Emplazado en la comuna de La Unión, este centro productivo se construyó en 12 meses y consideró 30.000 m2 de pisos y 1.200 m2 losas de gran panel. Uno de los atributos a destacar dice relación con el uso del hormigón de retracción compensada, que permitiría construir pisos sin juntas de hasta 1.600 metros cuadrados.
En 2012 la Cooperativa Lechera de La Unión, Colun, presentó ante el Servicio de Evaluación Ambiental su proyecto de construcción de la Planta Verde Colun que elabora productos a partir de leche fresca de vaca. La obra que se emplaza en la comuna de La Unión, provincia de Ranco, consideró una inversión de US$65 millones.
En el anuncio de la obra, la compañía afirmó que la creación de este inmueble industrial respondía al aumento sostenido en la producción de leche, asociado a la alta demanda de productos lácteos.
Entre los años 2014 y 2015, con la aprobación de la Comisión de Evaluación Ambiental de Los Ríos, se comenzó a construir el proyecto con una superficie de 50 hectáreas, el cual, además, consideró 30.000 m2 de pisos y 1.200 m2 de losas de gran panel (plataformas de grandes tamaños). De acuerdo a sus desarrolladores, el proyecto tendría una vida útil de aproximadamente 50 años y contó con tecnologías para el cuidado y resguardo del medioambiente, como en las zonas de almacenamiento transitorio de residuos peligrosos, como no peligrosos, sistemas de tratamientos de aguas servidas y sistema de residuos industriales líquidos, entre otros.
Desarrollo de ingeniería de pisos
Alfredo Grez, director ejecutivo en Katemu, cuenta que para el desarrollo de la ingeniería de los pisos y pavimentos en un proyecto debe estar bien coordinado, logrando una comunicación entre los distintos proyectistas y la operación, “de esta forma podremos contar con toda la información de las necesidades de la operación como también de los requerimientos de los otros proyectistas. Es por esto que, a través de varios estudios y análisis con el departamento de ingeniería de Colun, se pudo concretar y definir la obra, donde principalmente el foco eran los pisos a utilizar, tanto en la zona de almacenamiento como en la de producción, la que tenían diferentes requerimientos”, explica el ejecutivo.
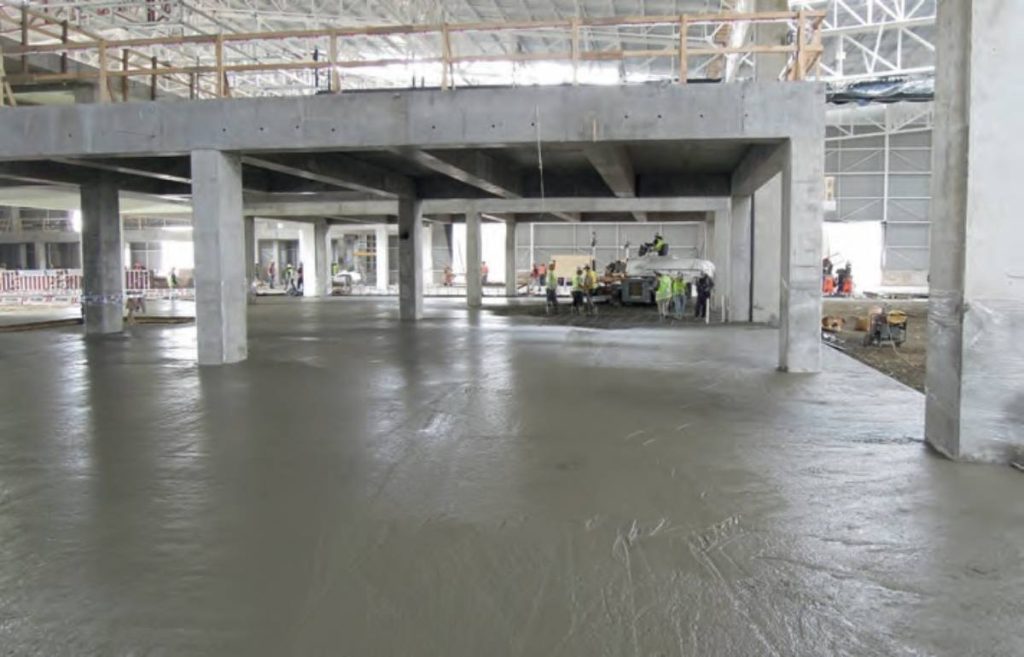
En tanto, Grez cuenta que “en la zona de producción nos enfrentamos a áreas con derrames de líquidos propios del proceso, donde se deben analizar los componentes y así identificar si son corrosivos para el hormigón”. El experto relata que también en esta área se tuvo que aplicar revestimiento de poliuretano para soportar los derrames.
En la zona de almacenamiento, se seleccionaron pisos de retracción compensada, tecnología jointless, con distanciamiento de juntas de hasta 40 metros, 1.600 m2 sin cortes. Los pisos de RC consiguen una alta resistencia a la abrasión y desgaste para soportar el continuo tránsito de grúas y la altura de los rack, los que demandan índices FF y FL=50 / FL=40; es decir, nivelación y planicidad de la superficie.
Desde Melón explican que este material corresponde a un hormigón expansivo que, cuando está debidamente restringido por la armadura u otros medios, va a tener una expansión inicial igual o ligeramente superior a la retracción por secado prevista. Debido a la restricción, durante la etapa de expansión, el hormigón experimentará una cierta pre-compresión, la que luego se irá alivianando durante la etapa de retracción. El resultado esperado es que, en su estado final de equilibrio, el hormigón permanezca con tensión nula o una ligera tensión de compresión residual, la que permitirá separar a gran distancia las juntas o cortes del piso industrial.
Por otro lado, en la zona de producción, se ejecutaron pisos PD3 Baskets, que tienen un sistema de transferencia de carga bajo juntas de construcción, como de las de contracción (o cortes), permitiendo disminuir el escalonamiento entre las juntas y así lograr pisos más durables y eficientes, indican los expertos.
Alfredo Grez, comenta que la ejecución de los pisos de retracción compensada es de extrema complejidad, “ya que por las características y la rigurosidad que se debe tener con el hormigón los tiempos de montaje no son muy extensos, por lo que nos obligó a disponer de mayor cantidad de maquinaria para trabajar más rápido en este proceso, es por esto que tuvimos que incorporar equipos de respaldo backup, los que nos permitió cubrir desperfectos mecánicos del proyecto. Además, para conseguir las ajustadas tolerancias de lisura, tuvimos que incorporar un personal especializado en índices FF y FL, equipos de compactación y máquinas de nivelación laser Somero que permiten cortar el concreto fresco a un nivel acabado, nivelarlo hasta dejarlo plano y hacerlo vibrar para que quede suave en una sola pasada”.
Asimismo, se utilizaron alisadoras mecánicas dobles de 48 pulgadas, máquinas que están hechas para enlucir y acabar concreto en curación, para así dejar los pisos más planos y resistentes al desgaste.
Por otro lado, Grez relata que en esta obra fue vital la coordinación y planificación con la constructora Precon y la hormigonera Melón. “Es por esto que consideramos y coordinamos frecuencias de despacho de 10 minutos como también la aplicación de planes de contingencia en caso de imprevistos, que nos permitió obtener paños comprometidos sin interrupciones, homogeneidad en el hormigón y una adecuada tolerancia en los conos”, relata el experto. U
Pisos industriales
De acuerdo con expertos de Melón, el desarrollo de hormigones especiales para pisos industriales ha sido un gran desafío, pues las nuevas exigencias de los pisos lo han llevado a investigar las diversas tecnologías que se usan en el mundo para aplicarlas en Chile.
En tanto, explican que el futuro de los pisos industriales busca tener superficies de operación que consideren plataformas de grandes tamaños (Pisos de gran panel), con gran capacidad de soporte, resistentes al desgaste, y por sobre todo, con características que reduzcan de forma importante los futuros costos de operación e intervención de las área de trabajo.
También, desde Melón comentan que es importante difundir las nuevas tecnologías presentes en el país y, por sobre todo, dar a conocer las nuevas tendencias en diseño y construcción de pisos industriales, que apuntan a desarrollar pisos más eficientes, con menos costos futuros de mantención. Además, se aconseja entregar información porque les permite a los inversionistas tomar las mejores decisiones en lo que respecta a la sustentabilidad de su proyecto.
Asimismo, recomiendan que cuando se desarrolla un proyecto industrial, es importante ejecutar una reunión interdisciplinaria entre el mandante, el arquitecto, los proyectistas, el operador, la constructora y los proveedores, con la finalidad de esclarecer las expectativas futuras de operación del proyecto. “Teniendo claridad del uso de la bodega, el servicio de los pisos, las cargas a las cuales estarán expuestas, el método de bodegaje, el tipo de equipos móviles que circularán al interior y la durabilidad del proyecto, recién se tendrían los antecedentes necesarios para construir un piso de calidad que asegure la inversión y sustentabilidad del proyecto”, finalizan.