El proyecto también destaca por la aplicación de un sistema de protección sísmica que implicó el desarrollo de columnas prefabricadas híbridas en hormigón armado y postensado.
La Forestal Papelera Concepción, FPC, con el objetivo de expandir su producción, en 2013 invirtió US$150 millones para construir en Coronel una nueva nave industrial destinada a la fabricación de papeles y productos tissue. Parte importante de esa inversión estuvo destinada a la construcción de los edificios que albergaron los equipos de producción y zonas de almacenaje. Se trata de aproximadamente 40.000 m2 de construcción prefabricada para uso industrial, con una altura de 18,5 metros, más un sector con subterráneo de 6 metros de profundidad, con puentes grúa de 40 y 10 toneladas.
Para el desarrollo de los elementos prefabricados, desde Tensocret se propuso la implementación de una planta móvil en coronel para la fabricación de la estructura. La propuesta comprendió la prefabricación del 20% de la estructura con elementos fabricados en la planta de Santiago y el 80% de los elementos fabricados en Coronel. “Optamos por una alternativa a la logística (Santiago a Coronel) de los materiales que fue montar esta planta móvil para fabricar los elementos de mayor peso ahí, con lo cual nos evitábamos todo el costo extra del transporte”, afirmó Diego Mellado.
En cuanto a los elementos constructivos que contiene cada estructura, Mellado explicó que el edificio de máquinas, que se divide en cuatro sectores (M1, M2, M3A y M3B), está constituido por nudos rígidos hormigonados in situ, pilares de hormigón armado de 26 metros (59 toneladas) y vigas pretensadas con una luz de 26 metros. En tanto, el edificio conversión se constituye en dos sectores: bobinas y conversión, este también está construido en base de nudos rígidos hormigonados in situ, con pilares de hormigón armado de 15 metros y vigas pretensadas con una luz de 30 metros.
Sistema sísmico
Patricio Bonelli, ingeniero estructural, explicó que las plantas industriales de hormigón armado generalmente están estructuradas con pilares prefabricados que reciben vigas prefabricadas de gran luz. Ha sido tradicional diseñar la unión de la viga con la columna como una rótula, recibiendo la viga en una consola. Ese tipo de estructura, en general, ha trabajado bien, más allá de algunas fallas en la unión viga columna que se presentaron en una estructura tras un terremoto en Turquía en 1999.
Por otra parte, su flexibilidad hace que los desplazamientos laterales sean importantes, complejizando el diseño de las uniones de los elementos no estructurales de fachada. “En Chile algunas empresas han optado por una unión húmeda en el extremo superior de la columna transformando el sistema de columnas en voladizo en marcos, que son más rígidos y con mejor desempeño y seguridad al colapso”, señaló Bonelli.
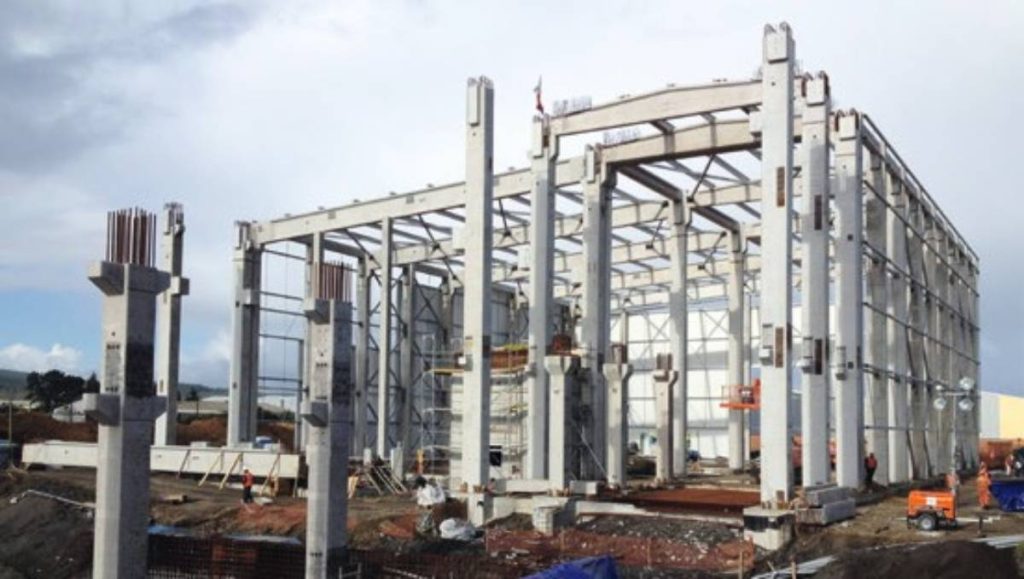
Asimismo, el experto afirmó que uno de los principales desafíos relacionados con los sistemas prefabricados, tienen que ver con el diseño de las uniones. La norma NCh2369 que se aplica a edificios industriales, da una serie de recomendaciones para el diseño de este tipo de estructuras, especialmente para sus uniones. En general, se intenta que la unión trabaje sin daños, es decir, dentro del rango elástico de respuesta, diseñando los elementos de manera que el daño ocurra en zonas alejadas de la unión, en sectores denominados como secciones críticas.
La planta de papel tissue de FPC está ubicada en un sector clasificado como zona 3, que corresponde a la de más alta intensidad sísmica del país. Por definición, en este tipo de proyectos es deseable que la estructura no colapse y que el nivel de daños sea el mínimo posible, de modo de permitir la continuidad de la operación de la fábrica y proteger su contenido, que puede tener un costo significativamente mayor al del edificio. De esta manera, daños y deformaciones permanentes después de un sismo son indeseables.
Para proteger la unión viga-columna que tenía el sistema y evitar el daño en las vigas que eran pretensadas y de gran luz, se decidió innovar en el diseño de las estructuras e incorporar un sistema de “marcos prefabricados híbridos”, de alto desempeño sísmico, que consiste en diseñar secciones que se pueden abrir sin dañar el resto. Estas secciones reemplazan a las clásicas rótulas plásticas, que corresponden a zonas donde se espera daño ante el sismo de diseño. Este sistema utiliza dos tipos de armaduras actuando simultáneamente; primero cables de postensado no adherido de acero de alta resistencia, que tienen como misión cerrar la sección una vez abierta y otorgar un comportamiento no lineal elástico y, opcionalmente, “armaduras especiales”, que son barras corrugadas con una zona no adherida usadas para disipar energía y dar resistencia al deslizamiento.
Se espera que este sistema después de un sismo importante, en lugar de observar un agrietamiento intenso y deformaciones residuales, se obtenga un mecanismo autocentrante, capaz de deformarse, disipar energía y de rotar, que genere una fuerza interna que obligue a que la unión vuelva a su posición original y que las aperturas se cierren. En definitiva, una estructura capaz de soportar movimientos sísmicos severos, que ante grandes desplazamientos solamente se abran las secciones críticas quedando el resto de la estructura sin daños y muy baja deformación residual. “Este sistema para diseño de estructuras prefabricadas de hormigón de alto desempeño está basado en una larga investigación desarrollada por el programa PRESSS en EE.UU. y actualmente está regido por ACI T1.2, el código de diseño ACI 318-11 y aceptado por IBC (International Building Code)”, destacó Bonelli.
En este proyecto se usó el sistema de uniones híbridas en la base y cerca del coronamiento de las columnas. Es por esto que desde Tensocret afirmaron que esta solución consistió en diseñar columnas de manera que, ante un gran desplazamiento lateral, estás se abrieran y se cerraran tras un sismo, haciendo que el resto de la estructura pudiera seguir en movimiento sin daño alguno. “El sistema consiste en poner en el interior de las columnas cables postensados desprovistos de adherencia con una fuerza restituida capaz de cerrar las uniones después del sismo sin dejar deformaciones remanentes. De esta manera, se abrirían solamente esos sectores protegiendo el resto de la estructura, especialmente las uniones”.
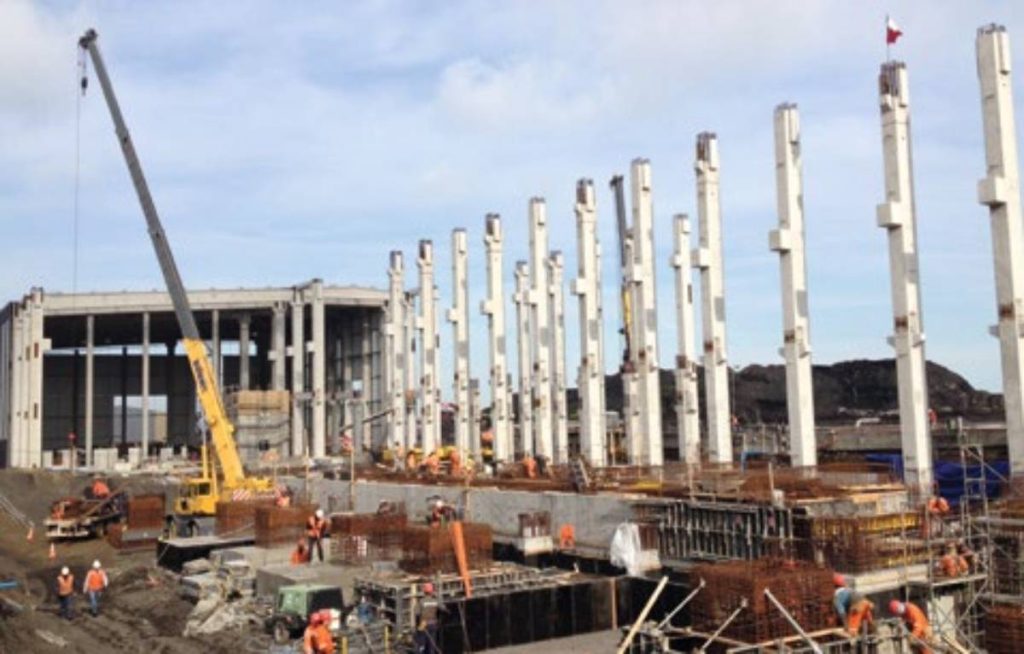
Asimismo, explicaron que los marcos rígidos tienen una característica bien importante en el sentido de que tanto la unión superior en que se unen la columna con la viga, como la unión inferior donde se une la columna con la fundación, son las partes claves del comportamiento como marco regulatorio.
Análisis de la estructura con uniones híbridas
Para evaluar el nivel de daño del proyecto con y sin uniones híbridas, se realizaron simulaciones numéricas no lineales de los pórticos. Los análisis se hicieron con el programa Ruaumoko 2D (Carr, 1982). Los cables postensados y las barras de acero dúctil (disipadores) de la unión híbrida, se incluyeron en el análisis con resortes rotacionales en paralelo, siguiendo las leyes histeréticas y los modelos físico-conceptuales.
Las leyes histeréticas, corresponden a una ley bilineal inelástica para el acero dúctil y una ley bilineal elástica para los cables postensados. Muestran los valores de los parámetros utilizados, donde k0 es la rigidez rotacional elástica, “r” es la razón entre la rigidez rotacional post-fluencia y la rigidez rotacional elástica, y M (el momento flector de fluencia). Para su determinación, se siguieron las recomendaciones propuestas por Celik y Sritharan (2004).
Como evaluación preliminar de la estrategia de modelación, se realizó un análisis incremental en dos sentidos (push-pull), aplicando una historia de desplazamientos en el techo.
El resultado preliminar, confirmó que el modelo es capaz de representar la respuesta de tipo bandera, que caracteriza a estas uniones. De esta forma, es posible realizar análisis tiempo-historia más detallados, utilizando acelerogramas que se consideran representativos de las condiciones locales sísmicas.
Análisis de la estructura original sin uniones híbridas
Para poder comparar el daño estructural y evaluar la efectividad de la solución propuesta, también fue necesario modelar y analizar la estructura original sin uniones híbridas.
Esto se realizó con el programa Ruaumoko 2D, a través de un análisis dinámico no lineal (Thiers, 2014). De esta forma, se consideraron las tres columnas, la viga de inercia variable y la viga de inercia constante.
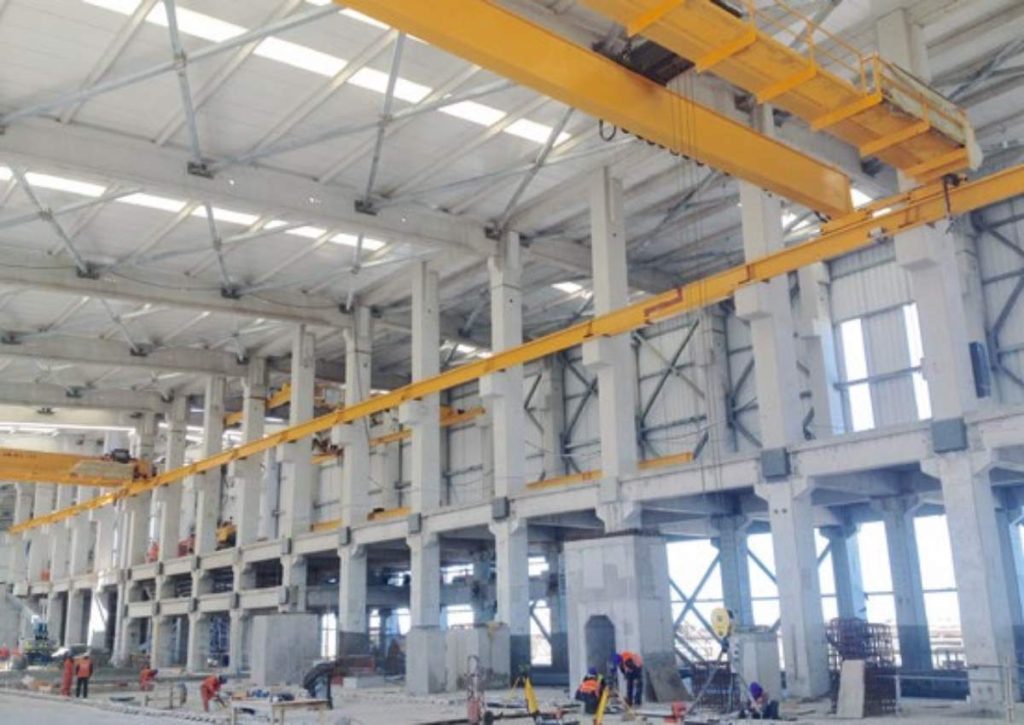
Para modelar la no linealidad de la estructura se asumió que las secciones críticas están en los extremos de los elementos y que el nudo tiene la resistencia suficiente para permitir que las secciones críticas fluyan antes de que el nudo falle. Para las vigas y las columnas se utilizaron elementos de plasticidad concentrada en sus extremos, del tipo Giberson (Sharpe, 1974), donde las rotaciones se concentran en los extremos del elemento.
La rigidez del resorte rotacional, se determina a partir de la rigidez tangente, correspondiente al nivel de deformación de la ley de histéresis considerada. En este caso se utilizó la ley de histéresis de Clough (1966), que corresponde a la ley de Takeda modificada, con parámetros a y b igual a cero. Como los elementos de hormigón armado tienen baja rigidez post fluencia, se utilizó un valor de “r” igual a 1 por ciento.
Resultados del modelo sin uniones híbridas
Los resultados demostraron desplazamientos en el techo del pórtico sin uniones híbridas que alcanzaron los 37 centímetros. Bonelli explicó que “este nivel desplazamientos es importante, ya que está asociado a la presencia de daños en las uniones y posibles fallas frágiles no localizadas por el método de diseño basado en fuerzas”. Además, se deben tomar precauciones en los elementos que se unen a la nave en la dirección transversal, para poder sostener este nivel de deformaciones. De manera complementaria, se observó la presencia de desplazamientos remanentes del orden de los tres centímetros.
Asimismo, mostró una fuerte incursión en el rango no lineal, con daños importantes en los pilares prefabricados sin uniones híbridas. Las máximas curvaturas alcanzadas fueron del orden de 0.0324m-1, por lo tanto, se debe confinar adecuadamente, dotar de ductilidad y reforzar los nudos.
También, se mostraron las secciones más solicitadas y un posible mecanismo de colapso del pórtico. A partir de estos resultados se recomienda proveer confinamiento en los nudos y en las secciones de los elementos donde se espera que se produzcan rotulas plásticas. Además, se debe detallar el refuerzo para evitar fallas frágiles e intentar localizar el daño en una sección critica preestablecido.
Los análisis de un diseño tradicional indican que se espera daño en las secciones críticas, con alargamientos unitarios en el acero de hasta un cuatro por ciento.
Resultados del modelo con uniones híbridas
El tipo de daño esperado sugirió la necesidad de controlar sus efectos y limitar los desplazamientos remanentes en la estructura. De esta forma, un sistema de uniones híbridas en los pilares prefabricados surgió como una estrategia adecuada para lograr estos objetivos. Se observó que la estructura alcanzaría desplazamientos en el techo del orden de 40 cm, levemente mayores que la estructura tradicional. Sin embargo, no habría daño estructural asociado y la estructura recuperaría su posición original sin deformaciones remanentes, reflejando las ventajas del sistema propuesto. Esto es posible ya que el resto de los elementos estructurales se diseñaron por capacidad, para asegurar la formación del mecanismo de colapso deseado.
Para la instalación de moldes se realizó un banco de pretensados para poder desarrollar vigas de 30 metros de luz que tuvo una profundidad de 2 metros y medio para poder tensar y hacer la pieza.
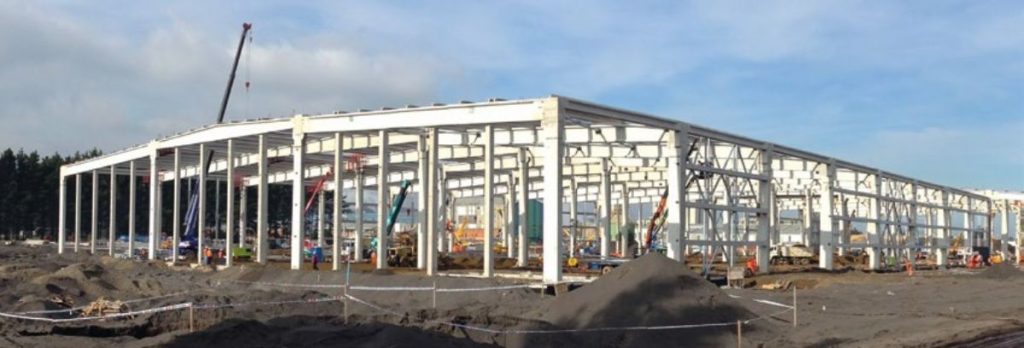
Asimismo, las vigas prefabricadas no incursionaron en el rango no lineal, permaneciendo elásticas durante el sismo. Sin embargo, deben poseer una resistencia adecuada para que la no linealidad se concentre en las secciones críticas diseñadas como una unión híbrida en las columnas.
Características técnicas
La planta se fundó sobre arena, por lo que el procedimiento del movimiento de tierra consintió en removerla para lograr los niveles solicitados por el proyecto y luego volver a colocar la arena, pero de manera compactada con procedimientos mecánicos e hidráulicos. “Esto fue un procedimiento bien importante tomando en consideración la profundidad de la roca basal. Sin embargo, es ideal para fundar siempre que hayas hecho un buen estudio de suelo que no va haber licuefacción y empleando los procedimientos adecuados para la compactación y confinamiento que te da una estabilidad”, explicaron desde Tensocret.
Se empleó una fundación normal estructural prefabricada que consiste en una zapata y en un vaso de fundación que recibe la columna dentro de este vaso de fundación, donde se aplica grouting de empotramiento que permitió la unión de la columna con la fundación (unión rígida de la base del marco). “Como también cuando se une el pilar con la viga se produce una segunda unión rígida que se materializa con armaduras que vienen expuestas a la vista por parte de la columna y por la viga el nudo. Por eso se llaman nudos agudos o rígidos porque se concretan en terreno”, detallaron.
Asimismo, para la instalación de moldes se realizó un banco de pretensados para poder desarrollar vigas de 30 metros de luz que tuvo una profundidad de 2 metros y medio para poder tensar y hacer la pieza. “El banco de pretensado nos permitía hacer una viga de inercia constante decir que tiene una altura común a todo lo largo de la viga y la otra viga es de una inercia variable donde varia su da las dos aguas del techo de 90 metros de ancho”, destacaron.
“Para lograr el efecto que se quiere cuando se está prefabricando en los pilares hay una secuencia de nueve pasos que tienen que ver con cortar los cables de postensados a un cierto largo, después limpiar y sacar el recubrimiento del cable, luego limpiarles la grasa ya que sujetan el cable postensado. Prontamente, se debe ubicar el cable postensado en el eje del pilar, después se hace la colocación de los anclajes en la cabeza de la pieza y los anillos de acero en las secciones críticas y finalmente, comienza el hormigonado y todo lo que tiene que ver con el postensado de los cables que se van haciendo uno a uno de forma controlada para confirmar la tención manométrica y de esa manera ya se obtiene la pieza para ser trasladada a la obra y ser montada”, finalizaron.