A 3.000 metros sobre el nivel del mar, se construye el nuevo Complejo Fronterizo en el Paso Los Libertadores, ubicado a 68 km de la ciudad de Los Andes, en la Región de Valparaíso. La instalación, en la frontera de Chile con Argentina, atenderá un mayor flujo de personas, vehículos y transporte de carga con Argentina (más de 4,3 millones de toneladas y sobre 1,5 millones de personas en tránsito), constituyéndose además, en la principal conexión terrestre entre Chile y el MERCOSUR, con un mercado potencial de 190 millones de personas.
Las principales obras consideradas en el proyecto son el edificio de Control e Inspección, el Edificio de Alojamiento para funcionarios, Subcomisaria de Carabineros de Chile, Vialidad de acceso y empalmes con la Ruta 60-CH, entre otras obras menores.
Un proyecto con diversas consideraciones técnicas debido al clima extremo. Colocación de hormigón para las fundaciones a -20°, utilización de hormigones prefabricados, y la generación de carpas para lograr un microclima adecuado, fueron parte de los desafíos en la alta montaña.
Hormigón prefabricado
Uno de los grandes protagonistas de la obra fue la ejecución de hormigón prefabricado, sistema constructivo que se contempló desde el inicio del proyecto. En la Cordillera, en pleno invierno la sensación térmica puede alcanzar los -20°C, escenario que determinó la ruta crítica del proyecto.
“En esas condiciones climáticas el fraguado del hormigón tiene una dificultad enorme. La reacción química de fraguado del hormigón comienza, en términos prácticos, recién a los 0°C. Al hacer las mediciones de la temperatura interior del cáliz de las fundaciones, éstas registraban -10°C, con lo cual resultaba imposible ejecutar el mortero de fijación del pilar prefabricado a la fundación. Las fundaciones fue lo único que se hizo in situ y con grandes dificultades, para lograrlo se generaron carpas con autoclave para lograr el clima necesario para que el hormigón tuviese la reacción de fraguado”, comenta Ernesto Villalobos, gerente general de Preansa, empresa que junto con SIRVE desarrollaron la ingeniería del proyecto.
La solución para la construcción de las instalaciones vino de la mano de estructuras de hormigón prefabricado, sistema que redujo la colocación de concreto in situ sólo a las fundaciones.
“Desarrollamos la ingeniería completa en conjunto con SIRVE, y fuimos incorporando todo nuestro conocimiento de los prefabricados, tanto en el edificio de control como en el hotel o edificio de alojamiento, y el edificio de Carabineros. En los tres edificios la estructura soportante se solucionó con elementos prefabricados, con distintos conceptos estructurales”, detalla el ejecutivo de Preansa.
Entre las numerosas obras ejecutadas destaca el edificio de Control de 25.000 metros cuadrados. El inmueble consta de tres vanos de 25 + 25 + 16 metros de luz, losas de 7,5 metros de luz, con una estructuración en base a marcos rígidos en ambas direcciones, con conexiones dúctiles en la unión viga-pilar. Se diseñó bajo la norma NCH433 con una carga bastante especial, ya que tiene considerado 1.350 kilos por m2 de nieve, y un sismo con un coeficiente de importancia de 1.2, “por lo tanto, se escogió para cumplir con todos las exigencias de resistencia y control de deformación de la norma, fue desarrollar un sistema de marcos rígidos. Todas las uniones de las vigas con los pilares son dúctiles, lo que implicó hormigonar la unión en terreno. También hay pilares metálicos que soportan una gran viga de madera curva. Para el caso máximo, se ocupó una viga de 1,50 metros de canto, y todas las losas son alveolares pretensadas. En algunos casos tuvimos que incorporar manguitos de conexión para poder disponer alguna armadura del nudo que no se podía colocar en la fábrica porque impedía el montaje de la pieza”, prosigue Villalobos.
Este edificio tiene circulación de vehículos en el segundo piso, en donde se hará un sistema de vialidad, con pavimento y veredas, eso a la postre son pesos muertos importantes.
La obra se inició entre febrero y marzo de 2017, para comenzar el montaje de los prefabricados en mayo. Paralelo a la prefabricación, partieron las fundaciones.
“El montaje se planificó justamente pensando en que tendríamos tiempos muertos a causa de la nieve”, complementa Ernesto Villalobos.
En condición de frío extremo, las maquinarias tienen serios problemas con el encendido. A modo de precaución se generó una zona de resguardo. “Este escenario motivó a que lo primero que se hizo fue construir un área con losa para tener un techo de manera de proteger los equipos. Ese fue nuestro primer objetivo, formar un campamento base que nos permitiera, desde ese punto, resistir los momentos de tormenta y resguardar al personal, herramientas y equipos”, indica Villalobos.
Con la constructora Dragados, se trabajó un plan para que en el caso de tormenta y en condiciones adversas, la instrucción fuese dar aviso de bajada inmediata al personal. Posteriormente la constructora tenía que despejar los caminos y actuar rápidamente para que se organizase la faena. “Ese programa también es importante en estas condiciones, el generar un procedimiento de aviso de bajada, donde lo que no puede quedar son equipos y gente atrapada arriba”, comenta Villalobos de Preansa.
Bajo estas condiciones ante el clima, la ventaja de trabajar con el prefabricado en este proyecto es que las estructuras venían terminadas. “Lo único in situ fue la aplicación de un mortero grout, especialmente fabricado para condiciones extremas, de fijación a las fundaciones, y para los nudos de conexión, que minimizó la dificultad en terreno. Para las conexiones especificamos un mortero especial de alta resistencia y rapidez KONA800, para generar la mezcla a más de 50°, momento en el que vaciábamos el material, sobre paredes que no podían tener -10°C. Partiendo desde esa temperatura se pudo fraguar y llegar a las resistencias iniciales admisibles para continuar con el montaje”, detalla el ejecutivo de Preansa.
Hotel singular
Desde el punto de vista de la ingeniería, el edificio de alojamiento tiene una configuración especial. Como lo señala Villalobos, “lo normal es un sistema de pilares, vigas y losas. Este edificio tiene una geometría distinta, es longitudinal, muy angosto de 3 y 4 niveles, de 12 metros de luz. En vez de pensar en un sistema de pilares y vigas, dada su geometría, se pensó en una estructura de elementos muro y losa. Muros de 1,50 x 1,50 metros y en algunos casos de 2 metros, lo cual fue el elemento constituyente que desarrolló este edificio. Hay desde muros en T, algunos muros en L más algunos pilares rectangulares en la zona del restaurante, y una cantidad mínima de vigas macizas pretensadas en ambas fachadas”.
Adicionalmente, está emplazado en roca. Lo que se ideó fue que el muro prefabricado incorporase desde fábrica la armadura hacia abajo. “Se monta el muro con un elemento auxiliar y armaduras salientes en la parte inferior, luego se procede a ejecutar la zapata, con esto se logra que solo con la excavación de la zapata, se pueda iniciar el montaje del prefabricado y dejar las fundaciones corriendo en forma paralela. Con esto se ganó bastante tiempo en terreno, y se logró un elemento adicional, esto es que la longitud de anclaje de este elemento hacia la fundación fue mínima, lo cual fue muy importante debido a que este edificio está emplazado en roca, por lo tanto excavar más abajo era muy costoso”, comenta Villalobos.
Para el montaje de ambos edificios se utilizaron grúas de 60, 90 y 160 toneladas.
Respecto del movimiento de tierra, se trata de un material de origen glaciar, una morrena con afloramientos de roca. Hubo sectores que en invierno, con la humedad, se congelaron y transformaron en hielo con tierra.
El proyecto es una gran planicie que se conecta a la carretera. Unido a los edificios también se ejecutaron viaductos de entrada de nueve metros de alto. Como lo señala Villalobos, durante el proceso de ingeniería y estudio de la prefactibilidad, se efectuó también el estudio logístico, “llegamos hasta los 3 mil metros de altura con dimensiones de vigas de una sola pieza a la obra. En total fueron 52 vigas que subimos sin mayores inconvenientes, respetando la pendiente máxima que permite vialidad que es de 12 por ciento”.
Edificios de Alojamiento de Funcionarios y de Carabineros
Las obras que involucraron la construcción del Complejo Fronterizo Paso Los Libertadores contemplaron, además del edificio de Control e Inspección, el Edificio de Alojamiento para funcionarios y las dependencias de Carabineros. Estas instalaciones, también se abordaron con prefabricados de hormigón, instalando los elementos en lugar de ejecutarlos in situ.
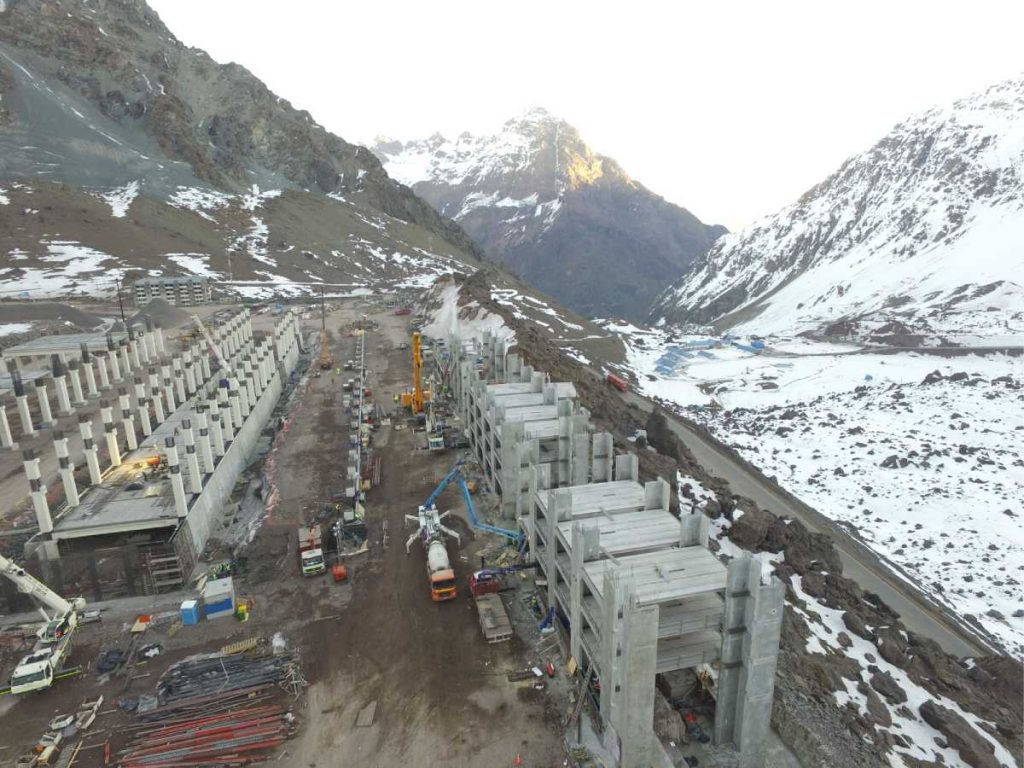
“Debido a la ubicación geográfica de este proyecto y el periodo en el que se ejecutó la fabricación, se hacía inviable la posibilidad de montar una planta en el lugar”, comentó Claudia Cid Perley, gerente de proyectos mineros de Tensacon S.A., firma encargada de la ejecución de estas obras. Por ello, para la ejecución de esta obra, se optó por transportar los prefabricados de hormigón desde la propia planta de la firma, ubicada en la comuna de Paine, a 190 kilómetros de la obra.
Sirve S.A. fue la empresa encargada del diseño de la obra, con Tensacon S.A. complementando aspectos del mismo, puntualizó Claudia Cid. Respecto a las características de esta instalación, la gerente de Tensacon explicó que “el Edificio de Alojamiento de Funcionarios, corresponde a una estructura habitacional que se emplazó al borde de una ladera generando 4 edificios independientes de 2, 3 y 4 pisos, los que se relacionaban mediante zonas escaleras. Los edificios corresponden a una estructura de marco compuesta por pilares, vigas y losas pretensadas alveolares, la que se completa con una capa de compresión en sitio que genera el diafragma rígido”.
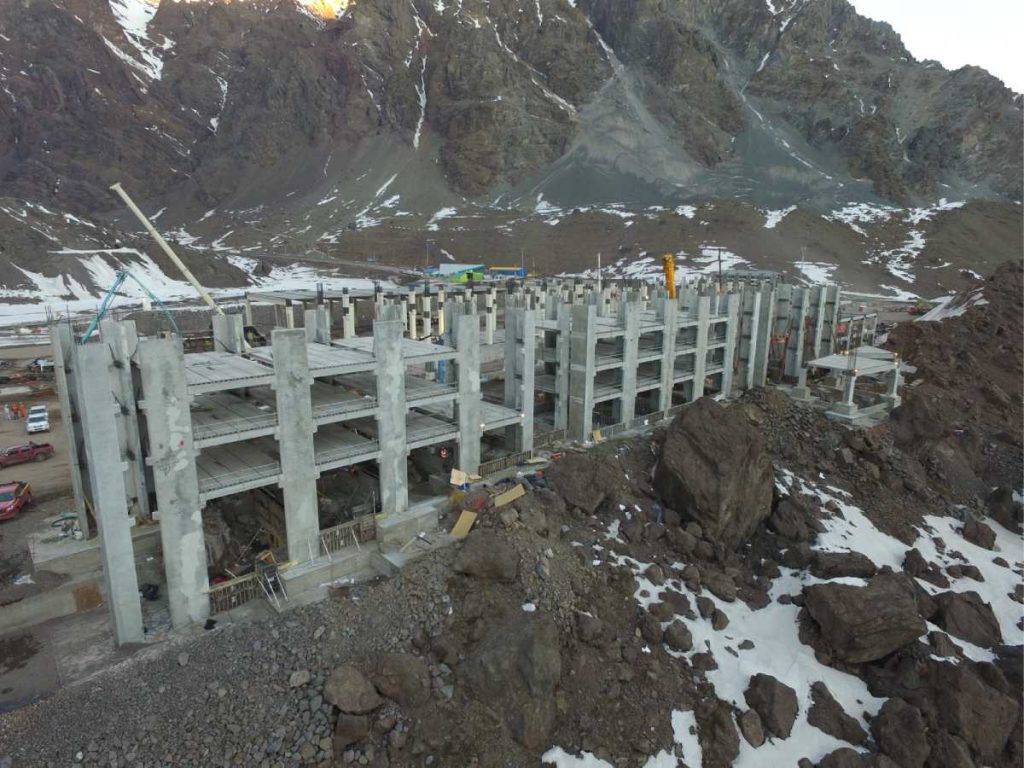
Asimismo, detalló que “los pilares eran muy particulares, ya que correspondían a secciones T y L que se conectaban a una fundación masiva ejecutada en terreno. Los pilares de mayor altura tenían 20 m. y un peso de 55 ton. Las vigas correspondían a vigas de sección rectangular pretensadas conectadas a los pilares mediante ménsulas y dowells. A su vez las losas corresponde a los alveolares de 30 cm. de espesor con una capa de compresión de 10 cm.”.
Para el Edificio Carabineros, por su parte, “se consideró una estructura de pilares perimetrales con un altillo interior de servicio, compuesto por vigas y losas, sistema de que se completa con una capa de compresión”, destacó la gerente de proyectos mineros de Tensacon. Asimismo, también subrayó que el diseño de esta instalación también fue ejecutado por Sirve S.A..
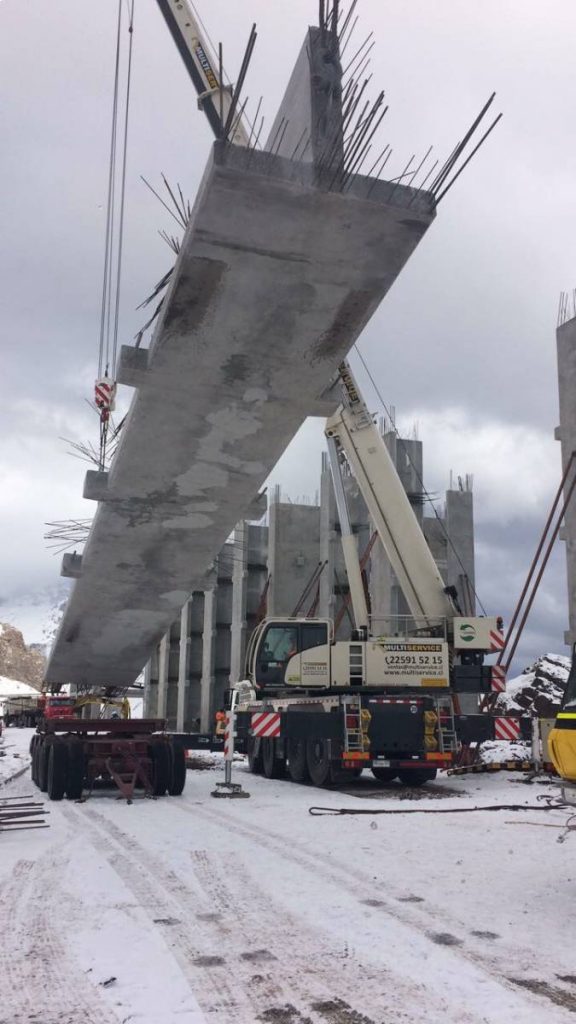
Respecto al hormigón utilizado en la fabricación de los elementos a utilizar en estas obras, Cid comentó que “el diseño contemplaba cargas importantes de nieve y ocupación, lo que genero piezas robustas y fuertemente armadas propias del lugar donde se encuentra emplazo el proyecto y la relevación de la estructura y su operatividad. Cabe señar -agregó- que esta estructura se encuentra 100% recubierta por revestimiento en fachada y cubierta, por lo que en este caso, no requiere de protecciones adicionales incorporados a los hormigones”.
En ese sentido, la profesional comentó que uno de los principales aportes de Tensacon a este gran proyecto fue “la fabricación y toda la logística asociada al transporte y el montaje de esta estructura, cuya mayor complejidad se daba por su locación, a 3.200 metros sobre el nivel del mar, con acceso por camino de montaña con circulación transito permanente de vehículos pesados y livianos, y junto con eso, el periodo en el cual se realizó el montaje, durante pleno invierno 2017, y finalmente, en el montaje de los pilares T y L que no tenia un punto de apoyo con el cual poder fijarse”.
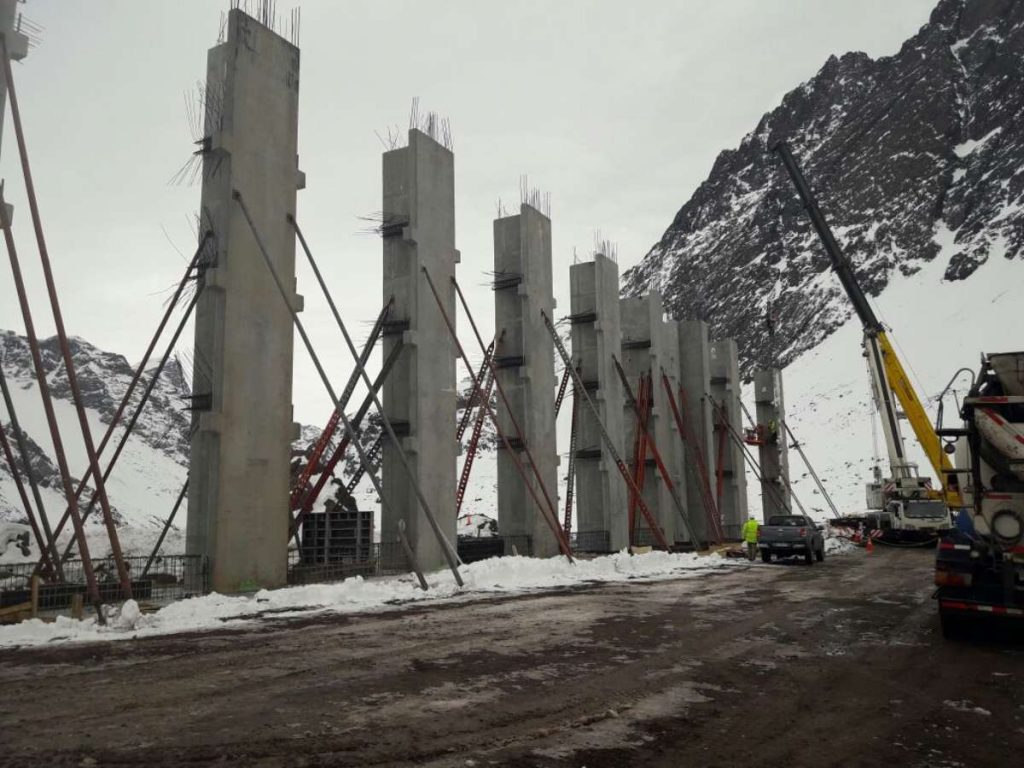
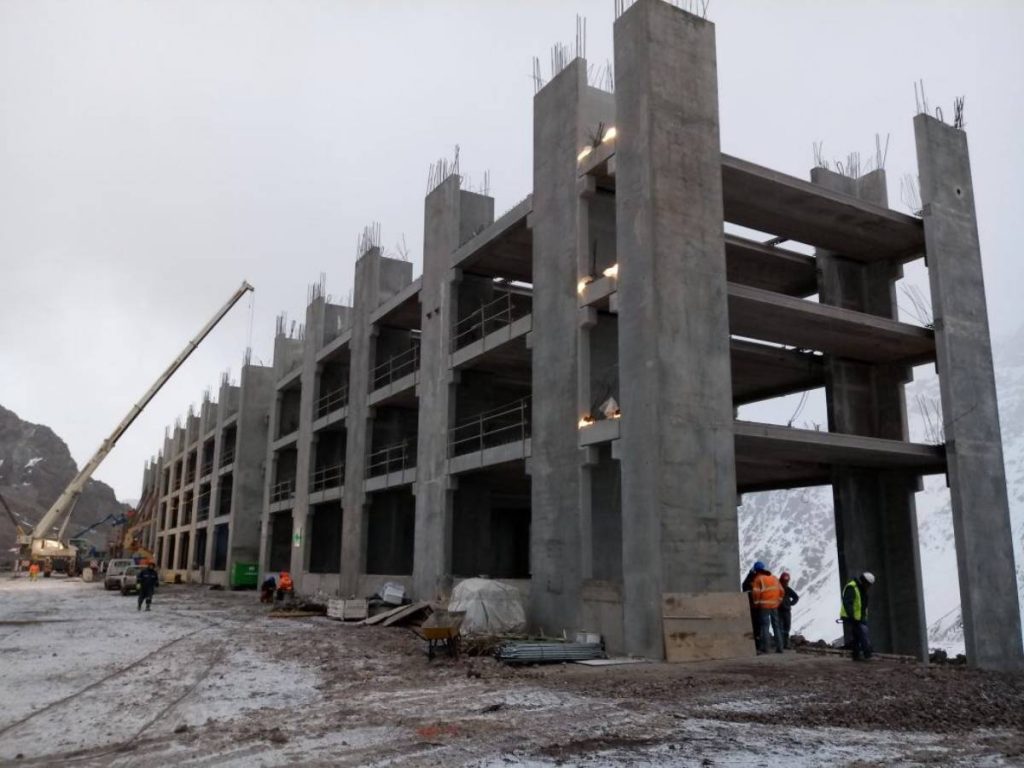
Sin dudas, el aporte del prefabricado de hormigón para el desarrollo de este proyecto fue fundamental. “La única posibilidad de ejecutar esta obra en el periodo, en el plazo y en el costo en que se ejecutó, fue haberlo realizado por mediante una estructura prefabricada de hormigón”, dijo Cid y agregó que “esta solución permitió reducir el plazo total en una temporada, lo que sin lugar dudas permitió asegurar los costos del proyecto. Si esta estructura se hubiese diseñado con otra materialidad, las dimensiones de los elementos estructurales hubiesen sido de mayores lo que hubiese tenido un impacto mayor en la construcción y el entorno”.