Aunque su uso se remonta a comienzos del siglo XX, no fue después de la Segunda Guerra Mundial cuando el bombeo del hormigón a edificaciones comenzó su desarrollo más progresivo, alcanzado en la actualidad alturas que llegan por sobre los 606 metros y que, dada la tendencia a edificios cada vez más altos, sigue evolucionando gracias al desarrollo de nuevos y potentes equipos. Este artículo se basa en la presentación “What are we going to pump that with”? que realizó Eamonn Connolly, máster en Ingeniería, Geotécnica e Ingeniería Estructural de la University of Aberdeen e ingeniero estructural en McHugh Construction, durante una de las sesiones virtuales de la convención que el American Concrete Institute llevó a cabo entre el 28 de marzo y el 1 de abril de 2021.
A medida que la construcción con hormigón avanza hacia las alturas, con torres que se elevan por sobre los 30 pisos, uno de los aspectos más críticos del proceso -y, al mismo tiempo, de los más poco abordados- dice relación sobre cómo bombear al hormigón de manera tal que esta faena se realice de forma óptima, asegurando que el material no presente inconvenientes a la hora de trabajarlo en edificaciones de gran altura.
El bombeo del hormigón y la capacidad de esta tecnología para colocar el material en altura no es nuevo y, prácticamente, viene experimentando una evolución constante desde la década de 1910, cuando es posible encontrar las primeras patentes de este tipo de equipos en Alemania.
Para Eamonn Connolly, máster en Ingeniería, Geotécnica e Ingeniería Estructural de la University of Aberdeen e ingeniero estructural en McHugh Construction, el verdadero desarrollo de la tecnología de bombeo del hormigón vino después de la Segunda Guerra Mundial. “La devastación del entorno generó una necesidad socioeconómica urgente de reconstrucción rápida y eficiente, lo que generó el desarrollo de nuevas tecnologías”, comentó.
“Lo que marca la diferencia en la construcción con hormigón es el desarrollo de las mezclas del material de alta resistencia, la eficiencia en los sistemas de bombeo y colocación, y la implementación de sistemas de encofrado que permitan un montaje seguro y rápido, con capacidad de reubicación eficiente”, agregó el ingeniero, citando a Stan Korista, un destacado ingeniero estructural, quien falleció en mayo de 2018.
Una primera aproximación a los equipos de bombeo de hormigón
“La necesidad es la madre de todas las innovaciones”, puntualizó Connolly. Por lo mismo, no resulta extraño que las principales mejoras e innovaciones en la tecnología de bombeo de hormigón nacieran en la Alemania post Segunda Guerra Mundial y que, como menciona antes el ingeniero, estas continuasen desarrollándose para hacer frente a los desafíos de la construcción en altura.
En ese sentido, Connolly explica que existen distintos tipos de bombas para hormigón. “Están las bombas neumáticas, cuyo uso es limitado y se utilizan principalmente en aplicaciones para shotcrete. Su funcionamiento se basa en un tanque de aire comprimido que empuja o proyecta al hormigón. Y, por otra parte, están las bombas de exprimir, cuyo sistema se basa en una cámara de vacío con un sistema rotativo que empuja el material”, explicó.
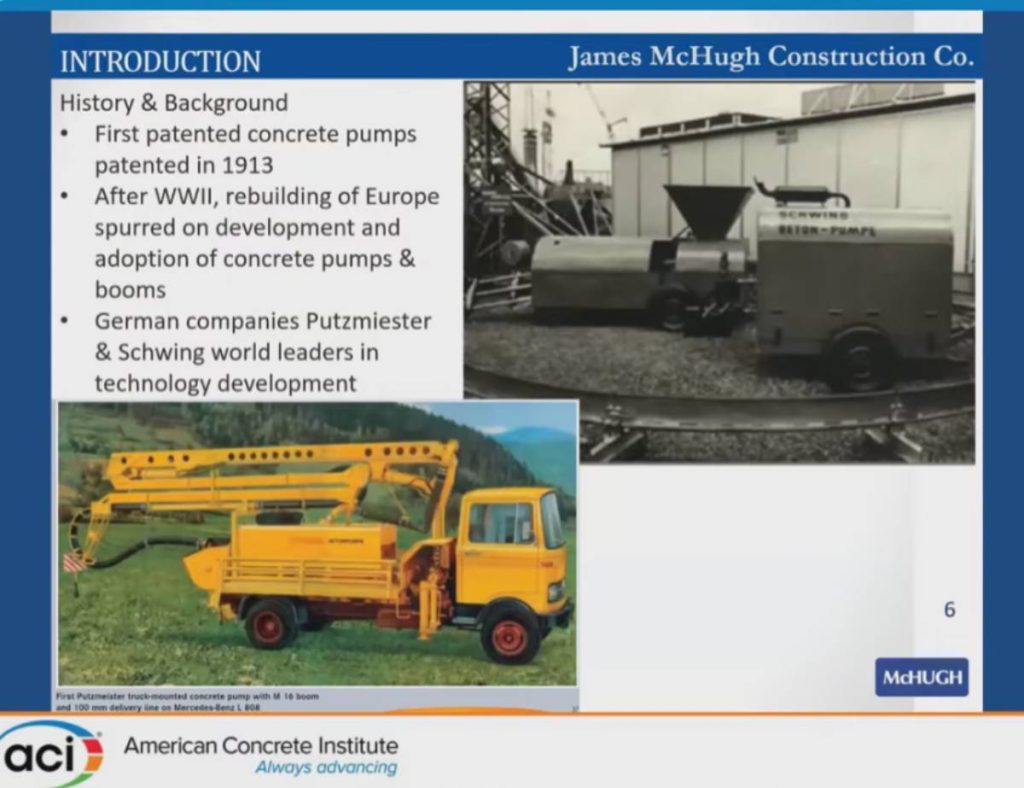
Este tipo de equipos, no obstante, es de alcance limitado tanto en distancia como en altura. En efecto, las bombas para hormigón basadas en el sistema de “exprimir” el material se utilizan principalmente construcciones de baja o mediana. “Las más comunes, sin embargo, son las bombas de pistón hidráulico. Estos equipos son los que se pueden ver prácticamente en cualquier faena”, aseguró.
El ingeniero estructural detalla que estas bombas tienen la capacidad de “colocar elevados volúmenes de hormigón a presiones extremadamente altas. Por ejemplo, la Putzmeister 14000 posee una capacidad de bombeo de 101,6 m3/h y opera a una presión nominal de 1.050 PSI, con un límite se seguridad de 1.750 PSI”, y agregó, en particular, que este equipo puede bombear hormigón a una altura en vertical de 600 metros. “Entiendo que el récord son 606 metros a una presión de 2.900 PSI, que se logró en 2008 durante la construcción del Burj Khalifa”, puntualizó el experto.
Funcionamiento del sistema de bombeo en altura
El funcionamiento de este tipo de bombas de hormigón -que Connolly destaca por su gran capacidad- consiste en “dos cilindros paralelos con pistones que operan de manera secuencial. Así, cuando un pistón retrocede, genera un vacío que succiona al hormigón desde la tolva, mientras el otro pistón avanza, impulsando hidráulicamente al material y empujándolo a través de una válvula hacia el sistema de tuberías”, detalló.
Gracias a este sistema, agrega el ingeniero, es posible bombear al hormigón a altas presiones, alcanzando también mayores alturas de colocación del material. “Gracias a estas características, el sistema puede trasladarse en ciclos muy rápidos”, destacó.
Para que este tipo de bombas -que, de acuerdo con lo que menciona el ingeniero, son las que trabajan mejor para el bombeo de hormigón para proyectos de gran altura- funcionen de manera óptima, se debe considerar la selección del tamaño del equipo y, especialmente, la configuración del sistema de tuberías que bombeará al hormigón.
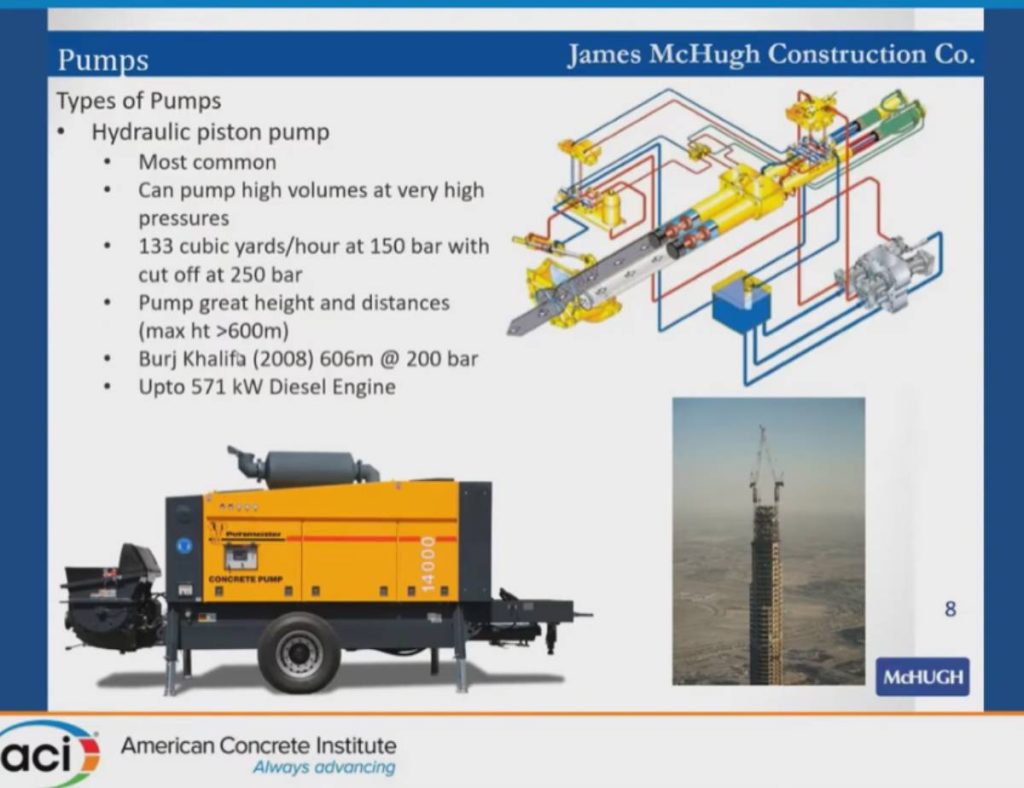
El mismo profesional confeccionó un diagrama –“básicamente, es una guía”, explicó– que considera una serie de elementos a la hora determinar cuál es la presión y el tamaño del bombeo del hormigón. Entre las variables que se encuentran en esta guía, se incluyen la tasa de flujo volumétrico, el diámetro de las tuberías o mangueras que bombearán al hormigón, la longitud del sistema (“esa longitud considera las curvas en 90 grados”, puntualizó), la altura vertical y las propiedades reológicos de la mezcla del hormigón.
De esta forma, de acuerdo con la herramienta que elaboró Connolly, la interacción de esas variables es clave a la hora de determinar, por ejemplo, la presión de bombeo y la ratio de potencia del equipo para un bombeo eficiente de hormigón. “Por ejemplo, si se coloca el hormigón a unos 45 m3/h, utilizando los parámetros que da el gráfico, debieses bombear el material a 171 PSI. Por el contrario, si se quiere realizar a 137 m3/h, la presión de bombeo debe ser de 614 PSI”, explicó.
El sistema de tuberías: elemento fundamental
Un punto crítico dentro del sistema de bombeo de hormigón lo constituyen las tuberías o mangueras que transportan al material. “Las tuberías es por donde se bombea al hormigón y se ven afectadas por los parámetros que comenté anteriormente”, dijo el ingeniero.
Las tuberías se hacen principalmente con acero especialmente fabricado para esta labor. Es decir, explica Connolly, deben soportar altas presiones, además de cargas cíclicas y tienen que estar diseñadas para material muy abrasivo para asegurar su reutilización, ya que producirlas encarece los costos. Para asegurar su vida útil, el ingeniero comenta que se deben llevar a cabo inspecciones continuas, mediciones visuales e instrumentales del grosor de las paredes de las tuberías y, especialmente, realizar un seguimiento de los metros cúbicos de hormigón que se bombean por esas tuberías.
En ese sentido, Connolly puntualizó que “para dar una idea de la expectativa de vida, la tubería de pared de media pulgada que se utilizó, por ejemplo, en el proyecto Vista, tiene una vida de 91.746 metros cúbicos de bombeo, mientras que una tubería con una pared de un cuarto de pulgada de espesor tiene una vida útil de 45.873 metros cúbicos de bombeo”.
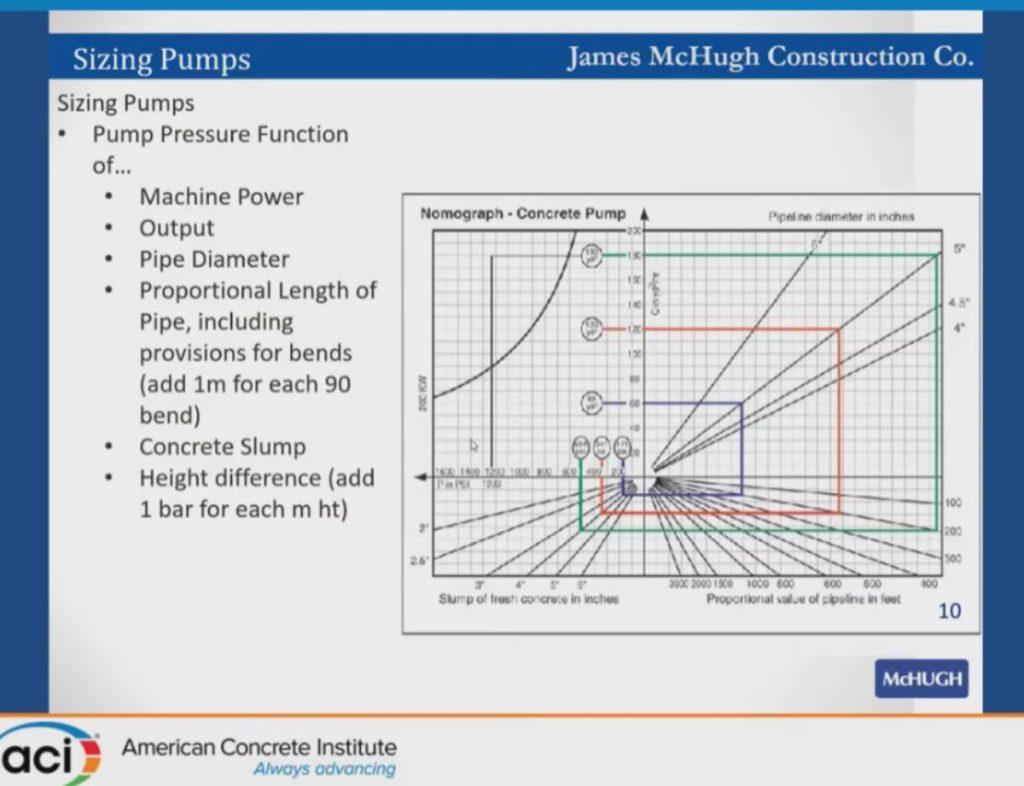
Otro aspecto es asegurar las tuberías por las que se bombea el hormigón, ya que cualquier movimiento o cambio de dirección puede afectar al material. Para ello, se deben asegurar las tuberías por lo que se utilizan puntales a lo largo del trayecto de las tuberías. “Cuando tenemos giros en 90 grados, se usan unos bloques que básicamente, encapsulan las esquinas en un bloque de hormigón, y cuando se regresa a la vertical, se agregan extensiones al núcleo de hormigón para que soporte la acción de todas las fuerzas involucradas en el proceso”, explicó.
Coordinación, diseños de mezcla y elementos esenciales
Cuando se busca extender una línea, ya una vez vertido el hormigón en un determinado sector, dice Connolly, lo que generalmente se hace es incorporar un pico de esponja, el que se inserta mediante un encaje especial con un compresor, en la parte superior de la plataforma de trabajo “y luego, utilizando otro compresor que se encuentra en la parte superior, básicamente empuja el punto de ensamblaje hacia abajo, a través de la misma tubería o manguera”, explicó.
Otro de los aspectos que destaca el ingeniero es la coordinación que debe existir entre los operadores de la bomba de hormigón y el equipo que esté en terreno, recibiendo el material. “La falta de comunicación podría causar accidentes graves en materia de seguridad y, potencialmente, la formación de burbujas de aire o la aparición de rocas en el hormigón que se bombea. Por este motivo, sólo operadores especializados en este tipo de equipos pueden operarlos”, puntualizó.
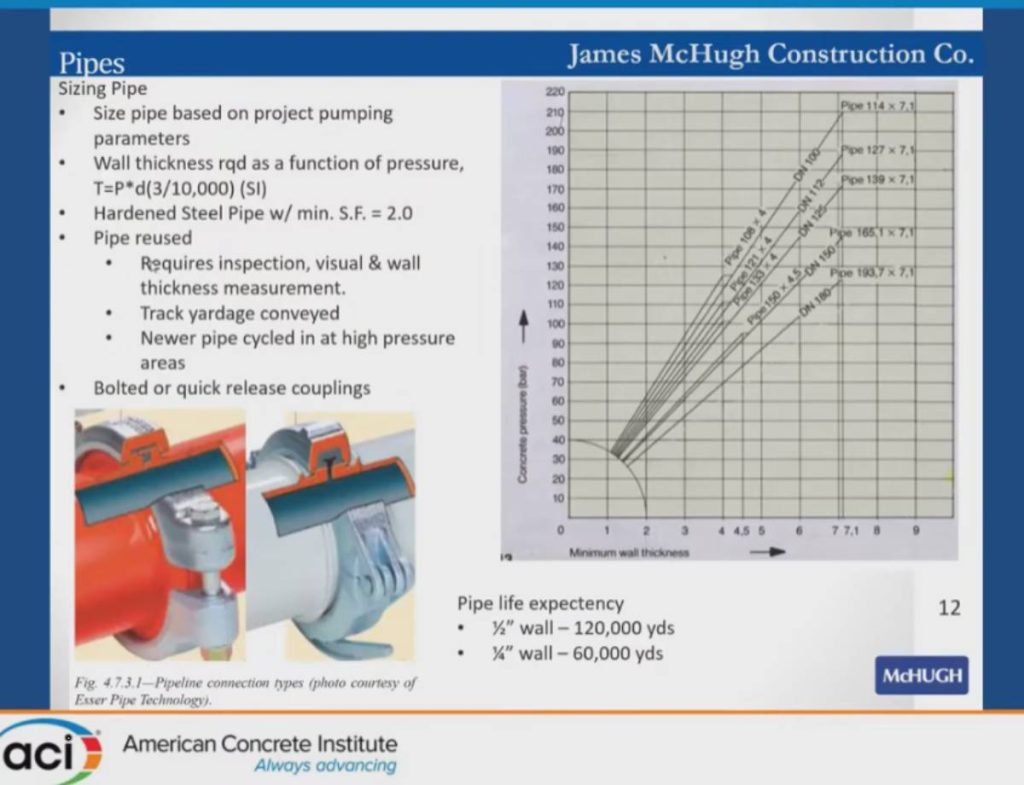
En otro aspecto, el ingeniero comenta que existen ciertos tipos de mezclas del hormigón que pueden resultar poco eficientes para el bombeo a grandes alturas, además de resultar complejas de limpiar. “Las mezclas con un módulo de elasticidad alto suelen ser problemáticas en ese sentido”, comentó el experto.
“Una de las soluciones que encontramos para ello es eliminar la mezcla de alto módulo de elasticidad a un balde y luego, mezclara con una mezcla de hormigón tradicional de baja resistencia. Una vez hecho eso, se limpia la mezcla original que está en la tubería con una esponja neumática y se vierte ese hormigón al balde”, agregó.
Logística: ¿dónde posicionar los equipos de bombeo?
Colocar el equipo que bombeará el hormigón a la altura deseada también es un desafío para los proyectos de gran altura, ya que su ubicación es vital para asegurar la eficiencia en la colocación del material. “Básicamente, la bomba que trasladará al hormigón debe colocarse con acceso fácil a la carretera, con espacio para al menos dos camiones mixer disponibles en todo momento, además de tener lugar para camiones extra adicionales”, recalcó Connolly.
Otro de los puntos que destaca el ingeniero es que, para tener una buena operación de bombeo del hormigón, es recomendable tener un tramo horizontal del 10% e incluso, 15% entre la bomba y la sección vertical donde se colocará el hormigón. “Esta configuración reduce las presiones operativas de la bomba y optimiza el rendimiento del sistema”, puntualizó.
Así, determinados estos aspectos, se debe analizar la forma en que se colocará el hormigón en el área de trabajo y, en ese sentido, el experto dice que uno de los equipos que se utilizan son las denominadas “placing boom”, maquinaria que consiste en un brazo articulado que puede expandirse y alcanzar una amplia área de trabajo. “Estos brazos pueden alcanzar grandes áreas de trabajo en altura, que van entre los 24 a 42 metros”, subrayó.
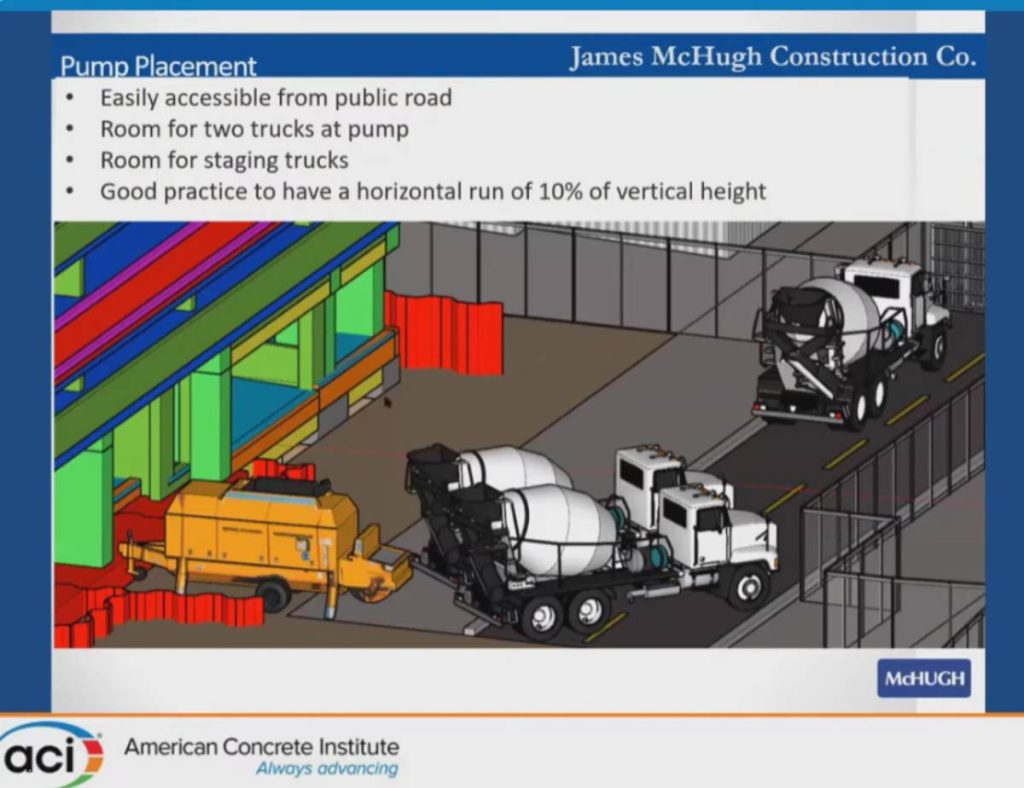
En ese sentido, el experto destaca que uno de los proyectos en el que participó se implementó esta tecnología. “En ese caso, se utilizó un sistema de distribución Putzmeister RS-850 con un brazo de colocación montado en la parte superior. Así, a medida que se avanzaba en altura del proyecto, el sistema de colocación se alzaba y volvía a posicionarse”, explicó.
“La ventaja de este sistema -añadió- es que se sustenta en las capacidades de elevación hidráulica de ese equipo. Esto quiere decir que, dado su propio diseño, es posible elevar el sistema sin la necesidad de una grúa auxiliar y, por ese motivo, se puede elevar con una ‘placing boon’ unida a su estructura”.
Por lo mismo, el experto subraya que esa característica representa un avance significativo en comparación con los métodos de bombeo tradicionales que, generalmente, requieren de una grúa para la elevación de la torre de bombeo de hormigón.
¿Cómo debe ser el hormigón a bombear?
Si bien el experto destaca una serie de elementos cruciales para el hormigonado en altura -y el rol que juega elección de equipos adecuados para esta labor- uno de los puntos más críticos en este tipo de faenas es, sin duda, la bombeabilidad del hormigón. “Garantizarla de forma consistente es el desafío primordial. La incapacidad de bombear hormigón a las tasas requeridas resulta en tiempos muertos significativos, que impactan negativamente en el cronograma y generando además una baja eficiencia en términos de costos”, comentó Connolly.
En ese sentido, el hormigón que se utilizará para el bombeo a grandes alturas debe diseñarse de manera cuidadosa, considerando factores como el tamaño y la morfología del agregado. “Su diámetro no debe ser más de un tercio que el diámetro de la tubería”, dijo el ingeniero y agregó que su forma también influye en la bombeabilidad del hormigón. “Agregados con formas angulares suelen ser más problemáticos que los redondeados”, aseveró.
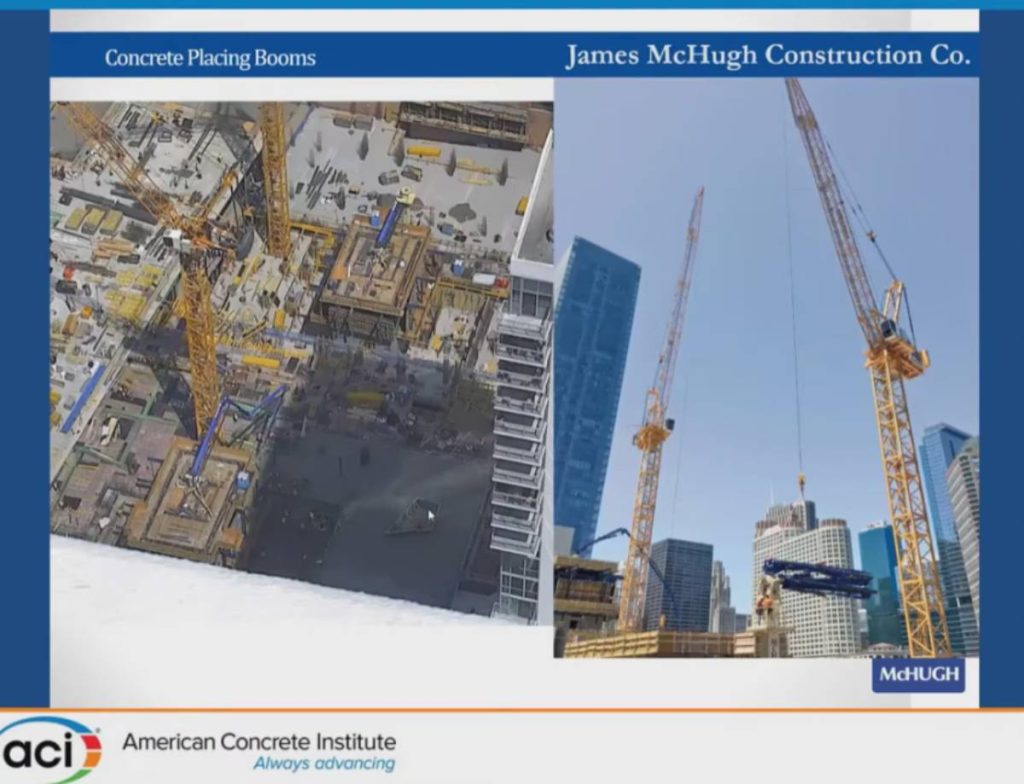
Según Eamonn Connolly, los agregados finos también colaboran en una mejor bombeabilidad del material y “es mucho mejor que sean naturales que artificiales”, dijo. En ese sentido, determinar el módulo de finura del árido se relaciona la bombeabilidad del hormigón. “Así, su el árido es demasiado fino, podría transformarse en un inconveniente”, advirtió el ingeniero.
Además, el experto agrega que la utilización de aditivos “que incrementan la trabajabilidad del hormigón, generalmente optimiza las características de bombeo del material”. En ese sentido, destaca el uso de aditivos superplastificantes, como también, de materiales cementosos suplementarios, como las cenizas volantes o la escoria. “Hay que tener este tipo materiales en cuenta, ya que mejoran la bombeabilidad del hormigón”, subrayó.
Otros factores críticos para la bombeabilidad del hormigón
Para el ingeniero, existen otros factores que deben considerarse a la hora de lograr una buena bombeabilidad del hormigón, permitiendo así una faena de colocación eficiente. Uno de estos, dice relación con el contenido de aire que debe tener el material a la hora de trasladar el hormigón en edificaciones de gran altura.
Al respecto, el ingeniero comenta que, si bien la pérdida de aire del hormigón puede ocurrir durante el proceso de bombeo, la recomendación es fijar una dosificación mayor de aire a la que realmente es necesaria en la mezcla inicial. En ese sentido, agrega que “hacer ensayos y tomar muestras de aire en el lugar de la colocación del hormigón es crítico. Todo comienza con un diseño de mezcla adecuado y ensayos de esa mezcla para asegurarse que todo funcione correctamente”, subrayó.
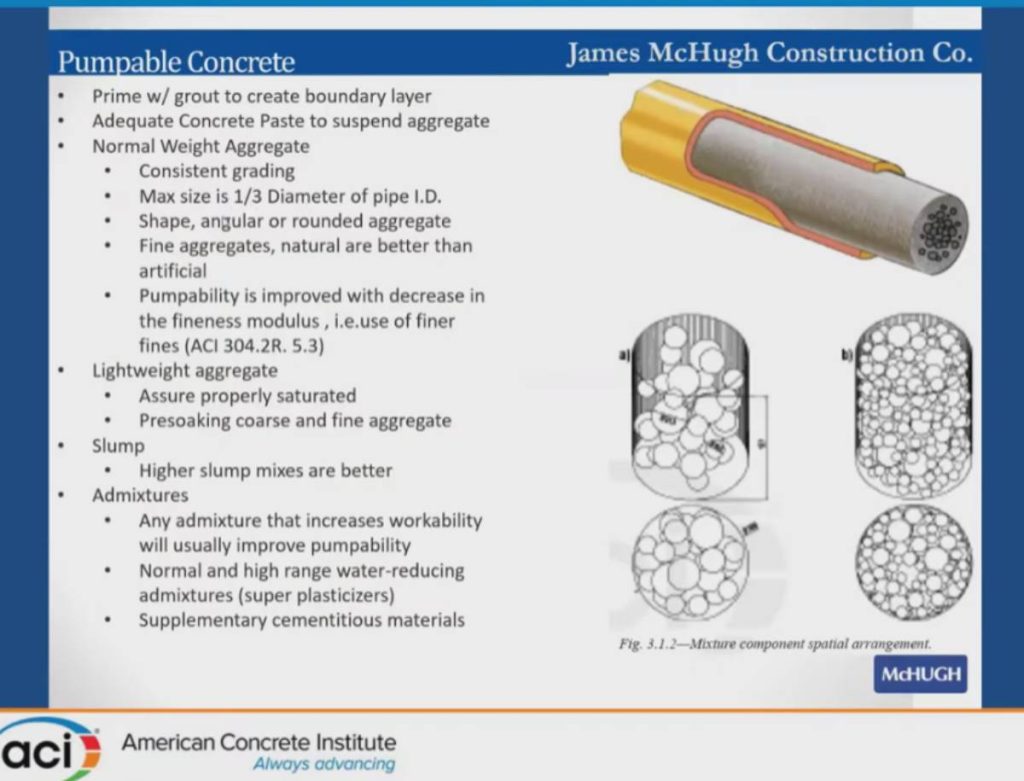
Otro de los elementos a consideración es el uso de fibras en el hormigón que se bombea a grandes alturas, como también, la bombeabilidad del hormigón de ultra alto desempeño (UHPC, en sus siglas en inglés). Respecto a las fibras, el ingeniero aclara que, en su experiencia, pueden utilizarse tanto fibras de material sintético (polipropileno) como de metal (acero).
“Con las fibras de acero nos encontramos ante un desafío ya que, al utilizar una gran cantidad, la masa del hormigón a bombear se incrementa. Sin embargo, con el uso de aditivos superplastificantes y una modificación de las mezclas, logramos utilizarlas con éxito”, puntualizó. Respecto al uso de hormigón de ultra alto desempeño, el ingeniero puntualiza que, al menos en los proyectos donde participó, no se utilizó este hormigón especial.
Junto con estos factores, los ensayos del hormigón, tanto al inicio de la faena de bombeo como al final de ésta, son claves para conocer el comportamiento del material y adecuar los diseños de mezcla para hacer más eficiente este trabajo, especialmente cuando se realiza a grandes alturas.
Em ese aspecto, el profesional destaca que se realizan mediciones iniciales “ya sea del aire o de la unidad de peso, así como del asentamiento o la extensión”, las que luego se comparan con los resultados obtenidos en el sitio de descarga del material. “Frecuentemente, las especificaciones del proyecto requieren este nivel de control, necesitando ajustes en el diseño de mezcla para compensar las variaciones observadas”, puntualizó.
Consideraciones finales
La evolución que presenta la tecnología de bombeo de hormigón a grandes alturas sin dudas que es significativa, ya que viene permitiendo la construcción de edificaciones cada vez más altas -valga la redundancia- en plazos reducidos. En ese sentido, Eamonn Connolly regresa al ejemplo del proyecto Vista, que aseguró el bombeo de hormigón a alturas cercanas a los 200 metros, en ciclos de construcción de tres días.
Esto demuestra que el avance que posee el desarrollo de esta tecnología, como también, sus desafíos a futuro. Uno de estos, asegurar ciclos de bombeo de hormigón continuos a alturas cada vez mayores, en directa relación a proyectos que crecen cada día más, especialmente en obras donde se alzan grandes torres de hormigón y que se desarrollan en Dubái y China, por ejemplo.
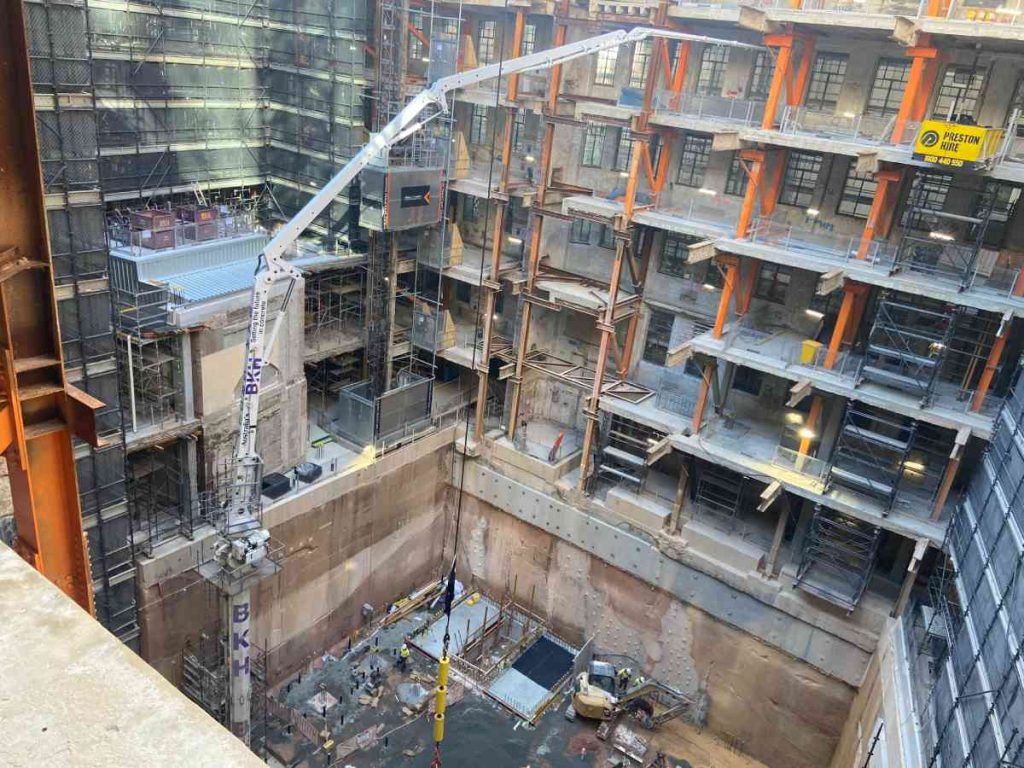
En ese sentido, el desarrollo de sistemas bombeo más potentes, tuberías que resistan una mayor abrasión y diseños de mezcla que mejoren la bombeabilidad del hormigón, permitirán que esta tecnología continúe avanzando para cumplir con su objetivo de transportar el material, de manera continua y eficiente, a grandes alturas.
A esto, también se pueden incorporar la aparición de nuevas tecnologías de automatización de procesos, como también, el monitoreo en tiempo real. Con este tipo de herramientas, el experto considera que podría mejorarse aún más la eficiencia de toda esta faena, lo que repercutiría también en, como se menciona antes, alcanzar mayores alturas en los proyectos, además de incrementar la sostenibilidad de la construcción de edificios de gran altura, gracias al desarrollo de diseños de mezcla de hormigón más sustentables.