Con un volumen de 7.000 metros cúbicos de hormigón, correspondientes a cerca de 1.600 elementos prefabricados de hormigón, el nuevo Truck Shop que monta la Vicepresidencia de Proyectos para la división Andina de la minera estatal posee características de diseño sísmico que no existen en otros proyectos similares, lo que hacen de este Truck Shop algo único en Chile y el mundo.
En los últimos años, se puede trazar un incremento en el uso de prefabricados de hormigón en la gran minería. “Las empresas mineras tienen claridad de los beneficios que involucra incorporar la prefabricación de elementos en el diseño de sus proyectos, por lo que no sólo están comenzando a incorporar los prefabricados en etapas tempranas del desarrollo de un proyecto, sino también, se están atreviendo a prefabricar estructuras de mayor complejidad en cuanto a la ingeniería, fabricación y montaje; construyendo estructuras prefabricadas que forman parte de la infraestructura para la operación minera de manera exitosa”, comentó Claudia Cid Perley, gerente de Proyectos Minería en Tensacon.
En ese sentido, el nuevo proyecto que lleva adelante la Vicepresidencia de Proyectos de Codelco (VP) para División Andina de Codelco, en el marco de los trabajos de la Fase 7 de la división, que obedecen a la expansión de la mina, cambia el paradigma. Esto, porque por primera vez en la estatal, se utiliza hormigón prefabricado de forma íntegra para la construcción de infraestructura crítica como el Truck Shop de la plataforma 3700.
Qué es y cuál es la utilidad del Truck Shop para la faena minera
Lo primero a aclarar es qué es un Truck Shop. Al respecto, Cristián Rodríguez, jefe de Construcción y Montaje en Codelco VP, explica que “es un centro de estación de servicio de los camiones de extracción”. Por su parte, Rubén Ramos Salas, especialista senior Ingeniería Civil Industrial en Codelco VP, puntualiza que se tratan tanto los camiones de extracción como los mineros y que en estas instalaciones contemplan “las naves de mantención, las losas de lavado, las naves donde se lubrican los camiones, las bodegas donde se encuentran todos los sistemas de repuestos de los equipos”.
Ramos también detalla que un Truck Shop contempla “un barrio cívico donde los trabajadores y los operadores viven, tienen sus oficinas, salas de cambio y facilidades”. Las instalaciones, dice el ingeniero, cuentan con sectores de acopio para los residuos que generan los propios camiones, los que incluyen el manejo de materiales peligrosos, “pero, básicamente, es un taller de mantención”, subrayó Rubén Ramos.
Dado el ritmo de mantención de los vehículos -aproximadamente, cada una semana según los personeros de Codelco VP- es que el Truck Shop constituye una infraestructura crítica para el desarrollo de la faena. “Sin el taller, la operación se detiene”, dijo Rubén Ramos, sentencia en la que está de acuerdo Cristián Rodríguez. “Las mantenciones in situ prácticamente no se hacen, menos en un rasgo que no es como la mantención de un camión tradicional. Por lo tanto, si no funciona este taller, en realidad, se para la flota y se para la minería”, sentenció.
De esta manera, la construcción de las nuevas instalaciones debe realizarse sin afectar el funcionamiento normal de la faena. En ese sentido, mientras se culmina el montaje del Truck Shop en la cota 3.700 (es decir, a 3.700 metros sobre el nivel del mar), el edificio nuevo tiene un “espejo” montado a 4.000 metros.
“Estas instalaciones son parte de la fase 7 de la mina”, explicó el jefe de Construcción y Montaje de Codelco VP. “Entonces, nos encontramos en fase de expansión para la explotación minera y para proyectar la explotación, estos edificios tienen que salir. Por este motivo, estamos construyendo antes de ir a desmantelar lo que ya existe y una vez se complete el nuevo Truck Shop, se desmantela su espejo para que avance la nueva fase de la mina”.
Del acero al hormigón: cambio en la ingeniería
Dada la importancia que tiene el Truck Shop dentro de la operación minera -y el momento que vive Codelco Andina, en pleno desarrollo del plan de extracción del mineral- las obras relacionadas con este complejo debían ejecutarse en tiempos acotados, los que además están limitados por el mismo clima donde se encuentra la mina, con temporadas de nevazones incluidas.
Una de las particularidades que poseen estas instalaciones es que su estructura es metálica. Es decir, estructuralmente sus componentes son de acero, tanto en los galpones como la infraestructura. Y, en ese sentido, el llamado a licitación que realizó la estatal para este nuevo Truck Shop estableció esa materialidad como el principal elemento constructivo.
En ese sentido, desde Salfa Montajes, empresa encargada de la construcción del nuevo Truck Shop, dicen que, si bien se estableció desde un inicio esa condición en cuanto materialidad constructiva, dada la experiencia de la empresa se analizaron diversos aspectos antes de ingresar su propuesta.
“Definimos un análisis estratégico de propuestas de valor para este proyecto, algunas directas propias de la ejecución y en segundo lugar la determinación de activos intangibles que surgieron en función de oportunidades producto de la ubicación, COVID, dificultades en los suministros en terreno principalmente de los hormigones y las estructuras metálicas, disponibilidad de campamento y principalmente las condiciones climáticas, porque estaba bastante restringido el período en el que podíamos construir”, explicó Carlos Fernández Novoa, gerente de Desarrollo e Innovación/VP Salfa Montajes.
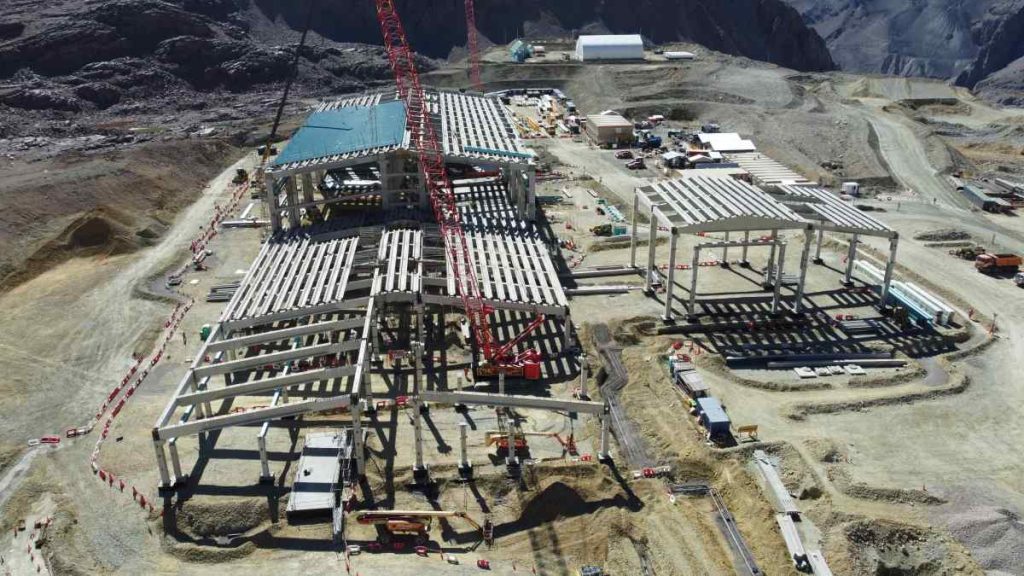
Para dar respuesta a esos desafíos, la constructora incorporó dentro de la propuesta la filosofía PPMod, siglas de preensamblado, prefabricado y modularización- con la que se abordan estrategias de industrialización en la fase de constructibilidad para la ejecución de los proyectos de construcción. Esa filosofía constructiva, que se había aplicado en proyectos anteriores, se utilizó para la licitación del Truck Shop de Codelco Andina. “Nosotros tomamos esta filosofía en el análisis de estrategias de ejecución e incorporamos una propuesta de valor al contrato y a lo que el cliente nos pedía, nosotros ofrecimos una propuesta alternativa”, explicó Fernández.
De esta manera, se propuso cambiar la materialidad constructiva: hormigón en lugar de acero. Desde Codelco Andina, destacan que esa modificación nació desde Salfa Montajes. “La propuesta se evaluó y aceptamos porque, dentro de esa evaluación, también hubo números importantes con respecto al montaje”, detalló Cristián Rodríguez. “Nosotros nos jugamos con una propuesta bastante arriesgada que es, no presentar la propuesta que Codelco solicitó y nos fuimos directamente a la propuesta alternativa de prefabricados”, subrayó Carlos Fernández.
Una vez aprobado el cambio en la materialidad, Salfa Montajes contactó a Tensacon para suministrar los elementos que darían forma a la futura edificación. En ese sentido, Claudia Cid comentó que “en Tensacon contamos con vasta experiencia en la prefabricación de naves en el segmento industrial, no obstante, el hecho de formar una alianza estratégica en conjunto con Salfa Montajes, para presentar su propuesta de valor, nos haría partícipe de la construcción del primer Truck Shop completamente prefabricado a nivel mundial”.
Dentro de los aspectos que hicieron a Codelco Andina optar por la propuesta basada en elementos prefabricados de hormigón, se encontraban los que comentó el gerente de Desarrollo e Innovación/VP de la constructora. “Las condiciones que tenemos acá en Andina, donde la mitad del año es prácticamente condición de nieve, es adversa para el montaje. Este tipo y este método de hormigón prefabricado mejoraba los tiempos de montaje”, destacó Rodríguez.
“También hay que recordar -puntualizó el especialista senior en Ingeniería Civil Estructural de Codelco VP- que esto se comenzó a ejecutar en pleno Covid. Entonces, era importante de analizar y mantener controladas las HH del proyecto”.
Prefabricados de hormigón: Una solución adecuada y aprobada
Al tratarse de un contrato del tipo EPC, en el que “el contratista es quien asume los riesgos vinculados al desarrollo de ingeniería, suministros y construcción de las obras respectivas”, desde Salfa Montajes explican que se desarrollaron una serie de talleres de constructibilidad en conjunto con Tensacon para abordar los diversos desafíos impuestos por el proyecto.
“Estos talleres tienen un foco específico para dar viabilidad a lo que se pretende realizar. En ellos se evalúan las condiciones del entorno tales como altura geográfica, viento, temperatura, nieve y plan de tránsito, con lo que se determina el plan logístico de almacenamiento, bodegaje, condiciones de montaje, equipos requeridos, cuadrillas, equipamiento, etcétera”, comentó Ricardo García Villegas, gerente de Ingeniería en Salfa Montajes.
“La obra se desarrolla a la intemperie”, explicó Cristián Rodríguez. “Estamos en una zona abierta, entonces, el montaje se debe realizar durante las estaciones de otoño y primavera, porque en invierno prácticamente no hay montaje. Incluso, durante el verano las tormentas eléctricas que se generan afectan el desarrollo de los trabajos. Entonces, sin duda lo bueno y la ventaja de la propuesta de Salfa venía por el lado de la disminución de HH por concepto de montaje”.
Otro de los aspectos a destacar es que, dentro de la planificación de la obra, la presencia de hormigón in situ se limitó sólo a conexiones mecánicas (conexiones húmedas). “En conjunto con Tensacon diseñamos muchas de estas conexiones, con bajo uso de hormigón en el lugar de obra, lo que hace más fácil protegerlas o mantenerla en condiciones ideales para que la estructura tenga las características requeridas por las especificaciones técnicas”, destacó García Villegas.
Así, de todo el volumen de hormigón que se utilizó para esta obra, un porcentaje importante correspondió a elementos prefabricados. Esto permitió que, a diferencia de los Truck Shops construidos con acero, se realizaran ajustes menores en cuanto al ensamblaje de las piezas. “Los elementos prefabricados vienen con un ensamble que es prácticamente como un lego. Entonces, A más B más C, luego se montan y se hormigona el nudo in situ, un hormigón prácticamente tipo grout para afianzar las uniones”, resaltó el jefe de Construcción y Montaje en Codelco VP. “Se tienen menos piezas finales”, puntualizó Rubén Ramos Salas.
Decisiones de ingeniería: Elementos con nudos rígidos
Una vez tomada la decisión de utilizar elementos de hormigón prefabricado para el Truck Shop, que además “es el primer Truck Shop en el mundo que se construye con hormigón prefabricado con nudos rígidos (conexiones húmedas)” -subrayó Vladimir Urzúa Mella, ingeniero civil estructural en Ingeniería DS, oficina a cargo del diseño sísmico del Truck Shop- se inició el diseño de las piezas.
En esta etapa también consideró, además de las restricciones climáticas, las relacionadas con el transporte de los elementos. “Al estar restringidos por la altura, eso claramente nos limitó el transporte”, explicó Cristián Rodríguez. Y desde Salfa Montajes, agregaron que el diseño de las piezas se limitó a 3,5 metros el ancho máximo -determinado por el uso de tres tipos de camiones: ramplas convencionales, ramplas de mayor capacidad y camas bajas- y 4,7 metros de altura máxima, “condicionada por un paso ferroviario previo a la bifurcación de Saladillo, que es de 4,80 metros”, detalló el gerente de Ingeniería de la constructora.
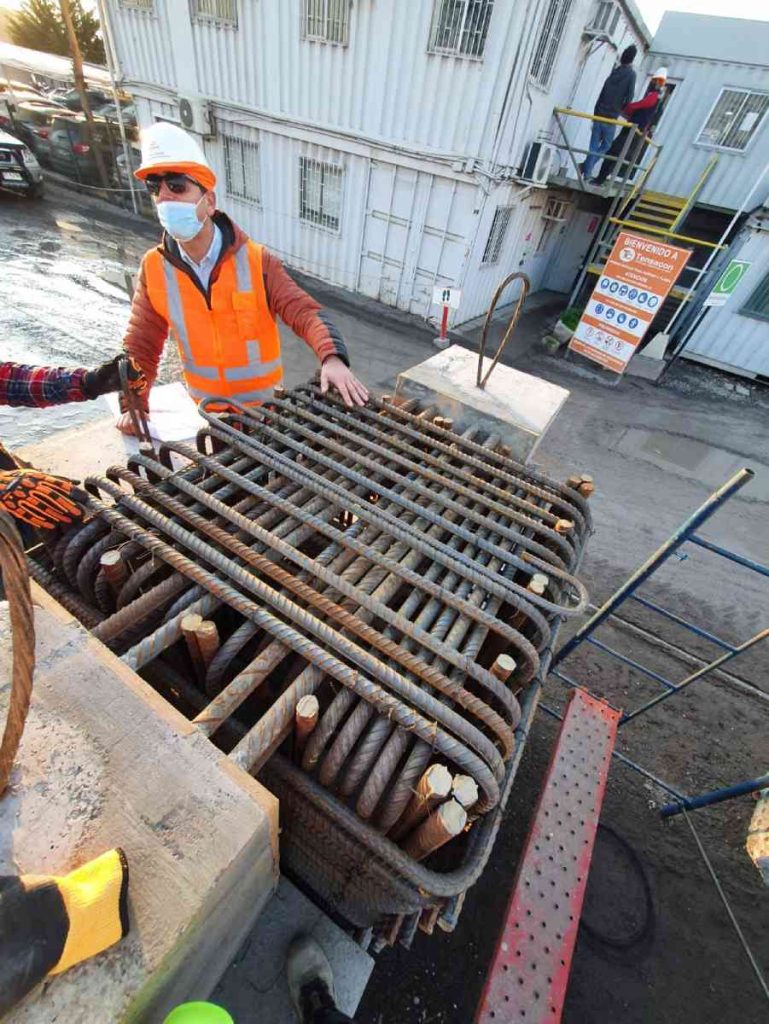
Sin embargo, debido a las dimensiones las propias del Truck Shop -la altura sólo del taller de reparaciones es de 24 metros- requería de elementos de mayor envergadura. “Por ejemplo, las columnas fueron divididas para viabilizar el transporte”, dijo Cristián Rodríguez, de Codelco VP.
En ese sentido, Claudia Cid, gerente de Proyectos Minería de Tensacon, relató que “en Tensacon se efectuaron diversas pruebas con los prefabricados, entre ellas, pruebas de calce de alta complejidad en relación con los nudos rígidos, las cuales tenían como propósito verificar la inexistencia de interferencias, establecer la secuencia de montaje óptima de los elementos y de las armaduras de conexión complementarias y la medición de los rendimientos”.
Asimismo, subrayó que “estos nudos contaban con una cuantía de acero de refuerzo alta, del orden de los 450 kg/m3”.
“Los elementos más largos a transportar alcanzaron 23m, los más pesados, 60 toneladas y se fabricaron un total aproximado de 1.600 elementos” -declaró Ricardo García Villegas-. Esto requirió que Tensacon, empresa proveedora de los prefabricados de hormigón, segmentara los elementos para cumplir con los requisitos de transporte y las condiciones propias del lugar de la obra.
Sobre la integración tanto de Tensacon como de los demás involucrados en el proyecto, el gerente de Ingeniería de Salfa Montajes destacó que se utilizaron conceptos de la metodología LEAN para llevar a cabo esta obra. “Se utilizó la integración vertical de toda la cadena de abastecimiento en la constructibilidad, para visibilizar en conjunto el cómo vamos a materializar esta construcción”.
“Normalmente, el hormigón que se utiliza en construcción tiene tolerancias mayores al ser desarrollado in-situ, pero para este proyecto hubo que diseñar y fabricar elementos de hormigón con tolerancias mecánicas, pero que contemplaran holguras para permitir el desarrollo de la metodología. Entonces, en esas soluciones tuvimos que involucrar a nuestro equipo profesional de terreno, a los calculistas para poder validar las soluciones y al proveedor de prefabricados para materializar esas uniones”.
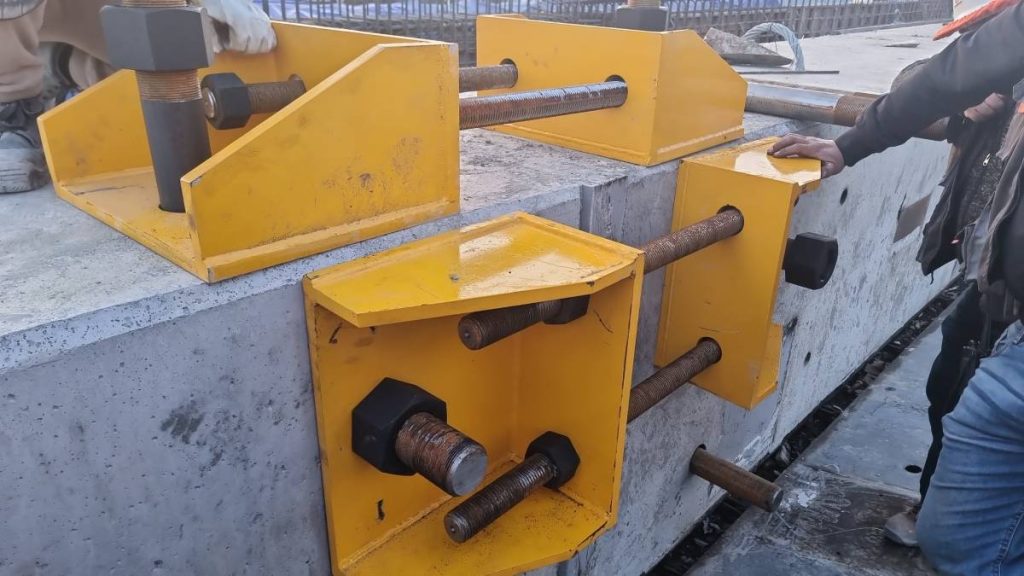
“Este proceso se extendió por unos meses y resultó muy útil, ya que cuando realizamos el taller de constructibilidad e incorporamos en la presentación, como auditor, al equipo integral de Codelco, en el que también participaron especialistas de todas las gamas de ingeniería, no tuvimos observaciones”, destacó Ricardo García Villegas
Planificación al detalle: Talleres de constructibilidad
Una vez tomada la decisión de construir el complejo con prefabricados de hormigón y analizadas las restricciones climáticas como de transporte, el siguiente paso fue desarrollar estrategias de constructibilidad de modo tal que se aprovecharan al máximo los beneficios de la prefabricación y la construcción industrializada.
“Por el lado de ingeniería, para poder sacar provecho a los prefabricados, lo que se debe hacer es una desagregación entre subestructuras de súper estructuras”, explicó el gerente de Ingeniería de Salfa Montajes. “Qué quiero decir con eso: las subestructuras son, esencialmente, todo el sistema de fundaciones y estructuras de apoyo. Esas, tenemos que diseñarlas en una forma temprana para que comience su fabricación y la ventaja será comenzar a fabricar mientras estamos haciendo instalación de faena. Todavía no instalamos los elementos, pero ya estamos haciendo hormigones en planta. Esa es la gran ventaja”.
En ese sentido, las fundaciones representaron entre un 25% a 30% del volumen total de los elementos prefabricados. “En comparación con un Truck Shop construido con acero, en fundaciones el edificio resultó un poco más grande porque había más peso, pero de todas maneras eran tamaños manejables”, comentó el especialista senior Ingeniería Civil Estructural de Codelco VP.
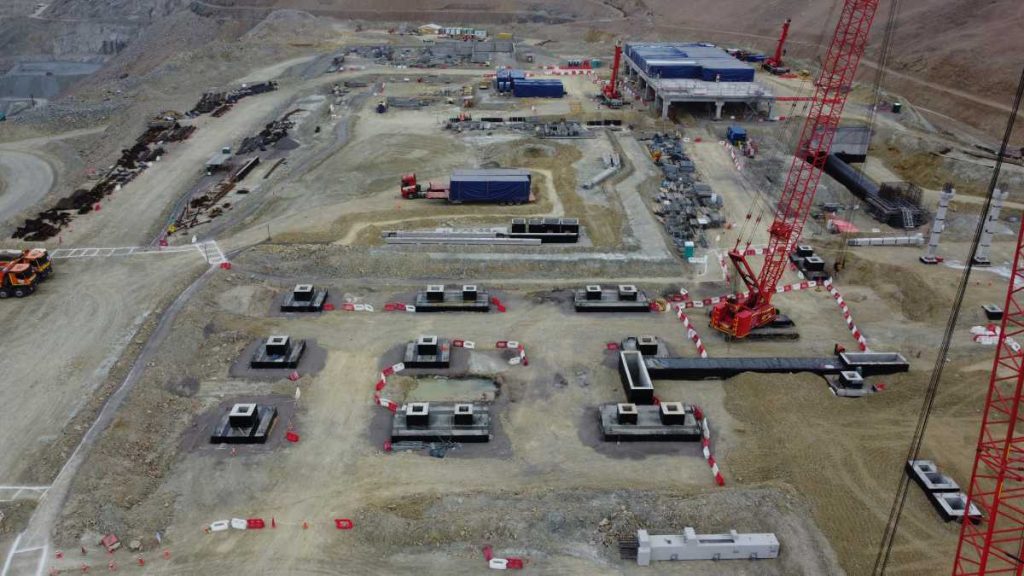
Asimismo, García Villegas destaca que mientras se prefabricaban las fundaciones segmentadas en 3 elementos para facilitar su transporte (fundaciones cuadradas de 5,5m de arista), en el terreno se realizaban trabajos de movimientos de tierra y trazados para llegar e instalarlas.
Junto con esto, otro gran punto en la construcción del Truck Shop fue el cómo se trabajaron las uniones de las columnas, cuya altura llegaba a los 24 metros. Para ello, estos elementos también se segmentaron, y gracias al desarrollo de prototipos a escala 1:1 en el marco del taller de constructibilidad previo a la ejecución del proyecto, se pudieron analizar y desarrollar soluciones para las dificultadas que planteó mantener las uniones de las columnas.
“Por razones que obedecieron a la logística de montaje y transportabilidad, nació la necesidad de segmentar las columnas, cuyo peso inicial bordeaba las 90 toneladas”, explicó la gerente de Proyectos Minería de Tensacon. “A raíz de lo anterior, nuestro departamento técnico, en conjunto con Ingeniería DS, diseñó para el proyecto un sistema conexión que permitió conectar verticalmente ambos segmentos de pilar, minimizar la complejidad de su ejecución en terreno y así evitar cualquier trastorno en los tiempos de montaje, lo cual también pudo ser verificado mediante una prueba de calce en nuestra planta”, agregó.
“En ese sentido -comentó Carlos Fernández Novoa- dado que las columnas tenían su unión a 14 metros de altura, donde se encontraba el nudo a hormigonar, y considerando la interferencia de la armadura, los componentes del hormigón y el diseño mismo de toda la unión, este nudo se convirtió en uno de los principales desafíos para el proyecto. Entonces, el haber desarrollado prototipos a escala 1:1, creo que es un gran avance para el éxito de lo que es la solución constructiva”.
Al respecto, Ricardo García Villegas destaca que se realizaron cuatro variaciones a la propuesta de unión entre las secciones de columnas, las que se llevaron a cabo en el taller de constructibilidad. “El prototipo se desarrolló con la tercera versión e implementamos una cuarta, que venía con mejoras incorporadas de la variación número tres”, dijo.
¿Cómo manejar el montaje? Planificación de las grúas
Desde Codelco, agregaron que otra de las restricciones para la obra en cuanto al montaje de los elementos prefabricados, tuvo que ver con el tipo de grúas a usar. “Tenemos que ocupar grúas de alto tonelaje”, subrayó el jefe de Construcción y Montaje de Codelco VP. “Se están utilizando grúas sobre las 300 toneladas, en especial, en los puntos con más dificultad de la obra”.
Para coordinar a los distintos actores, incluyendo el movimiento de las grúas de montaje, es que desde Salfa Montajes detallan que, dentro de los aspectos de la metodología LEAN que se utilizaron en el proyecto -como el caso de la integración vertical de los actores- también se ocuparon elementos digitales para asegurar el correcto desarrollo del proyecto.
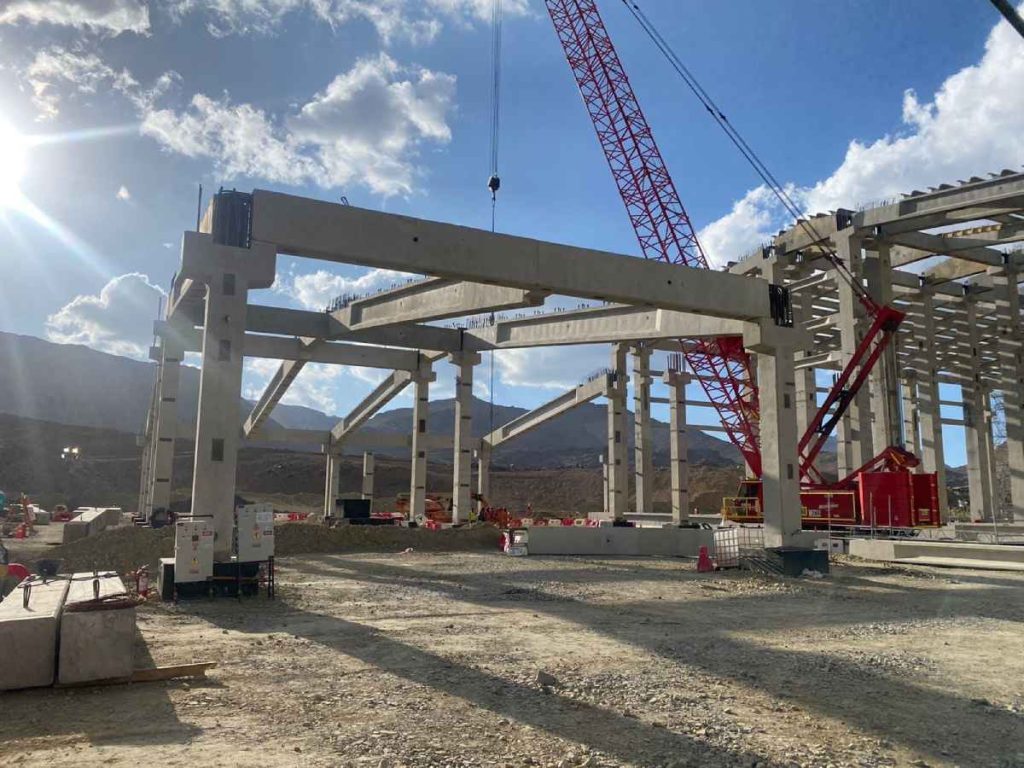
“Adicional a los prototipos con los que simulamos la unión en sí, realizamos una revisión a través de BIM 4D. Generamos animaciones del modelo 3D de acuerdo con el programa de construcción, para evitar trabajos simultáneos en la vertical y que ponen en riesgo a las personas y equipos, o inconvenientes como una secuencia incorrecta de montaje que podría dejar atrapadas a las grúas en medio de las estructuras durante las instalaciones” detalló Ricardo García.
“Por otro lado y para agilizar los procesos, la constructora, a través de Tensacon, desarrolló unos “exoesqueletos” especiales para rigidizar la estructura mientras fraguan las uniones de los elementos. “Se trata de dispositivos auxiliares temporales con la capacidad de carga de la unión durante los días de fragüe y que permiten proseguir los trabajos en otros frentes”, precisó Ricardo García.
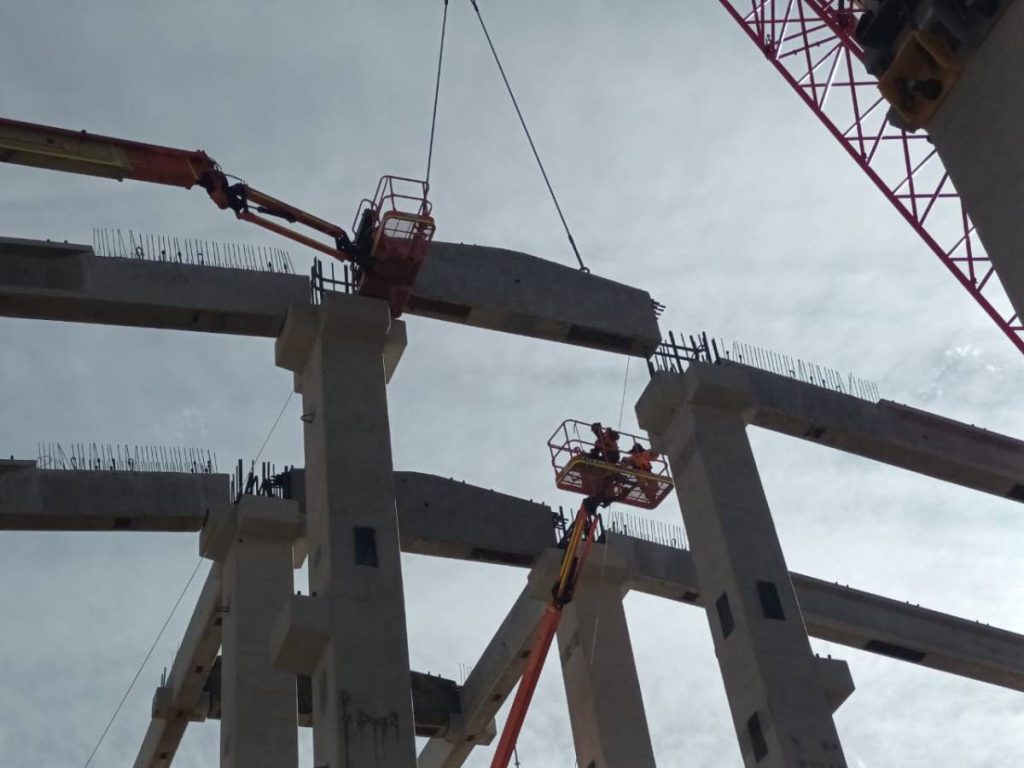
Diseño sísmico: un capítulo extra
Otro de los elementos a destacar de este proyecto se refiere a su diseño sísmico. Primero, porque el Truck Shop no se consideró, por parte de la Vicepresidencia de Proyectos de Codelco como un edificio de estructura metálica. “Al tener uniones húmedas, desde el punto de vista estructural estamos hablando de un edificio de hormigón tradicional”, destacó Rubén Ramos Salas. De esta manera, toda la ingeniería y el diseño sísmico desarrollado para este proyecto, más que “traducir” una estructura de acero a otra materialidad, es, efectivamente, levantar una edificación de hormigón a 3.700 metros sobre el nivel del mar.
En ese sentido, el ingeniero de la estatal explica que se debe conceptualizar el proyecto de manera distinta, “pero respetando siempre el layout”, puntualizó. Por el lado de Salfa Montajes, dentro de la exhaustiva planificación que se realizó para la ejecución del proyecto, también se realizaron análisis y se identificó “el riesgo de las condiciones geotécnicas y revisamos el impacto de ello, verificando la condición del sitio, que cuenta con varias particularidades”, detalló Ricardo García Villegas.
El gerente de Ingeniería de Salfa Montajes detalló algunas, como “la amplificación topográfica por la altura, ya que se mueve más que a nivel de un valle. Entonces, se analizó la amplificación topográfica, las características del suelo y, sobre todo, porque esto ha sido un relleno dinámico desde los años ochenta. Para considerar este último efecto se generó una predicción de asentamientos en dos etapas: asentamientos durante la construcción y asentamientos bajo un movimiento sísmico severo”.
“La condición de diseño que exige Codelco es bastante alta en cuanto a diseño sísmico”, subrayó Vladimir Urzúa Mella, gerente general en DS Ingeniería, oficina que estuvo a cargo de este ítem. “Para este caso particular, también se consideró la sobrecarga de nieve, que fue de 1.950 kilogramos por metro cuadrado y para efectos de masa sísmica, se consideró peso propio más cargas muertas, más equipos y el 50% de la sobrecarga de nieve. Entonces, nos dio una estructura bastante robusta, pero a la vez, bastante eficiente”, explicó el gerente general de DS Ingeniería, quien además es gerente técnico del Comité Iberoamericano de Hormigón Prefabricado e integrante del Comité NCh2369/2003.
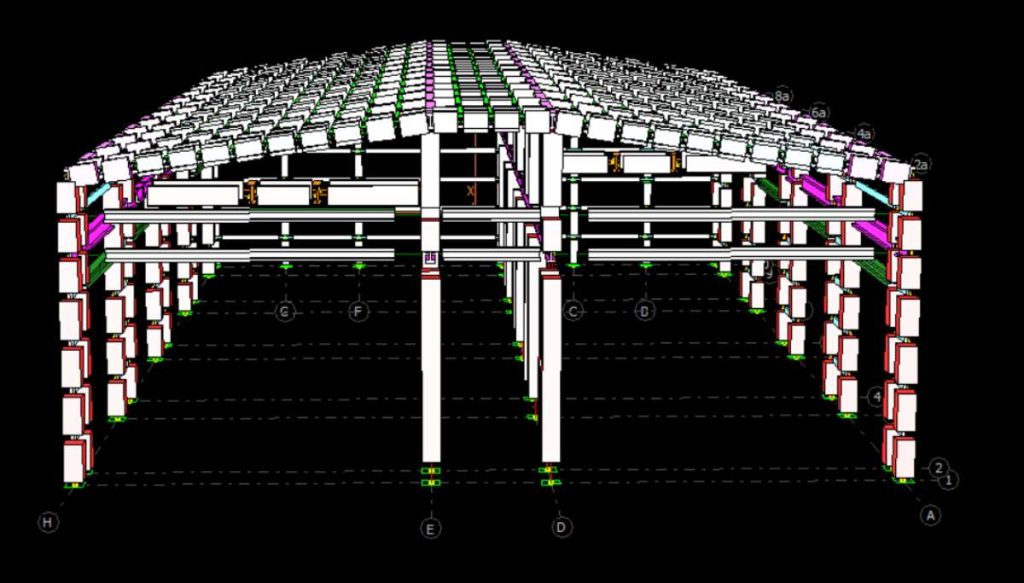
Para conseguir dicha robustez, se especificó que todos los elementos prefabricados de hormigón suministrados por Tensacon -columnas, vigas maestras, vigas secundarias, costaneras de techo, costaneras laterales y fundaciones- se fabricasen con hormigones de alta resistencia. “Para el caso de la súper estructura -dijo Vladimir Urzúa- se utilizaron hormigones que parten en G40 (columnas) y terminan en G55 (vigas)”. En esa línea, el ingeniero también comentó que se “usaron hormigones con relación agua/cemento menor que 0,4 con lo cual se obtuvieron hormigones impermeables, según ACI 318 S14”.
Para mejorar aspectos de constructibilidad de la obra, también se utilizaron “barras de acero de alta resistencia de 80 Ksi (Fy = 5.500 kg/cm2) con la finalidad de descongestionar los nudos rígidos y mejorar la constructibilidad, ya que teníamos columnas con cuantías de 400 kg/m3, Vigas con armadura pasiva 350 kg/m3 y Nudos rígidos con cuantías entre 450 a 550 kg/m3”, detalló Urzúa.
En el caso del diseño sísmico propiamente tal, el ingeniero civil estructural puntualizó que se usó “la norma NCh 2369, oficial del año 2003 (Factor de modificación de respuesta R=5 y amortiguamiento Ɛ=3%) y aparte, los criterios de diseño de Codelco”. En el caso específico de la sobrecarga de nieve, “ésta se estableció como criterio de diseño por Codelco y lo que hace muy exigente la solicitación sísmica es que se suma el peso propio con la carga muerta más el 50% de la sobrecarga de nieve, entonces, es una masa muy alta”.
La aplicación del modelo matemático para el diseño sísmico del Truck Shop, dice el gerente técnico del Comité Iberoamericano de Hormigón Prefabricado, consideró dos aspectos. “Uno, el proyecto ya terminado con la modelación sísmica, modelo 3D, y el otro, no menos importante, que es la estabilidad sísmica durante el montaje, porque, por ejemplo, los pilares se hacen en dos tramos, pero a medida que voy montando, monto el primer tramo, tengo que asegurar sísmicamente porque todavía no tengo hormigonado los nudos rígidos arriba (condición de péndulo invertido), que son los elementos que conectan las vigas con los pilares”.
Ahí es donde entran en juego los “exoesqueletos” desarrollados por la constructora, que son los que toman esa carga. “Después, se monta la segunda parte del pilar, con unos pivotes sísmicos, que son los que controlan la deformación horizontal en caso si viniera un sismo severo antes de que la estructura esté 100% hormigonada. Entonces, son dos etapas: primero, la estabilidad sísmica durante el montaje y la estabilidad sísmica durante la operación del Truck Shop. Eso es que lo hace un proyecto bien complejo”, puntualizó Vladimir Urzúa.
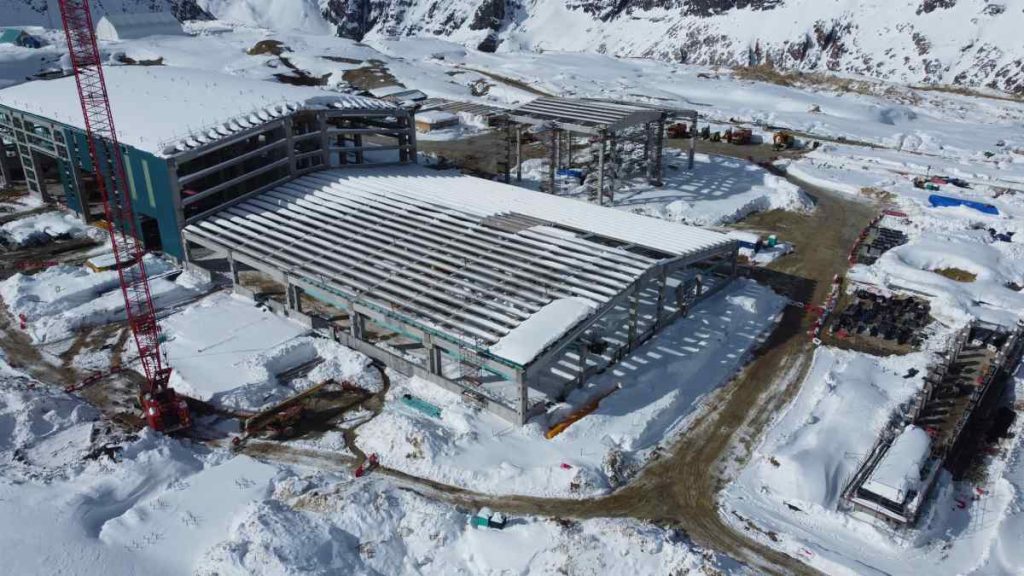
En ese sentido, Ricardo García Villegas explica que “se desarrolló una secuencia de montaje de los prefabricados que toma en cuenta las deformaciones del suelo durante las etapas constructivas y además la estructura resiste las deformaciones durante un sismo severo. Esto es muy importante y quiere decir que si se cierra un marco resistente y el suelo se sigue asentando, el marco toma la carga. Entonces, hay una secuencia de ejecución de los nudos que cierran los marcos para reducir el esfuerzo que tomen durante los asentamientos temporales”.
Asimismo, añadió que existe una segunda secuencia en la que “todas las conexiones hidráulicas, eléctricas y sanitarias de los edificios son lo último que se va a realizar, dando la tolerancia que el edificio se asiente durante la etapa constructiva temporal y posteriormente realizar las conexiones o tie-in”.
Para Vladimir Urzúa, el segundo análisis, que se refiere a la estabilidad sísmica durante el montaje de los elementos, es “fundamental en los proyectos de prefabricados”.
Un complejo único para la minería
La construcción de este Truck Shop representó, sin dudas, todo un desafío para las partes involucradas. “Si bien todos los proyectos son únicos”, subrayó Carlos Fernández Novoa, gerente de Desarrollo e Innovación/VP Montajes. “En particular aquí, el desafío de la transformación de una estructura que nunca se había hecho, en las condiciones, contexto y geografía, claramente, realzan su carácter único”, destacó.
En ese sentido, Vladimir Urzúa también enfatizó que se trata de un edificio único “en Chile y en el mundo, por eso este Truck Shop de Codelco Andina es tan vanguardista. En mi calidad de gerente técnico para el Comité Iberoamericano de Hormigón Prefabricado, no he visto ninguna edificación en el mundo que tenga este nivel ni mucho menos, esta sobrecarga”.
Otro de los aspectos que hace único a este proyecto fue el nivel de planificación que se tuvo para llevarlo a cabo. Como detalla Ricardo García Villegas, “el proyecto fue adjudicado el 25 de noviembre de 2021. Las prioridades estuvieron con la factibilidad de ingeniería y movimiento de tierra, que fueron liberados en la primera semana de enero de 2022, y entre diciembre de 2021 y marzo de 2022, preparamos el taller de constructibilidad. El taller se presentó a fines de marzo de 2022, se aprobó y comenzamos a construir prefabricados de inmediato en abril, realizando despachos en ese mismo mes”.
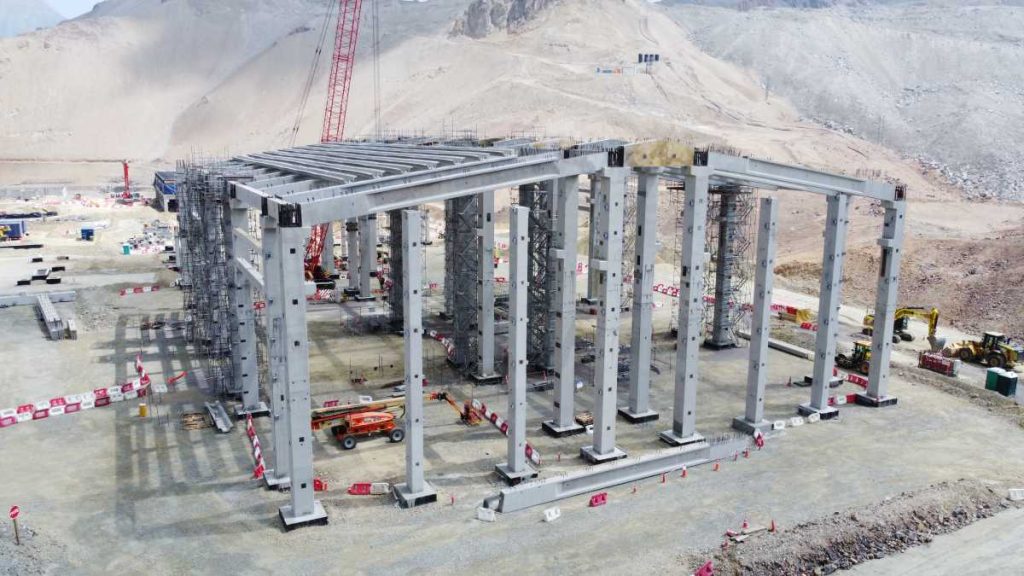
No sólo eso, “el cambio de materialidad para la edificación significó importantes beneficios en términos de protección contra el fuego, minimizando el uso revestimientos intumescentes y en materia de sustentabilidad, se redujeron al mínimo los despuntes, residuos de distinto tipo entre los que se cuentan los de aseo de camiones de hormigón”, dijo García Villegas.
“En cuanto a calidad, las condiciones de planta son mucho más controladas que en terreno, por lo que se reduce significativamente la fracción defectuosa de los hormigones. Incluso, la normativa para elementos prefabricados es más rigurosa en cuanto a análisis dimensional, lo que mejora todavía más la calidad”, destacó.
“La construcción de este complejo en nuestras instalaciones significó tremendos desafíos”, destacó Claudia Cid. “Se tuvo que revisar cuidadosamente el diseño de los hormigones para atender a las clases de exposición de acuerdo a las especificaciones técnicas del proyecto, el diseño de conexiones no convencionales, realización de pruebas de calce de alta complejidad, fabricación de elementos de gran volumen, cuantías de acero de refuerzo inéditas, tolerancias específicas del proyecto (de mayor exigencia que las establecidas en el PCI), diseño y logística de transporte, diseño de elementos transitorios para el montaje, elaboración de una secuencia de fabricación acorde a la secuencia de montaje de la constructora, entre muchos otros”.
“Sin duda, este proyecto generó un gran crecimiento y aprendizaje en nuestra compañía, no solo desde el punto de vista técnico, sino también en la consolidación de los equipos de manera interna y el gran aporte del trabajo colaborativo con nuestros clientes”, destacó la profesional.
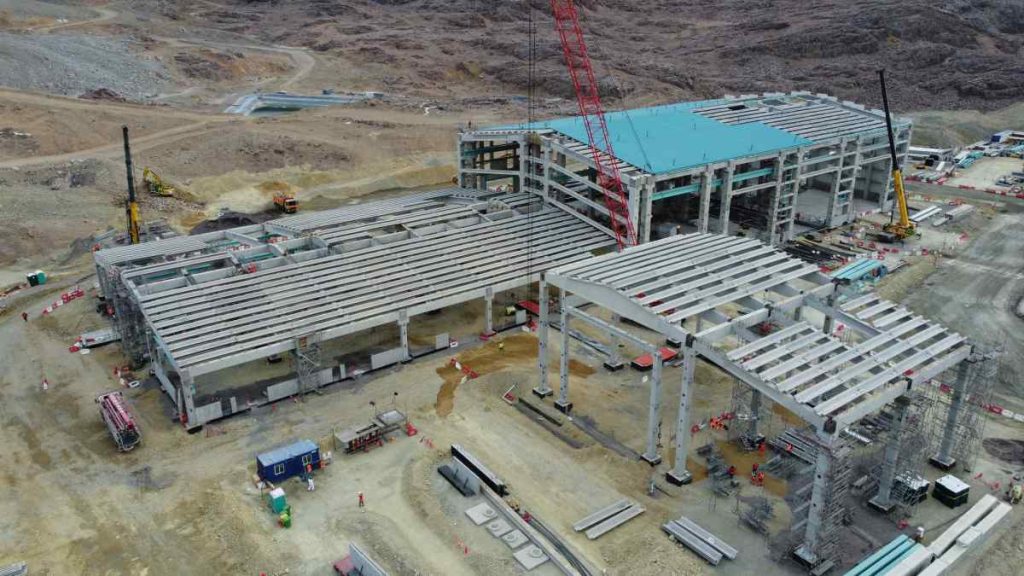
El innovador trabajo en el nuevo Truck Shop a cota 3.700 de Codelco Andina se está analizando en otras divisiones de la estatal. Según informó el jefe de Construcción y Montaje en Codelco VP, profesionales de la División El Teniente revisaron el proceso de montaje y el modelo del complejo desarrollado para división Andina, mientras que el especialista senior en Ingeniería Civil Estructural en Codelco VP comentó que en Codelco Salvador también se construye un Truck Shop con similares características, del que está a cargo el equipo liderado por Vladimir Urzúa.
FICHA TÉCNICA
TRUCK SHOP 3.700, CODELCO ANDINA
- Superficie total: 60.000 m2 aproximados
- Área construida: 12.206,08 m2
- Volumen de hormigón: 7.000 m3 de hormigón prefabricado (3.200 m3 en taller de camiones).
- Mandante: Codelco Andina
- Constructora: Salfa Montajes
- Diseño sísmico: DS Ingeniería
- Construcción de elementos Prefabricados: Tensacon S.A.