El abordar los proyectos bajo una planificación permite materializar el valor esperado de la inversión realizada para una obra gruesa con variabilidades en milímetros, que se puede obtener bajo el concepto de industrialización.
La planificación es la clave para materializar todo el potencial que significa industrializar una obra gruesa. Este genera las condiciones para poder incorporar procesos de terminaciones prefabricados y de montaje que dotan a la obra de las reales ganancias que ofrece la industrialización, la que se materializará solamente en un ambiente de alta productividad, para lo cual se requiere de recursos materiales, capital humano, información, herramientas y logística en forma oportuna, en cantidad y calidad requerida.
“Es aquí en donde la planificación se transforma en el punto de inflexión real para la industrialización, entendiéndola como el homologar una línea de producción industrial bajo la cual los conceptos de ritmo, producción diaria, secuencia y condiciones de satisfacción son los elementos comunes para todas las actividades del proyecto, teniendo mayor relevancia las actividades posteriores a la obra gruesa”, detalla Boris Naranjo Carrasco, director ejecutivo de Xpande Consultores, empresa consultora experta en productividad en la construcción.
El experto plantea los 10 pasos mínimos necesarios para ejecutar una obra de construcción industrializada, pero de manera eficiente.
Hoja de Ruta
1.- Estabilizar el proceso central, obra gruesa, que es aquel del cual “cuelgan” el resto de los procesos de la obra, para eso es necesario buscar la mejor alternativa disponible que permita poder tener variabilidades en milímetros, chequear en planta o en un piloto que las desviaciones esperadas sean materializadas.
2.- Planificar la obra bajo el concepto de producción diaria, determinando los recursos necesarios para garantizar mantener el ritmo determinado por la obra gruesa industrializada. En el caso puntual de la prefabricación, la experiencia señala que en un día de producción se pueden montar entre 14 y 18 paneles diarios, por lo que, si una casa se diseña con esta cantidad de paneles, el ritmo a replicar es recomendable que sea una casa, pues en el concepto de línea de producción este debe marcar a todas las actividades. Esta producción diaria requiere de un flujo de actividades determinado tanto en la unidad habitacional como entre unidades habitacionales, en el caso de un edificio debe ser el departamento y el piso; mientras que en obras de extensión debe ser la casa y el lote de casas.
3.- Se debe determinar todas las actividades mínimas necesarias para construir una unidad habitacional estableciendo una secuencia sin holguras, tanto verticales como horizontales. Esta condición es estrictamente necesaria para la línea de producción industrializada, pues si bien siempre se generarán algunas holguras en el momento de la ejecución en terreno, y esta es una discusión permanente con los equipos que dirigen una obra, es relevante sacarlas de la planificación inicial por dos razones: para que la planificación se enfoque en el suministro oportuno de los recursos y, junto con ello, para que el programa de ejecución de obra (no necesariamente el contractual con el mandante) esté permanentemente comparándose con la producción optimizada, sin holguras, de tal manera de tener como referente la productividad máxima con el sistema constructivo diseñado.
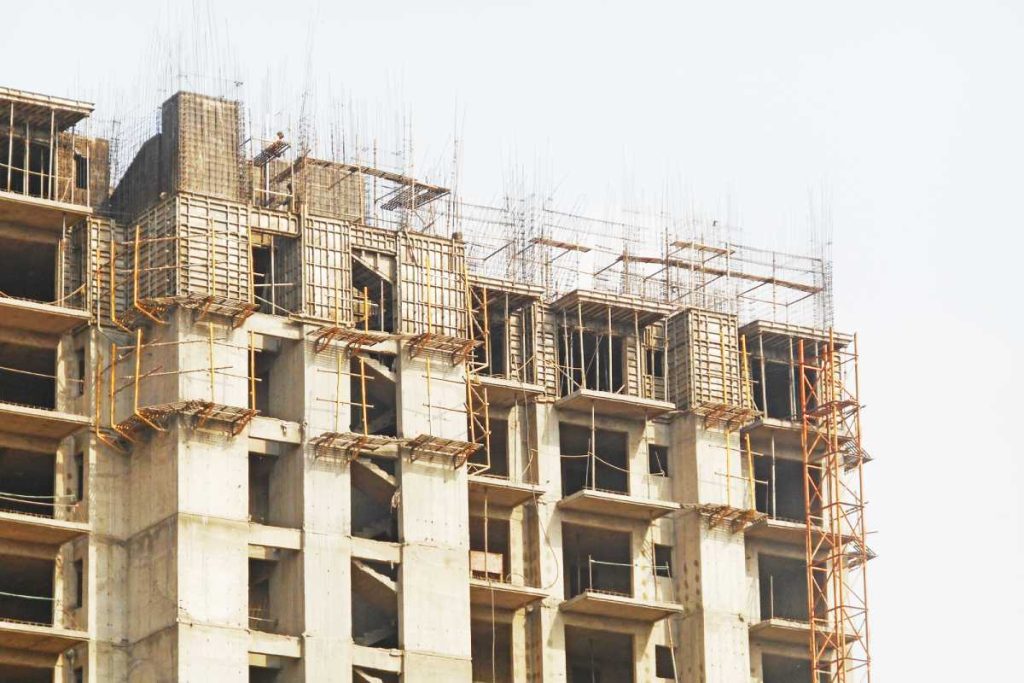
4.- Una vez definidas las actividades mínimas necesarias y su secuencia bajo el concepto de línea de producción industrial, se debe diseñar la programación que dará cuenta del plan objetivo de la obra, el que puede ser distinto al plan contractual con el mandante y, se definirá su carta Gantt además de las posibilidades de optimización con respecto al plan de una obra tradicional.
5.- A partir de la programación optimizada revisar con el equipo de obra integral el plan y el cronograma que de aquí emanan. Esto debe ser desarrollado bajo el concepto de “responsabilidad” de cada uno de los actores en cuanto a la planificación de todos los componentes de la obra bajo el ámbito de responsabilidad de cada involucrado, recursos materiales, cotización, pedidos, recepción y entrega, capital humano, selección, formación, entrenamiento, flujo de la información, avances, entre otros factores. Para esto, se encuentran disponibles herramientas de control de gestión visibles y disponibles en la organización, como MS Project, Primavera, Excel, u otros.
6.- Suministrar oportunamente al punto productivo, entendiendo por éste al lugar en donde el maestro y su equipo debe realizar el trabajo, ampliando el concepto de abastecimiento a una logística externa e interna que garantice el material en cantidad y calidad requerida para la producción diaria. Esto debe ser suministrado en kit de tal manera de controlar la producción a partir de los recursos y detectar sus pérdidas o mermas diariamente para tomar acciones correctivas y preventivas oportunamente.
7.- Implementar una metodología de control y seguimiento que monitoree la coordinación de los recursos con la debida antelación, entre cuatro y ocho semanas, dependiendo de la criticidad con la que se debe abordar la logística, lo que estriba de la localización, los tiempos de aprobación de pedidos, los tiempos de contratación, etcétera, que permita levantar las restricciones con la antelación requerida por el proyecto. Esto se puede llevar a cabo con la metodología Last Planner® u otra que garantice tomar las acciones necesarias para tener los recursos de acuerdo con el plan optimizado de producción.
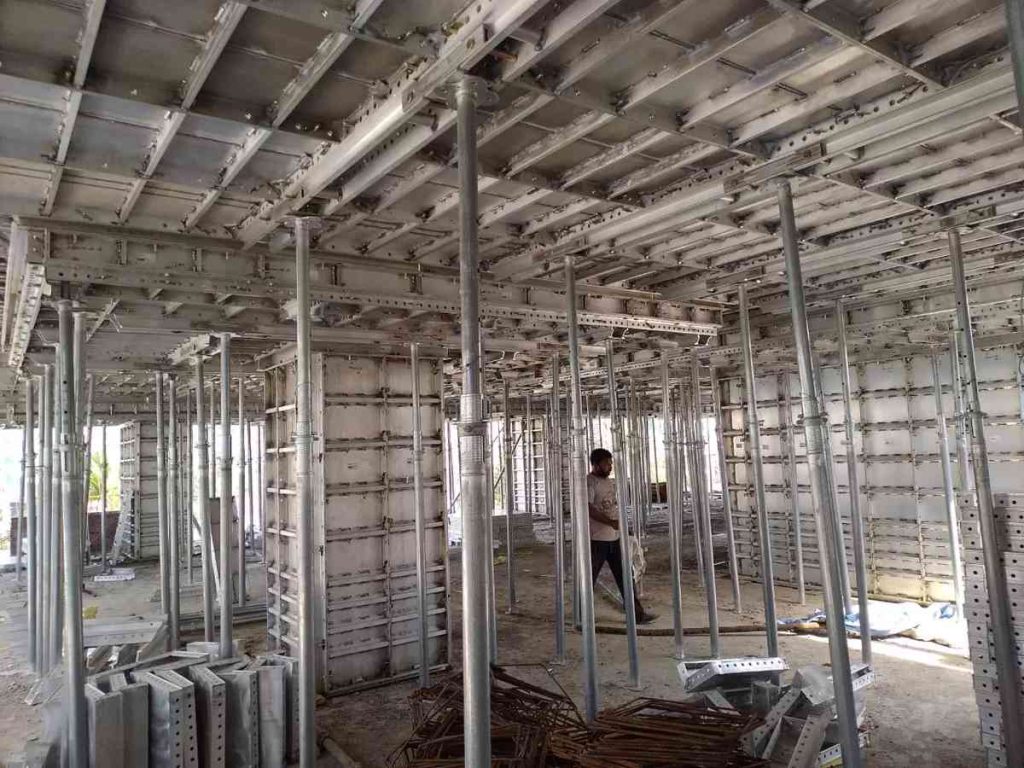
8.- Implementar una metodología de medición permanente de las condiciones de satisfacción de las actividades, entendiendo éstas últimas como las tolerancias objetivas de cada una de las actividades que van dando cuenta de que la salida del proceso está bajo la especificación comprometida para evitar los reprocesos, pues “rompen” la línea de producción industrial y se incurren en costos que no tiene considerado el proyecto.
Esta medición debe ser objetiva, entrenando al equipo humano que ejecuta la obra además de equiparlo con las herramientas necesarias para autoevaluar el resultado de sus procesos, pudiendo abordar las acciones correctivas oportunamente. El sistema de gestión de calidad debe contemplar también la revisión semanal de las desviaciones para generar las acciones preventivas que pueden corregirlo.
9.- Estrategia comunicacional y entrenamiento permanente al personal de obra para comunicar la planificación diaria de manera gráfica y fácil de entender con un alcance semanal que dé a conocer a todo el equipo de terreno la producción esperada, los rendimientos asociados y los recursos requeridos para la producción. Ante la llegada de un contratista o una incorporación al equipo de obra generar el proceso de inducción necesario para garantizar el flujo productivo continuo. Esto bajo el concepto de Visual Management en terreno, de fácil acceso y entendimiento.
10.- Búsqueda permanente de la mejora y la optimización detectando mermas de productividad en todos los procesos en ejecución bajo el concepto de construcción sin grasa, una estrategia clara identificando las tres vertientes de las pérdidas, asociando incluso un plan de incentivos al descubrimiento de las oportunidades.
Estos pasos deben abordarse oportunamente y con la antelación requerida, ya que los tiempos con que se cuenta en la construcción tradicional desaparecen y esos “meses” de holgura que daba la “obra gruesa” para comenzar las actividades de terminaciones ya no existen, pues lo que antes, en el caso de un edificio, era de aproximadamente dos meses para comenzar las terminaciones, esperando los tiempos de desalzaprimado y de rectificación de obra gruesa, pasan a ser días en el caso de la obra gruesa industrializada.
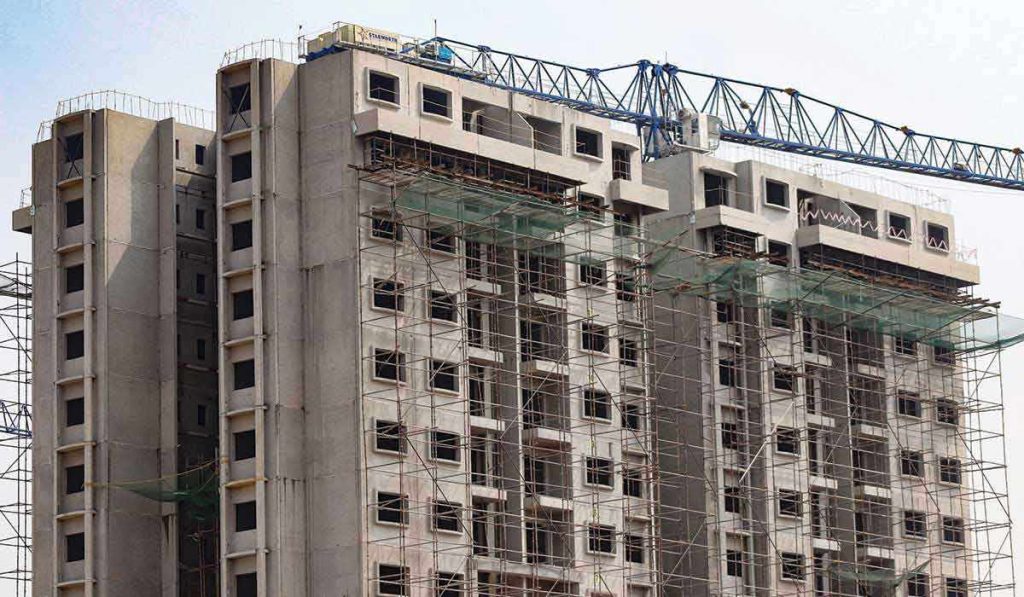
“Es aquí en donde se debe suministrar en kit que permita terminar las unidades habitacionales que vamos construyendo, abastecer un kit de ventanas que permita cerrar toda la unidad habitacional, la totalidad de las puertas que permitan cerrar todos los recintos, los muebles de closet, etc., es un flujo continuo en el cual se requiere la totalidad de los recursos en el más breve plazo por lo que las definiciones, contratos, cotizaciones, órdenes de compra, etc., son parte de las definiciones iniciales”, detalla Boris Naranjo.
De acuerdo al experto, estos son los 10 pasos mínimos necesarios para abordar proyectos de industrialización exitosos en la construcción, “esto no tiene que ver con un sistema constructivo en particular sino que requiere de una manera distinta de ver la concatenación de los procesos constructivos y su planificación, como columna vertebral del proceso, pues es la articulación eficiente de todos los actores y recursos que concurren en un proyecto constructivo lo que le da el carácter de línea de producción industrial”.
En resumen, no son el moldaje de aluminio manuportable, las casas prefabricadas o los elementos de montaje los que no funcionan, sino más bien, los equipos los que no articulan y no cohesionan un equipo humano, recursos o materiales en pos de optimizar los procesos. La herramienta para generar el verdadero cambio requerido es la planificación basada en el análisis operacional y bajo la lógica de una línea de producción industrial.