Con la posibilidad no sólo de asegurar producción de hormigón de forma continua, sino que, además, permitir dosificaciones exactas e incluso, la producción de hormigones especiales, las plantas móviles de hormigón se alzan como una excelente alternativa para el suministro del hormigón, ya sea en obras menores como en proyectos de gran envergadura.
La idea de trasladar y lograr una producción mecánica e industrializada del hormigón en el sitio de una obra no es nueva. Existen datos que muestran que ya a fines del siglo XIX, comenzaron a fabricar hormigones y morteros con el uso de mezcladoras mecánicas en plantas destinadas para la producción del material.
Uno de los inconvenientes de esa temprana forma de producción industrializada del hormigón era trasladar el producto ya premezclado desde la planta al sitio de la obra, incurriendo en gastos de transporte. Por ello, a comienzos del siglo XX, es que se conoce del primer evento que traslada la producción industrial al sitio de la obra: en 1909, en la localidad de Sheridan, en Wyoming, el material fue entregado por un mezclador accionado por caballos que utilizaba paletas para la mezcla.
Ese primer apronte de un vehículo que transporta el proceso industrializado de la fabricación de hormigón al lugar de la faena, sirvió para que en 1917 se ingresara la primera patente de lo que hoy conocemos como un camión mixer, equipo que finalmente comenzó a ser fabricado en la década de 1930, con una disposición similar a la que actualmente poseen este tipo de máquinas.
No obstante, la aparición de las plantas móviles de hormigón -también conocidas como mixeres volumétricos continuos- no se gestó hasta tres décadas después. Y si bien en un comienzo la idea de este tipo de maquinaria fue la posibilidad de producir el hormigón de la obra in situ de manera industrializada, con el paso del tiempo, se han incorporado nuevas tecnologías que en la actualidad la transforman en un nexo entre eficiencia en la entrega del material e incremento de la productividad en obra.
Plantas móviles de hormigón: Historia y definición
1964 fue el año en el que se ingresó la patente de lo que actualmente conocemos como una planta móvil o mixer volumétrico continuo de hormigón. La idea era tener una máquina que proporcionara el material por volumen y que pudiese transportar los ingredientes necesarios para la producción de hormigón en sitio, en vez de entregarlos y hacer el material en otro lado.
De acuerdo a la Volumetric Mixer Manufactures Bureau -organismo creado en 1999 que reúne a los principales fabricantes de estas unidades en Estados Unidos-, para el año 1979, ya se habían vendido más de 2000 unidades de este, en ese entonces, innovador equipo. De igual forma, para inicios de la década de 1980, ya existían varios actores en el mercado, el que incluso se extendió a Europa, específicamente a Italia, lo que facilitó mejoras e innovaciones en este tipo de maquinaria y, por ende, el desarrollo de los equipos automatizados más avanzados de la actualidad.
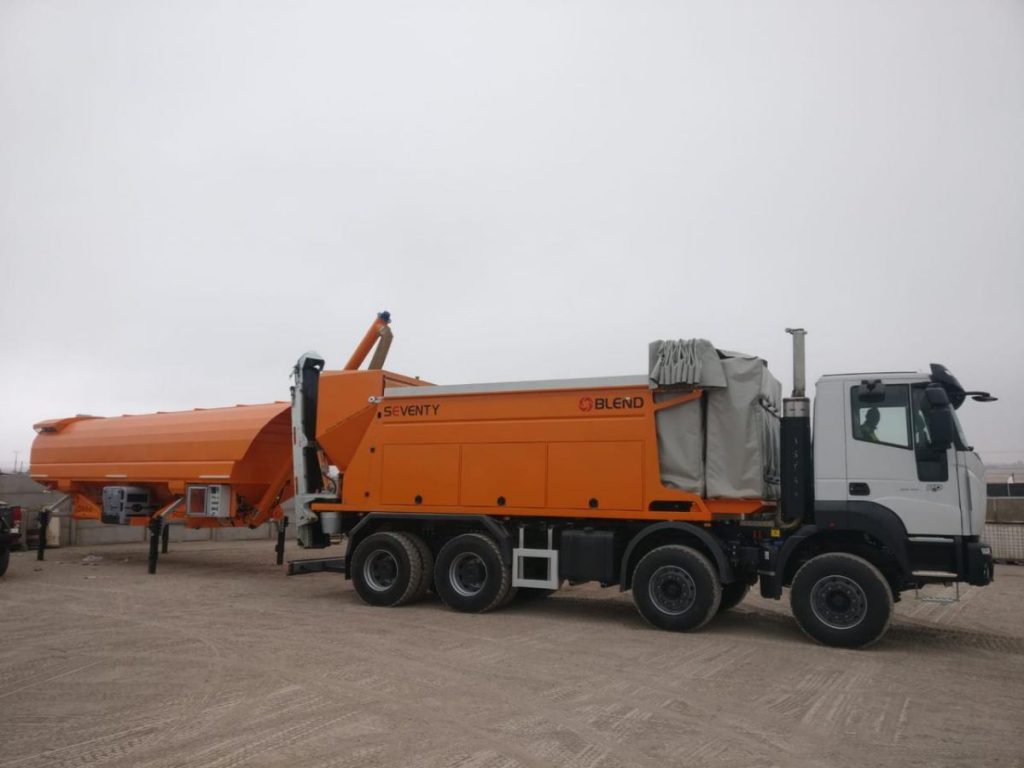
¿De qué se compone una planta móvil de hormigón? “Imaginemos un camión mixer convencional al que se le saca la betonera y, en el mismo camión, se monta una planta de hormigón, con su estanque de agua, tolvas de árido (fino y grueso), tolva de cemento y estanques de aditivos, además de otros elementos adicionales, según sea el requerimiento, como por ejemplo, una bomba de concreto incorporada”, comentó Rodrigo Reyes Jara, CEO de Durability Concrete, profesor de Innovación y jefe del programa Construcción 4.0 de la Pontificia Universidad Católica de Chile (PUC).
“Esta planta -agregó el también académico de la PUC- contiene todas las materias primas necesarias para confeccionar hormigón, pero la mezcla la realiza en el momento justo de la colocación, mediante un mezclado de alta revolución”.
Este proceso se realiza mediante un mezclado de alta revolución, “a través de un tornillo sin fin dispuesto en la parte trasera del equipo”. Una vez mezclado, el hormigón “se coloca mediante una cinta transportadora extensible, de tal forma de llegar al punto de colocación requerido”, dijo Reyes.
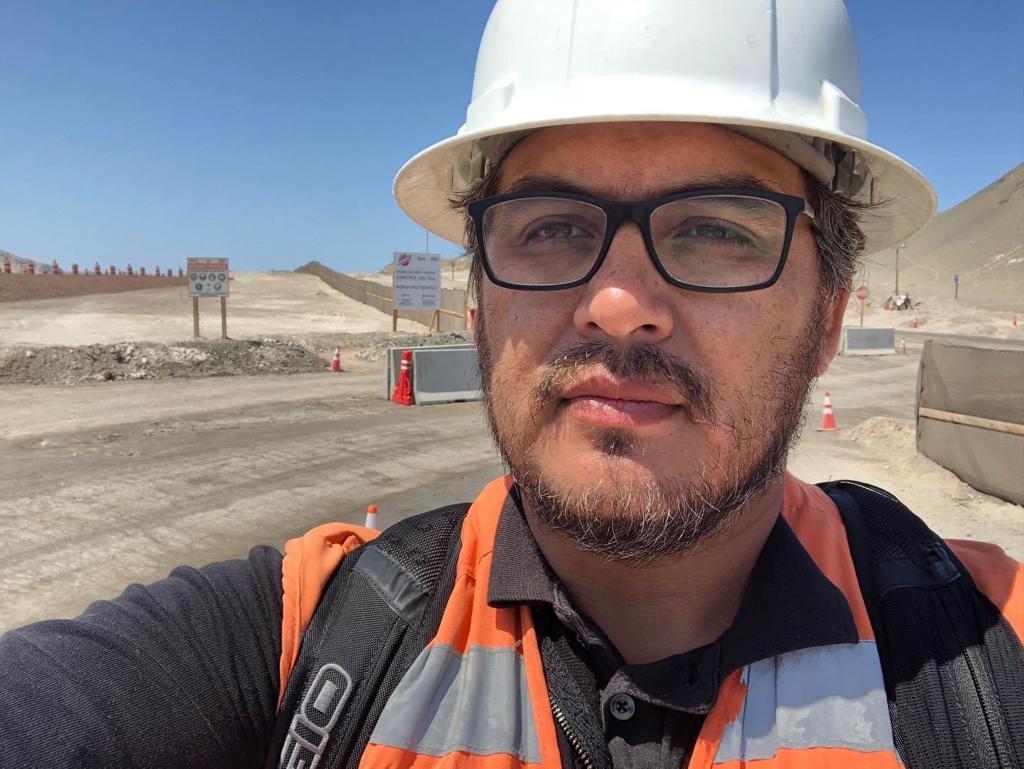
Otro tipo de planta de hormigón transportable son las denominadas plantas semimóviles, las que “pueden ser remolcadas por una camioneta o un camión, donde el equipo va montado sobre un carro de arrastre. En este caso, esta planta se alimenta de energía con un motor independiente, a diferencia de la montada sobre camión, del cual extrae la energía para su funcionamiento”.
En este tipo de equipos, los componentes y el trabajo a realizar son los mismos que los de un mixer volumétrico pero en vez de ir acoplada a un camión, un vehículo externo la transporta hasta el sitio de la obra.
Capacidades de las plantas móviles de hormigón
Una de las grandes ventajas que poseen las plantas móviles de hormigón o mixer volumétricos, es la versatilidad que estos equipos poseen gracias a su capacidad la que, según Rodrigo Reyes, es de un amplio espectro.
En efecto, las plantas móviles tienen dos maneras de producir hormigón: “en forma autónoma, es decir, hasta que las materias primas se acaben, o en mezclado continuo, lo que considera el relleno de las materias primas para asegurar la fabricación del hormigón de forma continua”, explicó el académico.
De esta forma, la capacidad de una planta móvil de hormigón puede variar dependiendo de cómo se van suministrando los materiales para la producción del material. “Se pueden producir desde 0,1 m3 hasta 12 m3 de forma autónoma”, puntualizó.
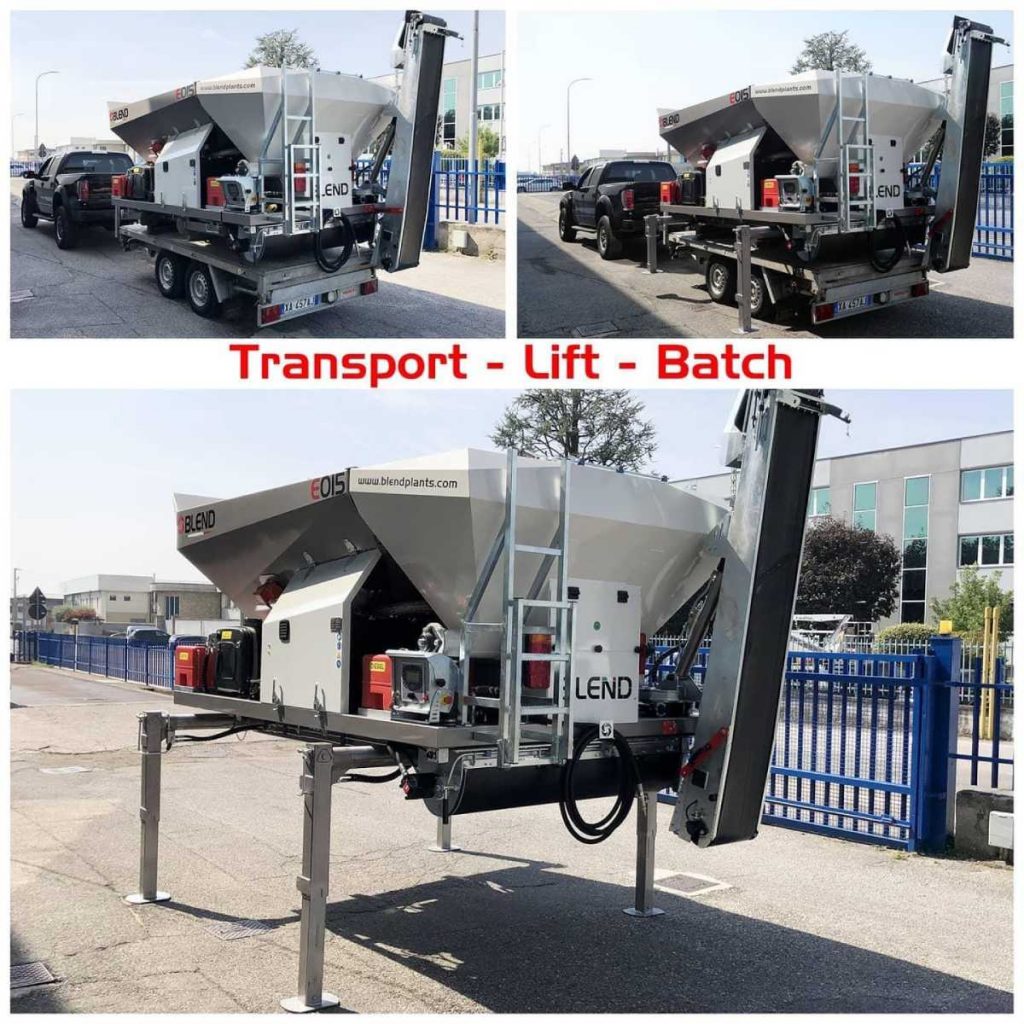
Para el caso que se utilice un mezclado continuo, Reyes explicó que, dependiendo del tipo de planta móvil de hormigón, este puede llegar a producir 70 m3/hora de hormigón. “También existen otro tipo de máquinas que tienen una mayor producción, se montan en poco tiempo, pueden transportarse con camión de arrastre y cuentan con la misma tecnología que los mixer volumétricos”, añadió.
“La gracia de esa clase de equipos -destacó Reyes- es que, al montarse en un par de horas, permiten tener un suministro constante de grandes cantidades de hormigón (hasta 120 m3/hora) sin necesidad de instalaciones de faenas permanentes”.
Programando cantidades y dosificaciones: la versatilidad de las plantas móviles de hormigón
Una de las grandes ventajas que poseen estos equipos, dice relación con la posibilidad de programar dosificaciones y cantidades para conseguir una mezcla adecuada y precisa de hormigón, sin merma de material.
“En la actualidad, las plantas móviles de hormigón están automatizadas en todas sus versiones, por lo que no requiere de intervención manual. En este caso, es una sola persona que la opera”, explicó Reyes. En este caso, el operador de la planta móvil de hormigón realiza todas las acciones mediante un computador central instalado en la máquina o a través de un control remoto.
La producción de hormigón en este tipo de equipos está basada en un sistema de cintas que transportan los áridos finos y gruesos, junto con el cemento, a la mezcladora para así, fabricar el concreto al volumen deseado para la obra.
“La tecnología actual es mucho más avanzada, ya que presenta dos cintas que transportan la arena y el árido grueso, en forma independiente, hacia el tornillo mezclador, luego de que este recibe el cemento, que es pesado en balanzas, y el agua y aditivos que son medidos por caudalímetros, para formar la pasta que aglomera el material pétreo que es medido o por peso o por flujómetro continuo, mezclando todas las materias primas a alta revolución, para obtener hormigón en menos de 10 segundos y en volúmenes que pueden ser desde 0.1 m3, con total homogeneidad”, subrayó Rodrigo Reyes.
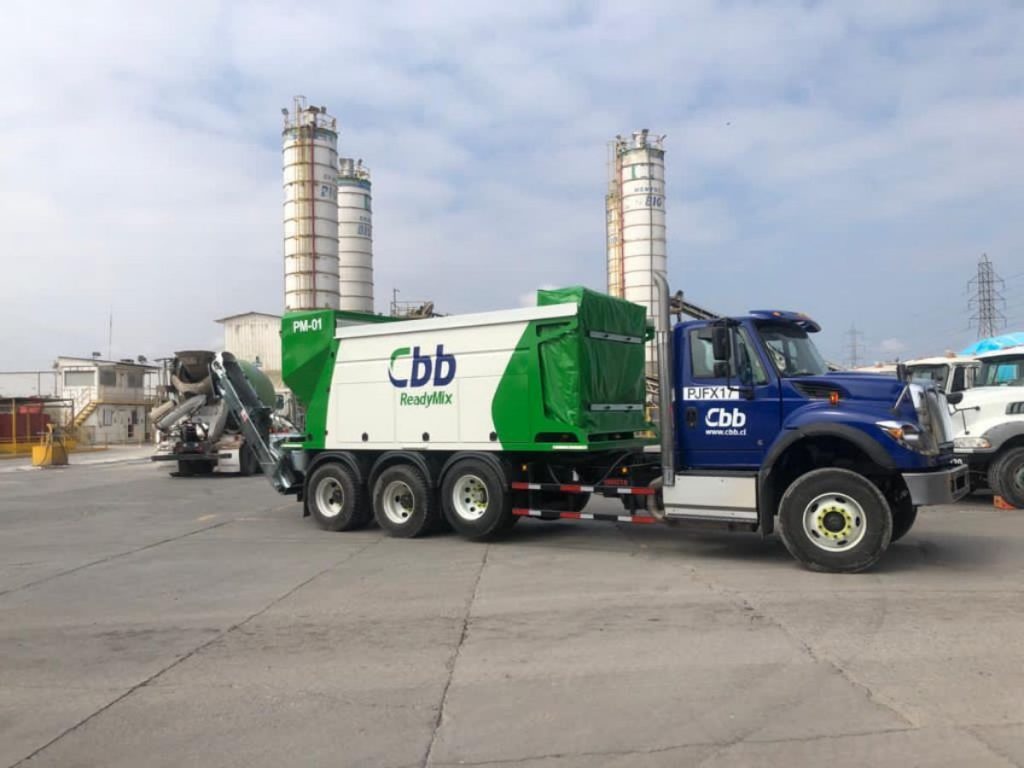
Gracias a esto, explicó el jefe del programa Construcción 4.0 de la PUC, las plantas móviles de hormigón de última generación poseen una mayor versatilidad, “ya que permite hacer mortero o shotcrete, sin tener que vaciar la tolva de árido grueso, así como tener un mayor rango de docilidad, que va desde un asentamiento de cono 0 cm hasta un autocompactante, además de no requerir de la operación manual de compuertas para el flujo del árido”.
El académico añadió que las máquinas más modernas como las italianas, equipadas con esta tecnología, tampoco cuentan con compuertas, las que sí están presentes en otras plantas volumétricas, por lo que el flujo de áridos para la mezcla se controla directamente a través de la velocidad de la cinta.
Asimismo, agregó que las plantas actuales, al disponer de un proceso completamente automatizado, también poseen “sensores con actuadores que detienen el proceso ante alguna anomalía de producción, como falta de áridos y otra materia prima”.
Producción de hormigón a la medida de la obra
Como se mencionó, la versatilidad de las plantas móviles o plantas volumétricas de hormigón -en especial, las de última generación- permiten la producción del material en cantidades exactas a los requerimientos donde se instalen esta clase de equipos.
¿Pueden, sin embargo, trabajar con distintas materias primas? Por ejemplo, el uso de áridos reciclados u áridos artificiales ya está siendo incorporado en los distintos diseños de mezcla del hormigón. En ese sentido, Rodrigo Reyes destacó que estas maquinarias “pueden trabajar con cualquier tipo de áridos que se requiera utilizar para la producción de hormigón. Incluso, se ha reutilizado árido reciclado de escombros”, aseguró.
Sin embargo, el experto puntualizó que “la limitación va más por el requerimiento según dosificación o colocación, pero se puede usar árido muy fino o grueso hasta 50 mm. Una limitación más de tipo logístico, podría ser el requerimiento de utilizar más de dos tipos de áridos en una mezcla, aún cuando se puede fabricar a pedido según el requerimiento específico para el proyecto particular, por ejemplo, si se requieren 3 o 4 tipos de áridos distintos, para lo que la planta tendría 4 tolvas de áridos independientes”.
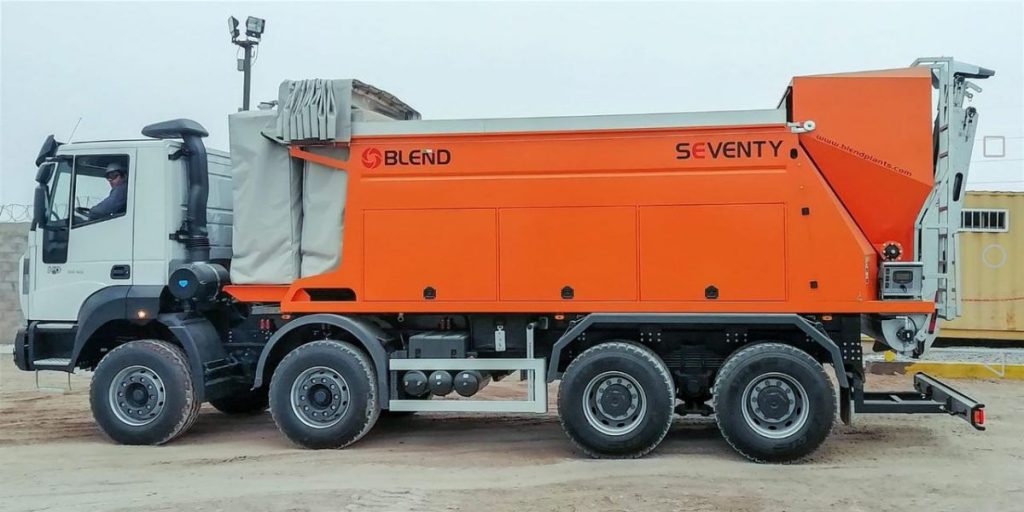
En ese sentido, y dadas las características de este tipo de maquinaria, existe la posibilidad de “programarlas” para producir hormigones con características especiales, como por ejemplo, autocompactantes, de alta resistencia o pigmentados, los que poseen dosificaciones de materias primas distintas a las de un hormigón tradicional.
“Se pueden agregar una serie de dosificaciones, las que estarán guardadas y a la espera de presionar un simple botón para cambiar de un tipo de hormigón a otro, con lo que esto significa en términos de optimización de diseño, sobre todo en el uso de la cantidad de cemento, cuestión que es fundamental para la disminución de la huella de carbono y otras consideraciones en la producción de hormigón dentro del marco de la economía circular, tan necesaria en estos tiempos ”, dijo el académico de la PUC.
Sin embargo, el profesional puntualizó que en la actualidad, “si un cliente requiere 3,5 m3 de un hormigón pobre y 4 m3 de un hormigón de alta resistencia, lo que típicamente haría sería comprar un camión mixer convencional (no volumétrico), con su capacidad completa de 7,5 m3 con hormigón de alta resistencia para colocar esos 4 m3 y derrocharía los 3,5 m3 restantes donde debía haber puesto hormigón pobre, lo anterior por efectos de que le cobrarían por la carga no transportada (o el aire trasportado), dado el costo de oportunidad de enviar ese mismo camión con más de 3,5 o 4 m3 a otra obra, si pidiera 2 camiones distintos con 4 y 3,5 m3”.
Justamente, las posibilidades que poseen las plantas móviles de hormigón, junto con la capacidad que tienen estos equipos de cambiar de una dosificación a otra, permiten la producción de volumen justo de material, “con lo cual no hay derroche de hormigón ni de resistencia”.
Es por ello que las plantas móviles de hormigón están capacitadas para la producción de hormigones con características especiales. “Se pueden hacer autocompactantes, de alta resistencia, con pigmentos, impermeabilizantes, con fibra, fabricar shotcrete, rapidset o cualquier otro tipo que se requiera”, destacó Reyes.
“En particular, los hormigones de rápido o instantáneo fraguado, para tránsito a un par de horas, se hacen con este tipo de equipos, por las posibilidades logísticas que ya se han mencionado, como hacer la mezcla en el momento justo de la colocación, con aditivos y cemento especiales para dicha faena instantánea”, agregó.
Versatilidad en obra: Plantas móviles para diversas aplicaciones
Gracias a los atributos expuestos, a juicio de Rodrigo Reyes las plantas móviles volumétricas de hormigón pueden utilizarse en diversos tipos de obras, en especial, aquellas que estén alejadas de las productoras del material.
El uso de las plantas móviles se ve más en obras que estén insertas en la ciudad y, en especial, “para bajos volúmenes que las plantas hormigoneras no atiendes porque se encarece el producto. Entonces, el uso de las plantas móviles permite acudir a una amplia variedad de obras de menor envergadura o detalle”, comentó el académico.
Asimismo, destacó que estos equipos son perfectos para “obras rítmicas, donde se requiere que el equipo produzca en forma continua o secuencial, esperando los ritmos de obra y no al revés, como usualmente ocurre de que la obra depende de que el camión mixer regrese cuanto antes porque el producto puede fraguar en la betonera”.
“En este mismo sentido -agregó- las constructoras que quieren controlar su propia producción, típicamente también compran su equipo para producir al ritmo que demandan sus necesidades específicas”.
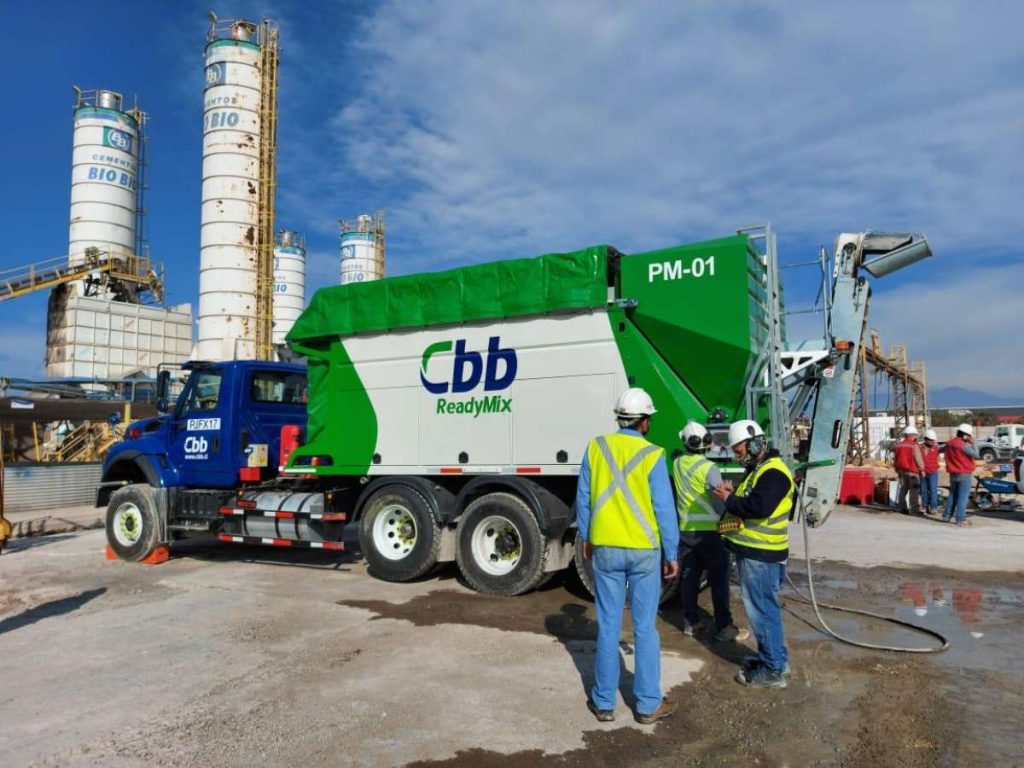
De igual forma, existen otros campos en los que las plantas móviles de hormigón pueden utilizarse con grandes resultados. Por ejemplo, comentó el experto, estos equipos son ideales para “los proyectos mineros, debido a las complejidades logísticas de estar lejos de los centros de distribución y por la alta demanda medioambiental, debido a las estrictas exigencias de permisología, las cuales son una ventaja en este tipo de plantas móviles que ayuda incluso a obtener puntos para adjudicar proyectos mineros al ser un gran aporte en no generar residuos y no requerir instalaciones de faenas, además que la logística requiere de equipos de dimensiones que permitan su tránsito y al mismo tiempo, acompañen el avance de la obra. Esto se puede trasladar a otras obras subterráneas como el metro”.
Junto con esto, aseguró, “otro nicho que se está abriendo con fuerza son las plantas de energía renovable como las solares y las eólicas, en donde estos equipos pueden ir moviéndose conforme avance la obra, lo que disminuye drásticamente el impacto medioambiental por tránsito de equipo”.
Reyes también destacó el uso de plantas móviles de hormigón en pavimentos, ya que “requieren de un avance acorde a la obra, como los tradicionales o incluso los pavimentos compactados con rodillo CCR”. En ese mismo sentido, destacó que su uso también se puede extrapolar “a todo proyecto que se encuentre en zonas de bajo acceso a plantas hormigoneras establecidas, como en algunas regiones del país, donde se puede llegar e instalar en el mínimo tiempo y funcionar con requerimientos de producción mínimos y de fácil acceso, tanto por las dimensiones del equipo, como por su versatilidad”.
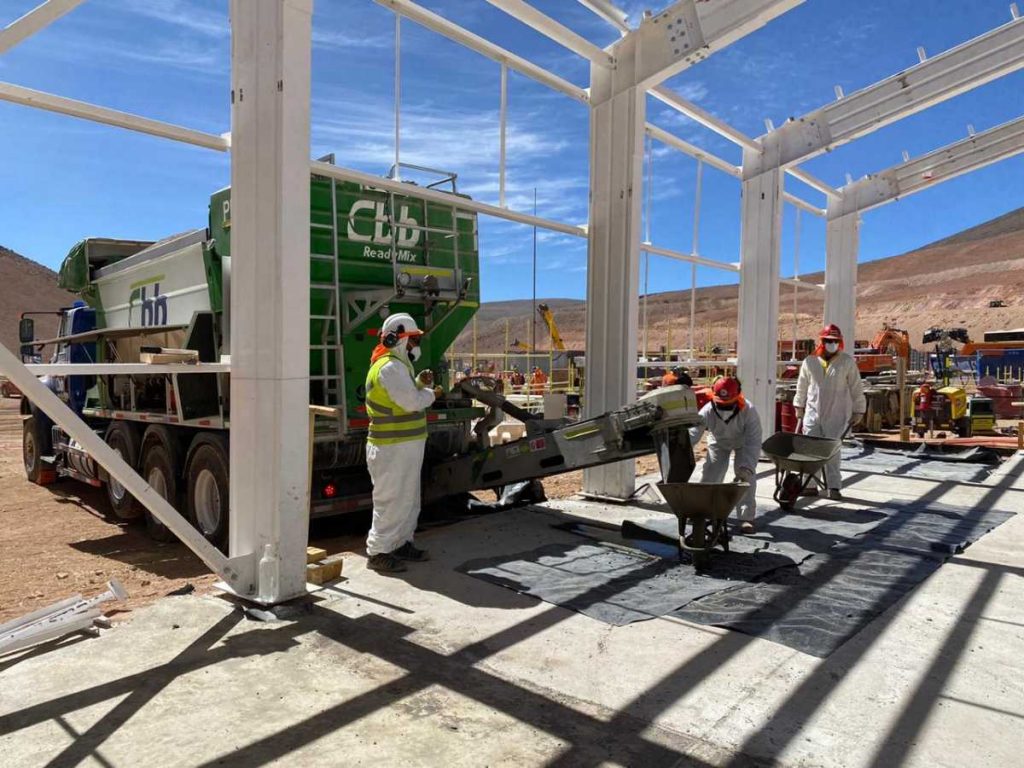
En ese sentido, el experto agregó que, por sus características, el uso de estos equipos es altamente recomendable “para el hormigón industrializado, ya sea en planta prefabricadora establecida o yard de faena, así como para las uniones húmedas de obra, que son volúmenes pequeños y de alto requerimiento de resistencia y calidad”.
Por último, comentó Reyes, “es altamente recomendable que los productores de hormigón premezclado ya establecidos cuenten con una flota de estas plantas móviles que les permita complementar su oferta, ya sea en proyectos especiales como los mencionados, así como para acceder a mercados que antes eran inaccesibles como los bajos volúmenes”.
En ese sentido, explicó que esto permitiría ofrecer hormigón al detalle o “distribuir mejor su flota combinada de plantas fijas con camiones mixer y de plantas móviles, por ejemplo, para la colocación del hormigón de término de una faena, que típicamente es de un volumen menor y su variabilidad en cantidad es alta, generando grandes pérdidas por concepto de escombros”.