El trabajo que la firma COST de Wisconsin realizó, utilizando shotcrete de forma innovadora para el proyecto, además de su experiencia con esta metodología constructiva, resultó clave para crear este nuevo espacio en uno de los museos más importantes de la ciudad. Este artículo se publicó originalmente en el volumen 26, número 1 de la revista Shotcrete Magazine, de la American Shotcrete Association, en enero de 2024.
Autores: Martin Palicki y Jared Stanwyck
Es extraño que el diseño de una edificación pueda transformarse en algo icónico de manera inmediata – una atracción en sí mismo. La Sagrada Familia de Gaudí es un buen ejemplo de ello. Es un festín visual – una escultura que toma la forma de un edificio. Muchos críticos arquitectónicos están diciendo lo mismo del recientemente inaugurado Centro Gilder en el Museo Estadounidense de Historia Natural (AMNH, en sus siglas en inglés) en la ciudad de Nueva York.
Oficialmente bautizado como el Centro Richard Gilder para la Ciencia, Educación e Innovación, la incorporación al AMNH es la guinda de un pastel muy prestigioso. El AMNH contó con 5 millones de visitantes en 2019 (el año más reciente en el que el índice TEA/AECOM clasificó a los museos). Es el noveno museo más visitado del mundo y en Norteamérica, es el segundo detrás sólo del Museo de Arte Metropolitano (MET), que también se encuentra en la ciudad de Nueva York.
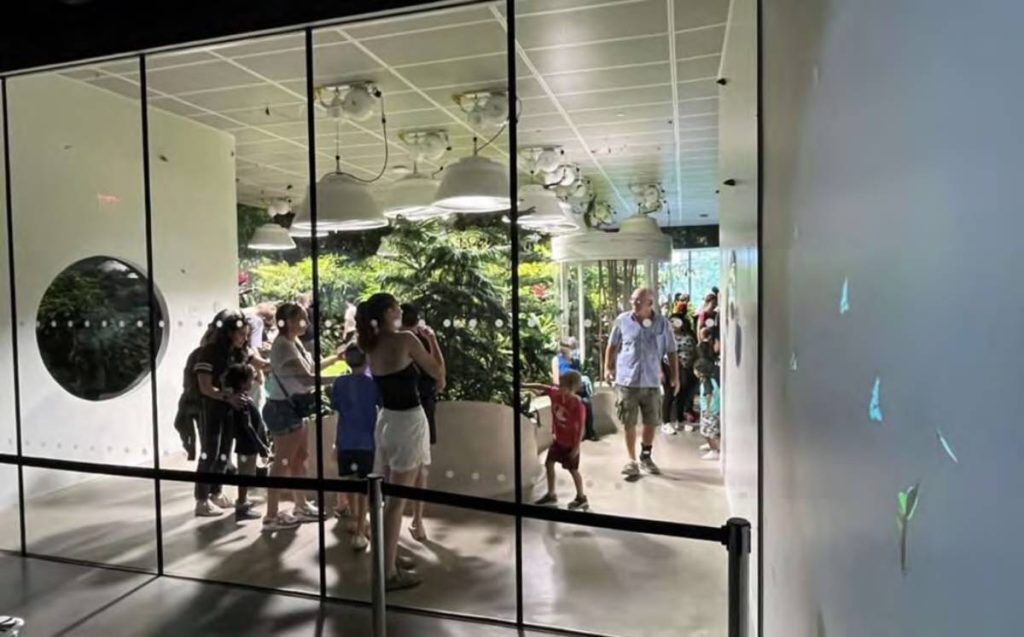
El Centro Gilder es una ampliación de 21.400 m2 que cuenta con 33 conexiones individuales, abarcando cuatro niveles, a otros 10 edificios del campus del AMNH. Además de ayudar en la unificación del museo, Gilder alberga exhibiciones impresionantes, incluyendo un insectario, el vivero de mariposas de la Familia Davis, la muestra de nuevas colecciones y la experiencia inmersiva de “Invisible Worlds” -un entorno mapeado por proyección que lleva a los visitantes a reinos científicos y naturales casi imposibles de observar bajo circunstancias normales.
El edificio en sí mismo también captura mucha de la atención y fanfarria de este nuevo espacio. Diseñado por el estudio de arquitectura Studio Gang, el edificio es curvilíneo y fluido. O, en lenguaje arquitectónico, no rectilíneo. El exterior orientado al oeste cuenta con ventanas de cristal que se asoman desde formas onduladas y suaves de granito rosa.
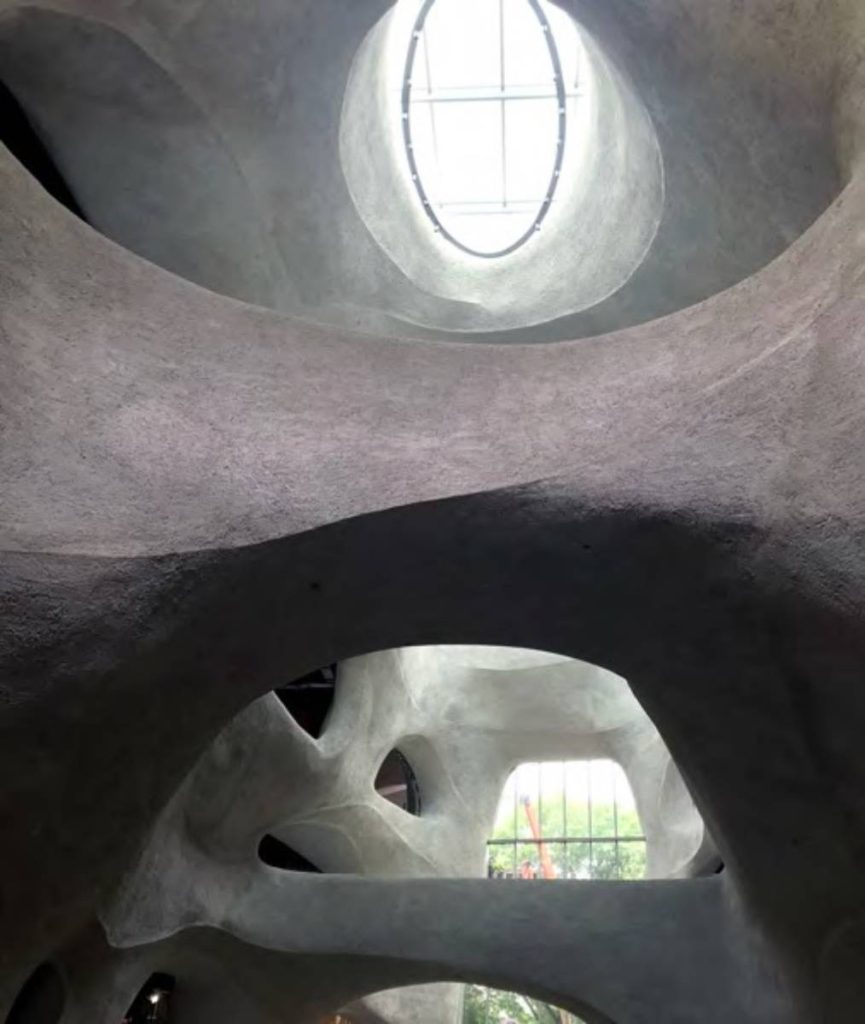
El vestíbulo del atrio interior, con sus 24 metros de altura, evoca a un cañón y se fabricó con un material que recubre prácticamente todas las superficies, aplicado de maneras novedosas. Las aberturas hacia los espacios de exhibición y los puentes que cruzan el atrio son amorfas -no se repite forma alguna en el diseño. El acabado es blanquecino y, aunque el material principal es hormigón, el efecto es orgánico y casi como mirar un hueso a nivel microscópico con sus grietas y tendones que se extienden por todo el espacio.
Las habilidades para construir
Llegar con un diseño de esta magnitud requiere de talentos específicos, pero averiguar cómo construirlo, eso es una habilidad completamente distinta. AECOM Tishman, director de construcción y contratista general, recurrió a COST -una firma de Wisconsin- para que le ayudara a crear este edificio, así como los medios y métodos constructivos para el proyecto. Le asignaron al presidente de COST, Mike Schmuhl, y a su vicepresidente, Greg Marks, una función única de asistencia en el diseño. En lugar de simplemente tomar planos y construirlos, COST jugó un papel crucial en el equipo para determinar (o ayudar) cómo se lograría la visión del arquitecto.
Con base en Jackson, Wisconsin, y con oficinas en Orlando, FL, y Berryville, AR, COST-Inc lleva brindando servicios de construcción temáticos y especializados para proyectos alrededor del mundo desde 1957. Aunque su trabajo puede apreciarse en diversos ambientes, desde edificaciones comerciales a recreacionales y ambientes residenciales, la oficina es quizás más conocida por su trabajo en espacios de atracción temáticos.
De hecho, la compañía se fundó para crear hábitats animales realistas en el Zoológico del Condado de Milwaukee en una época cuando los recintos para animales se estaban reinventando para que fuesen menos como jaulas y más como ambientes naturales. COST es conocida por la atención al detalle en su fabricación y proyectos recientes incluyen el trabajo en el Parque Temático Lost Island, la Estación Meow Wolf Convergence (en Denver) y la Cala del Hipopótamo en el Zoológico de Cincinnati, hogar de Fiona, hipopótamo conocido en el mundo entero.
Gilder brindó a COST la oportunidad de exhibir sus habilidades más allá de la temática decorativa, uniendo diseño, ingeniería, fabricación y arte de nuevas maneras. “Estábamos muy entusiasmados de ser parte del equipo que creó este proyecto épico, el que perdurará durante las generaciones venideras”, dijo Jeff Sheiber, vicepresidente de ventas en COST. “Estamos agradecidos de que el Museo Estadounidense de Historia Natural, AECOM Tishman y Studio Gang confiaran en que teníamos las habilidades únicas necesarias para lograr su visión”.
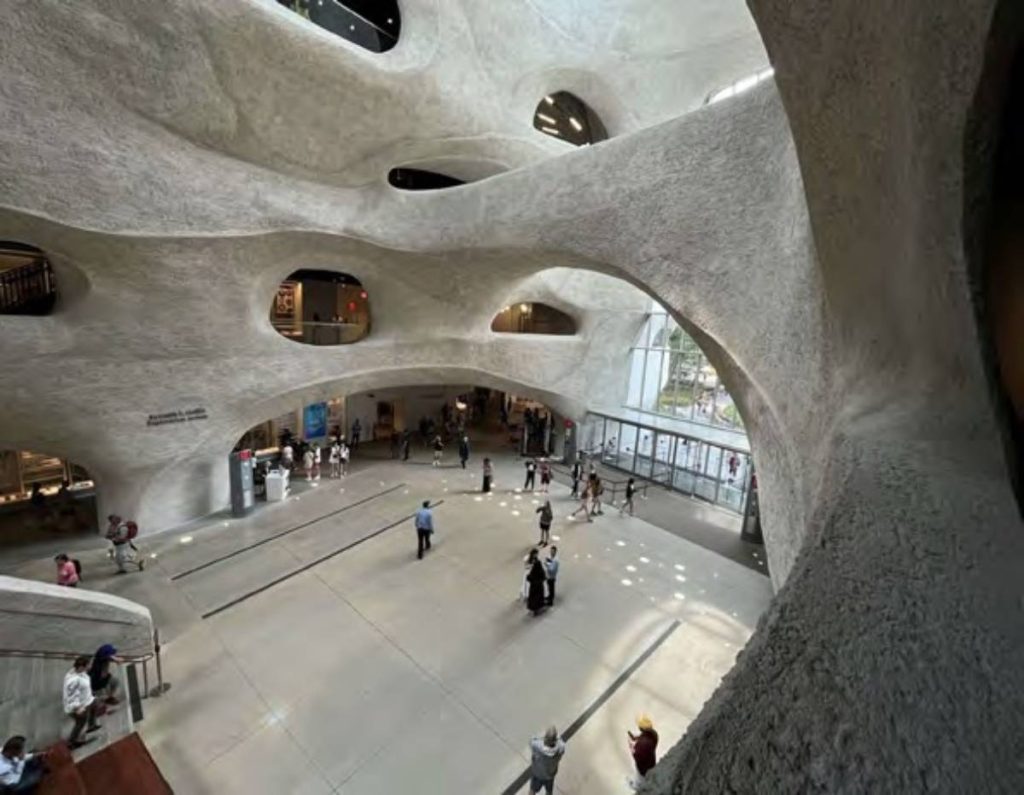
Fabricación innovadora
La visión y el mandato resultaron claros: crear un edificio con un mínimo de líneas derechas y ángulos rectos y donde no se repitan las formas. Y claro, sin uniones visibles.
“El museo y los diseñadores sabían la forma que querían para el edificio, pero no estaban exactamente seguros respecto a cómo hacerla”, dijo Sergio Castro, senior manager de COST en Wisconsin. “Fue una verdadera colaboración mental entre el grupo de ingeniería, el museo, los directores de construcción y nosotros en COST-Inc”.
El equipo de diseño en COST, liderado por Kaleigh Warren, directora de diseño, con el apoyo de Schmuhl, determinó que los encofrados tradicionales no serían los apropiados para el proyecto. Ese método generalmente se basa en verter hormigón dentro de moldajes de madera contrachapada o terciada, que son complejas de convertir en formas suaves y redondeadas.
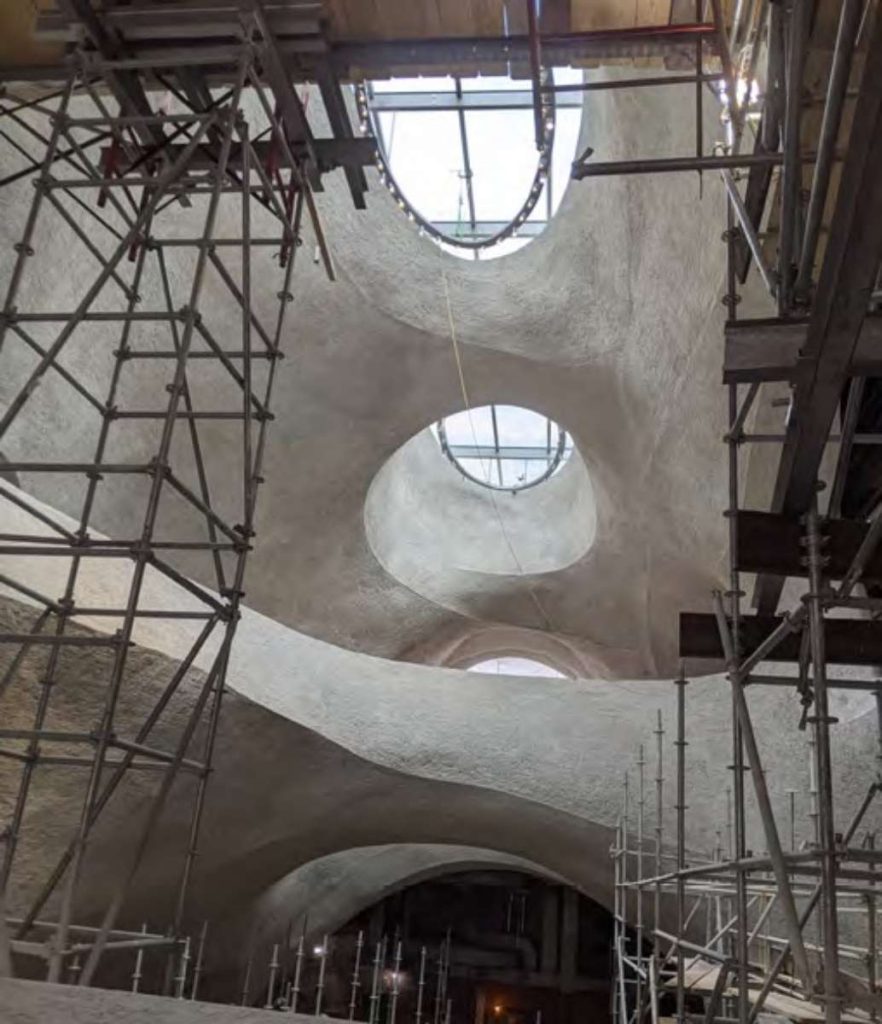
La solución fue utilizar una mezcla húmeda de shotcrete, una metodología bien establecida de rociado de una mezcla cementosa sobre una malla de barras de refuerzo. El shotcrete -u hormigón proyectado- se utiliza comúnmente para muros curvos en túneles. También, en decoración de rocas, tales como parques temáticos o hábitats de animales. Para Gilder, sin embargo, la aplicación debía funcionar como una mezcla entre ambas. El shotcrete debía entregar el soporte estructural de un túnel, como también, la estética y acabado de decoración de rocas. La gran experiencia de COST con el shotcrete resultó perfecta para el proyecto.
Como prueba de concepto, bajo el liderazgo de Schmuhl, COST fabricó una muestra para que la examinaran el contratista general y Studio Gang. “Creamos una sección del modelo en nuestro taller para demostrarle al equipo que podíamos ejecutar su visión”, comentó Castro. “Y funcionó”.
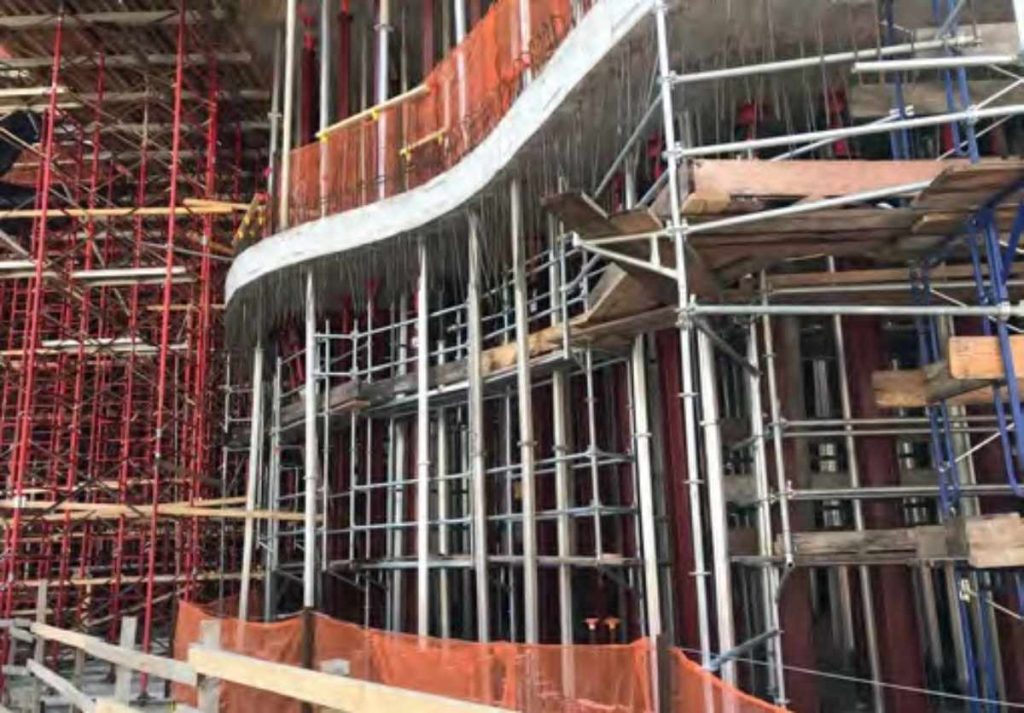
“Nos enorgullecemos de poder encontrar nuevas formas para abordar los problemas y observar el proceso de fabricación desde diferentes aristas”, puntualizó Sheiber. “Gilder muestra que, con el enfoque adecuado, efectivamente puedes combinar constructibilidad, longevidad y estética en un proceso”.
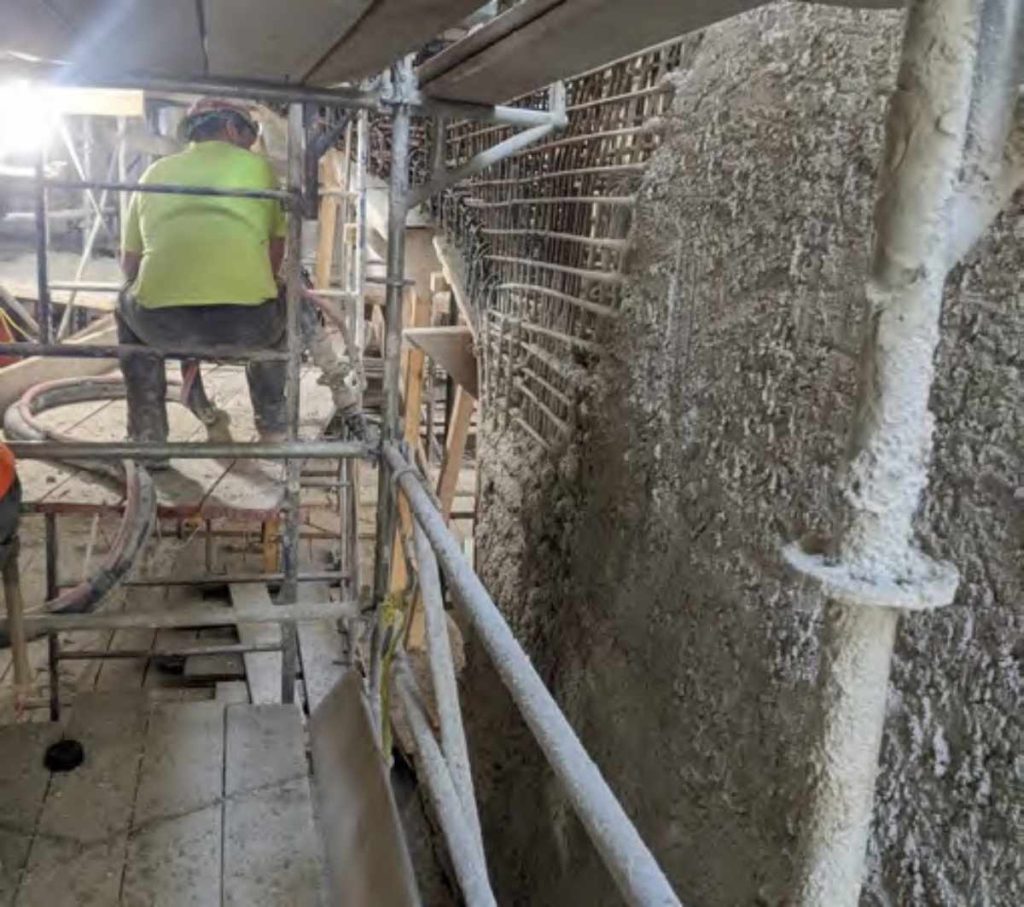
La odisea de las barras de refuerzo
Para crear las formas únicas de la estructura, COST diseñó, fabricó e instaló encofrados tubulares y las barras de refuerzo. Los moldajes con forma de tubo actuaron como una guía básica y punto de montaje para las barras, las que luego se rociaron con shotcrete.
Bajo el liderazgo de Bobby Lynch y Randy Ferguson, gerentes en COST, y con el apoyo de Corey Rabbitt, director de operaciones de campo, la construcción comenzó en el sitio con la fabricación de columnas perimetrales y losas de piso de hormigón fabricadas de forma convencional.
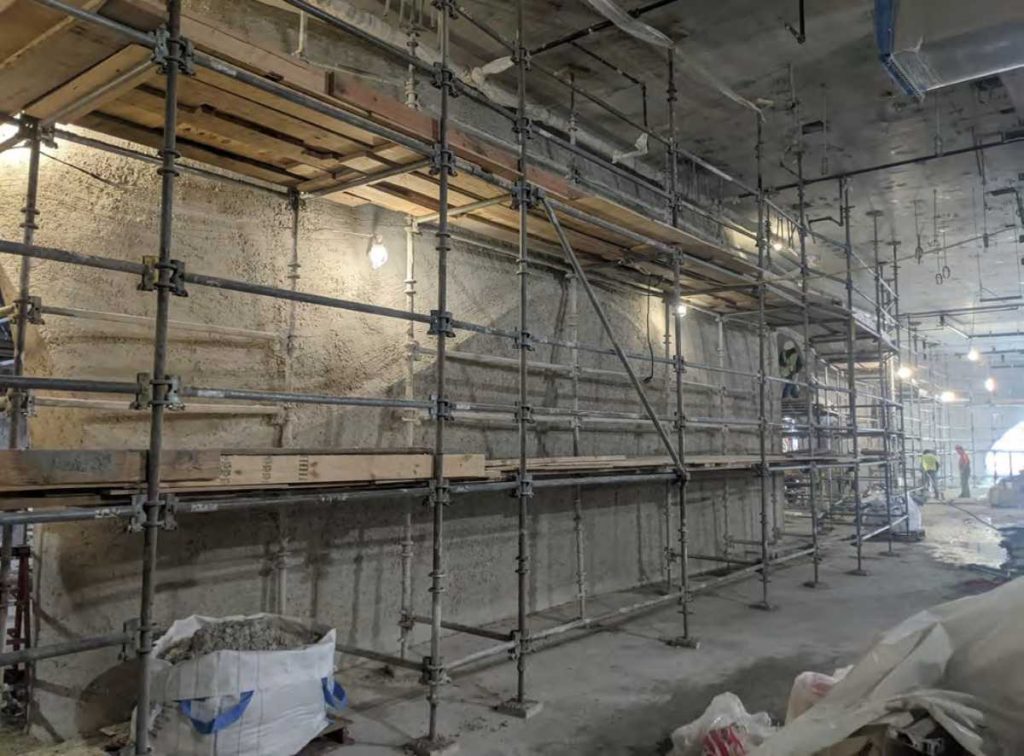
A continuación, se diseñaron de manera individual más de 900 moldajes tubulares, los que se fabricaron en Wisconsin, se identificaron y luego, se despacharon al lugar de la obra. Debido al patio de servicios existente debajo, el diseño estructural de los muros del cañón requirió de rutas de carga en sólo seis puntos de aterrizaje principales. La instalación de estos encofrados tubulares fue el primer gran paso para darle vida al Centro Gilder.
Cada moldaje con forma de tubo fue inspeccionado meticulosamente en su lugar y jugó un rol clave en el proyecto. Sostuvieron cada losa de piso de placa plana (que se sostenía mediante apuntalamiento dinámico) y también actuaron como una guía básica y punto de montaje para las barras de refuerzo. Los separadores en los moldajes tubulares se codificaron y etiquetaron con colores.
La necesidad de 453 toneladas de barras de refuerzo (también fabricadas en Wisconsin bajo la guía de Jamie Ehlke, director de tienda) se extrajo de numerosos modelos computacionales en 3D; las barras se etiquetaron con números de identificación que coincidían con los bosquejos creados por el equipo de diseño de COST. Más de 50 semirremolques viajaron desde Wisconsin a Brooklyn, donde se instaló el sitio de acopio antes de que las piezas se llevaran al lugar de la obra.
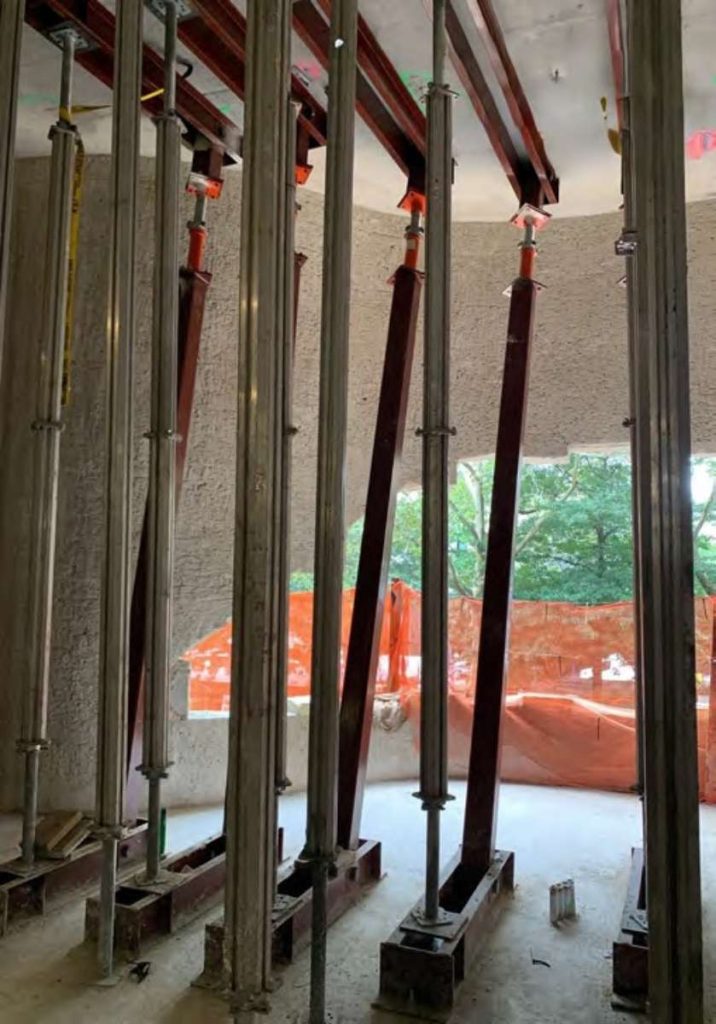
“El espacio en el sitio en el centro de Manhattan fue extremadamente limitado”, explicó Castro. “La logística necesaria para traer los componentes al lugar tuvo que ser precisa. No teníamos espacio en el sitio para almacenar materiales, por lo que tuvimos que traerlos directamente desde el patio de preparación de forma coordinada”.
Los tubos se anclaron a las losas y cada pieza individual de las barras de refuerzo se unió al moldaje tubular. Luego, se inició el trabajo de aplicación del shotcrete. Los equipos trabajaron en secuencia; a medida que se completaron las secciones de tubos y barras de refuerzo, los equipos de shotcrete se hicieron cargo y el proceso continuó.
Shotcrete como nunca antes
COST utilizó dos mezclas diferentes de shotcrete para el Centro Gilder. La primera fue una capa estructural gris, que le brindó estabilidad estructural al edificio. Se aplicó como primera capa sobre las barras de refuerzo, de acuerdo con lo requerido por el ingeniero. A la capa estructural le siguió otra de acabado blanco, la que también produjo cualidades estructurales adicionales para el edificio, pero que no era necesaria para la ingeniería de la edificación.
La aplicación se llevó a cabo mediante una bomba rociadora de shotcrete, controlada por los operadores de boquilla de COST Mike Tower y Steve Thomas (certificados por ACI), en una secuencia de disparo previamente planificada. Esto fue necesario para crear la estética específica del complejo, como lo requirió Studio Gang. Los equipos comenzaron a rociar la capa gris desde la base y avanzaron hacia arriba. Debido a la cantidad de apuntalamiento dinámico colocado, el espacio era extremadamente limitado hasta que la capa estructural se completó y fue capaz de soportar la carga.
El espesor de la capa de acabado se revisó previo a su finalización para garantizar que no hubiera peso adicional no deseado sobre el edificio. Una vez confirmado el espesor correcto, COST aplicó una técnica de aplicación con pala irregular sobre la superficie del acabado para lograr la apariencia final. El color blanco se consiguió a través de la adición de un cemento blanco Tipo I a la mezcla. No se utilizaron ni pinturas ni tintes en la superficie.
El exterior del edificio se manejó de una forma algo distinta. No había columnas perimetrales para el muro exterior de la cara oeste. En vez de ello, COST elaboró una serie de paneles de barras de refuerzo prefabricados en vez de piezas individuales de barras, como se hizo para el interior. El shotcrete se aplicó de forma tradicional y puede verse expuesto en el interior del muro. La superficie exterior se cubrió con paneles de granito, los que se colgaron sobre placas metálicas que se incrustaron en el shotcrete.
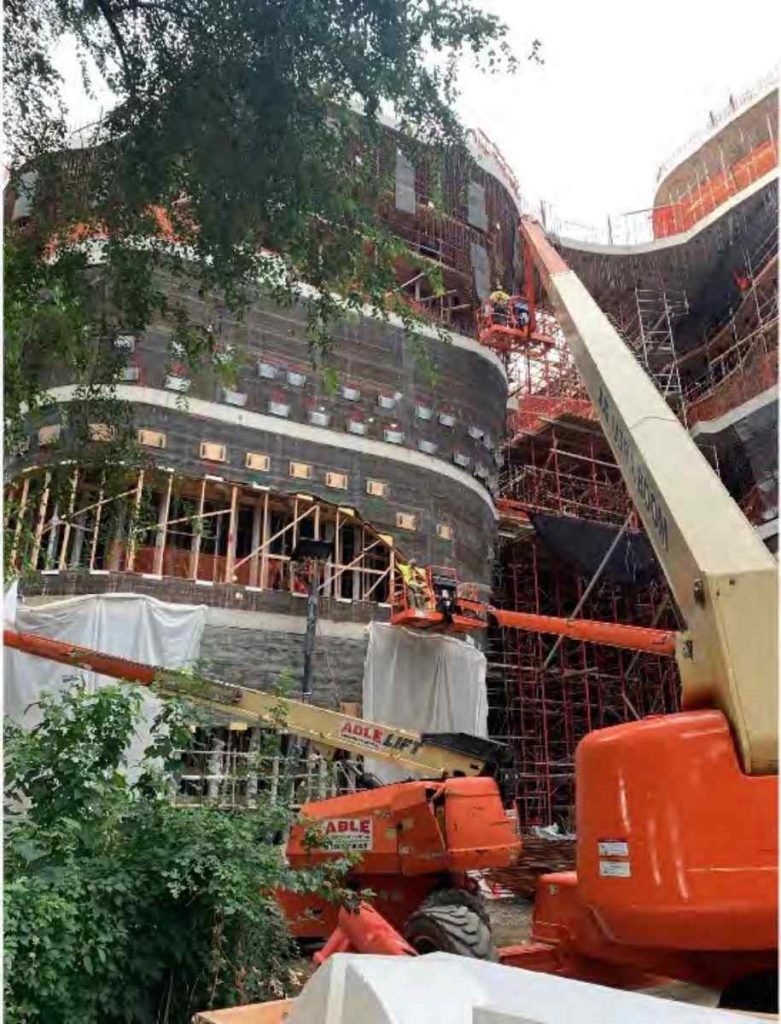
“Los paneles de granito tenían una tolerancia de variación extremadamente pequeña. Los paneles prefabricados de barras de refuerzo que produjimos en Wisconsin nos dieron mayor control sobre la geometría y permitieron que otros colgaran fácilmente el granito exterior”, explicó Castro.
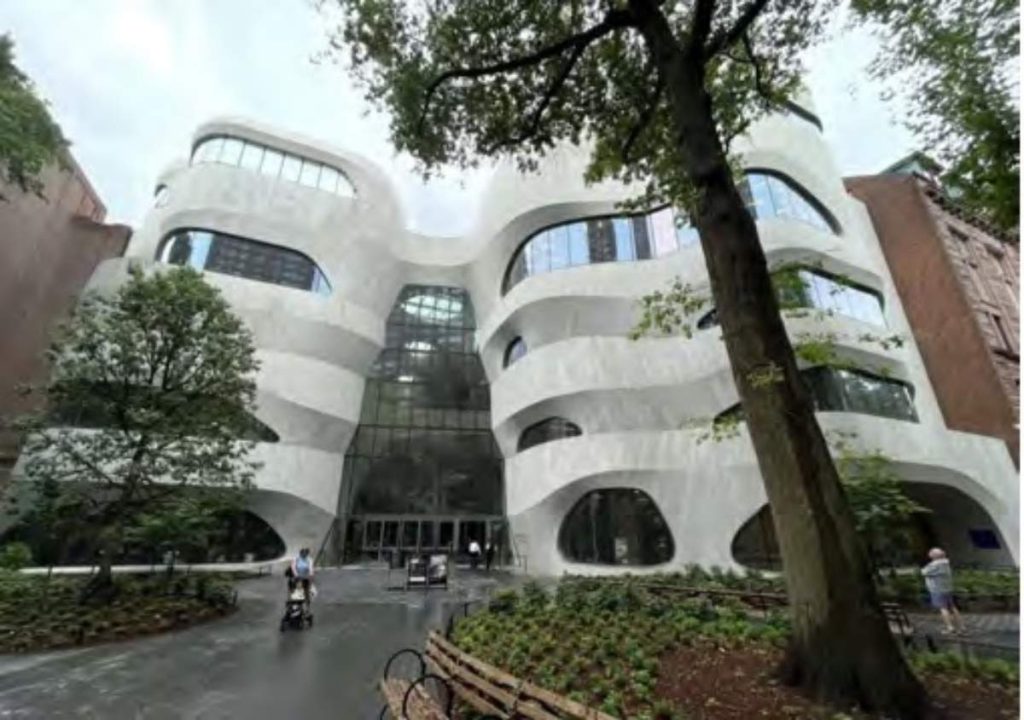
El edificio ya finalizado abrió sus puertas el 4 de mayo de 2023 y desde esa fecha, viene cautivando a tanto los visitantes del museo como a los amantes de la arquitectura.
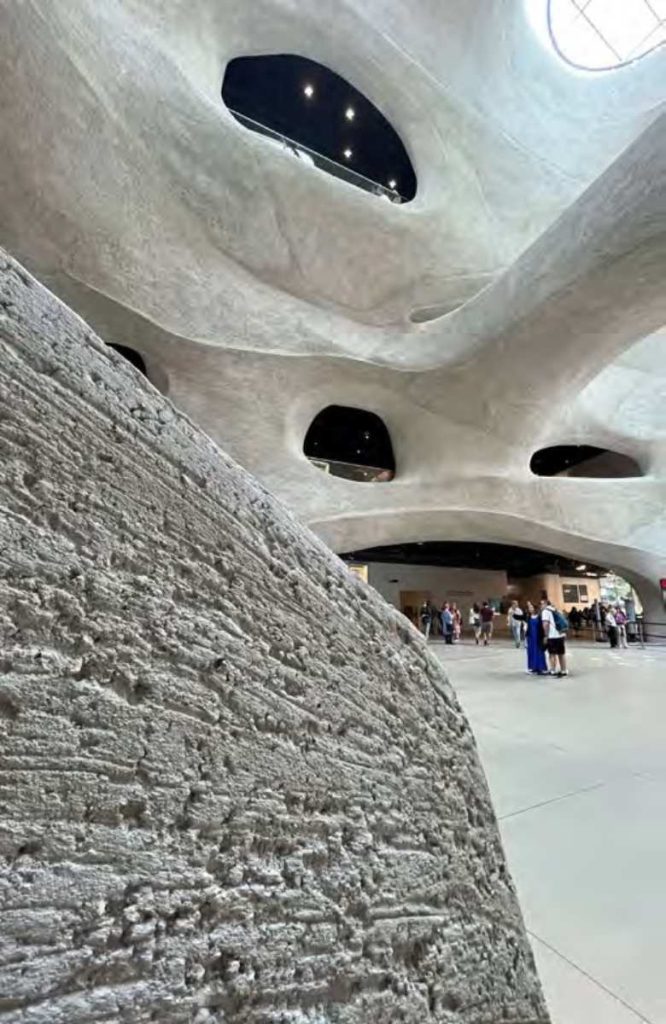
“El producto terminado evidencia que COST conoce las barras de refuerzo y sabe de shotcrete y fuimos capaces de hacer prácticamente todo con estos elementos”, dijo Castro. “Bien a menudo, los profesionales de los parques temáticos observan estas herramientas y sólo piensan en lo bonitas que son estas obras de roca. ¡para las que, por supuesto, son excelentes! Pero sus capacidades superan la temática arquitectónica y pueden utilizarse de formas realmente innovadoras para construir lo imposible”.
Ficha técnica
- Proyecto: Museo estadounidense de Historia Natural (AMNH), Centro Gilder.
- Ubicación del proyecto: Nueva York, NY.
- Contratista de Shotcrete: COST de Wisconsin Inc.
- Arquitectura/Ingeniería: Studio Gang.
- Fabricante de equipos: REED equipos para shotcrete.
- Suministrador de materiales: Tec-Crete Transit-Mix Corp.
- Contratista general: AECOM Tishman.
- Mandante: AMNH.