Con una drástica reducción de juntas, esta tecnología -que viene utilizándose en Chile durante los últimos años- asegura la construcción de pisos industriales de calidad, acorde a las exigencias que demandan los nuevos centros logísticos de distribución. En el siguiente artículo, se analiza un caso de éxito en el que se utilizó el hormigón de retracción compensada.
La tecnología de los hormigones de retracción compensada para pisos y pavimentos no es nueva en el mundo, pero sí en su aplicación constructiva en Chile. Este tipo de pisos tienen un 90% menos de juntas si se comparan con los pisos industriales convencionales; no se produce alabeo, se logran con ellos mayores resistencias al desgaste y durabilidad.
Esta tecnología ofrece una solución más eficiente para industrias donde la distribución es una variable crítica en su negocio, intensivas en tráfico de montacargas y bodegaje en altura, como el retail. Estas son las ventajas que necesitan los modernos centros de distribución para lograr una operación más eficiente. Esto le ha permitido a la empresa proveedora el llevar a cabo importantes proyectos en el ámbito industrial, en donde se han corroborado todos sus beneficios.
Una de las últimas experiencias constructivas con esta técnica, fue la desarrollada en el Centro de Distribución Lo Aguirre de la empresa de retail Walmart en el año 2011, el que, según la misma firma, pretende convertirse en uno de los centros de distribución más modernos de Sudamérica.
Ubicado en la comuna de Pudahuel, cuenta con 58.000 m2 y su principal característica es la instalación de un sorter automático que por sí solo alcanza una producción máxima de 250.000 cajas por día. Este gran avance tecnológico en la operación pudo llevarse a la práctica por un sin número de innovaciones incorporadas en los procesos de diseño, construcción y montaje, y una de las más importantes, es la calidad de los pisos, tanto en su terminación superficial de planeidad y aporte al ahorro de iluminación, cómo en su disminución en las juntas en más de un 90%.
La visión del contratista
La empresa Katemu fue la encargada de construir y diseñar el piso súper plano de más de 50.000 m2 de esta obra industrial, utilizando la tecnología de retracción compensada, situación que la llevó a recibir el récord por haber elaborado el pavimento con esta tecnología más grande de Latinoamérica.
Este sistema, según explicó Alfredo Grez, actual director ejecutivo en Katemu, permite contar con pisos ultra planos y extra resistentes, sin alabeo, con un 30% más de resistencia a la abrasión y lo más destacable es que se logran separaciones entre juntas de hasta 40 m (1.600 m2), en donde los cortes no son necesarios, reduciendo los costos de mantención de las juntas, grúas, reposición de ruedas de los vehículos que transitan sobre él, y manejo de las grúas en forma más fluida, brindando una operación del Centro de Distribución mucho más eficiente.
El tiempo de construcción de los pisos es menor a los convencionales, ya que las faenas y terminaciones son más reducidas logrando terminar las labores antes de las 20 hrs, lo que evita la paralización de obras por ruidos molestos, y posee una superficie reflectante, muy importante para la mantención de la limpieza de la obra y por un efecto de ahorro energético al necesitar menos iluminación.
Para poder implementar la tecnología de retracción compensada, Katemu no sólo contó con la asesoría técnica de la empresa norteamericana The Fricks Company, sino que también trabajó en conjunto con la empresa Pétreos, quienes les permitieron cubrir la demanda de materiales necesarios y alcanzar la gradación de áridos apropiada para poder construir con éxito el piso industrial de Walmart.
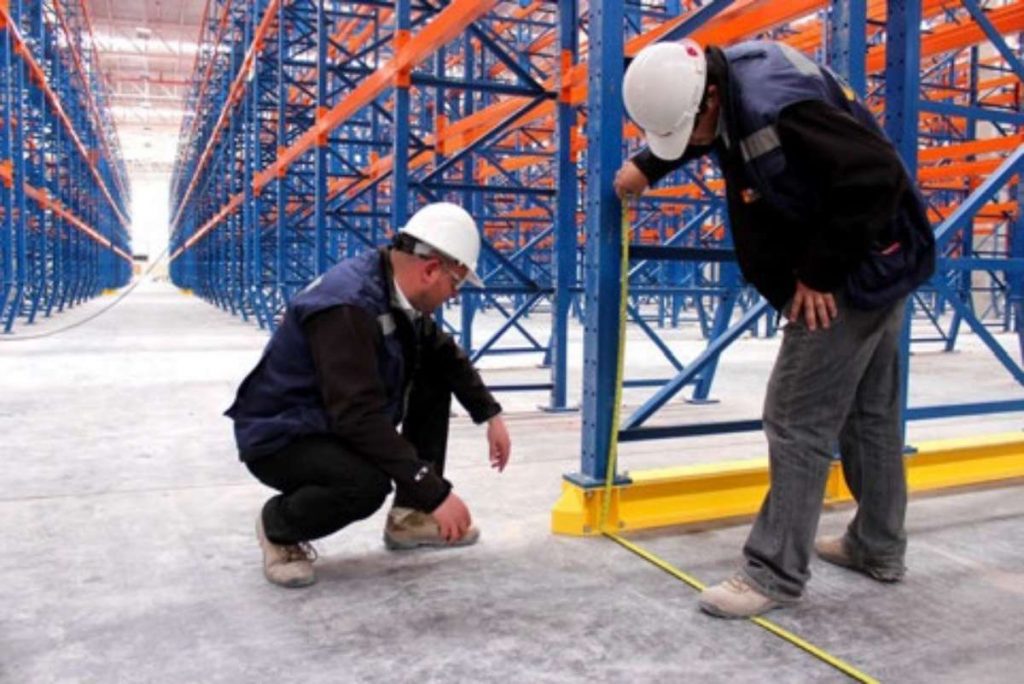
“El programa original tenía planificado terminar el piso en tres meses, pero con este sistema lo finalizamos en menos de un mes y medio. Esto se pudo lograr, ya que pudimos programar en 12 minutos la frecuencia de entrega de los mixers, lo que nos ayudó a acelerar el proceso y cumplir con éxito nuestra meta”, aseguró Grez.
Antes de comenzar el proceso de construcción, el co-fundador de Katemu destacó que fue necesario tener en consideración el clima y la zona en donde se construirá el piso industrial.
“En el tema de la retracción compensada nosotros diseñamos la dosificación apropiada para los áridos, aditivos y cemento con que dispone la planta hormigonera elegida, es decir, el diseño de mezcla que se utilizará en Santiago no va a ser la misma que se manipulará en una planta en Antofagasta, porque los áridos son totalmente distintos y podríamos posiblemente contar con otro tipo de cemento. Todos estos detalles son muy importantes, dado que esta tecnología requiere de una rigurosa especificación, sin tolerancias y con un estricto control de calidad”, dijo.
Una de las ventajas más importantes del sistema constructivo es que disminuye hasta un 95% las juntas, logrando un importante ahorro en costos de mantención de los pisos y de equipos montacargas. Para cumplir cabalmente con esta cifra, esta tecnología requiere que el hormigón sea reforzado en ambas direcciones debido a que, al momento de expandirse y contraerse, la masa de cemento deja en tensión el refuerzo, dejando el hormigón en compresión (proceso similar al postensado interno), lo que impide la formación de grietas en el piso.
En particular para el proyecto de Walmart se logró más de un 90% menos de juntas, que con un hormigón tradicional. “Las cifras hablan por sí solas, pues con el hormigón convencional lo más probable es que el piso hubiese quedado en 36.700 m lineales de juntas, mientras que con el de retracción compensada se obtuvieron tan solo 3.300 m lineales”, sostuvo Grez.
Además, en este proyecto se implementó la protección de las juntas de construcción con un elemento llamado “Armor-Edge”, el cual aumenta aún más la durabilidad del piso. Este refuerzo de juntas queda embebido en el hormigón, colocado en conjunto con barras de traspaso del tipo “Diamond Dowels”, consiguiendo distribuir las cargas efectuadas por las ruedas de los montacargas, así como el proteger el borde de las losas, evitando el desconchamiento de éstas.
Para lograr el proceso de nivelación del hormigón en este piso, se utilizaron equipos láser de última generación. Para la terminación superficial, es importante ocupar máquinas de alisado mecánico de pavimentos, comúnmente llamados “helicópteros” del tipo doble, dado que son más pesados, por lo que la carga y la fricción que tienen sobre el hormigón es mayor. Con esto, se busca una mayor lisura y, a la vez, se está disminuyendo la relación agua/cemento de la capa superficial de hasta 3 milímetros, haciendo que esa zona sea más resistente a la abrasión.
La visión de la hormigonera
Tomando como partida la información referente al ambiente de colocación, consistencia, resistencia, y tamaño máximo de los áridos en un hormigón de retracción compensada, la empresa Pétreos procedió a ejecutar el diseño de la mezcla, necesarios para construir el piso industrial más moderno del país y de Latinoamérica.
Una particularidad del diseño del hormigón entregado por The Fricks Company – Katemu, es que no permite holguras, debido a que la mezcla debe ser homogénea para contar con la calidad que se espera y ejecutar esta técnica constructiva apropiadamente.
Por ello, el actual jefe de Innovación y Desarrollo del Grupo Polpaico, Pablo Castro, afirmó en la ocasión que “si bien el desafío fue el diseño propiamente tal, nuestras plantas tienen un sistema de control automático y un aseguramiento de calidad que permite controlar el proceso, y cumplir con los estándares normalizados, respetando las tolerancias establecidas. Además, agregamos algunas inspecciones adicionales producto de esta experiencia, pero sólo para tener mayores antecedentes. Todo fue suficiente para tener el control y garantizar la homogeneidad del hormigón”.
Sin embargo, el profesional agregó que, si bien no hubo mayor complejidad en la provisión de la mezcla requerida, la dificultad central del proyecto se dio en dos ámbitos: la calidad del producto y en su exigida logística. Sobre el primero, se desarrolló un hormigón con características muy específicas atendiendo al diseño provisto por Katemu, ya que dentro del producto se consideraron elementos especiales, materias primas que en su justa proporción nos entregó las respuestas que el contratista y el mandante esperaban.
Y en relación a la logística, “un hormigón con estas particularidades obliga a un avance mayor en la obra, por tanto, se requería de una capacidad de distribución muy exigida, la cual llevo a estudiar muy acuciosamente las rutas propicias para abastecer desde una planta principal y una secundaria de apoyo, y así mantener un flujo continuo en la obra, logrando las descargas en los tiempos requeridos por el mandante”, enfatizó Castro.
Además, agregó que “fue un desafío, porque había que acondicionar la entrega de la planta para soportar la frecuencia de abastecimiento. Lo anterior ratifica la importancia de contar con los equipos necesarios para producir rápidamente el material y garantizando que el hormigón cumpla con las docilidades especialmente ajustadas para este tipo de requerimientos. Dado que la tecnología constructiva permite trabajar con hormigones de alta docilidad, se ajustó el diseño de ésta, apuntando a conseguir un hormigón bombeable, el cual permite disminuir los tiempos de descarga y obtener un mayor rendimiento en la confección de los pavimentos”.