¿Cómo asegurar que el hormigón de nuestra obra ha alcanzado la resistencia adecuada para, por ejemplo, comenzar el descimbre de encofrado desde un piso para avanzar al siguiente? ¿De qué manera se puede monitorear la temperatura del núcleo en una fundación masivo? Para esta y otras aplicaciones, Hilti desarrolló la tecnología Concrete Sensors, con la que buscan ayudar al mandante en la toma de decisiones al registrar datos en tiempo real y así, mejorar la productividad de la obra.
Si bien la estimación de la resistencia del hormigón a través del método de la madurez no es nueva -los primeros estudios sobre el tema datan de la década de 1940- y su aplicación continúa siendo la misma, los equipos que se utilizan para medir y entregar los datos que determinen la madurez hormigón siguen cambiando y actualizándose.
Desde el uso de termocuplas, pasando por el sistema de datalogger hasta llegar en la actualidad a sensores capaces de funcionar a través de la tecnología Bluetooth, de este modo los datos para medir la madurez del hormigón y así, tomar decisiones acertadas sobre descimbres o puestas en marcha, son cada vez más precisos.
Esta precisión en los datos junto con otros atributos como la robustez de los propios sensores, entre otras características, son las que resaltan los Concrete Sensors, la cual es una tecnología desarrollada por Hilti que toma estos elementos y los lleva a un ambiente de trabajo tal, que permite conocer en tiempo real la resistencia a la compresión simple alcanzada por la mezcla específica de hormigón, a través del estado de madurez.
Analizando muestras de hormigón chileno
El primer peldaño para el desarrollo de esta nueva tecnología es el análisis del hormigón que el mandante utilizará en la obra, de modo tal que se puedan personalizar todas las variables y que el especialista a cargo de revisar la curva de madurez del hormigón reciba el detalle de su mezcla y no un estimado.
Sobre esto, Juan Pablo Rodríguez, actual Product Manager Global y ex Marketing Manager E&I de Hilti, explicó que el primer paso es analizar en laboratorio la mezcla particular. “En el caso chileno, las primeras pruebas cilíndricas y cúbicas se enviaron para análisis a nuestro laboratorio en Boston, Estados Unidos. Se midió la edad equivalente entre ambos tipos de muestras y luego, nuestros técnicos subieron al sistema las curvas de temperatura versus resistencia a la compresión simple, considerando las diferentes temperaturas de colado”.
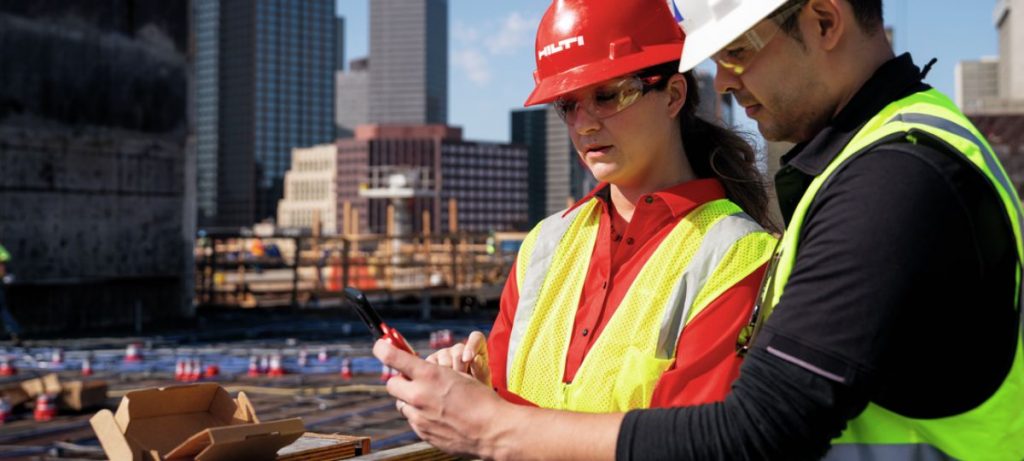
En este caso, precisó Rodríguez, el sistema se refiere a “la aplicación móvil que tiene el mandante para revisar el Concrete Sensor. En este caso, quien utilice esta tecnología podrá, a través de la aplicación, tener una lectura de un sensor en específico que esté en una mezcla en específico, en este caso, la que se utilizó en la obra”.
Mejorando la conectividad para la transmisión de datos
Aunque el uso de Bluetooth en los sensores que miden la humedad y temperatura del hormigón -los factores con los que se determina la madurez- se viene dando desde hace unos años, estos tienen un inconveniente: si estos se colocan muy profundo en el hormigón, la conexión se pierde y en definitiva, ese sensor no transmitirá los datos para analizar la madurez del material.
Uno de los desarrollos que presenta la tecnología Concrete Sensors y que resuelve este inconveniente. “Lo que se hizo para solucionar este problema, el que podríamos denominar como ‘profundidad de empotramiento’, fue que se instaló la cabeza de censado separada de la cabeza de transmisión. Físicamente, son dos sensores unidos por un cable”, explicó el ejecutivo de Hilti.
De esta forma, comentó el Product Manager, se resuelve un inconveniente que se hace notorio especialmente cuando se trabaja con, por ejemplo, hormigones masivos. “Para este tipo de hormigones, se necesitan sensores en superficie y en el centro, especialmente por si aparecen fisuras térmicas. En el caso del sensor en el centro de la masa de hormigón, su conexión se pierde al minuto que viertes el material. Por este motivo, Concrete Sensors posee un cable de medición que se amarra al centro y luego, se coloca el transmisor a unos 5cm de la superficie”.
En esa línea, Rodríguez destacó que el largo del cable sólo dependerá de la necesidad del mandante, por lo que esta tecnología posee un nivel de flexibilidad que otros sensores de similares características no poseen.
¿Cómo minimizar la presencia de medidores en obra?
Junto con esto, y para asegurar una transmisión continua y efectiva de los datos, esta tecnología se complementa con la instalación de hubs que, aclara Rodríguez, se rentan. “Con esto, se incrementa el alcance de la señal y así, el mandante se conecta directamente a los sensores, no por medio de un móvil, revisando la data de su mezcla en tiempo real a través de la aplicación”.
“De esta forma -complementó- se puede utilizar, por ejemplo, Bluetooth para fundaciones más pequeñas. Para áreas de trabajo más grandes, lo ideal es contar con los hubs”.
Asimismo, el ejecutivo destacó el alcance que tiene la señal de transmisión de esta tecnología. “Los hubs poseen un alcance de unos 300 metros. El alcance del Bluetooth, por otra parte, está en el orden de los 25, 30 metros. Esto, claro, dependiendo de los obstáculos que estén frente al sensor”.
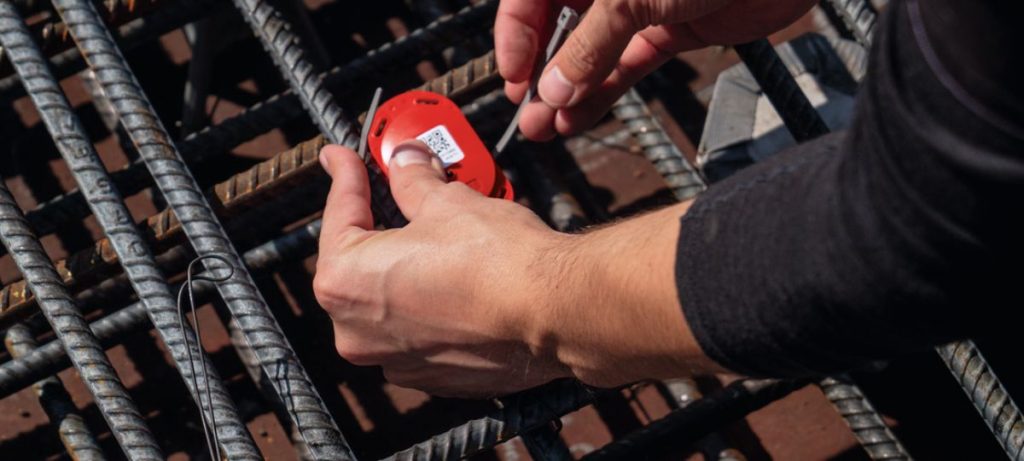
A modo de ejemplo, en Chile la empresa Hilti estudió 2 pilotos en hormigones masivos y el alcance de los sensores fue de 1,5 metros máximo. Los obstáculos que pueden impactar esta reducción del alcance podrían ser: la distancia de instalación del sensor, el encofrado, agua estancada, hielo, equipos, materiales, etcétera.
Data en tiempo real: Ventajas de Concrete Sensors
Otro de los aspectos -quizás el más relevante- que presenta la tecnología de Concrete Sensors es que ofrece data en tiempo real al mandante, lo que ayuda a que éste tome decisiones basados en información relevante sobre la mezcla de hormigón utilizada en obra.
“Nadie está tratando la data en tiempo real”, aclaró Juan Pablo Rodríguez. “El sistema funciona en base a algoritmos matemáticos que trabajan en función a los resultados de los ensayos realizados sobre la mezcla a utilizar en la obra en nuestro laboratorio o en alguno que cumpla con el estándar Hilti. Por ejemplo, nos suministran un hormigón, el que tipificamos con un código interno G14-28. Entonces, el mandante encontrará ese hormigón, con el mismo nombre, en la aplicación”.
De esta forma, el sistema de algoritmos matemáticos lo único que ejecuta es un ajuste a la curva de madurez. “Entonces, la lectura en tiempo real de temperatura y humedad hará que el algoritmo matemático, que simplemente es el ajuste a la curva, de la información en tiempo real”, comentó.
Así, el personero de Hilti destacó que, en el caso de hormigones no masivos, se pueden tomar decisiones sobre el descimbre de encofrados sólo revisando los datos que arroje el sistema respecto a la resistencia del hormigón utilizado en obra, ya que éste ya se encontraría registrado. “Por ejemplo, si quiero saber cuándo puedo sacar el encofrado y los paneles del piso 4 para pasar al 5, no debo esperar a que lleguen los resultados del laboratorio el día 7 o el 14. Con este sistema, el mandante puede decir ‘ok, llegó a 30 MPa, ya puedo descimbrar’”.
En el caso hormigones masivos, este sistema cuenta con un sistema de alarmas que notifican al usuario cuando se produce un delta entre el núcleo del masivo y la superficie. “Pongo el caso: el mandante puede establecer que la aplicación de Concrete Sensors de una alarma cuando la diferencia de temperatura entre el centro y la superficie del elemento sea de un 22%. ¿Para qué es esa alarma? Para crear microclimas, para cubrir el elemento con sábanas especiales, para humedecerlo. Todas esas acciones sólo se logran con datos en tiempo real”, subrayó.
Aportando a la productividad de la obra
Con funciones como ajustes de vertido de hormigón a bajas temperaturas -ideal, recalcó Rodríguez, para obras que se ejecuten en altura- entre otras prestaciones, el sistema que compone a Concrete Sensors puede ajustarse a cualquier necesidad que tenga la obra y, en base a esto, la toma de decisiones beneficia a la productividad de la misma, a través de la información que Hilti obtuvo de los ensayos en el hormigón utilizado en la obra en cuestión.
En ese sentido, Juan Pablo Rodríguez subrayó el sistema Concrete Sensors busca entregar “data temprana para que el mandante tome decisiones inteligentes. Esta tecnología está desarrollada para tomar decisiones en tiempo real y que busquen incrementar la productividad de la obra”.
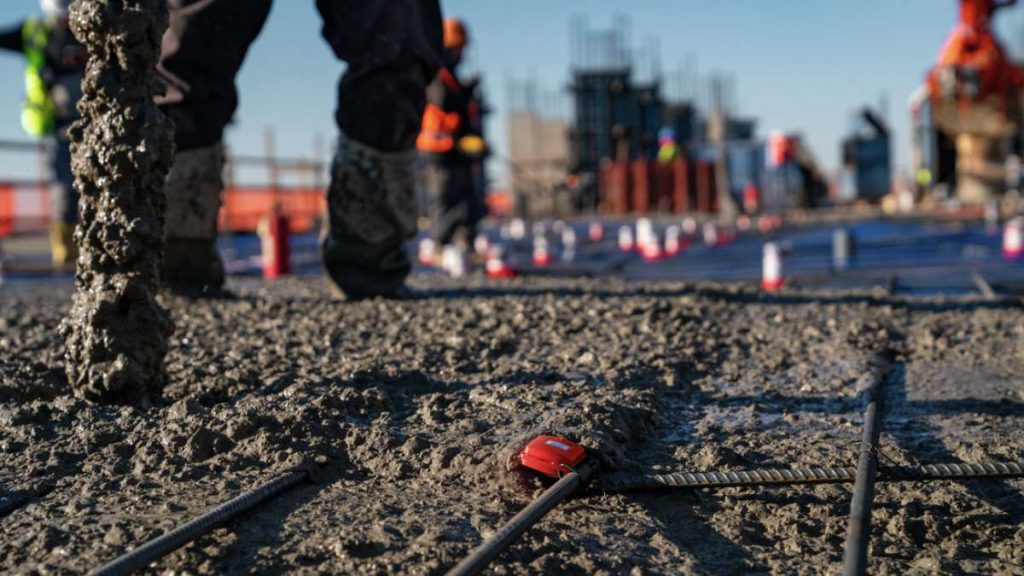
Cabe mencionar que la empresa Hilti prevé el lanzamiento en Chile de esta tecnología para el año 2023, por lo que si se busca información de estudio, ésta se encontrará disponible en el sitio web www.hilti.cl a partir del segundo semestre de este año.
Actualmente, a nivel nacional se están trabajando pilotos de prueba y las muestras son enviadas a los laboratorios en Estados Unidos, en donde el servicio completo ya se encuentra a disposición de todos los clientes.