Si bien en un inicio se contempló la construcción bajo un sistema tradicional, luego de un análisis temprano conjunto entre mandante y prefabricador, se llegó a la convicción de utilizar esta tecnología constructiva para el desarrollo de este tipo de infraestructura, lo que generó elementos prefabricados de hormigón con características únicas en el mundo, dadas las especificaciones técnicas solicitadas para esta gran obra.
A fines de 2023, el directorio de Antofagasta Minerals -responsable de operaciones mineras como Zaldívar y Los Pelambres, entre otras- anunció una inversión de US$4.400 millones para el proyecto Nueva Centinela (DMC), transformándose en la mayor inversión minera iniciada en los últimos cinco años.
Respecto a este gran proyecto, Iván Arriagada, presidente ejecutivo de Antofagasta Minerals, explicó que “Nueva Centinela es un proyecto clave para nuestro crecimiento, ya que agregará 144.000 toneladas de cobre, 3.500 toneladas de molibdeno y 130.000 onzas de oro adicionales por año, con la primera producción esperada para 2027. Este proyecto contribuirá significativamente a la aspiración del Grupo de producir 900.000 toneladas de cobre en el largo plazo”.
Entre las obras que considera el proyecto Nueva Centinela (DMC), se incluye la construcción de una segunda planta concentradora de cobre en Minera Centinela y la ampliación de su planta para producir molibdeno. Junto con estas obras, también se desarrollarán una serie de elementos que permitirán la operación de un proyecto que, como destacan desde Antofagasta Minerals, se situará entre las 15 principales minas de cobre del mundo gracias a esta expansión en su capacidad productiva.
Así, dentro del proyecto Nueva Centinela (DMC) se contempló la construcción de una grúa gantry o grúa pórtico -elemento que se mueve sobre una estructura similar a un pórtico y que se utiliza para elevar y transportar cargas pesadas- además de cámaras recuperadoras para áridos. Para la fabricación de estos elementos, el uso de prefabricados de hormigón resultó clave.
Desafíos para el prefabricado de hormigón en el contexto de Nueva Centinela
Como se mencionó anteriormente, la construcción de infraestructuras mineras está experimentando una transformación sin precedentes con la adopción de elementos prefabricados de hormigón. Un ejemplo de ello se puede apreciar en el truck shop en Codelco Andina, infraestructura fabricada de manera íntegra con esta tecnología.
En el caso del proyecto Nueva Centinela (DMC) se implementaron soluciones que combinan hormigones de ultra alta resistencia, acero de alta calidad y estrategias de pretensado complejas, permitiendo materializar estructuras que hace pocos años se consideraban técnicamente inalcanzables.
De acuerdo con Gigliola Rivano Barisone, jefe de Proyectos en Preansa -empresa que suministró los elementos prefabricados de hormigón para la construcción de la infraestructura requerida por el proyecto DMC- la iniciativa nació en un escenario en el que la necesidad de ahorrar tiempo, buscar la eficiencia económica y garantizar la durabilidad a largo plazo motivó la transición del método constructivo in situ a técnicas de fabricación en planta.
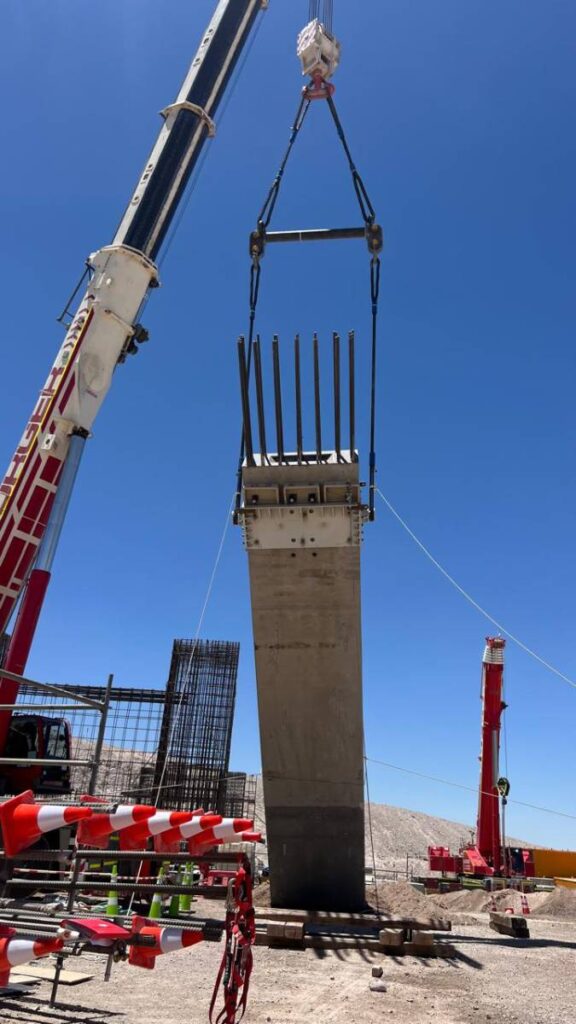
Así, el proyecto DMC, que originalmente contemplaba tres estructuras –el edificio de hidrociclones, la grúa gantry y las cámaras recuperadoras de áridos– evolucionó: mientras el edificio de hidrociclones se mantuvo en su concepción metálica por razones de cargas y complejidad en la fabricación, explica la personera de Preansa, la grúa gantry y las cámaras se adaptaron a un proceso de prefabricación que ha permitido optimizar tiempos, asegurar la calidad y minimizar la mano de obra en terreno.
Transitar desde metodología constructiva tradicional a prefabricado de hormigón
Inicialmente, se proyectaba que las estructuras se erigirían mediante construcción tradicional de hormigones in situ. Sin embargo, fue durante las primeras reuniones de coordinación –explicó Rivano– que se destacó el potencial de prefabricar estos elementos, en vez de utilizar la metodología tradicional.
“Este fue un proyecto que en su concepción original estaba pensado como un proyecto in situ, tanto para el edificio de hidrociclones como para la grúa y para los túneles de recuperación. Pero, posterior a ese planteamiento, se decidió traspasar a prefabricado los elementos de la grúa y las cámaras, basándose en el ahorro de tiempo, la longevidad de las estructuras y la baja mantención que permite usar hormigón en lugar de estructuras de acero”.
Este cambio en la metodología constructiva -pasar de hormigones in situ a prefabricados- que se articuló en estrecha coordinación entre el equipo de diseño y las empresas fabricantes, implicó no sólo replantear la logística y la ejecución, sino también una profunda adaptación en la planta de fabricación.
“Para poder materializarlo solamente podíamos participar un par de empresas en Chile que tuviéramos la capacidad de fabricarlo. Y, en efecto, los desafíos técnicos y logísticos nos dieron la ventaja comparativa necesaria para llevar a cabo la fabricación de elementos tan masivos”, destacó la vocera de Preansa.
La solución de prefabricar en planta –y de ensamblar en obra mediante uniones húmedas– se impuso, en parte, por las ventajas inherentes a contar con un ambiente controlado. Se minimizan las incertidumbres propias de la ejecución en terreno, se estandarizan los procesos de curado y se reducen los tiempos de montaje. En efecto, comenta la experta, mientras en la fábrica se producen elementos pesados y dimensionalmente exactos, en terreno se avanza en paralelo en otras áreas críticas de la obra, acortando así el plazo total de construcción.
Desafíos logísticos asociados al proyecto
El proceso de trasladar la ingeniería básica –que en teoría resulta “geométricamente perfecta”– a planos de fabricación y, posteriormente, a piezas prefabricadas, generó múltiples desafíos.
En ese sentido, la jefe de Proyectos de Preansa puntualizó que “lo que en el papel parece sencillo, en la realidad implica un mundo de diferencias, porque cada elemento debe adaptarse a la naturaleza del acero con estrías, a la masividad del hormigón y a la precisión necesaria para el pretensado. Por eso, la primera pista de vigas pretensadas pesadas fue, sin duda, el desafío más duro”.
Entre los retos más complejos se destacó la integración de armaduras pasivas con una alta concentración o cuantía. Vladimir Urzúa Mella, ingeniero civil estructural de vasta trayectoria y responsable del diseño matemático de los elementos prefabricados, entrega datos precisos respecto a las denominaciones y cuantías utilizadas en el proyecto:
“Para el marco rígido de la grúa gantry, se utilizaron hormigones de clase G50 en los pilares y G55 en la viga carrilera, complementados con acero de alta resistencia de 80 Ksi (Fy = 5.500 kg/cm2)”, puntualizó. “La columna más alta alcanza una altura de 19 metros y un peso de 95 toneladas, mientras que la viga carrilera más larga mide 20,7 metros con un peso de 77 toneladas”.
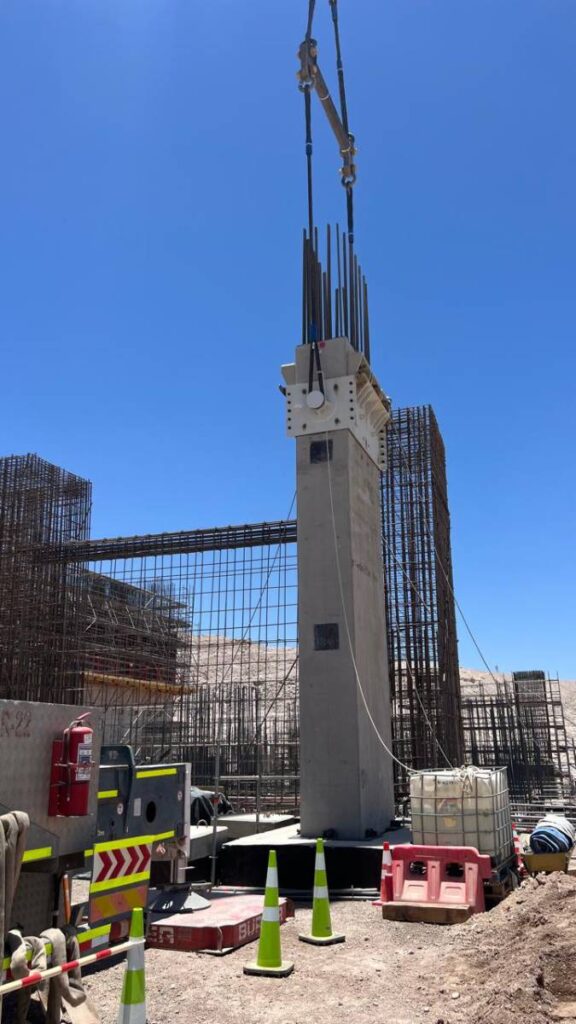
En cuanto a las cámaras recuperadoras de áridos, Urzúa especificó que “se emplearon vigas pretensadas en sección mixta, con hormigones que oscilan entre G55 y G70, y en algunos casos se incorporan hasta 98 cables de ϕ0,6 pulgadas. Este detalle técnico, que implica una fuerza horizontal en bancada de 1.955 toneladas, marca un hito en el desarrollo de vigas pretensadas en Chile, ya que las cabezas de tiro debieron ser reforzadas, superando el límite anterior de 1.500 toneladas”.
“Nos enfrentamos a retos importantes -agregó Rivano- como la unión de dos pistas de pretensado, cada una con una longitud de 150 metros, para formar elementos que, en algunos casos, alcanzan las 140 toneladas. Las modificaciones en la fábrica, necesarias para trabajar con piezas de más de cuatro metros de ancho, resultaron cruciales para dotarnos de la capacidad técnica necesaria.”
Junto con eso, la jefe de Proyectos en Preansa subraya el reto que supuso el manejo de hormigones ultra especiales. La producción de hormigón G70, por ejemplo, permitió alcanzar resistencias superiores a 80 MPa a los ocho días, un resultado que superó las expectativas y validó la estrategia de fabricación en planta. La densidad de los hormigones –con cuantías que en algunos elementos se elevan hasta 450 kg/m3– implicó el uso de una concentración inusual de armaduras, lo que a su vez demandó una planificación meticulosa en el moldeado, el vertido y el curado del material.
Una de las dificultades técnicas más complejas resultó en la necesidad de controlar la hidratación y la temperatura interna durante el fraguado. De acuerdo con Rivano, la experiencia en obras de “vigas de puente” permitió al equipo anticipar las complicaciones inherentes a grandes volúmenes de hormigón. Así, mediante el uso de curado con vapor y el control de secuencias de llenado –en ocasiones, el vertido de una pieza de 40 metros cúbicos demoraba hasta seis horas– se logró garantizar que el producto final cumpliera con los exigentes estándares de calidad planteados por el proyecto.
Innovación en la ingeniería y en el diseño
El carácter innovador del proyecto DMC no se limitó únicamente a los aspectos técnicos de la producción; también se reflejó en la forma en que la ingeniería y el diseño se adaptaron a las exigencias de la prefabricación. Durante el desarrollo del proyecto se recurrió a modelos matemáticos y simulaciones computacionales que permitieron prever las tensiones y las deformaciones en cada uno de los componentes.
“Utilizamos modelos de simetría y análisis estructural para determinar, por ejemplo, que las vigas pretensadas en las cámaras recuperadoras debían soportar una fuerza horizontal en bancada de 1.955 toneladas; este dato fue determinante para rediseñar las cabezas de tiro y garantizar la estabilidad global de la estructura”, destacó la vocera de Preansa.
La coordinación entre la oficina de ingeniería y la planta de fabricación fue fundamental para lograr que lo diseñado en papel se tradujera en piezas prefabricadas con exactitud en algunos casos milimétrica.
“El traspaso de la ingeniería básica a planos de fabricación fue un proceso iterativo. En cada fase se revisaban las diferencias entre lo teórico y lo práctico; el uso de uniones húmedas en los pilares –con conexiones tipo macho-hembra hechas con sistema match-casting– y la fragmentación de pilares de más de 20 metros en dos piezas ensambladas en obra, son ejemplos de cómo se adaptó el diseño a las realidades de la producción”, subrayó Gigliola Rivano.
Otro aspecto decisivo fue la incorporación de elementos de pretensado que permitieron que las estructuras soportaran las elevadas cargas sin perder integridad. El proceso implicó el uso de cables de alta resistencia, cuya tensión debió ser controlada con precisión.
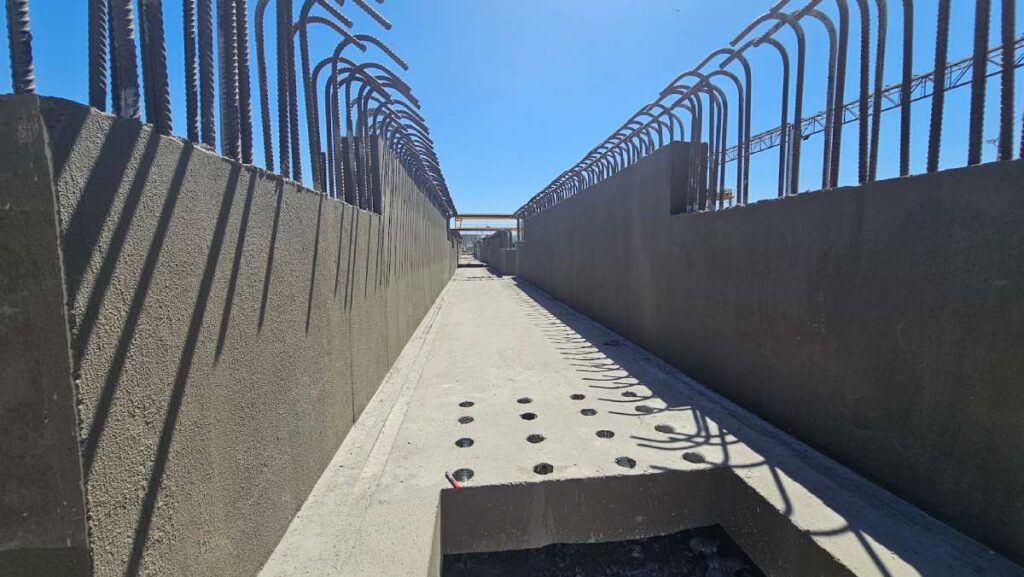
“Contar con dos pistas de pretensado y unirlas en una única estructura es un reto de ingeniería que pocas empresas pueden afrontar. La precisión en la tensión y ubicación de los cables y la compatibilidad con los insertos, ductos y armaduras fue un desafío que, afortunadamente, pudimos superar gracias a la gran experiencia acumulada y a la tecnología de modelamiento 3D aplicada”, agregó.
Esta integración tecnológica confiere a las estructuras una excepcional capacidad para soportar cargas extremas, lo cual se traduce tanto en una mayor seguridad operativa como en una vida útil extendida.
La importancia de una planta que permita cumplir con el desafío
La jefe de Proyectos en Preansa subraya la importancia de contar con una planta de fabricación adaptada especial y exclusivamente para este tipo de proyectos, en la que incluso la logística interna –como el desplazamiento de piezas masivas con puentes grúa o la coordinación en el acopio de elementos– representa un reto que se ha convertido en uno de los diferenciadores técnicos.
En ese sentido, Vladimir Urzúa respalda esa afirmación con datos precisos y cuantificables. El ingeniero civil estructural detalló que el proyecto DMC se erige sobre dos pilares fundamentales:
- El marco rígido para grúa gantry, con un peso propio de 434 toneladas y un puente de 66 metros, en el que se utilizan hormigones G50 para pilares y G55 para la viga carrilera.
- Las cámaras recuperadoras de áridos, en las que las vigas pretensadas –algunas de las cuales cuentan con hasta 98 cables de ϕ0,6″– trabajan en sección mixta y requieren resistir fuerzas horizontales de hasta 1.955 toneladas.
Tal como explica el experto, estas innovaciones implican “un gran avance tecnológico, ya que ahora se puede prefabricar muchos elementos de grandes dimensiones combinando aceros de alta resistencia, alta fuerza de pretensado y hormigones de alta resistencia”.
Asimismo, añade que estas cifras y especificaciones técnicas son el reflejo de un proceso de ingeniería meticuloso y de la capacidad de adaptación frente a los desafíos de la construcción en un entorno tan exigente como el minero.
Impacto del uso de prefabricados en la gran minería
El traslado de gran parte de la fabricación a ambientes controlados no sólo permitió lograr una calidad superior de los elementos prefabricados, sino que también ha tenido un impacto directo en términos de competitividad y seguridad operativa en las faenas mineras. Según comenta la jefe de Proyectos de Preansa, las ventajas del prefabricado se ven reflejadas en una serie de aspectos fundamentales:
• Reducción de la Mano de Obra en Terreno. En el entorno minero, cada trabajador extra se traduce en altos costos operativos. Rivano explicó que “un trabajador en la planta de prefabricados puede equivaler a dos o incluso tres en campo, considerando además los costos asociados a campamentos, transporte y medidas de seguridad”. Esta racionalización de la mano de obra es fundamental en un contexto en el que, como se comentó anteriormente, la constructora tenía una dotación máxima de campamento y no podía superar las 500 personas en la obra.
• Ahorro en Tiempos y Costos. La producción en serie de elementos prefabricados, con ciclos de desmoldeo y curado que permiten reutilizar las pistas de fabricación en cuestión de horas, se traduce en un ahorro significativo en el plazo total de la obra. En ese sentido, Rivano destacó que “mientras se realizan las obras civiles en terreno, nosotros podemos estar prefabricando; de allí que el plazo total de la obra se reduzca drásticamente, permitiendo que la inversión se recupere en menos tiempo”.
• Mejoras en la Seguridad. Otro aspecto decisivo es que la prefabricación reduce la exposición a condiciones adversas y al manejo manual de elementos en terreno, lo que mejora los índices de seguridad. La necesidad de utilizar grúas especiales –e incluso dos en tándem para mover elementos de gran masa– es un reflejo de la rigurosidad con la que se abordaron estos procesos, minimizando así los riesgos de accidentes en faenas donde la seguridad es una prioridad absoluta.
• Sostenibilidad y Control Ambiental. La concentración de la producción en planta permite un uso más eficiente de los recursos y la minimización de residuos. Además, la capacidad de fabricar en un ambiente controlado ayuda a evitar inconsistencias debidas a condiciones climáticas adversas y a optimizar el consumo de energía, un aspecto que ha comenzado a valorarse en términos de impacto ambiental en la minería moderna.
La integración temprana del prefabricado en el proceso de diseño –tal como enfatiza Vladimir Urzúa Mella– resultó decisiva para que las oficinas de ingeniería hoy incorporen estas tecnologías de manera natural en la planeación básica de sus proyectos.
En esa misma línea, la jefe de Proyectos en Preansa puntualizó que “en la actualidad, las fundaciones y otros elementos estructurales ya vienen diseñados para ser enviados al prefabricador, lo que permite que los proyectos se desarrollen de forma modular, como si se tratase de un gran juego de ‘Lego’, donde cada módulo se une con conexiones húmedas y se arma en obra sin las complicaciones de un moldaje in situ tradicional”.
El avance del prefabricado de hormigón y su camino en la gran minería
La inclusión de esta tecnología constructiva en el desarrollo del proyecto DMC refleja, en gran medida, la experiencia previa que vienen acumulando las empresas dedicadas a la prefabricación en Chile. En el caso específico de Preansa, la participación en proyectos que contaron con elementos de “vigas de puente” y otras obras de gran envergadura, permitió al equipo a cargo de los elementos para Nueva Centinela anticipar y resolver problemas que, de otra forma, habrían supuesto cuellos de botella en la producción.
En ese sentido, Rivano subrayó que “hemos alcanzado un nivel de expertise tal, que actualmente somos capaces de fabricar elementos masivos –algunos de hasta 140 toneladas– con la misma velocidad y precisión que piezas convencionales. Esa capacidad nos abre la puerta a nuevos retos, especialmente en proyectos mineros, que requieren de elementos prefabricados con características de diseño complejas”.
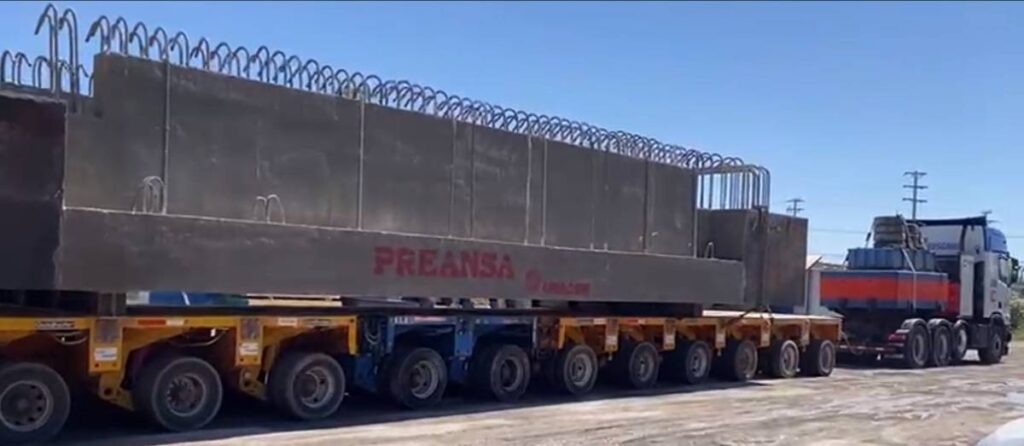
Asimismo, resalta el impacto de tener una planta adaptada específicamente para estos proyectos. “Tuvimos que adecuar la fábrica, modificar las pistas de pretensado y ajustar la logística interna para manejar piezas que, en condiciones normales, serían impensables. Esto nos ha permitido no sólo cumplir con los plazos, sino también garantizar que cada elemento cumpla con todos los requerimientos de diseño, técnicos y de calidad”, explicó.
De acuerdo con la visión que tiene la profesional, el futuro apunta hacia una mayor integración del prefabricado, particularmente en proyectos mineros y de infraestructura civil. La experiencia del proyecto DMC abrió el camino para que, en un nuevo paradigma, toda la ingeniería de un proyecto se conciba desde la perspectiva de la fabricación en planta, apostando a reducir la incertidumbre en terreno y a mejorar la eficiencia global del proceso constructivo.
“Lo que antes parecía una modificación puntual en el proceso constructivo, en la actualidad se transformó en un importante cambio en la manera de pensar la infraestructura”, puntualizó Rivano. “La modularidad y la prefabricación ya permiten que proyectos de gran envergadura puedan ejecutarse simultáneamente en la fábrica y en obra, disminuyendo significativamente el tiempo total y los recursos necesarios”.
En esa línea, también el impacto positivo se asocia a la eficiencia en materia económica, destaca la experta. Con los altos costos de mano de obra y las dificultades logísticas en faenas mineras –donde, además, la seguridad y los límites de los campamentos imponen requisitos muy estrictos– los elementos prefabricados de hormigón se posicionan como la alternativa más eficiente. Y es que sus beneficios se traducen en ahorro de costos, menor impacto ambiental y, sobre todo, en la posibilidad de ejecutar proyectos en plazos reducidos.
Un aspecto aún por estudiar: el impacto en la sostenibilidad
A juicio de la jefe de Proyectos en Preansa, la experiencia del proyecto Nueva Centinela (DMC) abre un interesante camino, que se refiere a la manera en que la industria del prefabricado de hormigón aporta al desarrollo más sostenible y eficiente de un importante sector productivo del país, como lo es la gran minería.
En ese sentido, las cualidades que posee este sistema constructivo, como la reducción en el número de trabajadores en terreno, el ahorro en tiempos de ejecución, además de los avances técnicos que permiten la producción de piezas de mayor calidad -casi personalizadas, dependiendo de los requisitos del proyecto- son factores que, en conjunto, potencian la competitividad de la industria.
Junto con esto, la mayor eficiencia en el uso de recursos y la reducción de residuos contribuyen a minimizar la huella ambiental de las operaciones, un aspecto que adquiere una importancia creciente en el contexto actual de sostenibilidad.
“No se trata únicamente de reemplazar una técnica por otra -explicó Gigliola Rivano- estamos hablando de revolucionar la forma en que concebimos toda la construcción de infraestructuras mineras. Prefabricar en ambiente controlado no solo garantiza la calidad, sino que se traduce en ahorro de recursos y en una mayor responsabilidad ambiental.”
Estas innovaciones, que combinan la precisión del diseño asistido por ordenador, el control de calidad en los ensayos en laboratorio y la experiencia práctica en planta, están sentando las bases para que futuros proyectos –ya sean desaladoras, obras civiles o nuevas faenas mineras– puedan incorporar de forma natural la metodología del prefabricado. La posibilidad de ensamblar estructuras complejas a partir de módulos producidos en ambientes controlados permite alcanzar un nivel de estandarización que antes estaba fuera de alcance, reduciendo la incertidumbre inherente a la construcción en campo.
Tal avance se suma a la creciente tendencia internacional de apostar por la construcción modular y prefabricada. En un entorno en que cada día se valoran más la seguridad, la rapidez y la optimización de recursos, la experiencia en proyecto Nueva Centinela (DMC) se transforma en una suerte de modelo a seguir en el sector. En ese sentido, se vislumbra una mayor integración de las técnicas de prefabricados de hormigón, en donde el “hacer en obra” se transforme, progresivamente, en “fabricar en planta y ensamblar en terreno”.
Proyecto Nueva Centinela y los desafíos del prefabricado de hormigón
El proyecto Nueva Centinela (DMC) de Antofagasta Minerals evidencia cómo la inclusión de prefabricados de hormigón para el desarrollo de infraestructura en obras críticas de la gran minería permite entregar soluciones eficientes para el desarrollo de ese importante sector productivo.
La transición del método constructivo tradicional al uso de prefabricados de hormigón, desarrollados con hormigones de alta resistencia (G50, G55, G60 y G70) y acero de 80 Ksi, logró superar barreras que en el pasado se consideraban insalvables.
Con pilares de 19 metros de altura, vigas carrileras precisas y la incorporación de sofisticadas técnicas de pretensado –que exigieron reforzar componentes críticos, como las cabezas de tiro ante fuerzas de pretensado de hasta 1.955 toneladas– el proyecto DMC traza una ruta para el prefabricado de hormigón que marca un antes y un después en el sector.
En ese sentido, tanto Gigliola Rivano como Vladimir Urzúa destacan los aspectos más complejos que hubo que abordar para que el diseño original se tradujera en uno que permitiese el uso de prefabricados de hormigón como elementos estructurales principales:
• La transformación del proyecto original in situ a un modelo prefabricado se fundamentó en la búsqueda de eficiencia, ahorro en tiempo y reducción de riesgos en terreno.
• La adaptación en la planta y la integración de tecnologías avanzadas –por ejemplo, la modificación de las pistas de pretensado para trabajar con elementos de más de cuatro metros de ancho– fueron factores cruciales para lograr la materialización del diseño.
• La experiencia acumulada permitió enfrentar y resolver los desafíos técnicos relacionados con la alta concentración de armaduras, la dosificación de hormigones ultra especiales y las complejidades logísticas inherentes a mover piezas que alcanzan las 140 toneladas.
Asimismo, para el ingeniero civil estructural, este proyecto no se trata simplemente de un cambio en los materiales o en la metodología constructiva, sino de una nueva manera de concebir este tipo de obras, pensando en un diseño que sume a esta tecnología constructiva en su fase más temprana de desarrollo.
“Incorporar el prefabricado en la ingeniería básica significa que cada proyecto se diseña desde el inicio pensando en la fabricación en planta. Esto no sólo reduce los tiempos de construcción, sino que mejora en gran medida la calidad y durabilidad de las infraestructuras mineras”, agregó la jefe de Proyectos de Preansa.
La sinergia entre diseño, cálculo de ingeniería y producción en ambiente controlado es el sello distintivo de este avance. La modularidad de las estructuras –que permitió ensamblar componentes mediante uniones húmedas tipo “macho-hembra”, como se evidencia en el marco rígido de la grúa gantry y en la fragmentación de pilares de más de 20 metros de alto– no sólo facilitó el transporte y el montaje, sino que también generó una eficiencia en cuanto a costos y mejoró la seguridad de las operaciones. Se evita, por ejemplo, la necesidad de montar formaciones monolíticas en terreno que implicarían riesgos y tiempos prolongados de ejecución.
Además, el impacto del uso de prefabricados en la economía de las obras se hace tangible cuando se considera que en la planta se puede producir la rotación de moldajes en cuestión de horas. Esto, en contraste con el enorme esfuerzo que representaría realizar el mismo trabajo in situ, se traduce en un mayor control de la calidad del hormigón, en la reducción de posibles variaciones debidas a las inclemencias climáticas y en una mayor predictibilidad en la planificación de obra.
Otro punto de relevancia es el desarrollo y validación de hormigones de alta resistencia. La investigación y los ensayos previos permitieron crear mezclas que garantizan, en el caso del hormigón G70, alcanzar más de 80 MPa a los ocho días, superando con creces las especificaciones originales. Este logro técnico, que fue decisivo para optar por la fabricación en planta, abrió la puerta a realizar estructuras con cuantías de hasta 450 kg/m3, un nivel de armado que exige un control extremadamente riguroso del proceso de curado y del vertido.
En ese aspecto, Rivano destacó que “el manejo de estos hormigones especiales –que utilizan áridos de muy bajo tamaño y conos altos alta calidad y bajos en cloruros– fue un factor clave para que no se generasen fisuras en los elementos ni juntas frías entre vertidos, incluso cuando el llenado de una pieza masiva demoraba hasta seis horas”.
Cada vez más las mineras y las empresas de ingeniería incorporan soluciones modulares en sus proyectos, ya que las ventajas –en términos de tiempos, costos, seguridad y durabilidad– son evidentes. Según comenta la experta de Preansa, las oficinas de Ingeniería consultan y solicitan activamente asesoría en la incorporación de prefabricados en proyectos nuevos, y en algunos casos, hasta forman parte de los bancos de datos de proveedores especializados en este tipo de soluciones.
“Si en la actualidad somos capaces de fabricar estos elementos masivos con tal precisión y rapidez, somos capaces de abordar cualquier proyecto con la certeza de que las barreras tradicionales pueden ser superadas con innovación y compromiso”, subrayó la jefe de Proyectos de Preansa.