Aunque utilizado principalmente para grandes presas, este hormigón posee una gran versatilidad, lo que permite aplicarlo en obras de diversa índole, manteniendo sus ventajas: ahorro en tiempo y transporte, entre otros aspectos positivos del hormigón compactado con rodillo.
El HCR nace como una alternativa para la construcción de presas, con un primer antecedente en la reparación de estructuras que se hacían hacia fines de los 70, como respuesta a los problemas de fisuración del hormigón tradicional que se producían a causa de las elevadas temperaturas que provoca la hidratación del cemento. Luego, este método constructivo se fue perfeccionando para ser aplicado en presas de tipo gravitacionales, donde la primera experiencia concreta fue la presa de Willow Creek, construida en 1982 en Oregon, EEUU, luego de lo cual se expande rápidamente al mundo.
La tecnología ingresa a Chile con la presa Pangue, en los años 90, lo que significó un hito en la historia del HCR, constituyéndose en su tiempo en la más alta del mundo -121 metros de altura- construida en base a esta tecnología. La segunda obra relevante en el país construida con esta técnica de hormigón correspondió a la presa Ralco -terminada en el año 2002- con un volumen total de HCR de 1,5 millones de metros cúbicos y una altura de 155 metros.
Tecnología y aplicación
“El HCR es un hormigón muy seco, sin asentamiento de cono, transportado y colocado con equipos comúnmente utilizados para el movimiento de tierra, que finalmente es compactado mediante el uso de rodillos vibratorios. Todo lo cual permite una rápida ejecución de las presas, reduciendo el tiempo de construcción y los costos con respecto al hormigón tradicional”, explicó Luis Uribe, actual director del Comité de Túneles y Espacios Subterráneos de Chile (CTES) y ex ingeniero especialista en HCR de la empresa de ingeniería INGENDESA, la que participó en la construcción de las presas Pangue y Ralco.
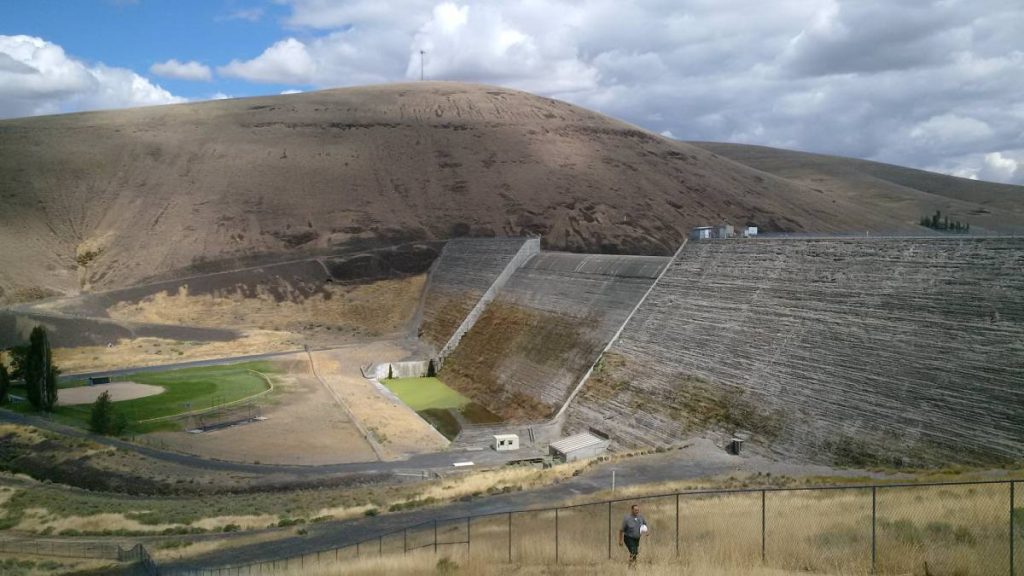
En términos de aplicación, la experiencia señala que lo mejor es hacerlo en capas de 30 centímetros de espesor final, es decir, de 36 cm. de material suelto para luego compactarlas con rodillos vibratorios, generalmente de doble tambor sobre 10 toneladas. De esta forma, una parte del control de calidad se hace en función de la compactación y de su grado de densidad.
“En las presas de HCR -explicó Uribe- exigimos una densidad mínima del 98,5% como grado de compactación para las capas de la presa, lo que asegura una buena resistencia e impermeabilización y se alcanzan las cualidades que exige el diseño, eminentemente relacionadas con resistencia a tracción del hormigón”.
Para trabajar las juntas entre capas se realiza una limpieza, para lo que se utiliza agua y aire a presión como en un hormigón tradicional, para obtener una buena pega y algo de resistencia a la tracción.
En proyectos de sismicidad moderada sólo basta con aplicar mortero de junta en tramos cortos junto a la cara aguas arriba -con un espesor de entre 0,5 y 1 centímetro- con el fin de asegurar la impermeabilidad.
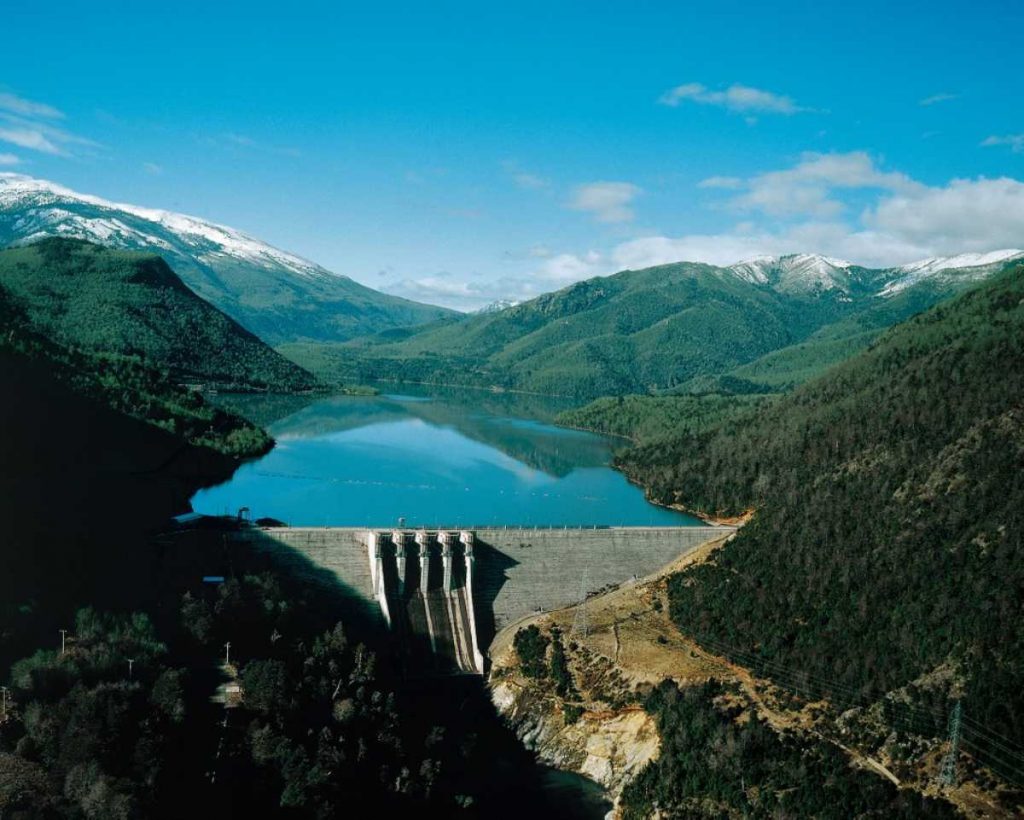
Sin embargo, en proyectos ubicados en sectores de alta sismicidad -como es el caso de Pangue y Ralco- se debe aplicar un mortero en toda la superficie de la junta, lo que permite una mejor colocación y asegura la resistencia a la tracción. En un principio, en Pangue, se utilizó un hormigón de junta con gravilla, pero luego se cambió a mortero de junta para Ralco, con lo cual se obtuvieron mejores resultados. Este mortero también cumple la función de disminuir los problemas de segregación del HCR que se concentran en la zona inferior de las capas de hormigón colocadas.
¿Por qué usar HCR?
El HCR destaca porque al colocarse muy seco, se puede disminuir el cemento y reemplazar un importante porcentade de éste por puzolana u otro tipo de adiciones (fyerach) o un filler inerte. Esto abarata la mezcla y produce una disminución importante en la generación del calor de hidratación del hormigón, mejorando el control de las fisuras en la estructura.
Ahora, en relación a la reducción de los plazos de ejecución, esto se logra por la utilización de equipos pesados para el transporte, colocación y compactación del HCR, lo que disminuye tanto los tiempos como también la mano de obra requerida.
Por otra parte, las presas de HCR se consideran en proyectos hidroeléctricos porque permiten simplificar las obras de desviación de los ríos intervenidos, con el consiguiente ahorro en los costos y en los tiempos de construcción de los proyectos. “Lo anterior se debe a que este tipo de presas permite soportar crecidas que viertan por sobre la estructura durante la etapa de construcción, sin que se generen daños y permitiendo retomar las faenas muy rápidamente, tal como ocurrió en el caso de Ralco”, explicó Uribe.
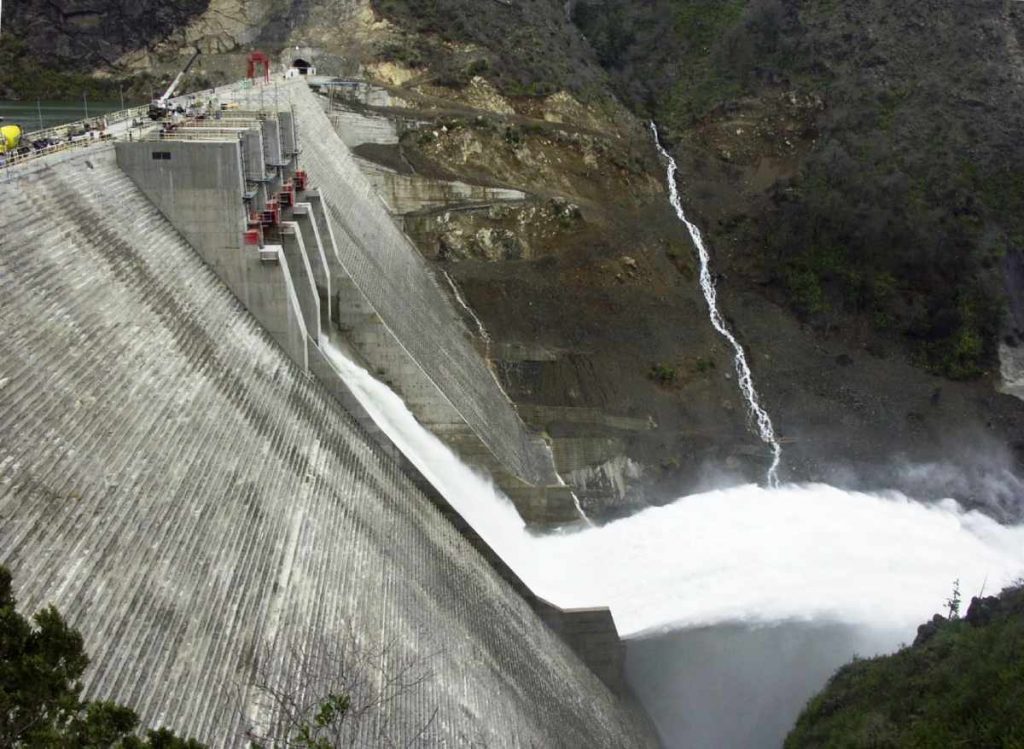
“El HCR se dosifica y mezcla de la misma forma que un hormigón convencional pero con muy poca agua, entregando una apariencia de gravas húmedas durante el transporte, descarga y compactación. Se transporta, coloca y compacta con técnicas asociadas a los terraplenes, con lo que se logran rendimientos propios de los movimientos de tierra, con dosis de cemento muy bajas, donde las mezclas alcanzan densidades mayores a las de un hormigón vibrado tradicionalmente”, explicó por su parte Luis Pinilla, ex director y secretario del Comité Ejecutivo del Instituto de la Construcción.
Mitos y verdades
En Chile, la experiencia con las presas Pangue y Ralco (ambas construidas con HCR), sumada a los avances en el resto del mundo, han permitido concluir, por ejemplo, que el porcentaje de reducción del costo disminuye al aumentar el volumen de la presa; además, que todas las mezcladoras de hormigón tradicional sirven para fabricarlo, incluso las pequeñas betoneras, propias de pequeñas faenas, y las mezcladoras y los camiones revolvedores.
Junto con esto, la mezcla se puede transportar en cualquier equipo de transporte de tierra, como pequeñas volquetas, camiones tolva, cintas transportadoras, cargadores frontales y canoas, entre otros. Mientras que se puede compactar con equipos de cualquier tamaño, como las placas vibratorias, los pisones manuales y los rodillos manuales y vibratorios lisos de gran tamaño, explicó Pinilla.
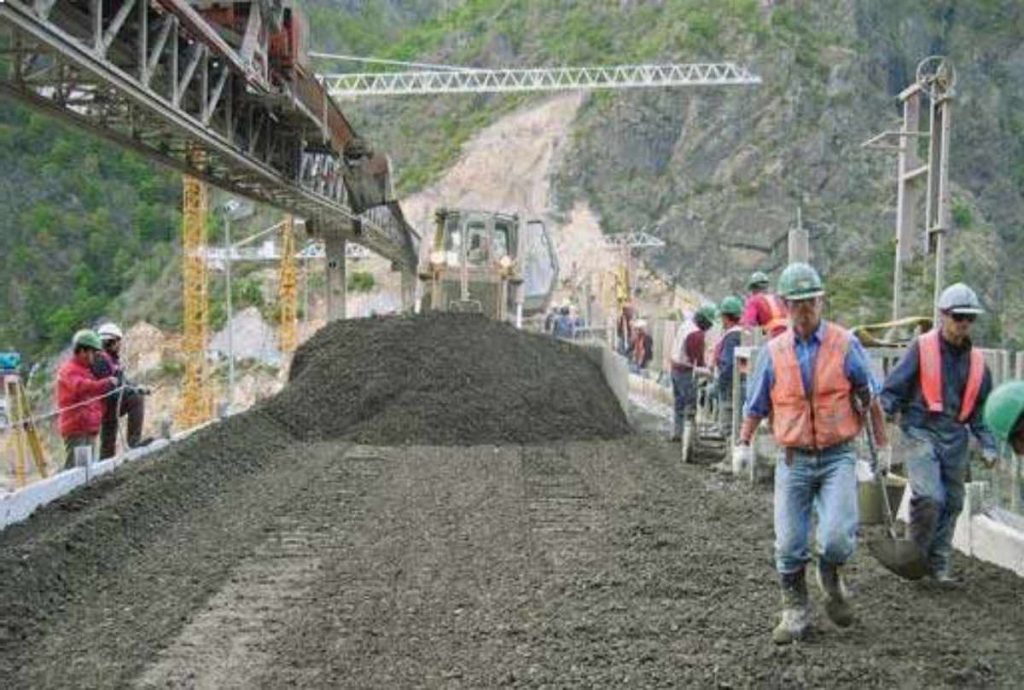
Ahora, en relación a la trabajabilidad y las densidades del HCR, éstas se pueden controlar con equipos de laboratorio especiales de bajo costo, para grandes masas; y con los mismos equipos de control de densidades de los terraplenes para obras pequeñas.
Otras aplicaciones
El HCR ha visto su mayor desarrollo en la construcción de presas, sin embargo, es completamente extrapolable a otra serie de obras, donde hace gala de sus principales beneficios: reducción de plazo y costos.
A juicio de Pinilla, “en toda obra de hormigón sin armar se puede emplear HCR con ventajas importantes”. Ejemplos de esto, comentó el especialista, lo constituyen pruebas en construcciones de muro de contención de suelos, donde en un sector de unos 75 metros de largo, de un camino que se construyó en la ladera de un cerro, se requirió de un terraplén apoyado en un muro de sostenimiento.
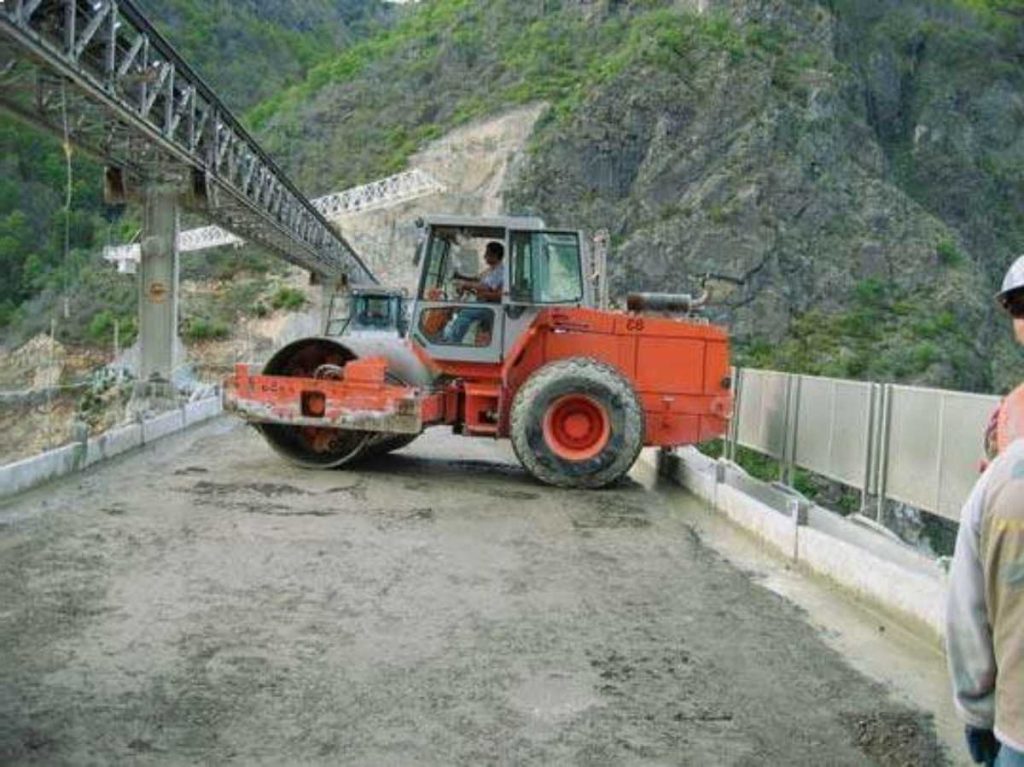
Para esto, se compararon dos sistemas: uno de ellos en base a un diseño de muro tipo cantilever en hormigón armado. El otro, un muro gravitacional empleando hormigón rodillado. El muro de HCR se ejecuta en forma simultánea, se compacta el HCR y el terraplén en la misma capa horizontal con los mismos equipos de compactación y accesos para el terraplén. El resultado: los moldes para el HCR resultan más livianos y se requieren sólo en una cara. Pero lo más significativo, con este sistema se termina el muro y el terraplén al mismo tiempo, reduciendo de 55 a 28 días el plazo de construcción del conjunto, con una significativa reducción de los costos finales.
Otra experiencia interesante ha sido la aplicación de HCR para protecciones de desbordes de presas, como una solución frente a la necesidad de ampliar la capacidad de los vertederos. De esta forma, su aplicación ha permitido actualizar la utilización de vertederos escalonados -muy empleados hasta la primera parte del siglo XX- los que se compatibilizan con los métodos de colocación y los moldes que se emplean para la construcción de HCR. Para caudales no muy elevados, es posible disipar hasta un 85% de la energía, generando una reducción importante de las obras de protección o de disipación aguas abajo.
Con lo expuesto, Pinilla buscó desvirtuar que el HCR sólo es ventajoso en las presas, porque mientras menor volumen presenta una obra de hormigón, mayores so las ventajas del HCR en plazos y costos. Esto, porque se pueden usar los mismos equipos que para fabricar hormigón estándar o dimensionado para obras pequeñas. Asimismo, para el transporte se pueden ocupar desde carretillas a grandes camiones tolvas.
Pavimentos de HCR
En Chile, se han hecho algunas pruebas en superficies para la industria forestal, donde se han pavimentado extensas zonas con hormigón rodillado, con la ventaja que es posible entrar en servicio de inmediato, con rápida colocación y buena resistencia al trabajo de los cargadores.
También se ha considerado para la construcción de caminos complejos para el acceso en zonas de bosques, donde las forestales necesitan entrar con sus camiones y maquinaria. Además de túneles para tuberías y acueductos. De esta forma, la experiencia indica el HCR puede ser una buena metodología de pavimentación provisorio, rápida y de bajo costo.
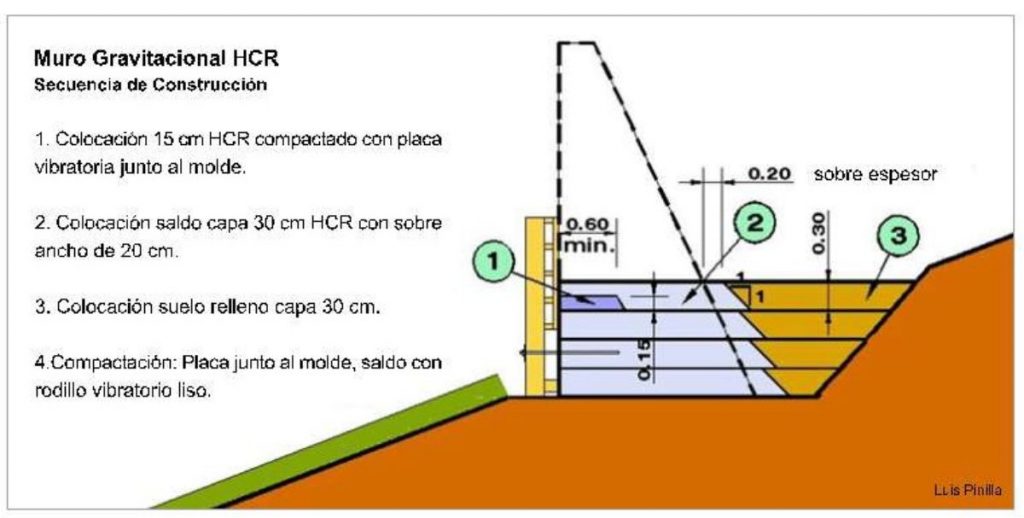
“El HCR -explicó Pinilla- se justifica y cuenta con gran aplicación en pavimentos industriales para usos especiales, como los que deben resistir la circulación de maquinaria pesada. Por ejemplo, en Estados Unidos, gran parte del transporte de carga se hace en ferrocarriles usando contenedores. En las estaciones intermodales se ocupan portacontenedores con grandes neumáticos y cargas concentradas. Se construyen pavimentos con HCR de 60 cm de espesor y bajas exigencias de terminación debido a la escasa velocidad de los equipos que transitan sobre ellos”.
Sin embargo, el empleo del HCR en pavimentos de calles y carreteras, que ha sido ensayado en numerosas ocasiones en todo el mundo y también en nuestro país, no ha sido exitoso. En relación con el equipamiento, se registran economías marginales, puesto que los hormigones tradicionales usados en pavimentos también utilizan camiones tolvas similares a los usados en movimientos de tierra, junto con equipos para esparcir, compactar y terminar de alto rendimiento y relativamente baratos. De esta forma, no hay economías importantes ni en el transporte ni en la colocación, donde el ahorro es marginal, mientras que las terminaciones, defectuosas, concluyó Pinilla.