Aplicando herramientas de diseño matemáticas y un diseño de mezcla especial, un grupo de académicos de la Universidad de Ghent desarrolló una nueva forma de fabricar estructuras de hormigón con tecnología de impresión 3D, optimizada para una mayor velocidad constructiva.
Uno de los desafíos que se presentan con la tecnología de hormigón 3D es cómo lograr trasladar un diseño 2D a una estructura impresa 3D de manera realista, de tal forma que ésta represente la topología presentada en el plano original, sin adecuaciones de última hora en torno al diseño.
Bajo esa premisa, un grupo de investigadores de la Universidad de Ghent, en Bélgica, en conjunto con el Instituto de Tecnología de Israel, Technion, idearon una nueva metodología que aborda ese paso, gracias a la aplicación tanto de herramientas matemáticas de diseño como la optimización del diseño de mezcla del hormigón utilizado para la obra.
Esta nueva metodología, bautizada como OptiBridge, abarca distintos ángulos del elemento fabricado -en este caso, un puente- como su reología, durabilidad y aspectos estructurales y de diseño, con la finalidad de superar ciertos inconvenientes que se presentan a la hora de fabricar estructuras de hormigón con tecnología de impresión 3D.
Diseños mejorados a partir del 2D
Uno de los primeros aspectos que abarca esta nueva metodología es el del diseño. Para ello, se planteó un paso peatonal de 2 metros de ancho por 5 de largo, cuyo diseño se realizó utilizando herramientas matemáticas. “En este caso, se aplicó una optimización a la topología estructural de un problema de vigas en 2D, incluyendo la optimización de un perfil de tendón para postensado”, explicaron los responsables del proyecto.
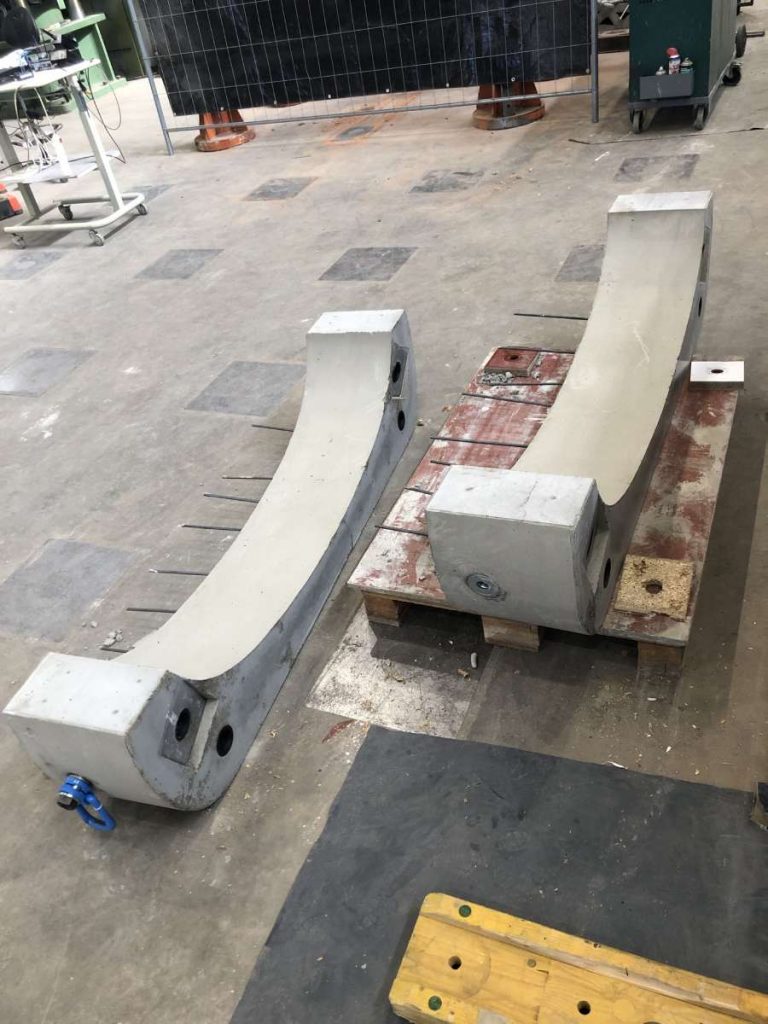
Junto con esto, “también se utilizó una secuencia de optimización de topología 2D para, valga la redundancia, optimizar la rigidez de las dos caras de las vigas. Estas soluciones matemáticas sirvieron como inspiración para el desarrollo de la figura 3D de todo el puente”, subrayaron los investigadores.
Finalmente, se desarrolló un modelo paramétrico que incrementó el nivel de flexibilidad en el prediseño de la geometría 3D. De esta forma, agregaron, cada una de las vigas se inclinó levemente a fin de “contrarrestar las fuerzas horizontales y laterales introducidas por las cargas de diseño de la plataforma. Posteriormente, se realizaron análisis post numéricos para estimar las fuerzas internas y así, optimizar la actual fuerza pretensada y el número de barras de refuerzo”, puntualizaron.
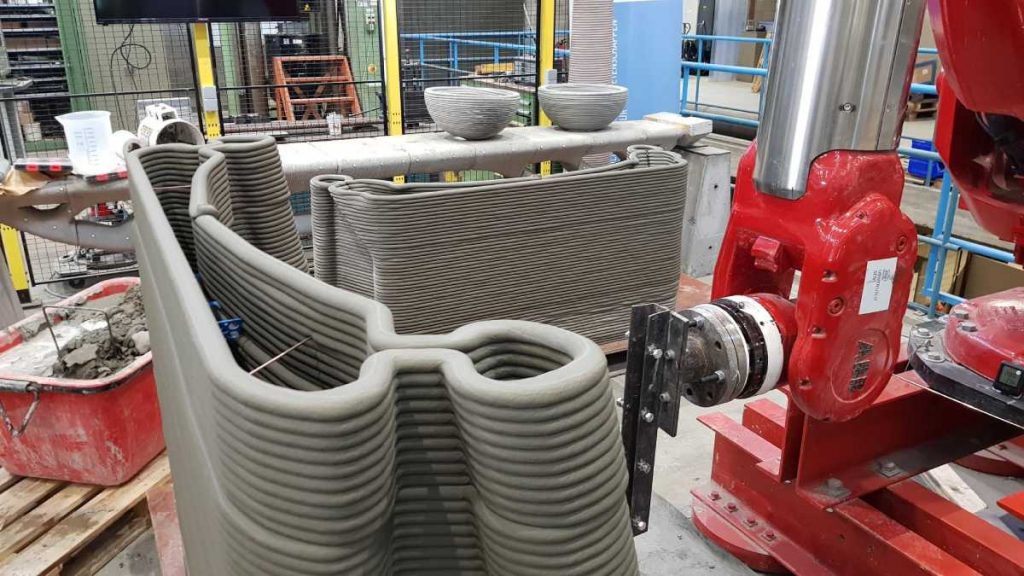
Optimización del diseño de mezcla
Para testear de mejor forma esta nueva metodología, se ejecutó la construcción de un paso peatonal a escala real. “Inicialmente -comentaron los involucrados en el proyecto- los experimentos consideraron la impresión 3D del puente en dos secciones. Sin embargo, debido a limitaciones en el transporte, el puente final tuvo que subdividirse en cuatro segmentos separados”.
Según lo informado por el equipo que desarrolló esta nueva metodología, la impresión de los cuatro segmentos se realizó en dos días consecutivos y tomó “sólo 40 minutos de impresión por día”, subrayaron y precisaron que “este marco de tiempo sólo consideró el tiempo de impresión real y descartó la preparación y limpieza”.
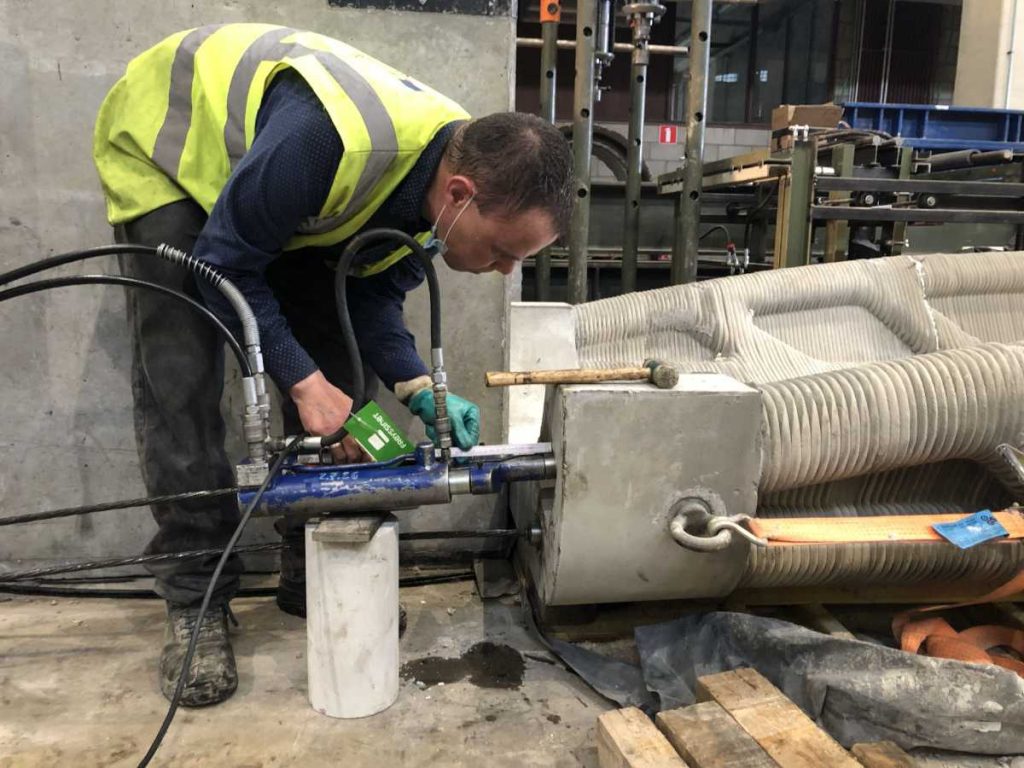
Para conseguir esa velocidad de impresión, se desarrolló una mezcla especial del hormigón a imprimir que buscó un tiempo de fraguado rápido y, a su vez, una resistencia mejorada a temprana edad, permitiendo así la impresión de ángulos sobresalientes de hasta 45 grados.
Los próximos pasos de OptiBridge
La última fase del proyecto consistió en unir y alinear los cuatro segmentos, insertar las barras de refuerzo y tendones postensados, al mismo tiempo que “se utilizó hormigón autocompactante para rellenar el vacío y, posteriormente, pretensar toda la estructura”, detallaron los investigadores.
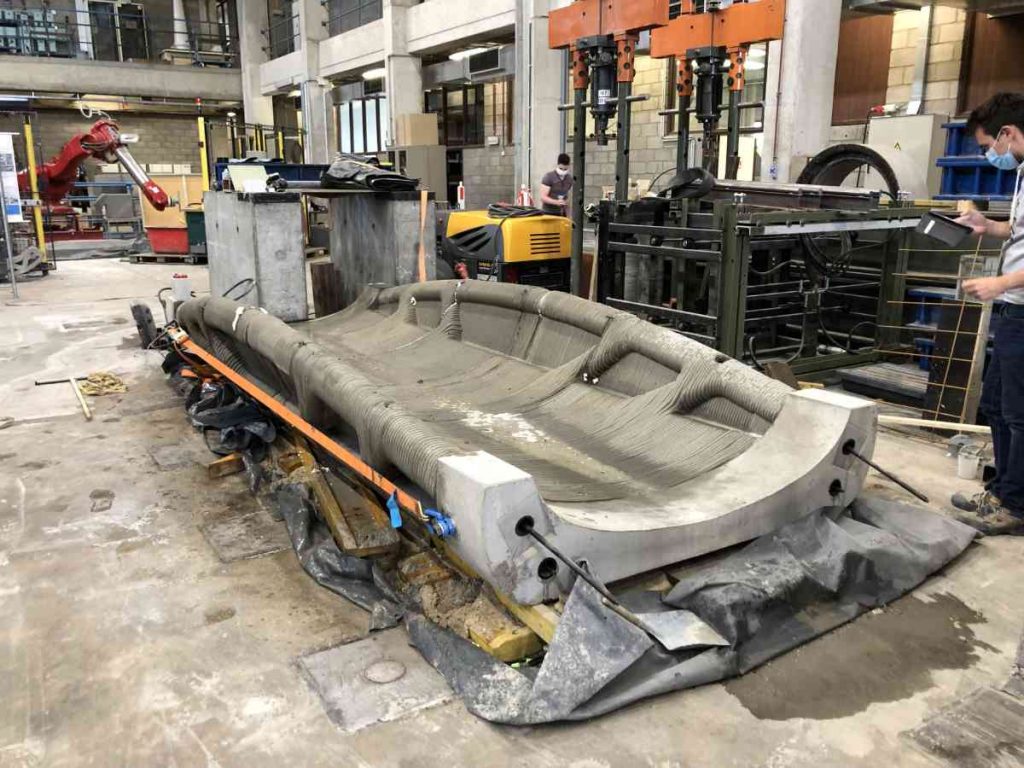
Una vez realizado ese proceso, el puente se levantó y giró hacia su orientación final para así, colocarlo en una locación temporal mientras se llevan a cabo más análisis de la estructura.
En ese sentido, los investigadores comentaron que se realizarán ensayos en el puente que midan tanto su durabilidad como también, su capacidad de carga. Asimismo, detallaron que esta estructura, fabricada con esta nueva metodología de construcción 3D, se utilizará como prueba para evaluar la sostenibilidad de los elementos fabricados con tecnología de impresión 3D.
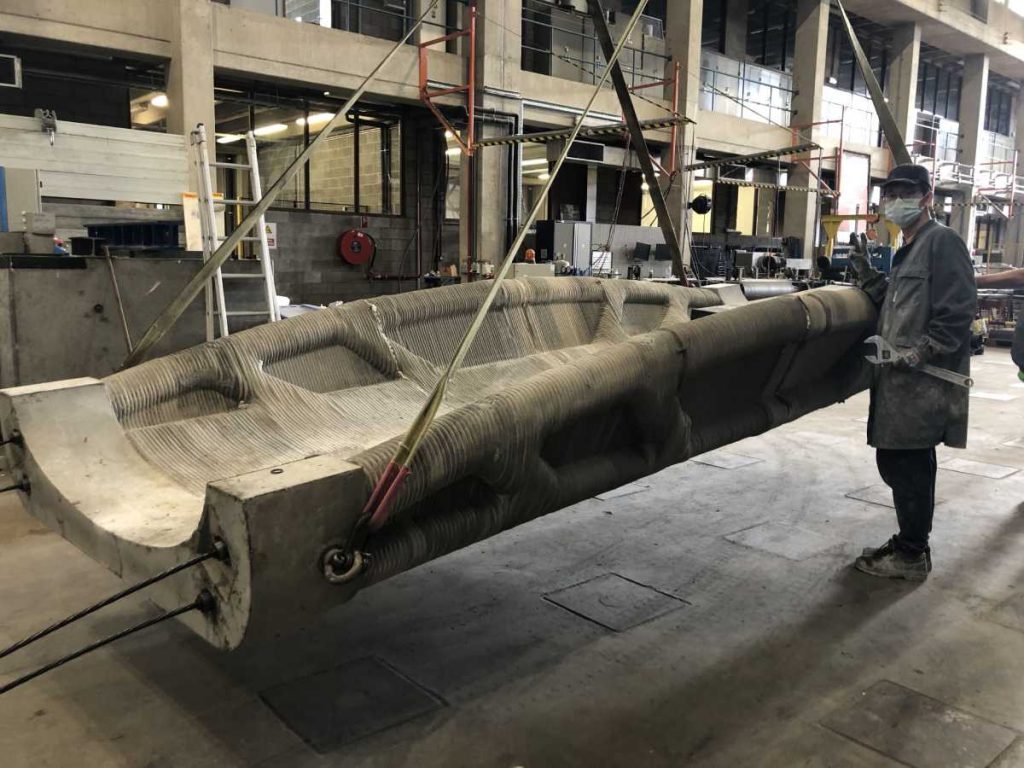
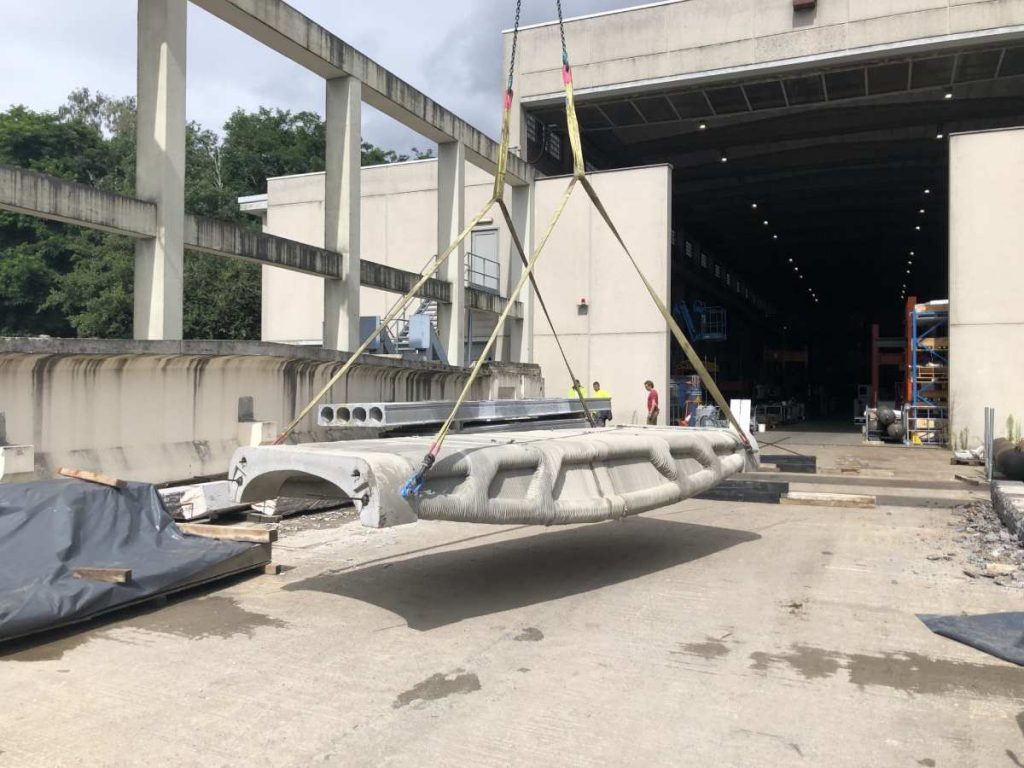