En este artículo, publicado originalmente por la revista Shotcrete Magazine de la American Shotcrete Association, se entregan detalles técnicos de la reparación de este túnel que transporta agua a una central eléctrica y que, por su ubicación y condiciones climáticas del sitio de la obra, hubo que realizar una serie de ajustes en la planificación y ejecución del proyecto, en el que shotcrete jugó un rol clave para llevarlo a cabo.
Autor: Jason Myers, ingeniero civil de la Polytechnic University at San Luis Obispo, actual vicepresidente de operaciones y director de seguridad en Dees Hennessey, firma que suministro el shotcrete para este proyecto.
Fuente: Shotcrete Magazine
Enfrentarse a un proyecto con acceso limitado, que el material se deje vía helicóptero, que el acceso del personal más cercano se encuentre a 8 kilómetros del sitio de la obra y que la salida más próxima esté a unos 800 metros de distancia, la única solución para manejar todas estas externalidades es el shotcrete. El Túnel Poe tiene 24 kilómetros de extensión y se ubica a los pies de las Montañas de Sierra Nevada, en un área de escarpados cañones. El túnel transporta agua desde un depósito ubicado en la bifurcación norte del Río American, hasta la central eléctrica Poe, donde se genera la energía. El túnel tiene un diámetro cercano a los 6 metros y se construyó en la década de 1950.
El mandante, Pacific Gas & Electric (PG&E) inspeccionar de manera regular el túnel y durante la inspección realizada en 2016, se descubrió fisuraciones importantes en el shotcrete de la estructura que causaron preocupación. Ese mismo año, el contratista general realizó algunas reparaciones de emergencia mientras se diseñaba y aprobaba un arreglo completo para el túnel. Dees Hennesey, Inc (DHI) se adjudicó el contrato para la obra y Syblon Reid (SRCO) ejecutó la colocación del shotcrete para los trabajos de reparación finales. El alcance consistió en un nuevo revestimiento para el túnel de una extensión de 28 metros. Una vez que SRCO logró mover el proyecto para la temporada de 2019, se decidió aumentar el alcance y ejecutar el revestimiento con shotcrete para una extensión de 180 metros del túnel. Esta decisión se realizó dos semanas antes de la colocación del hormigón proyectado. El diseño para el grosor del túnel fue de 250 mm, sin incluir otras reparaciones. El volumen final de shotcrete colocado sobrepasó los 380 metros cúbicos.
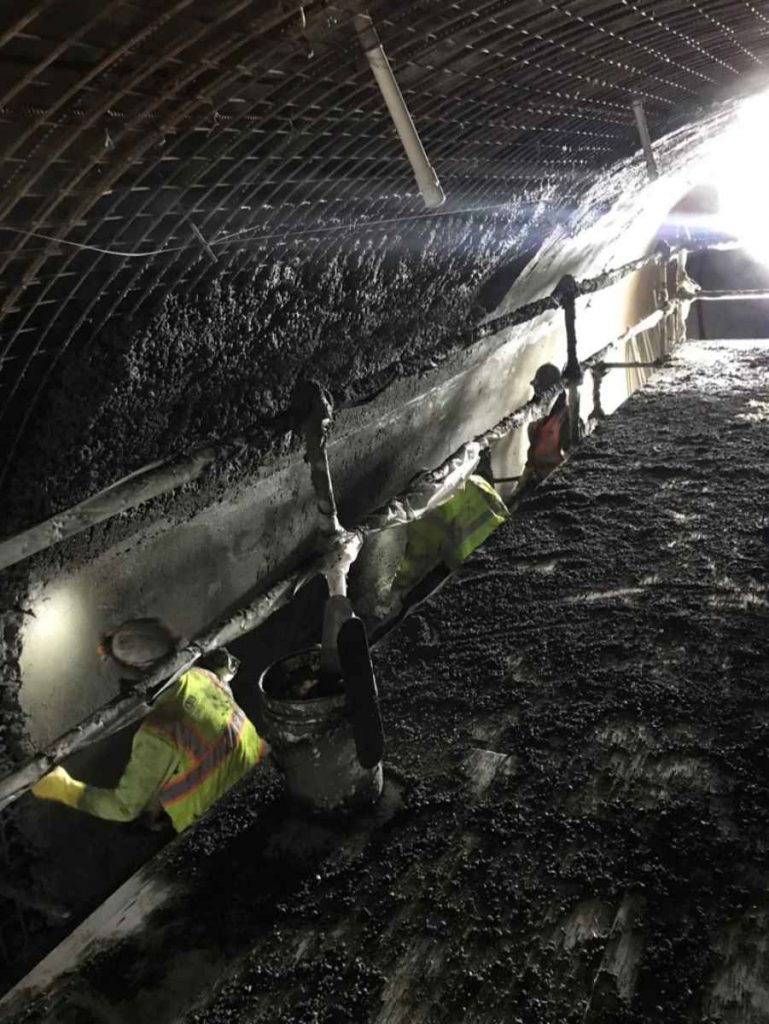
Las dificultades a superar en el proyecto giraron en torno al acceso del sitio de la obre. La locación del trabajo con shotcrete se ubicó a unos 700 metros de la entrada más cercana al túnel. Además, no se podía llegar a esa entrada en vehículos o caminando debido a que se encuentra ubicada en el cañón mismo. A esas dificultades, hay que añadir que en la parte superior del cañón, pasa una sección importante del río y entremedio, la línea férrea se mantiene activa. Otro inconveniente fue el suministro de material, ya que la planta de hormigón más cercana al sitio se encuentra a dos horas.
Se desarrolló un plan para que, tanto las bombas de shotcrete como el material mismo, fuesen entregados en un helicóptero, atravesando el cañón. De esta forma, se logró bombear shotcrete fresco a 700 metros del sitio de la obra. Uno de los desafíos con respecto al calendario que hubo que enfrentar resultó ser la capacidad de carga del helicóptero. La manera más funcional y económica de transportar el shotcrete fue utilizar un helicóptero que pudiese transportar 0,4 m3 por vuelo, cruzando el cañón. Este método resultó ser el balance adecuado para proporcionar el suficiente shotcrete a la bomba, sin sobrecargarla y al mismo tiempo, permitió que se vaciara el transporte en un tiempo razonable. Esto permitió además que el helicóptero aterrizara y recargara combustible cuando se vaciaba un camión con el material. Para llegar a la obra, el equipo tuvo que realizar un viaje de unos 5 minutos en buggy todos los días desde la entrada para vehículos más próxima hasta el lugar donde se ejecutó el proyecto.
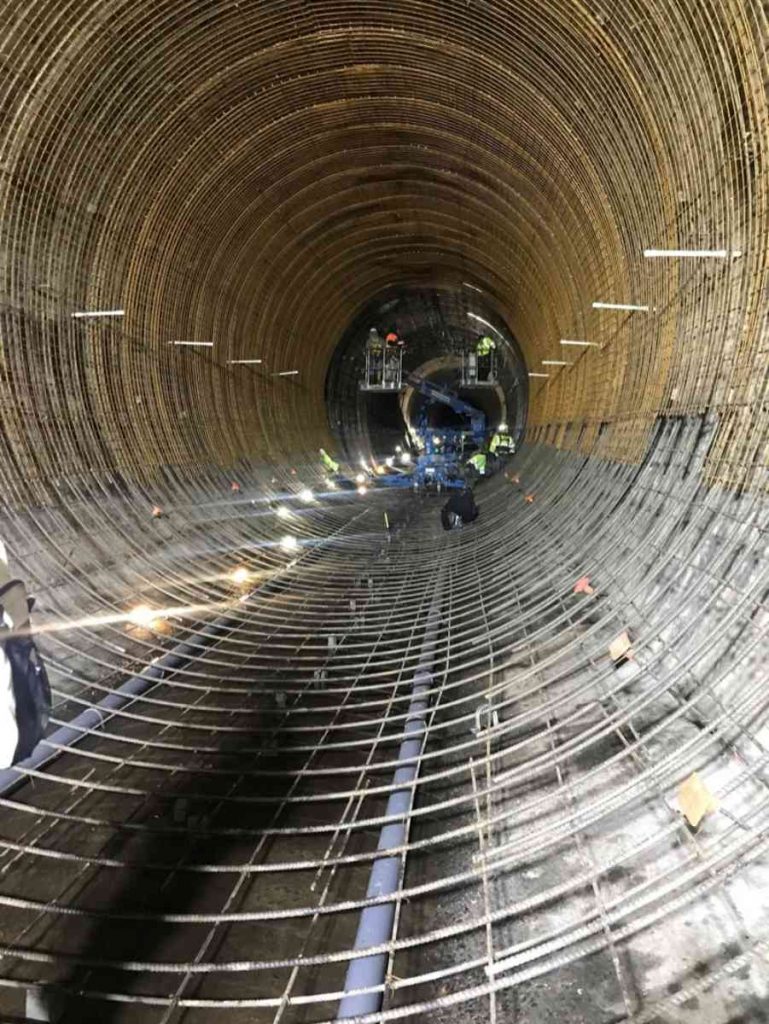
Para el nuevo revestimiento, se utilizó una mezcla de shotcrete con aditivo retardante para permitir el tiempo de preparación y entrega del material, el transporte por helicóptero y el bombeo de la mezcla de hormigón proyectados. Asimismo, se utilizó un asentamiento alto en la mezcla para que así, el shotcrete pudiese ser bombeado a 700 metros desde fuera de la entrada al lugar de las obras. Una vez colocada la sección superior de la instalación de hormigón proyectado, se utilizó el acelerante para shotcrete MAPEI Mapequick AFK 888 para lograr un fraguado rápido y colocar el shotcrete.
La gran ventaja que el hormigón proyectado tuvo en el proyecto fue su flexibilidad. Por ejemplo, este atributo pudo verse en la secuencia de trabajo, en la planificación del proyecto, en avanzar o detener la obra en respuesta a factores externos. Al utilizar shotcrete, se eliminó el uso de encofrados y la secuencia de trabajo pudo modificarse cada vez que cambiaban las circunstancias. Este proyecto se llevó a cabo durante los meses de invierno, por lo que hubo que tener en cuenta siempre las condiciones climáticas y en ocasiones, el helicóptero despegó hasta el punto en que el viento o la lluvia comenzaban. Al usar shotcrete, se pudo ajustar fácilmente la locación de las juntas de construcción y comenzar al día siguiente o cuando las condiciones climáticas fuesen favorables.
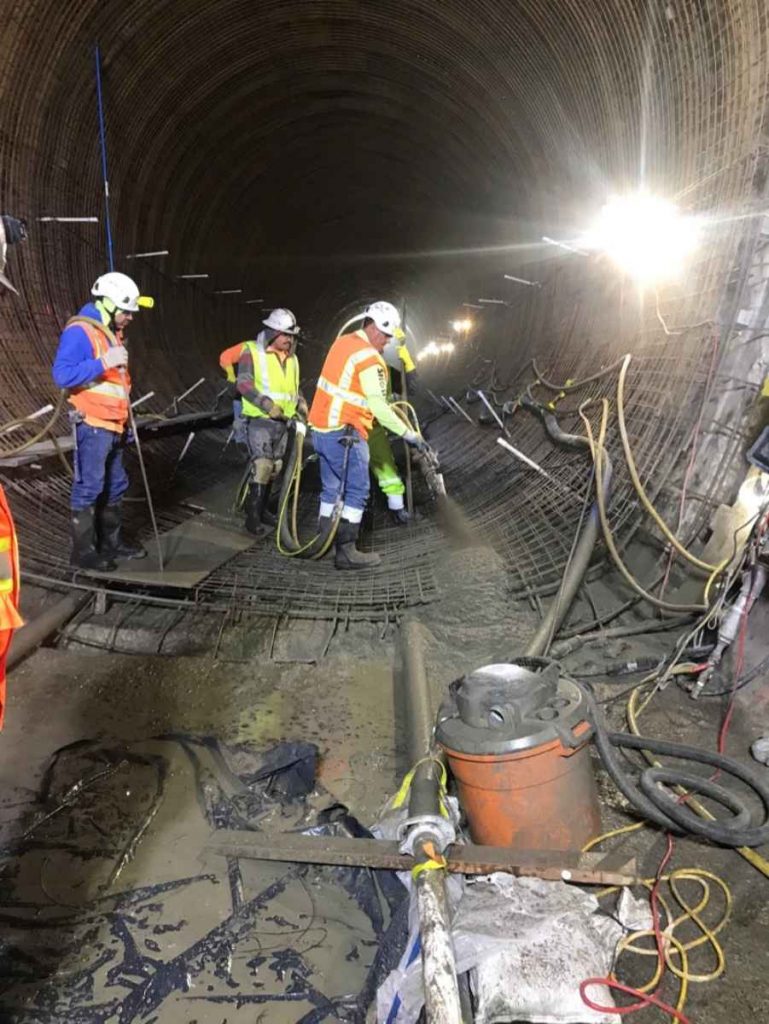
Esta flexibilidad también permitió ajustes de último minuto en la secuencia de colocación del hormigón proyectado. Los planos no mostraban que el ingeniero quería que se colocaran franjas horizontales en el nivel invertido del túnel hasta llegar a la línea de resorte y desde ahí, ir de un lado a otro a través de la porción superior del túnel hasta el otro lado. Este es un túnel de 6 metros de diámetro. Gracias a la flexibilidad del shotcrete, se lograron cambiar las secuencias de colocación del material para cumplir con los requerimientos del ingeniero sin costos adicionales o restricciones en la calendarización del proyecto. En ese sentido, sólo la flexibilidad que brinda el hormigón proyectado, que evita el uso de encofrados, permitió doblar el tiempo de planificación, responder los desafíos climáticos y volver a secuenciar todo el proyecto, completándolo antes de lo presupuestado en el proyecto original de 27 metros.
En ese sentido, el proyecto ejecutado en el Túnel Poe resultó único, en gran parte por los desafíos logísticos que implicó la obra. El shotcrete logró entregar soluciones únicas y pese a los inconvenientes, con una correcta planificación y ejecución, el hormigón proyectado respondió a cada uno de los desafíos que impuso el proyecto.