El uso del hormigón proyectado o shotcrete para el sostenimiento de túneles es ampliamente conocido. Sin embargo, esta metodología se puede ver cada vez más en pozos o shafts para distintos usos, como se puede revisar en este interesante artículo publicado originalmente por la revista Shotcrete Magazine, de la American Shotcrete Association, en el que se analiza la aplicación del shotcrete en pozos de obras secundarias y cómo esta metodología dialoga con los proyectos ya existentes.
Autores: Paul von der Hoeh, Norbert Fuegenschuh, Richard Gradnik
Traducción y edición periodística: Felipe Kraljevich M.
En la actualidad, la construcción de toda clase de shafts de hormigón proyectado -shotcrete- se está haciendo cada vez más popular, especialmente en el área de Europa Central. Se necesitan shafts en combinación con proyectos de infraestructura, centrales eléctricas, de tratamiento y distribución de agua. Algunos de los pocos usos específicos de los shatfs incluyen: ventilación, sistemas de evacuación de emergencia, cámaras de compensación, transporte de agua y elevación de tuberías o cámaras de caídas en el manejo de aguas servidas.

La colocación del shotcrete en los shafts requiere una preparación del trabajo precisa y una elección bien meditada del método de pulverización para asegurar un proceso de construcción optimizado. Este proceso y la ejecución final se ilustra más adelante a través de diferentes casos de estudio.
Colocación del shotcrete
Dependiendo del diámetro y profundidad del shaft, el shotcrete puede aplicarse ya sea de manualmente o a través de un equipo de boquilla manipulado de manera remota. Comúnmente, se utilizan tres tipos de métodos para colocar el shotcrete para el sostenimiento de la roca excavada o de la superficie del suelo: una mezcla en seco, mezclas semi-húmedas y mezclas húmedas de hormigón proyectado. Cada uno de estos métodos tiene ciertas características y debe seleccionarse en función de las condiciones y circunstancias específicas del proyecto en cuestión.
Shotcrete de mezcla seca
Una ventaja decisiva del shotcrete de mezcla seca es que el reducido espacio que ocupa el equipo en el sitio de la obra en comparación con otros métodos. En particular, en áreas urbanas densamente pobladas y en locaciones montañosas empinadas, el almacenamiento del shotcrete secado en horno en silos puede evitar el desplazamiento constante de vehículos que suministren el hormigón y puede llenarse en grandes lotes.
Este proceso es particularmente ventajoso en shafts angostos y, en general, proyectos donde se utilizan cantidades pequeñas e impredecibles o donde el uso de hormigón premezclado no es económicamente eficiente. Normalmente, se alcanzan rangos de pulverización de hasta 4m3/hr. Para reducir la formación de polvo y el rebote, es absolutamente necesario utilizar una unidad de prehumedecimiento.
Shotcrete de mezcla semiseca
El shotcrete de mezcla semiseca es una variante que es poco utilizada en la actualidad, aunque posee ventajas significativas. El hormigón mismo tiene una composición similar al hormigón rociado húmedo, pero los materiales del hormigón se encuentran parcialmente humedecidos (similares a los niveles de humedad que veríamos en nuestras fuentes de áridos, del 3 al 5%) y se le agrega agua en la boquilla durante el proceso de rociado. Esencialmente, esto también tiene sentido para shafts más estrechos, ya que aquí tampoco se pueden alcanzar altas tasas de rociado (hasta 6m3/hr. – dependiendo del tamaño de la bomba). Dos de las mayores ventajas sobre el shotcrete de mezcla seca son el bajo factor de rebote y la significativamente menor generación de polvo. Además, es especialmente adecuado su uso si se dispone de una planta mezcladora en el sitio de la obra, ya que puede producirse fácilmente.
Shotcrete de mezcla húmeda
In contraste con las variantes previas, el shotcrete de mezcla húmeda principalmente se rocía con un sistema mecánico de manipulación de boquilla y puede alcanzar tasas de rociado significativamente más altas (hasta los 25 m3/hr.). La formación de polvo y el rebote también pueden reducirse significativamente al compararlo con los procesos en seco. Debido al espacio de trabajo del operador del pulverizador y la relación costo-efectividad de volúmenes de hormigón más grandes, el uso de este método generalmente toma sentido sólo en shafts de diámetros más grandes.
Historias de Casos
5,5 metros de diámetro y 85 metros de profundidad
Descripción del proyecto
Un buen ejemplo del uso de shotcrete en shafts profundos y estrechos es el pozo de ventilación de un largo túnel de carretera de 3,6 km de extensión, ubicado en los Alpes al sur de Alemania. El túnel de carretera de un solo tubo con un túnel de rescate paralelo se ventila a través de un falso cielo y una cámara de ventilación conectada. Luego, el aire de escape se extrae de la caverna al aire libre a través de un shaft de ventilación. El shaft mismo se hundió desde la superficie a una profundidad de 85 metros utilizando una excavadora y tronaduras con un diámetro de excavación de 5,5 metros. El área de preparación para el shaft se ubicó a unos 100 metros más alto que el portal norte del túnel principal en la ladera de la montaña y se podía llegar a través de una vía de acceso temporal de 500 m de largo. Dependiendo de las condiciones geológicas, se aplicaron entre 150 a 300 mm de shotcrete -en su mayoría, de una sola capa- para el sostenimiento, reforzado con malla metálica soldada (WWF, en sus siglas en inglés). Esto equivale a un área aproximada de 1.500 m2.
Selección del método de rociado
Debido a la muy estrecha ubicación, se tomó la decisión de aplicar shotcrete de mezcla semiseca de manera manual. Esto fue principalmente por las pequeñas cantidades requeridas para cada etapa del trabajo (usualmente, menos de 3 m3), lo que significó que el volumen de entrega del mixer de hormigón, de alrededor de 7 m3, pudiese producirse en el transcurso de varias horas. Otro factor decisivo fue la posibilidad de tener shotcrete en el lugar listo para su uso durante las faenas de excavación. Las condiciones difíciles y potencialmente cambiantes del suelo requirieron que los operadores pudiesen aplicar el hormigón proyectado en poco tiempo.
Trabajos de construcción
El trabajo comenzó a mediados del año 2020 con la construcción de un precorte de 6 metros de profundidad al que se le aplicó shotcrete reforzado con clavos, y el área de preparación del sitio. Los 56 metros superiores se excavaron con un sostenimiento avanzado que utilizó pilotes de chapa metálica, mientras que la sección bajo los 56 m se excavó completamente mediante perforación y voladura. Por lo tanto, se eligió una miniexcavadora de 3,5 toneladas, la que pudiera equiparse con un taladro y un martillo hidráulico. Debido a la longitud y flexibilidad requeridas del cable, se utilizó una grúa telescópica sobre orugas (fabricada por Sennebogen) de 130 toneladas (118 toneladas) para las elevaciones verticales dentro y fuera del pozo.
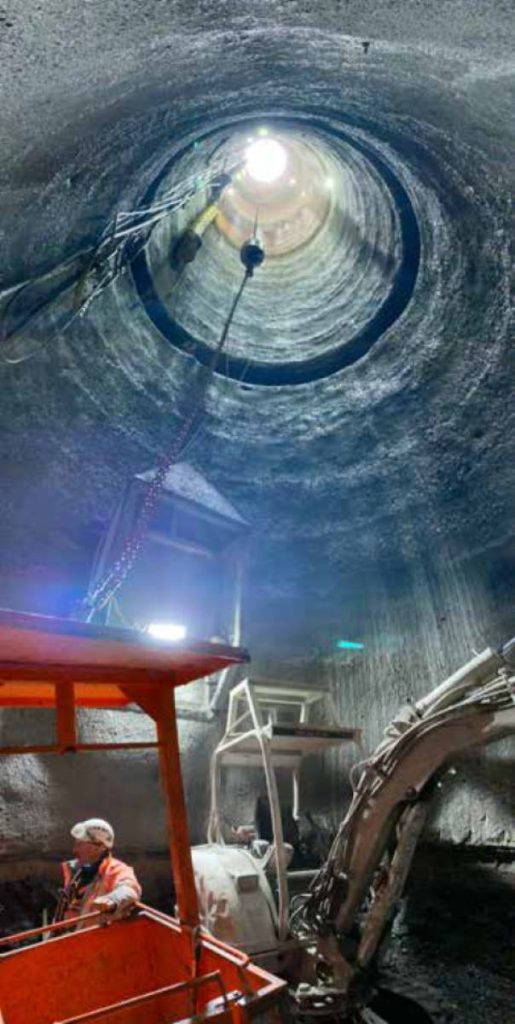
El hormigón se produjo en una planta mezcladora en el sitio de la obra, ubicada en el portal del túnel principal, aproximadamente a 2 kilómetros del sitio del shaft y se acopió temporalmente en el sitio de la obra en una tolva de manipulación. Como dispositivo de pulverización se utilizó una pistola rotativa para shotcrete de mezcla seca Aliva 262, con aire comprimido suministrado desde un compresor Atlas Copco GA75.
Para transportar el hormigón, se adhirió al muro una tubería de acero de 50 mm. de diámetro. Se prestó particular atención a una fijación adecuada ya que el gran peso del hormigón y la tubería sobre los 85 metros representaban un grave riesgo para el personal. Las líneas de suministro se ampliaron a intervalos regulares, generalmente cada 5 metros.
El shotcrete se suministró mediante la pistola rotativa, la que se ubicó en la superficie con el compresor de aire a través de la tubería de acero hacia la boquilla. Luego, el operador de shotcrete añadió el agua y el acelerante. La velocidad a la que se agregó el acelerante fue de aproximadamente un 5% a un 8% para lograr la curva de resistencia inicial requerida de J3 (consultar la Guía Austriaca para Shotcrete [1] y la Norma Europea [2]). Se utilizó agua tibia para iniciar el proceso de hidratación durante el tiempo frío de invierno.
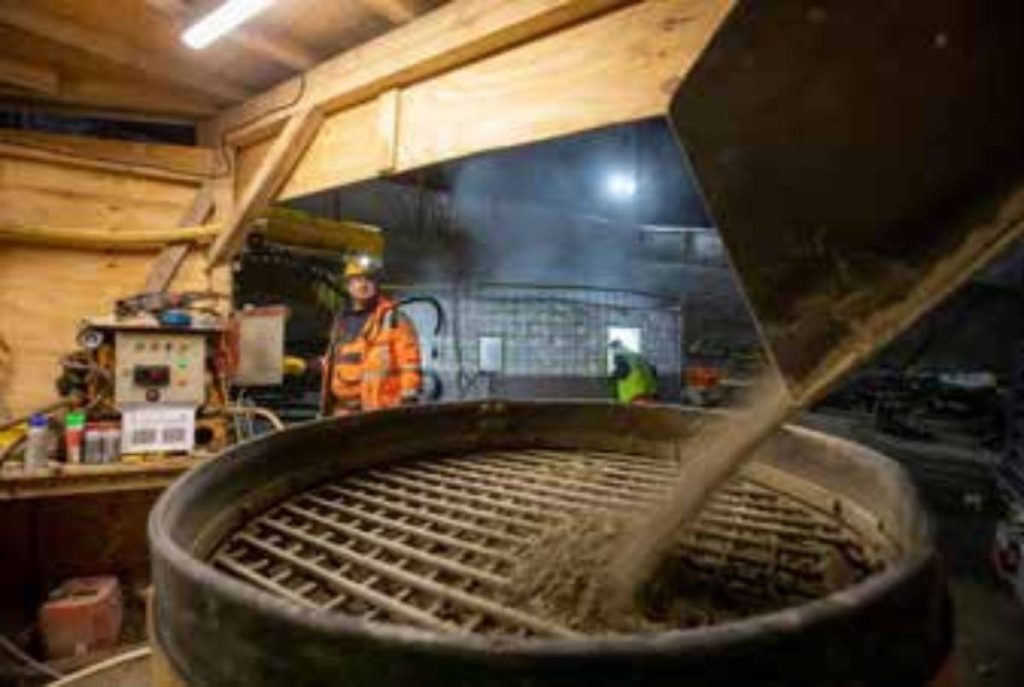
El uso de shotcrete semiseco también entregó seguridad laboral y ventajas económicas, ya que la cantidad de polvo y rebote es significativamente menor comparado con el hormigón proyectado de mezcla seca. Los trabajadores fueron equipados con respiradores con purificadores de aire energizados y se diseñó un concepto de ventilación adaptado a las condiciones de la obra. La comunicación obligatoria entre el pistolero y el shotcretero se garantizó por radio.
Las tasas de pulverización promedio alcanzadas fueron de 1,5 m3 a 2 m3 por hora, incluyendo el tiempo de preparación.
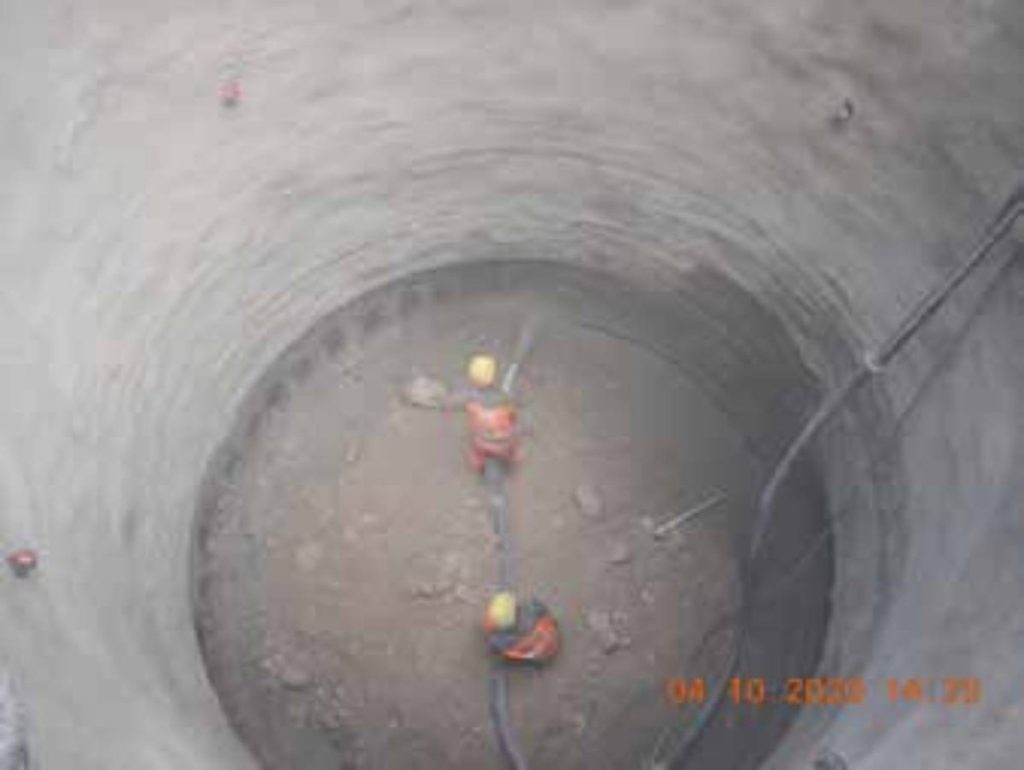
Control de espesor
Se llevó a cabo una comparación de las cantidades del shotcrete entregado y del instalado como parte del proceso de evaluación post construcción de la excavación del pozo. Las cantidades entregadas se evaluaron con la ayuda de los albaranes de entrega de la planta dosificadora. Las cantidades instaladas se establecieron mediante imágenes de escáner láser. La determinación de la diferencia entre el escaneo de la superficie de shotcrete terminada y el escaneo del terreno excavado confirmó que se necesitaba aproximadamente un 30% de shotcrete adicional para rellenar la sobreexcavación. Esto, además de aproximadamente un 20% de rebote.
8 metros de diámetro y 30 metros de profundidad
Descripción del proyecto
El pozo de rescate del túnel Füllbach, un túnel ferroviario de una vía cerca de Coburgo, en Alemania, tiene una profundidad de 30 metros y sirve como una ruta de escape del túnel principal, que posee una extensión de 1,1 kilómetros. Con un diámetro de excavación de poco menos de 9 metros, el espacio disponible permitió el uso de máquinas más potentes. La excavación se llevó a cabo completamente con el método de perforación y voladura, con el subsecuente soporte de shotcrete. El primer revestimiento consistió en una cáscara de shotcrete de doble capa con un espesor de 200 mm y una doble capa malla de acero soldada de refuerzo. El área de superficie total de shotcrete fue de aproximadamente 815 m2.
Selección del método de rociado
Esto significó que se requirieron 14m3 de hormigón proyectado por tanda de excavación de 1,3 metros, los que se dosificaron en tandas por la planta dosificadora ubicada en el sitio de la obra y se entregaron mediante camiones para entrega de hormigón habituales. Debida a la alta cantidad requerida por ronda de excavación y el diámetro relativamente grande del shaft, se tomó la decisión de utilizar boquillas manipuladas de forma remota para la colocación del shotcrete.
Trabajos de construcción
Una vez preparada el área de preparación del sitio de la obra y construido el anillo de cabecera del pozo, pudo comenzar el hundimiento del shaft. Para los trabajos de perforación necesarios se utilizó una única plataforma de perforación de un solo brazo. La plataforma y las cajas de basura se subieron y sacaron con la ayuda de una grúa móvil de 60 toneladas (54 toneladas). El material suelto se excavó utilizando una excavadora compacta de 8 toneladas (7 toneladas). Para la aplicación del hormigón proyectado, se utilizó un manipulador de pulverización Normet AL-503, el que se caracteriza por su diseño compacto y largo alcance de hasta 8 metros. El suministro de hormigón se aseguró gracias a una bomba de hormigón Sika-PM702. El acelerador de fraguado rápido y el aire comprimido se agregaron en la boquilla. Con el sistema utilizado, podrían alcanzarse velocidades de rociado de hasta 15m3 por hora.
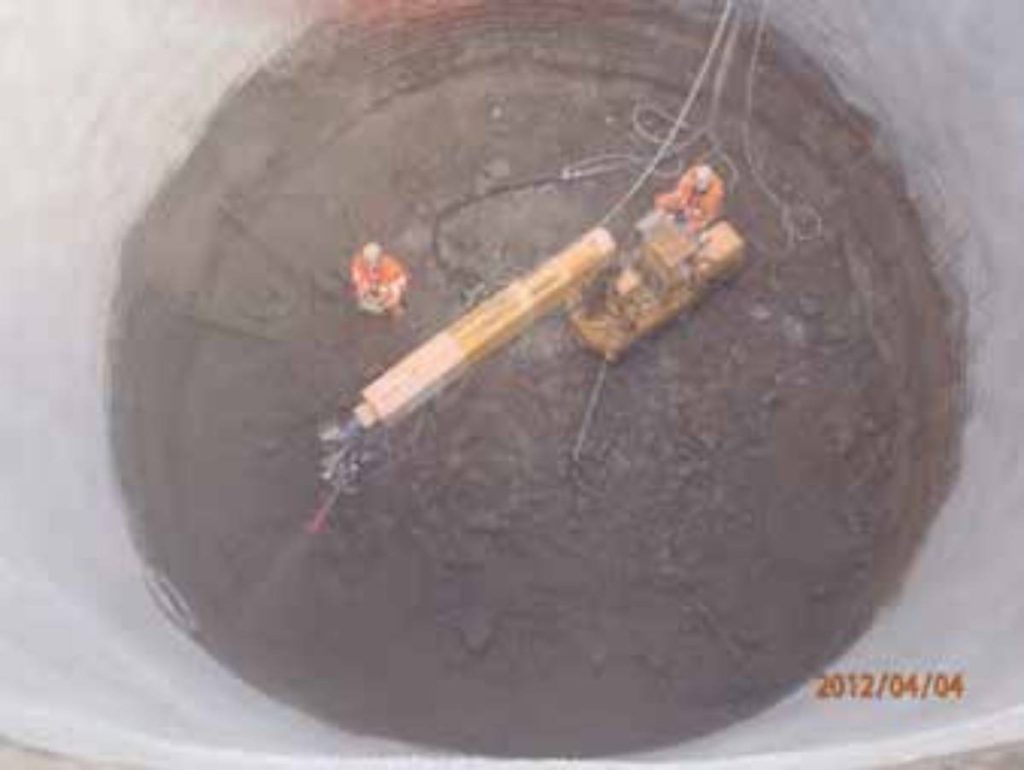
42 shafts con 3,4 metros de diámetro
Descripción del proyecto
Debido a los problemas existentes con el drenaje de aguas residuales durante evento de fuertes lluvias, actualmente se está construyendo un nuevo colector bajo la ciudad de Viena. El alcantarillado existente, que es demasiado pequeño, descarga las aguas servidas al río Wien durante los desbordes provocados por la tormenta, causando graves problemas sanitarios y medioambientales en la capital de Austria. La construcción del nuevo colector de Wiental tiene una extensión total de 8,6 kilómetros con un diámetro de 3,60 metros y se excavará completamente con una TBM (Tunnel Boring Machine). Para conectar las alcantarillas existentes y brindar acceso y opciones de rescate, se construirán un total de 52 pozos a lo largo del curso del alcantarillado. 42 de estos shafts se excavarán utilizando un tipo de construcción de pozo en terreno blando denominado Método de Excavación Secuencial (SEM, en sus siglas en inglés), además del sostenimiento con shotcrete. Dependiendo de las condiciones geológicas, en algunos lugares se realizará la mejora del suelo mediante inyección de lechada. Los mismos shafts tienen un diámetro de excavación muy pequeño, de poco menos de 3,5 metros, y una profundidad de 21 metros. El revestimiento primario se realiza con una cáscara de shotcrete de 300 mm de espesor y una o dos capas de refuerzo de malla de acero soldada. Se instalará un total de 7.000 m2 de hormigón proyectado. Después de la finalización de los trabajos, cada pozo tendrá un revestimiento final de 300 mm de espesor y las respectivas instalaciones interiores tales como las tuberías para conectar el alcantarillado y escaleras de acceso.
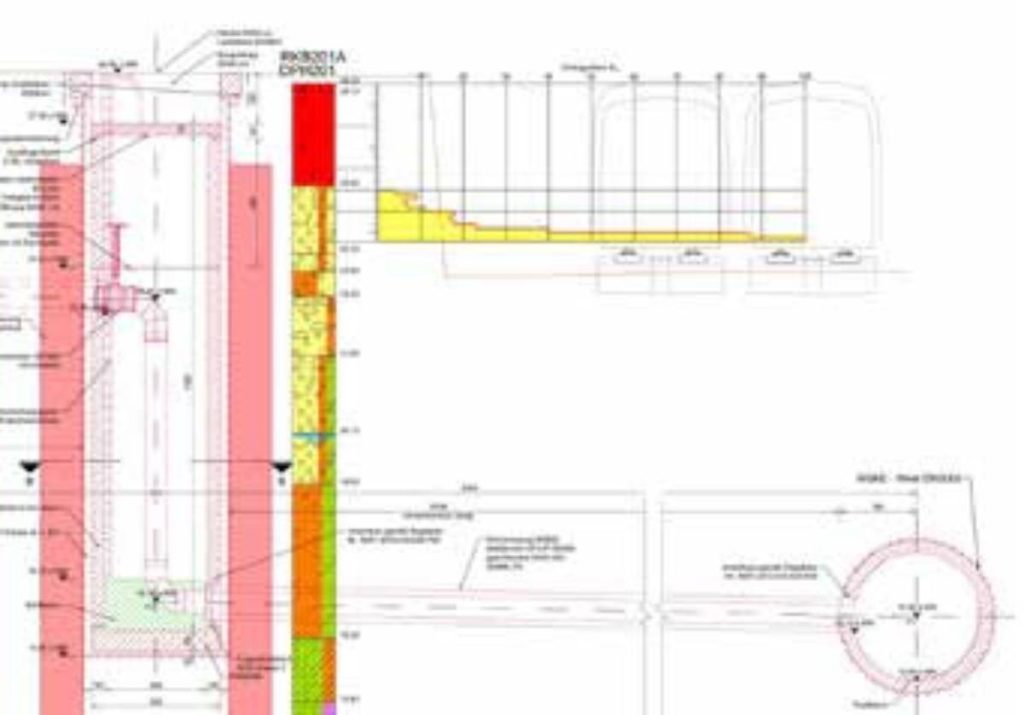
Estado actual de la preparación de la obra
Con la construcción comenzando en abril de 2024, el trabajo actualmente se concentra en la construcción de la plataforma de lanzamiento de la TBM y el trabajo de preparación para el proyecto. Ya se han realizado las primeras consideraciones sobre la excavación de los shafts. El trabajo de excavación se planificó para que se ejecute utilizando una excavadora ubicada en la superficie y equipada con un brazo telescópico y una pala hidráulica de agarre. Los trabajos de excavación correctivos en el fondo del shaft se llevarán a cabo utilizando una miniexcavadora. Se utilizará una grúa móvil para logísticas y para levantar equipamiento dentro y fuera del pozo. A efectos de programación, serán necesarios un total de tres equipos para poder trabajar en varios pozos al mismo tiempo. Comenzando con un shaft a la vez en la fase inicial, se planea construir tres shafts de manera simultánea durante las etapas posteriores.
Selección del método de rociado
Lo que es interesante y, al mismo tiempo, desafiante sobre este proyecto es el gran número de shafts similares con muy pequeños diámetros de excavación. Además, el tamaño de las áreas de preparación individuales del sitio es muy limitado debido a la ubicación dentro de la ciudad y el poco espacio de maniobra. Con una cantidad de hormigón proyectado requerida de menos de 3 m3 por tanda de excavación y las situaciones de difícil acceso, aún se discute si se utilizará shotcrete de mezcla seca o húmeda.
Debido a los edificios residenciales colindantes y a las transitadas calles, una de las mayores preocupaciones es la gran cantidad de polvo que, potencialmente, se puede generar durante la proyección de shotcrete de mezcla seca. Por otro lado, el hormigón proyectado de mezcla húmeda no es la solución más económica debido a las pequeñas cantidades requeridas y al limitado espacio disponible. Además, el shotcrete de mezcla húmeda debe entregarse siempre por un vehículo de reparto de premezclado, mientras que los materiales del shotcrete secados al horno pueden acopiarse en grandes silos in situ y están disponibles en todo momento. La decisión final se tomará durante los ensayos de rociado en el primer pozo. En este tiempo, también se optimizará aún más el concepto de la máquina.
Se tomará especial atención al traslado de los equipos de la obra, ya que aquí se puede ahorrar gran mucho tiempo de trabajo debido a los números procesos de reubicación desde un pozo excavado al siguiente.
Debido a las condiciones de trabajo muy estrechas en el shaft, con sólo 3,6 metros de diámetro, el shotcrete se aplicará de forma manual. Por lo tanto, probablemente se utilizará una pistola eléctrica rotativa Aliva (por ejemplo, la Aliva 262), que transporta al hormigón proyectado de forma neumática a través de la manguera de suministro. La ventaja de este sistema es que se puede utilizar tanto para shotcrete de mezcla húmeda como seca.
Conclusión
Los shafts construidos con shotcrete a menudo presentan desafíos únicos para los proyectos. En muchos casos, el método constructivo es diferente al que se utilizó para el túnel principal (Frecuentemente, utilizando una TBM), presentando desafíos en el reclutamiento de personal con experiencia y certificado para trabajos en pozos. Las condiciones de la superficie y las ubicaciones de los shafts son, muchas veces, estrechas, presentando desafíos no sólo para el suministro del material, la descarga de residuos y los movimientos de los equipos, sino también con respecto a cuestiones medioambientales como el control del polvo y del ruido. Los representantes de los proyectos deben poner especial atención en estas circunstancias especiales desde el inicio, para poder hacer frente a estos desafíos.
Referencias
1. OEBV Guideline Sprayed Concrete. Austrian Society for Construction Technology OEBV. Vienna. 04/2013.
2. European Standard EN 14487-1 Sprayed concrete – Part 1: Definitions, specifications and conformity. CEN European Committee for Standardization. 2022.
3. Kusterle, Jäger, John, Neumann and Roeck (2014). “Spritzbeton im Tunnelbau”, Betonkalender 2014.
4. Hoefler, Schlumpf and Jahn. (2020). “Sika sprayed concrete handbook”, Sika Services AG.