros tanto en Estados Unidos como en Canadá. Los autores entregaron diseños de mezcla para shotcrete, monitorearon los disparos de prueba y ensayaron al material tanto en el terreno como en laboratorio. A través de estos proyectos, los autores acumularon más de una década de data sobre el desempeño del shotcrete y la experiencia en proyectos como los que se discutieron en este artículo.
Diseño de mezcla de shotcrete para sostenimiento subterráneo
El shotcrete u hormigón proyectado puede utilizarse como un revestimiento inicial del sostenimiento del terreno durante el proceso de construcción de un túnel. En metodologías constructivas sobre suelo blando, como el Nuevo Método de Construcción de Túneles Austriaco (NATM, en sus siglas en inglés), también conocido como Método de Excavación Secuencial (SEM, en sus siglas en inglés) o Método de Revestimiento de Hormigón Rociado (SCL, en sus siglas en inglés), el shotcrete u hormigón proyectado es un componente crítico de la construcción del túnel. Granes cavernas construidas con el método SEM incluyen a la estación Beacon Hill en Seattle, construida en 2006; la estación de metro China-Town en San Francisco, de 2016; el Conector Regional, Los Ángeles; y la Línea Púrpura del tren liviano en Washington, D.C.. El shotcrete también puede utilizarse en minería sobre roca dura con máquinas tuneladoras (Tunnel Boring Machines o TBM, en sus siglas en inglés) o con métodos de perforación y voladura para brindar soporte final al revestimiento. Estos proyectos incluyen a túneles hidroeléctricos tales como el túnel de la represa John Hart, en el Río Campbell, BC; el proyecto hidroeléctrico Upper Lillooet, Pemberton, BC; el proyecto para completar el túnel Kemano T2, en Kemano, BC; y los proyectos de túneles suministradores de agua, tales como el proyecto para completar el túnel Seymour-Capilano, en Vancouver Norte, BC. Todos estos proyectos requirieron que el shotcrete se aplicara tanto en orientación aérea como vertical; desarrollar suficiente resistencia a la compresión a una edad temprana (hasta 24 horas) para el sostenimiento del terreno; cumplir con la resistencia a la compresión especificada a 7 y 28 días; lograr la fuerza de adhesión a la roca especificada y cumplir con los requisitos de durabilidad. Los requerimientos típicos de desempeño especificados se encuentran listados en la Tabla 1.
Diseño de mezcla
Las mezclas de shotcrete se diseñan para cumplir con los requerimientos especificados de desempeño y para brindar una constructibilidad adecuada. Comparado con el hormigón colocado in situ, típicamente las mezclas de shotcrete poseen:
- Un contenido de material cementicio más alto para minimizar el rebote y que el material pueda dispararse de manera apropiada.
- Trabajabilidad mejorada para su bombeo y dispersión de aditivo de líquido acelerante en la boquilla (cuando se utilice).
- Bajo contenido de árido grueso, esto es, alto contenido de arena para minimizar el rebote y facilitar el bombeado y disparo del material.
- Un tiempo de retención de asentamiento extendido para cumplir con los requisitos de horario de la construcción.
Materiales cementicios suplementarios (SCMs, en sus siglas en inglés) se utilizan de manera amplia en el shotcrete. Estos incluyen a ceniza volante, humo de sílice y escoria, aunque no se limitan sólo a estos. Los SCMs reaccionan con el hidróxido de calcio, un subproducto del proceso de hidratación del cemento, para formar silicato cálcico hidratado (CSH, en sus siglas en inglés) a través de la reacción puzolánica. Esto resulta en una reducción de la porosidad y una mejora en la resistencia a la compresión y durabilidad en el shotcrete aplicado. Los SCMs poseen partículas similares o más pequeñas que las del cemento y, basado en ello, pueden ayudar a compactar o densificar la mezcla a través de la distribución del gran por tamaño. Además, las partículas de cenizas volantes o de humo de sílice son, en su mayoría, de forma esférica, lo que mejora las características de bombeado y disparo en la mezcla. Cada tipo de SCS se agrega en un cierto porcentaje por masa del total de materiales cementicios del shotcrete para cumplir con los requisitos de desempeño y constructibilidad. La Tabla 2 muestra un diseño de mezcla típico para shotcrete de mezcla húmeda, diseñado para el sostenimiento del terreno.
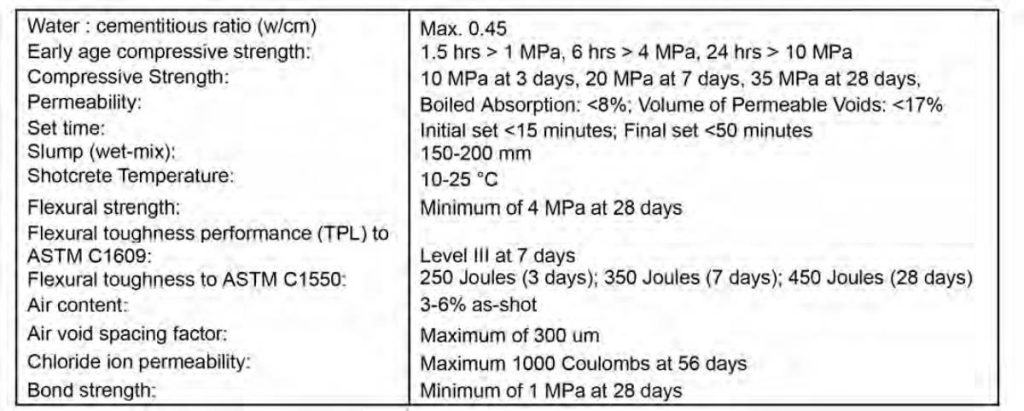
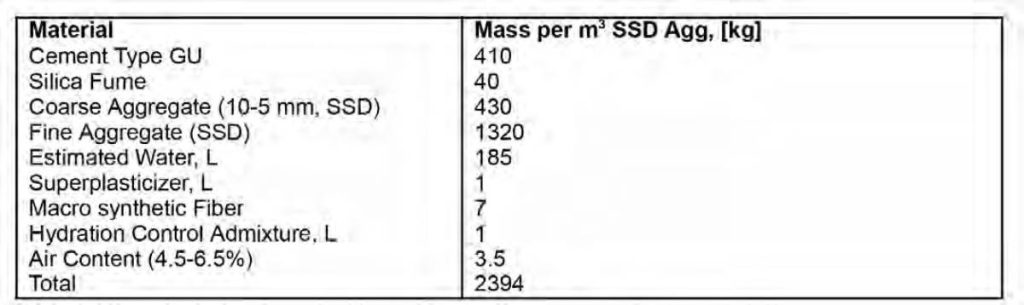
Acelerante libre de alcalinos
El acelerante libre de alcalinos (AFA, en sus siglas en inglés) se añade a la mezcla húmeda del shotcrete en la boquilla para acelerar el tiempo de endurecimiento y el desarrollo de resistencia a la compresión a una edad temprana del material, que va de 1 a 24 horas. El ritmo del desarrollo de resistencia a la compresión temprana es crítico para el sostenimiento del terreno ya que también reducirá el ciclo de tiempo de construcción tanto para la excavación como para el mismo sostenimiento. Desde comienzos de la década del 2000, los AFA se han utilizado en la industria del shotcrete para reemplazar a los acelerantes basados en alcalinos.
Los AFA tienen un valor de pH de 2-4, el que es similar a las bebidas colas carbonatadas. Los AFA se pueden añadir a la boquilla tanto como un aditivo líquido químico para aplicaciones de shotcrete de mezcla húmeda o como aditivo químico en polvo, el que se premezcla en la mezcla del shotcrete para aplicaciones del material en seco.
Para la mayoría de los requisitos de sostenimiento del terreno del shotcrete a aplicar, se requiere de una resistencia a la compresión temprana de 1.0 – 2.0 MPa (145-290 psi) para facilitar las actividades de la construcción. Los AFA se deben añadir en la dosis correcta para lograr el desarrollo de resistencia a la compresión temprana adecuado. Basado en la experiencia de los autores en diversos proyectos de túneles, generalmente toma una dosis de AFA de ente 4%-6% por la masa del cemento para alcanzar la resistencia requerida en cerca de 1-3 horas. Las variaciones al desarrollo de la resistencia a la compresión temprana dependen del diseño de mezcla del shotcrete, incluyendo el tipo de cemento y los aditivos químicos utilizados, la marca y desempeño del acelerante, la temperatura del shotcrete, la temperatura ambiente y el manejo y distribución adecuados del acelerante y las habilidades de disparo del operador de boquilla. La Fig. 1 muestra desarrollos típicos de resistencias a la compresión tempranas con dosis de AFA cuando se representa de acuerdo con la plantilla de curva J1-J2-J3, desarrollada por la Sociedad del Hormigón Austriaca (Ref. 10, 11). Generalmente, se considera a J2 como el requisito de desempeño mínimo para el desarrollo de resistencia a la compresión temprana del shotcrete en la mayoría de los proyectos de sostenimiento de terreno.
Cuando se utilizan distintos tipos de cemento, tales como Tipo V o Tipo GUL (Tipo GU con 15% de caliza), es posible que se retrase el tiempo de endurecimiento. Por lo mismo, una dosis más alta de AFA se requiere para desarrollar de manera adecuada la resistencia a la compresión a edad temprana. Los AFA reducirán, no obstante, la resistencia a la compresión en edades tardías, incluyendo las resistencias a la compresión a 7 y 28 días. La Fig. 2 muestra el desarrollo de la resistencia a la compresión para un shotcrete de mezcla húmeda con 0, 4%, 6% y 8% de AFA. Muestra que con 8% de AFA añadido al shotcrete, la resistencia a la compresión a 28 días podría reducirse de 62 MPa (9000 psi) a cerca de 36 MPa (5200 psi). Por ello, es importante añadir el acelerante en el diseño/dosis especificada para minimizar los efectos adversos en el desarrollo de la resistencia a la compresión en edades tardías.
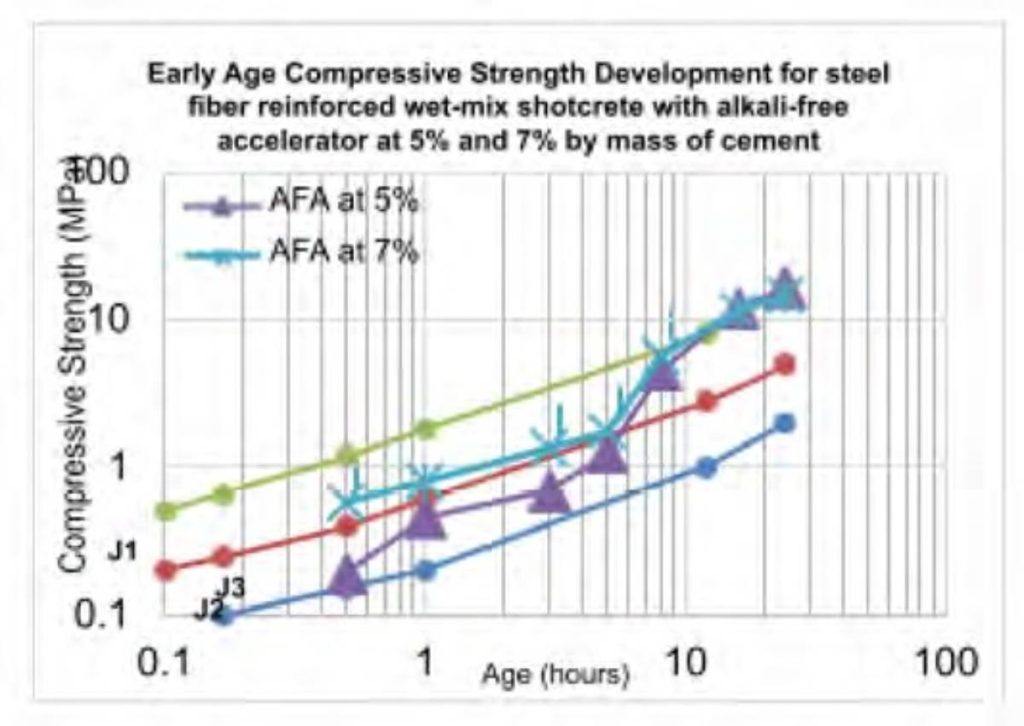
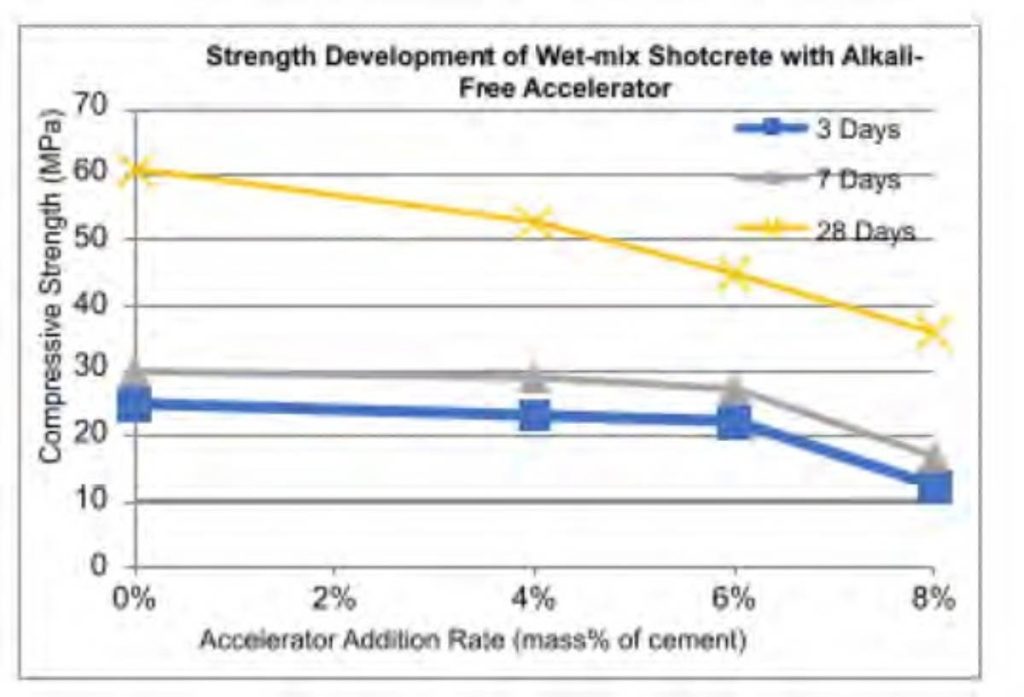
Avances en el shotcrete reforzado con fibra
La propiedad más significativa del shotcrete reforzado con fibra (FRS, en sus siglas en inglés) es la energía absorbida luego de fisuras en el shotcrete, esto es, su resistencia a la flexión. Luego que el shotcrete se fisura, las fibras se arrancan o se fracturan durante el proceso de agrietamiento, redistribuyendo así las cargas y controlando la propagación de la fisura mientras el sistema de revestimiento del FRS experimenta deformación. Tanto las macrofibras sintéticas como las fibras de acero se utilizan en shotcrete de mezcla húmeda para aplicaciones subterráneas a través de América del Norte. Las fibras se utilizan para reemplazar, ya sea de forma parcial o total, la malla de acera en los sistemas de sostenimiento de la superficie, reduciendo el tiempo de ciclo de construcción y generalmente entregan, en generan, un mejor desempeño al sostenimiento del terreno. Combinar shotcrete reforzado con fibra con un sistema de anclaje a la roca diseñado adecuadamente es uno de los sistemas de sostenimiento del terreno más eficientes utilizado en muchas minas y túneles civiles.
Comúnmente, el diseño del FRS se realiza en métodos basados por el desempeño, los que utilizan los resultados de ensayos de resistencia a la flexión. Entre los ensayos de resistencia a la flexión típicos, se incluyen los siguientes:
- ASTM C1550 Determinación de la resistencia a la flexión con panel de ensayo redondo con carga central
- ASTM C1609 Determinación de la resistencia a la flexión con viga de ensayo con carga a tres puntos
- RILEM TC 162-TDF: Ensayo y métodos de diseño para hormigón reforzado con fibra metálica (viga de ensayo agujereada)
- Estándar Británico (BS) EN 14651 Ensayo para hormigón con fibra metálica – midiendo la resistencia a la tensión y flexión (viga de ensayo agujereada)
La resistencia a la flexión, la resistencia residual y la carga máxima (resistencia máxima) son los factores más importantes al momento de evaluar el desempeño del shotcrete reforzado con fibra.
Durante la década pasada, los autores condujeron más de 5.000 ensayos de resistencia a la tensión y resistencia a la tensión residual en FRS utilizado en proyectos subterráneos en Estados Unidos y Canadá. Los ejemplos de los resultados de estos ensayos se analizarán y publicarán en un futuro paper. Basados en la experiencia, existen tres especificaciones para proyectos típicas para la resistencia a la flexión para el shotcrete reforzado con fibra que se utilizan en América del Norte.
Nivel de desempeño de resistencia (TPL, en sus siglas en inglés) basado en el ensayo ASTM C1609
Cuando se especifica TPL, se requiere que el panel de ensayo del shotcrete se corte en vigas con dimensiones de 100x100x350 mm y se ensaye bajo ASTM C1609. En ocasiones, las muestras de shotcrete pueden dispararse directamente sobre moldes de viga de 150x150x550 mm, con ambos extremos inclinados para prevenir acumulación o rebote. Los autores ensayaron más de 3.000 vigas de FRS bajo ASTM C1609 desde el año 2011. Se encontró que, si el TPL cumple con el Nivel III de Desempeño por Resistencia, generalmente cumple los requisitos de sostenimiento en la mayoría de las superficies.
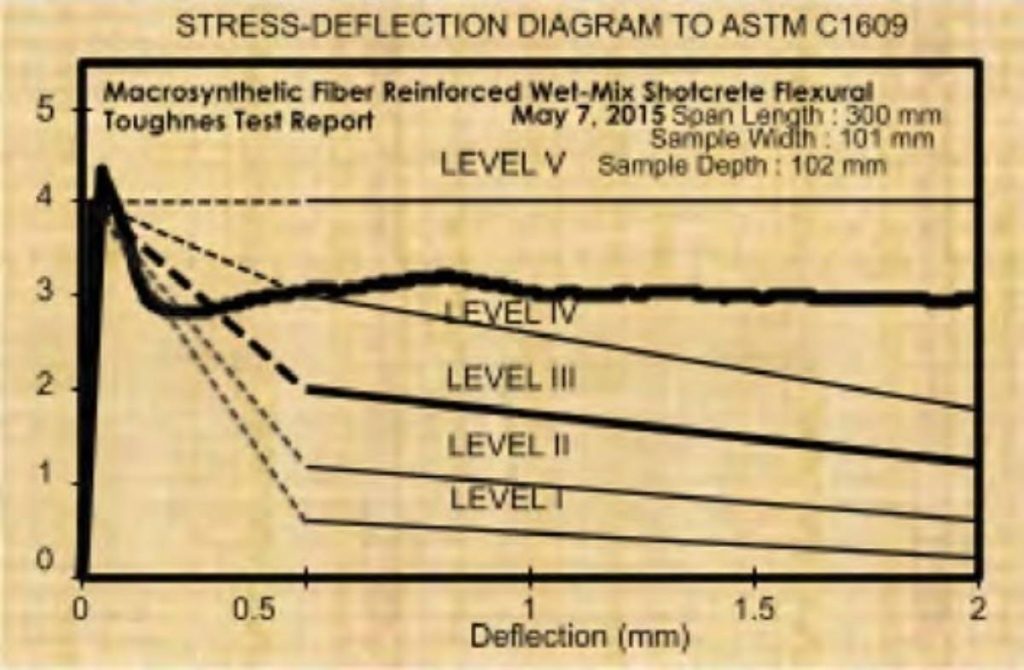
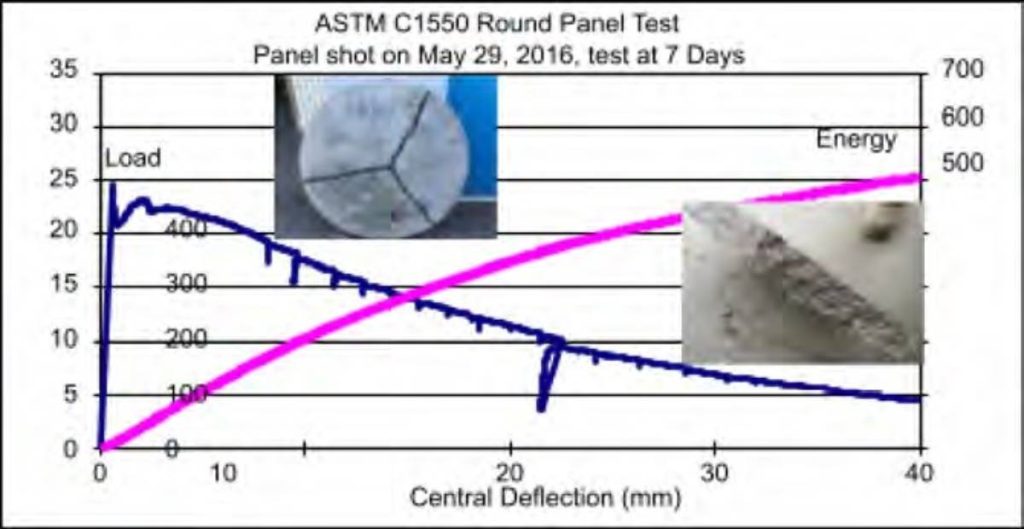
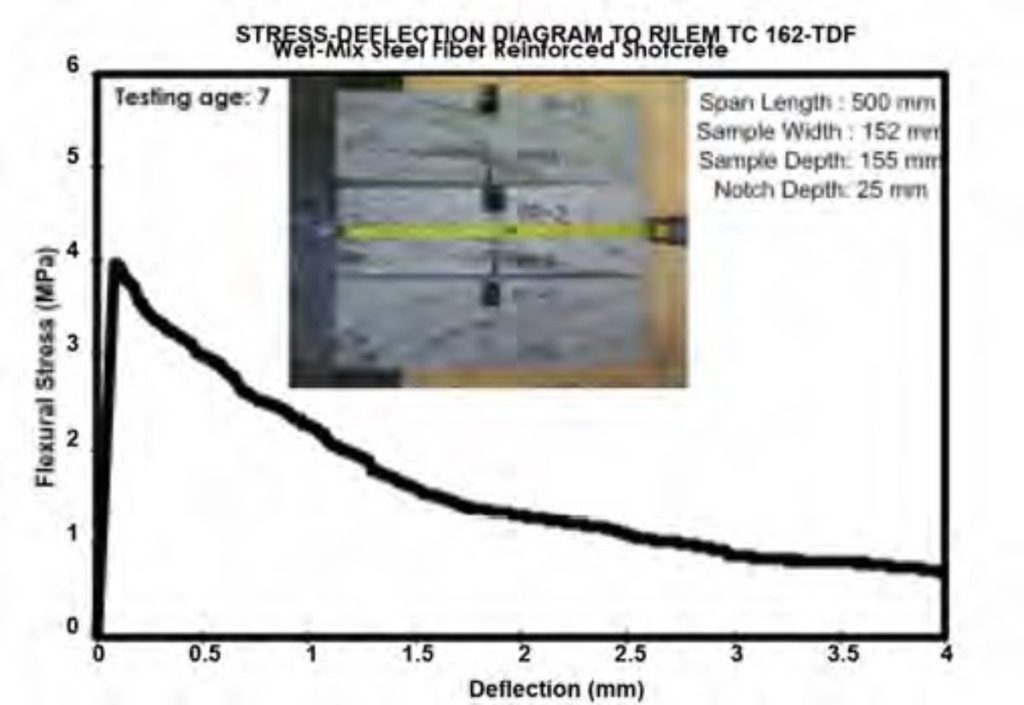
Método de panel redondo determinado (RDP) basado en el método de ensayo ASTM C1550
Cuando se especifica el método RDO, requiere muestras de paneles redondos determinados (RDP) con dimensiones de 800 mm de diámetro para disparar el material, y 75 mm de espesor. Los RDPs se ensayan bajo ASTM C1550 y se reportó una desviación de hasta 40 mm de energía total absorbida. La Fig. 4 muestra un resultado típico de resistencia a la flexión vs. ensayo de desviación. Los autores realizaron más de 2.000 ensayos de paneles redondos bajo ASTM C1550 desde 2011. Si la resistencia a la flexión supera los 320-450 Joules, generalmente cumple con los requisitos de sostenimiento para la mayoría de las superficies. Para túneles de roca dura, comúnmente se especifica una resistencia a la flexión de sobre 320-350 Joules para cumplir con los requerimientos generales. Para túneles de superficie blanda, tales como SEM, se especifica una resistencia de 450 Joules para cumplir con los requerimientos generales.
Método de viga agujereada basado en BS EN 14651 / RILEM-TC-162-TDF resistencia a la tensión residual
La resistencia a la tensión residual en FRS también puede ensayarse bajo el método de ensayo de viga agujereada BS EN 14651. La viga de shotcrete se pre-agrieta cortando con una sierra una muesca de 25 mm. de profundidad en la parte inferior de la viga, en el centro de la sección transversal de 150 mm x 150 mm. Luego, se aplica sobre la viga una carga de flexión de tres puntos. La Fig. 5 muestra una curva típica de tensión de tracción residual vs. deflexión para la prueba de viga agujereada.
Tanto ASTM C1609 como ASTM C1550 pueden brindar información suficiente sobre la resistencia a la flexión de los FRS. Son aplicables tanto en shotcrete reforzado con fibras metálicas o en refuerzo de macrofibras sintéticas. BS EN 14651 / RILEM-TC-162-TDF emplea una muesca en la viga, introduciendo intensidad de esfuerzo. Ese ensayo se desarrolló originalmente por RILEM para estudiar la resistencia a la tensión residual basado en la fractura mecánica, aunque generalmente se acepta que una fisura se propagará a través de la muesca. Los autores ensayaron aproximadamente 50 vigas con este método de ensayo durante la pasada década. La mayoría de las especificaciones para túneles civiles con shotcrete requieren tanto de ensayos ASTM C1609 o ASTM C1550, o ambos. Muy pocas especificaciones en América del Norte solicitan los ensayos BS EN 14651 o RILEM-TC-162-TDF.
Certificación de las mezclas de shotcrete y de los operadores de boquilla
Antes de la construcción, la especificación del proyecto requiere que la mezcla de shotcrete esté precertificada. Típicamente, esto se realiza al menos 60 días antes de la colocación del shotcrete. Para proyectos de gran envergadura en los que el shotcrete es parte del proceso de sostenimiento del túnel o mina, tales como SEM, la certificación de la mezcla del shotcrete podría comenzar hasta 6 meses antes del inicio de las obras. Normalmente, la certificación de la mezcla requiere que la mezcla del shotcrete se aplique con el mismo equipo y cuadrilla que se utilizará durante la construcción, para asegurar que el shotcrete se coloque de forma adecuada durante todo el proyecto. Durante la certificación de la mezcla, el material se dispara sobre paneles de ensayo. Se ensayan las propiedades plásticas de temperatura, contenido de aire y asentamiento (en lotes), como también el contenido de aire y asentamiento (durante el disparo del material). Cuando se utiliza un acelerante, el tiempo de endurecimiento inicial y final se ensaya bajo ASTM C1117 y se ensaya la resistencia a la compresión a temprana edad hasta 24 horas, utilizando el método de ensayo de viga final. Los testigos se extraen de los paneles de ensayo y se testean para resistencia a la compresión, absorción hervida y volumen de vacíos permeables, penetración rápida de iones de cloruro, etcétera. Las vigas se cortan de los paneles de ensayo para determinar su resistencia a la flexión bajo ASTM C1609. Paneles redondos se disparan y ensayan para resistencia a la flexión bajo ASTM C1550. Todos los resultados de los ensayos deben cumplir con los requisitos especificados por el proyecto.
Los acelerantes se utilizan de manera común en aplicaciones subterráneas de shotcrete. La dosis del acelerante determina el tiempo de endurecimiento y el radio de desarrollo de resistencia a la compresión a temprana edad del shotcrete. La dosis del acelerante debe calibrarse con la bomba dosificadora del acelerante y la bomba de shotcrete que se utilizarán en el proyecto. Una calibración adecuada de la dosis de acelerante es una de las partes más importantes de la certificación de la mezcla. Información detallada sobre la calibración de la bomba dosificadora de acelerante puede encontrarse en (Ref. 12, 13). Luego que la mezcla de shotcrete se precertificó, la certificación de los operadores de boquilla requiere que los operadores apliquen el shotcrete de manera adecuada para alcanzar el desempeño especificado y los requerimientos para el sostenimiento de la superficie. Más específicamente, la certificación de los operadores de shotcrete requiere lo siguiente:
- Los operadores deben comprender lo básico de la tecnología del hormigón y el shotcrete. Esto incluye cómo el cemento se hidrata, los efectos de la temperatura en el shotcrete y los efectos del acelerante y otros aditivos químicos en el desempeño del shotcrete.
- Trabajabilidad, bombeabilidad y disparabilidad: los operadores deben comprender que el asentamiento, o la consistencia de la mezcla del shotcrete, es crítico para par el transporte, bombeo y disparo del material. Aplicaciones aéreas y verticales poseen diferentes desafíos para la aplicación del shotcrete.
- La preparación del sustrato, incluyendo limpieza, rugosidad y la condición de humedad de la superficie receptora, debe ser una superficie seca saturada (SSD, en sus siglas en inglés) para alcanzar una unión óptima.
- Adecuada calibración de la bomba de dosificación del acelerante.
- Adecuada aplicación del shotcrete en la orientación especificada, incluyendo aérea, vertical, a 45 grados, etcétera.
- Adecuado control del ángulo, distancia y patrón de disparo de la boquilla para minimizar el rebote y sobrerociado.
- Procedimiento adecuado para aplicar capas gruesas de shotcrete, incluyendo aplicaciones multi capas.
- Si el shotcrete se cae, ya sea desde superficies aéreas o verticales, los operadores deben poder determinar inmediatamente qué fue lo que ocurrió y cómo realizar las correcciones necesarias.
El proceso de certificación de los operadores de boquiila es esencial para un proyecto exitoso ya que se logra lo siguiente:
- Educa a los operadores respecto a materiales de shotcrete, equipos, tecnología del hormigón y los efectos de aditivos químicos, incluyendo acelerantes.
- Los prepara para el proyecto. Típicamente, el componente más difícil a incluir en el sistema de apoyo del shotcrete es seleccionar a operadores de boquillas certificados.
Usualmente, el bosquejo de certificación de los operadores se diseña para cada proyecto. Se requiere disparar sobre secciones con alta congestión de refuerzo, incluyendo refuerzo empalmado, vigas de celosía, conjuntos de acero y otros tipos de refuerzos e incrustaciones (Fig. 6). Cada operador que trabaje en la aplicación de shotcrete para un proyecto debe estar certificado.
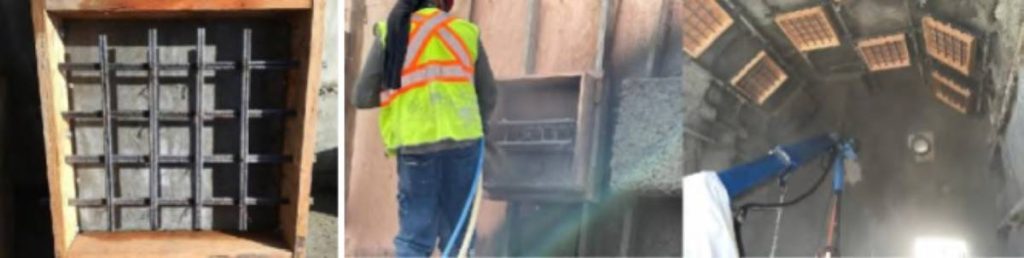
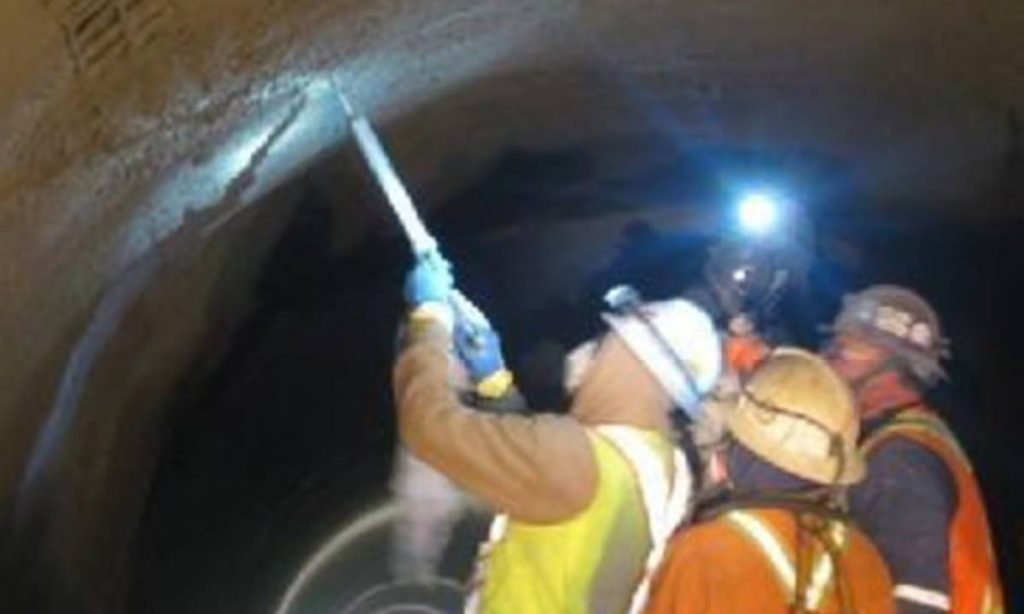
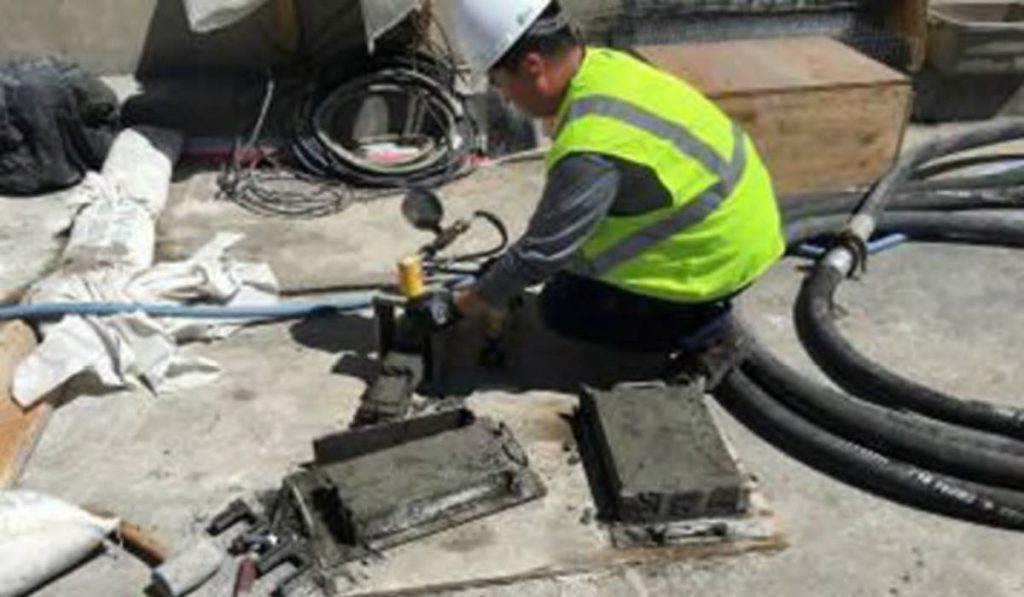
Inspección y pruebas de control de calidad en la construcción
Durante la construcción con shotcrete, se requiere un plan de inspección y pruebas de control de calidad y necesita ejecutarse para asegurar que el shotcrete colocado in situ cumpla con las especificaciones requeridas por el proyecto, y si no, realizar acciones de remediación adecuadas de manera inmediata.
La inspección de campo para el shotcrete se conduce normalmente con otras actividades de inspección del túnel, tales como monitoreo del terreno, progreso de la excavación, etc. y normalmente las lleva a cabo un ingeniero o tecnólogo a tiempo completo, a quien cita el dueño del proyecto, o un consultor de shotcrete citado por el contratista.
Las actividades de inspección típicas incluyen las siguientes:
- Evaluación de la rugosidad de la superficie, libre de partículas sueltas y condición de humedad previo a la aplicación del shotcrete.
- Aplicación del shotcrete: Habilidades de disparo de los operadores, incluyendo control de rebote y sobrerociado, espesor del shotcrete y dosis de acelerante, si se utiliza.
- Revisar por cualquier shotcrete defectuoso, incluyendo vacíos, fisuras, signos de sobredosis de acelerante, fallas potenciales en el shotcrete, etc..
Los ensayos de campo para el shotcrete los llevan a cabo técnicos o ingenieros certificados para asegurar que el shotcrete plástico cumpla con los requisitos de desempeño especificados para la aplicación y bombeo del shotcrete. Típicamente, el asentamiento, contenido de aire y temperatura tanto para el shotcrete dosificado como el que se va disparando, se ensayan cuando el material se entrega en el sitio de la obra. El asentamiento debe ensayarse en la planta dosificadora, como también en la locación donde de descarga el shotcrete desde el transmixer a la bomba, dentro del túnel. Si se requiere que el shotcrete se mantenga por recorridos largos o en tiempos de retención más grandes, tales como más de un cambio de 12 horas, usualmente se realiza un control de aditivo hidratante para mantener la trabajabilidad del shotcrete. Siempre que exista una pérdida significativa de asentamiento, por ejemplo, una pérdida de más de 50 mm, se necesita ejecutar una acción inmediata para retemplar al shotcrete con un aditivo o disponer del shotcrete para evitar que el material se endurezca dentro del transmixer.
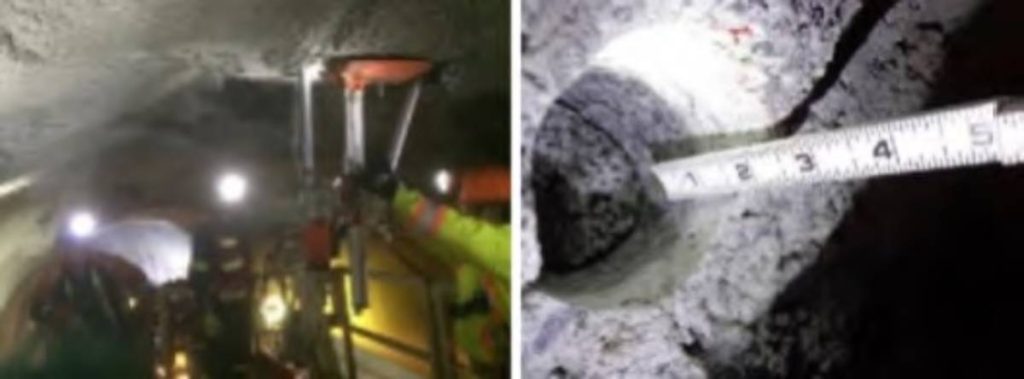
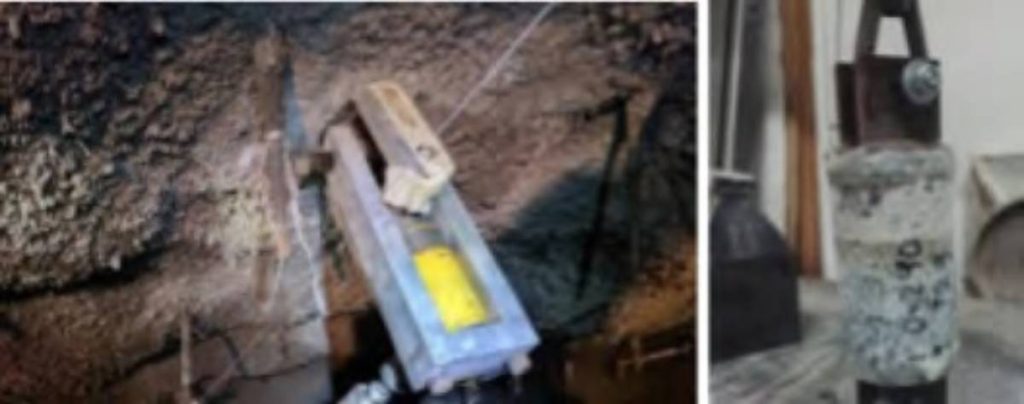
Los ensayos de endurecimiento se realizan bajo ASTM C1117. Cuando se agrega el acelerante a una dosis adecuada, el tiempo inicial, es decir, el tiempo cuando el shotcrete pierde completamente su asentamiento o bombeabilidad, es menor a los 15 minutos aproximadamente, y el endureciemiento final, es decir, el tiempo cuando el shotcrete comienza a desarrollar resistencia a la compresión, es menor a los 50 minutos.
La Fig. 7 muestra un ensayo in situ de tiempo de endurecimiento con un penetrómetro, bajo ASTM C1117.
La Fig. 8 muestra ensayos de resistencia a la compresión a edad temprana en muestras de shotcrete con el método de viga final. Si se requiere resistencia a la compresión a edad temprana para sostenimiento de superficie, tales como 1,.0 a 2.0 MPa (150-300 psi) para volver o continuar las actividades de la construcción bajo shotcrete fresco recién aplicado, los ensayos deben conducirse a distintas edades tales como 2 horas, 4 horas, 6 horas y hasta 24 horas. El ensayo de tiempo de endurecimiento y de resistencia a la compresión a edad temprana es común para túneles cuando se requiere el desarrollo inmediato de resistencia a la compresión, como en túneles SEM.
Cuando el shotcrete se endurece, la consolidación del shotcrete in situ, su espesor y unión con el sustrato pueden evaluarse vía inspección visual del orificio del testigo. La resistencia de la unión puede ensayarse para evaluar la resistencia a la tensión de la unión entre el revestimiento de shotcrete y la roca de sustrato. La resistencia de la unión puede realizarse al extraer un testigo y con ensayos in situ, o extrayendo testigos para luego ensayarlos en laboratorio. En ocasiones, la resistencia a la tensión de la unión se especifica con un mínimo de 1.0 MPa. La Fig. 9 muestra el orificio de un testigo extraído in situ. La Fig. 10 muestra el ensayo de unión in situ y el ensayo de resistencia de la unión en laboratorio. Sin embargo, se debe advertir que algunos tipos de roca más débiles pueden caer a valores por debajo de 1.0 MPa en los resultados del ensayo de resistencia de la unión, resultado en una falla del sustrato y no de la unión del shotcrete.
Nuevos desarrollos: shotcrete masivo para estructuras subterráneas
Durante las últimas décadas, más y más proyectos estructuras permanentes subterráneas se han construido con shotcrete. Entre ellas, la construcción de muros estructurales de shotcrete masivo utilizando el método “híbrido” (disparar y vibrar) son desarrollos recientes. Estructuras para estaciones subterráneas altamente reforzadas, con dimensiones de 200 a 1.500 mm de espesor se están construyendo en la actualidad con shotcrete. Esto involucra una combinación de shotcrete estructural y tecnologías de aplicación subterránea de shotcrete. Las estructuras de shotcrete más grandes desarrollan temperaturas internas más altas debido al calor de la hidratación del cemento. Cuando las estructuras de shotcrete son lo suficientemente gruesas, la disipación del calor será materia de preocupación y requerirá de control térmico y un plan de protección.
Para prevenir las fisuraciones térmicas en las estructuras de shotcrete masivo, se desarrolló un plan de control térmico (TCP, en sus siglas en inglés) como un documento de diseño. El TCP especifica las medidas necesarias para cumplir con los requisitos de control térmico, incluyendo el eso de mezclas de hormigón de baja temperatura (“low-heat concrete”), reduciendo la temperatura de colocación del shotcrete, entregando sábanas de protección térmica y utilizando tuberías internas de enfriamiento. Un proyecto reciente de muro estructural de shotcrete masivo en Vancouver, BC, implementó un TCP utilizando tuberías de enfriamiento y mantas térmicas (Ref. 14). La Fig. 11 muestra un muro de shotcrete con alta congestión de refuerzo y un muro con tuberías de enfriamiento.
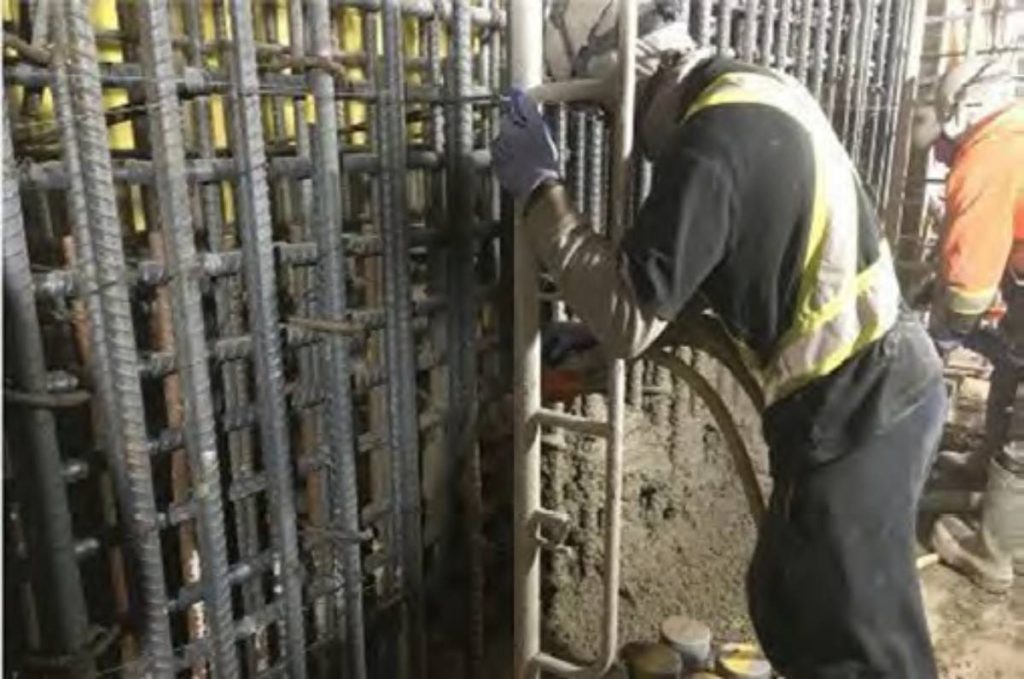
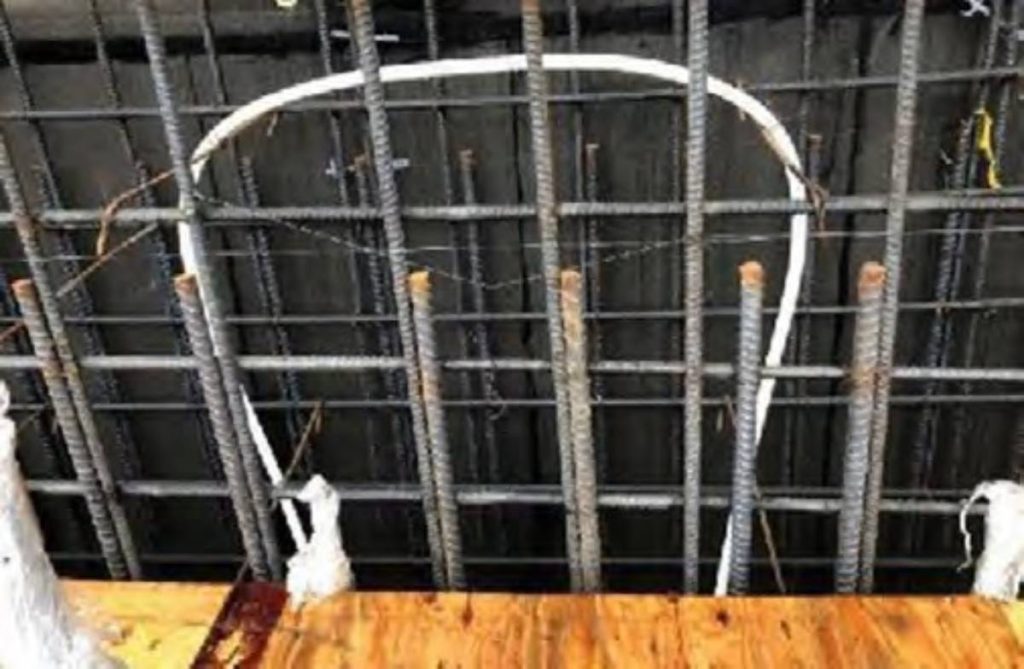
Durabilidad del shotcrete
Más y más túneles civiles se diseñan para tener una vida útil de 70 años o más, algunos incluso con 100 años de servicio. La vida útil para un túnel civil depende principalmente de la vida útil de la estructura que soporta al túnel, incluyendo al revestimiento final y otras estructuras. Cuando se diseña una estructura de hormigón, la vida útil y los requisitos de durabilidad anularán los requerimientos estructurales mínimos del desempeño mecánico, incluyendo la resistencia a la compresión, módulo de elasticidad, momento de flexión y resistencia a la tensión, etc.
Es crítico considerar los factores de durabilidad cuando se diseña para una vida útil prolongada. Los factores de durabilidad tales como resistencia a las condiciones climáticas, corrosión, ataques químicos, reacción de áridos alcalinos, carbonatación y deterioro por congelación-deshielo son todos influenciados por el diseño de mezcla del hormigón y las propiedades de transporte del hormigón durante la vida útil de la estructura. Las estructuras civiles subterráneas, incluyendo túneles, huecos, cavernas y otras, a menudo se ven expuestas a uno o a varios de los factores nombrados. Por lo mismo, la vida útil de la estructura depende, principalmente, de la vida útil de las estructuras de shotcrete. La durabilidad de las estructuras de shocrete depende del diseño de mezcla del hormigón y del proceso de aplicación.
Una pregunta que se realiza en ocasiones sobre el shotcrete: ¿será tan durable como el hormigón colocado in situ? Un reciente proyecto de investigación terminado (Ref. 15) comparó las propiedades de transporte para el shotcrete con las del hormigón colocado in situ. Los resultados muestran que el shotcrete aplicado de manera adecuada logrará propiedades de transporte iguales o meores que las del hormigón colocado in situ. Basado en la investigación, se modeló la vida útil utilizando un programa avanzado para modela vida útil (STADIUM), con diferentes condiciones de exposición y temperatura. El shotcrete presenta un tiempo igual o mayor para el inicio de la corrosión del acero de refuerzo, lo que proporciona una vida útil mayor (Ref. 15).
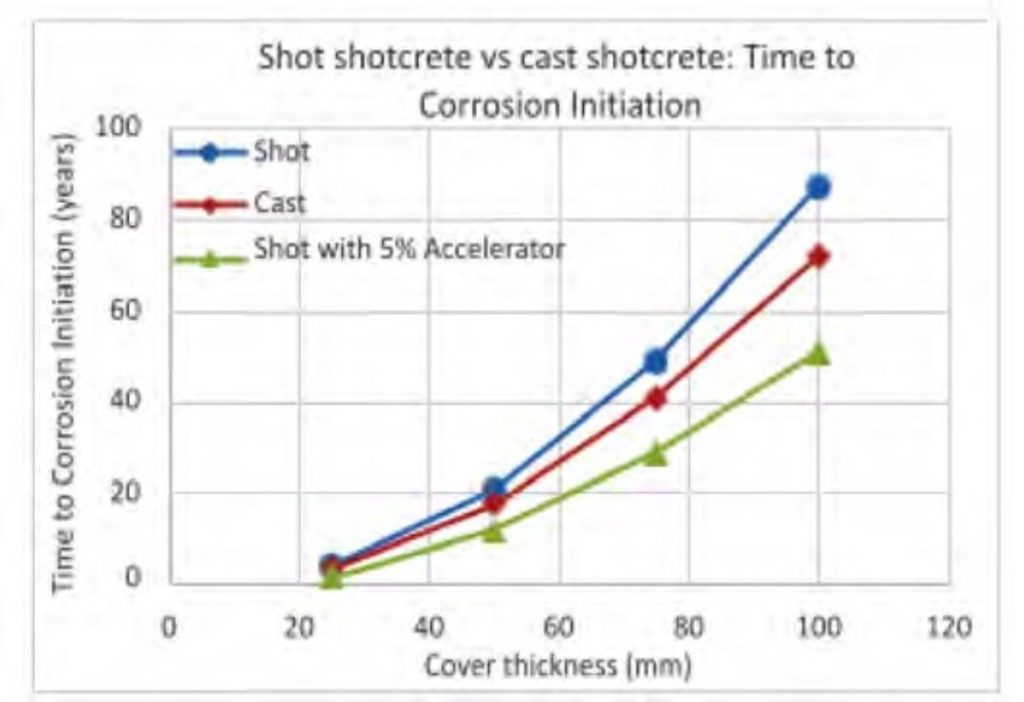
Esta investigación también indicó igual o mejor durabilidad para el shotcrete entregado, siempre que se utilice una dosis moderada de acelerante. Cuando se usa, la calidad de la matriz del shotcrete tiende a degradarse. Mientras que el acelerante aumenta el radio de hidratación del cemento y la evolución del calor, entregando un desarrollo más temprano de resistencia, también resulta en una matriz cementicia endurecida más permeable. Los iones químicos tienden a migrar más rápido y con menor resistencia cuando se utiliza un acelerante. Por ejemplo, cuando se añade un acelerante en un 5% por la masa de cemento en el shotcrete, las propiedades de transporte tienden a reducirse y por lo mismo, disminuye el tiempo de vida útil (Fig. 12, Ref. 15). Si bien el acelerante es crítico para el sostenimiento subterráneo para alcanzar un endurecimiento rápido y resistencias a la compresión a temprana edad confiables, la dosis de acelerante a utilizar debería ser controlada de manera acuciosa para que la estructura de shotcrete pueda cumplir tanto los requisitos de sostenimiento del terreno y la durabilidad requerida.
Códigos y desarrollo de estándares
Los códigos, estándares y documentos guía para shotcrete son desarrollados y actualizados regularmente por el Comité 506 del American Concrete Institute (ACI). Típicamente, las especificaciones de los proyectos están preparadas por el ingeniero diseñador en consulta y/o revisión del especialista en shotcrete. Aquí hay algunas de las guías y especificaciones para shotcrete más comunes utilizadas en Norteamérica:
- ACI 506.5-2018: “Guide for Specifying Underground Shotcrete.” Este documento se actualizó en 2021
- ACI 506R-2015: “Guide to Shotcrete”
- ACI 506.2-2018: “Specification for Materials, Proportioning and Applicaction of Shotcrete”
- ACI ACI – CP-60 Craftsman Workbook for ACI Certification of Shotcrete Noozleman
Estas guías y especificaciones, junto con otros documentos relacionados de ACI, ASTM, CSA, ASHTO, y el Cuerpo de Ingenieros del Ejército de Estados Unidos, entregan las bases para el desarrollo de un programa QA/QC adecuado.
Recientemente, el Código ACI 318-19 para Construcción de Edificaciones de Hormigón Armado incluyó requisitos para la colocación de shotcrete estructural (Ref. 16).
Conclusiones
El shotcrete se utiliza cada vez más para el sostenimiento del terreno en construcciones subterráneas. El uso de acelerantes libres de alcalinos (AFA) y refuerzo de fibras son dos grandes avances en el uso del shotcrete en ambientes subterráneos durante las últimas dos décadas. Los AFA son eficientes en reducir el tiempo de endurecimiento del shotcrete y para el desarrollo de resistencias a la compresión a temprana edad. Las fibras, por su lado, han transformado enormemente el diseño de sostenimiento de superficies y las metodologías de construcción. La calidad del shotcrete para el sostenimiento requiere de lo siguiente:
- Mezcla de shotcrete de alto desempeño
- Certificación de mezcla de shotcrete y programa de certificación de operadores adecuados
- Monitoreo riguroso de la construcción y de los programas de ensayo
El shotcrete se está utilizando cada vez más para el revestimiento final en la construcción de túneles. Ejemplos incluyen túneles de transporte de agua en proyectos hidroeléctricos y para tratamiento de aguas, y túneles viales y ferroviarios. El shotcrete estructural también se está utilizando en mayor cantidad en construcción subterránea para estaciones de metro en grandes áreas metropolitanas de Norteamérica. Las estructuras de shotcrete masivo, incluyendo muros fuertemente reforzados, pueden construirse se manera apropiada con el proceso de shotcrete estructural híbrido (disparo y vibración) junto con la provisión de un adecuado plan de control térmico.
La colocación duradera del shotcrete para el sostenimiento de la superficie es un punto crítico para la construcción de estructuras subterráneas duraderas. En particular, con muchas más estructuras subterráneas que requieren tener una vida útil sobre los 100 años, la durabilidad de los materiales del shotcrete y las estructuras resultantes, incluyendo resistencia a ataques químicos, es una consideración importante. La investigación realizada por los autores demostró que, con un diseño y colocación adecuados, el shotcrete puede entregar igual o mejor durabilidad en comparación el hormigón colocado in situ.
Referencias
1. Zhang, L.; Morgan, D. R., “Fiber reinforced shotcrete tunnel lining quality control and testing in North America,” 10th World of Tunnel Congress, May 2009, Vancouver, Canada
2. Zhang, L.; Morgan, D. R., “Quality Control for Wet-Mix Fiber Reinforced Shotcrete in Ground Support,” Shotcrete for Underground Support XII, Singapore Oct 11-13, 2015
3. Zhang, L.; Morgan, D. R., “Recent Development of Shotcrete in Western Canada,” The 7th International Symposium on Sprayed Concrete Modern Use of Wet Mix Sprayed Concrete for Underground Support -Sandefjord, Norway, 16.- 19. June 2014
4. Morgan, D. R.; Zhang, L., Pildysh, M., New Hemp-Based Fiber Enhances Wet-Mix Shotcrete Performance. Shotcrete Magazine, Spring 2017, pp1-11.
5. Zhang, L.; Morgan, D. R., Walter, T., McInnes, B., Rule, A., Mitchell, A., “Shaft Lining with Dry-Mix Shotcrete,” Shotcrete Magazine, Summer, 2018., pp 48-56.
6. Radomski, S. M.; Zhang, L.; Morgan, D. R.; Graham, D.; “Structural Modifications to Hydroelectric Turbine Draft Tube Ceiling Using Accelerated Wet-Mix Steel Fiber Reinforced Shotcrete Applied up to 2m Thick Overhead,” Shotcrete Magazine, Summer, 2019, pp 43-48.
7. Zhang, L., “Air Content in Shotcrete: As-shot vs. As-batched,” Shotcrete Magazine, Winter, 2012. pp 50-54.
8. Zhang, L.; Morgan, D. R., “Variability of Compressive Strength for Shotcrete,” The 7th International Symposium on Sprayed Concrete Modern Use of Wet Mix Sprayed Concrete for Underground Support -Sandefjord, Norway, June 2014, p 19.
9. Zhang, L.; Morgan, D. R.; Moalli, S.; Gagnon, D.; Dugas, D., “Tunnel Shotcrete Lining for Hydroelectric Projects in British Columbia, Canada,” Shotcrete Magazine, Summer, 2019, pp 40-48.
10. Heere, R.; and Morgan, D. R., “Determination of Early Age Compressive Strength of Shotcrete,” Shotcrete Magazine, Vol. 4, No. 2., Spring 2002, pp. 28-31.
11. Bernard, S., “Early-Age Strength Tests Methods for Fiber-Reinforced Shotcrete,” Shotcrete Magazine, Spring 2005, pp. 16-20.
12. Zhang, L., “Calibration & Verification of Accelerator Dosing Pump,” Shotcrete Magazine, Summer, 2012, pp 42-44.
13. Millette, D., “Using Accelerators for Shotcreting,” Shotcrete Magazine, Fall 2011, pp. 36-39.
14. Zhang, L. Morgan, D.R. Kirk, I. Rolland, A. and Karchewski, R., Mass Shotcrete Wall Construction and Thermal Control Plan, ACI Materials Journal, V. 118, No.3, May 2021, pp 71-82.
15. Zhang, L.; Morgan, D. R.; Mindess, S., “Comparative Study on Transport Properties of Shotcrete vs. Cast-in-Place Concrete,” ACI Materials Journal, May-June, 2016, V. 113, No. 3, pp 373-384.
16. Hanskat, C, Holland, T. and Suprenant, B., Shotcrete Incorporated into ACI 318-19 Building Code. Concrete International. Vol 41, Issue 12, 2019, pp 31-35.