En este artículo -publicado originalmente en la revista Shotcrete Magazine de la American Shotcrete Association- se analizan los distintos desafíos que tuvo este interesante proyecto y cómo el shotcrete u hormigón proyectado resultó clave para llevarlo a cabo, pese a los constantes inconvenientes que presentó la obra.
Autor: David Graham, director de proyectos en PCIRoads, con más de 40 años de experiencia en la industria del shotcrete, participando en numerosos proyectos que incluyen el uso de hormigón proyectado en edificaciones, puentes, túneles, represas, silos y estabilización de suelos.
Fuente: Shotcrete Magazine
La represa y esclusa de Ice Harbor se autorizaron bajo la Ley de Ríos y Puertos de 1945. Construido en 1956, el proyecto incluye una represa, una planta de energía, una esclusa de navegación, dos pasos para peces, un vertedero removible y una instalación para facilitar el desvío para peces juveniles. Proporciona navegación, energía hidroeléctrica, gestión de riesgo de inundación, ecosistema para peces y la fauna de la zona, recreación y riego incidental.
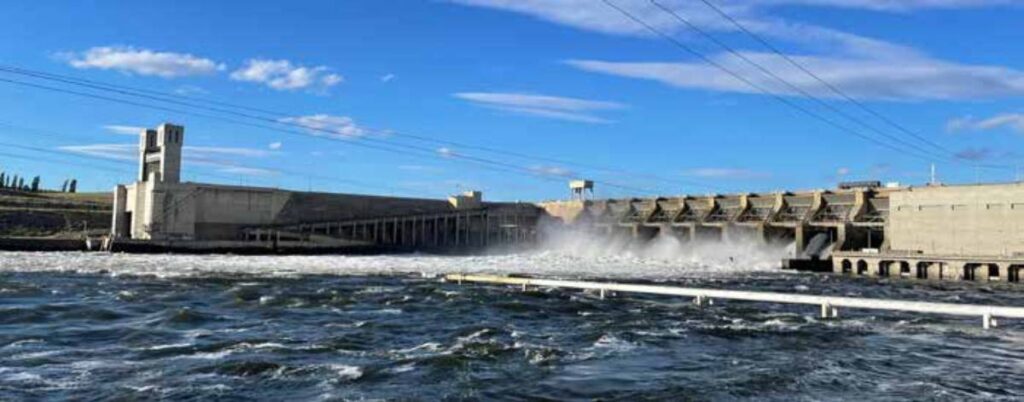
La represa, ubicada en el río Snake, cerca de la confluencia con el río Columbia en Burbank, Washington, tiene una longitud de 860 metros con una altura efectiva de 30 metros. Es una represa de gravedad construida con hormigón, con un terraplén de tierra.
En 2016, el propietario adjudicó un contrato para reconstruir tres unidades generadoras para mejorar las condiciones hidráulicas para el paso de peces y mejorar la eficiencia de generación eléctrica de las turbinas.
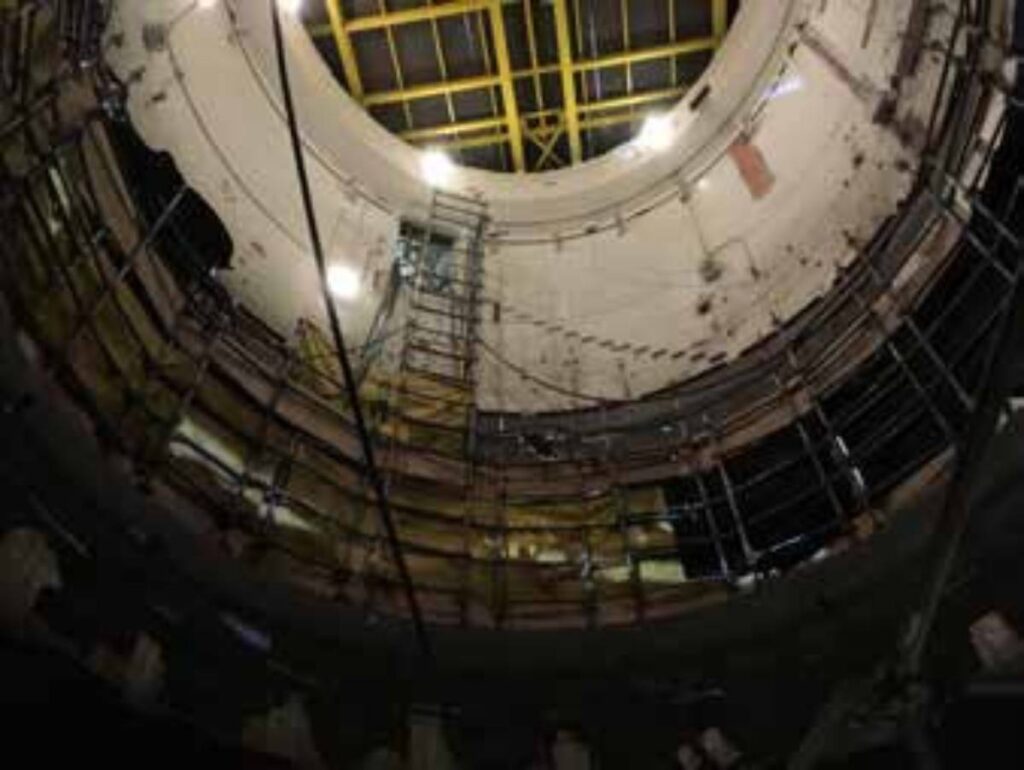
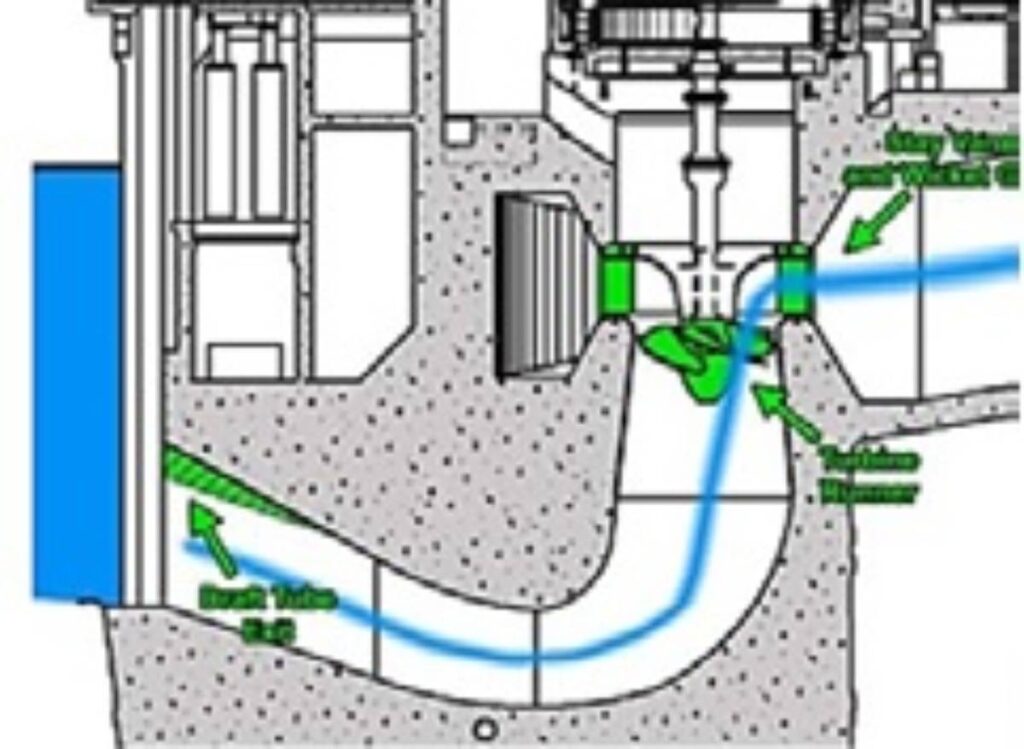
Este contrato incluyó modificaciones estructurales en el techo del tubo de aspiración, lo que requirió la aplicación de shotcrete húmedo o de mezcla húmeda acelerado con 59 kg/m3 de fibra acero, hasta 1,9 m de espesor en aplicaciones de altura. Dado que la aplicación de shotcrete en altura con ese espesor es poco frecuente, esto representó un desafío para el diseñador y el contratista.
Maquetas de preconstrucción / Calificación del proceso y del operador de shotcrete
Para calificar el diseño de mezcla del shotcrete, el tipo y la dosificación del acelerante, además de los procedimientos de aplicación de shotcrete por parte de los operadores certificados por ACI, se construyeron varias maquetas de secciones del techo a escala real con espesores de hasta 1,9 metros.
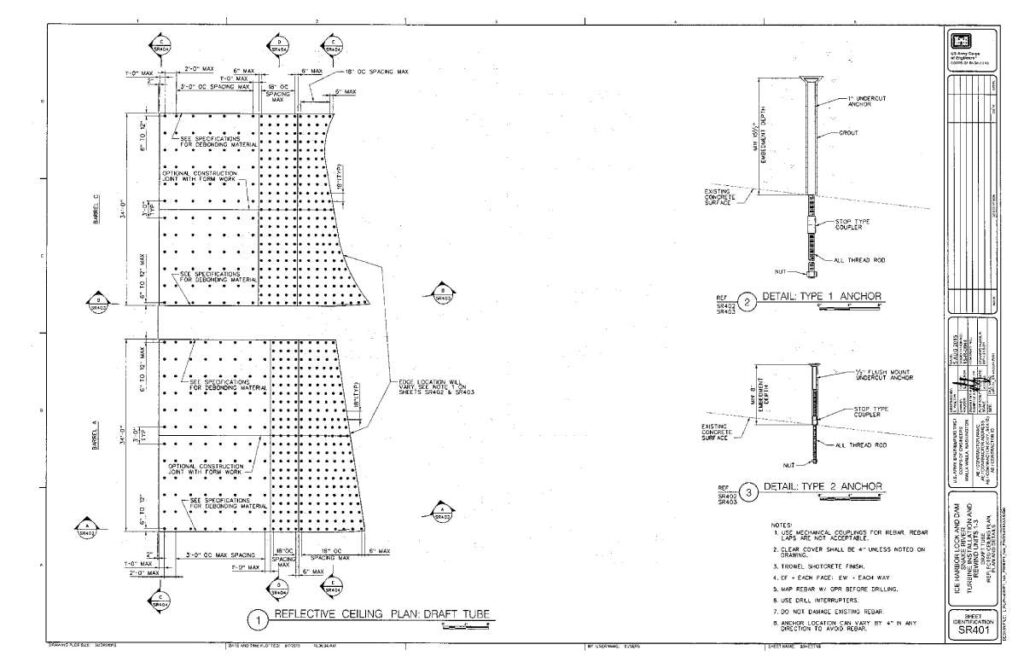
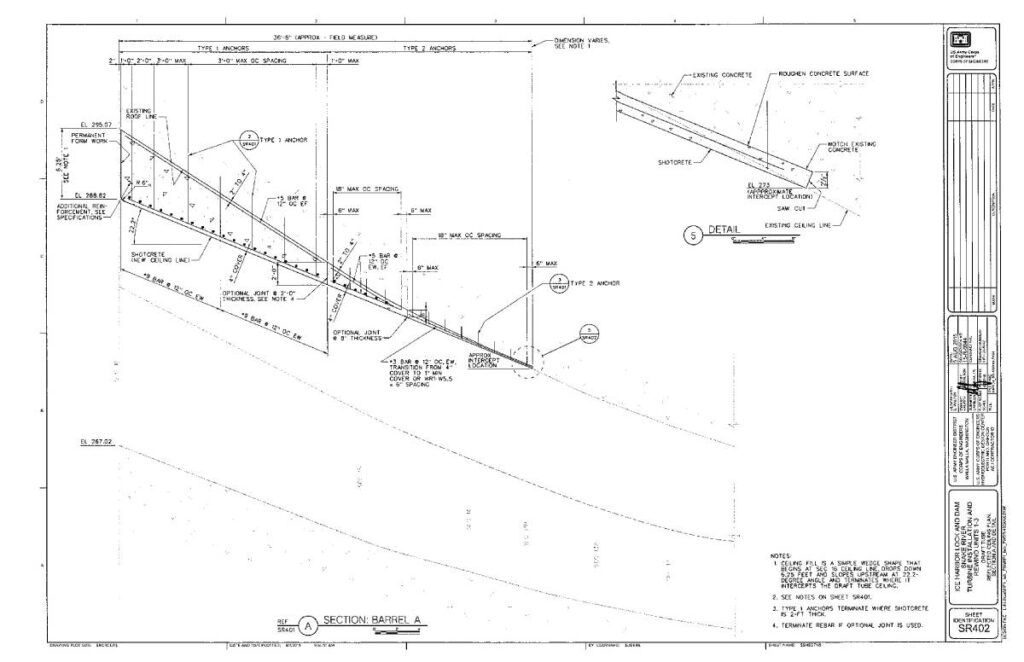
Estas maquetas de las secciones replicaron las condiciones de obra incluyendo anclajes socavados de 25 mm de diámetro, secciones con mallas de acero de refuerzo #9 (#29) y #5 (#13) y el acabado final.
Cada operador de shotcrete calificado para este proyecto tuvo que completar una maqueta de preconstrucción aceptable previo a la colocación del shotcrete en el lugar de la obra. Después de la construcción de la maqueta, cada bloque se cortó por la mitad para permitir al ingeniero diseñador realizar una inspección visual de las secciones cortadas y observar la calidad de la envoltura del acero de refuerzo y la consolidación de las múltiples capas de shotcrete colocadas encima.
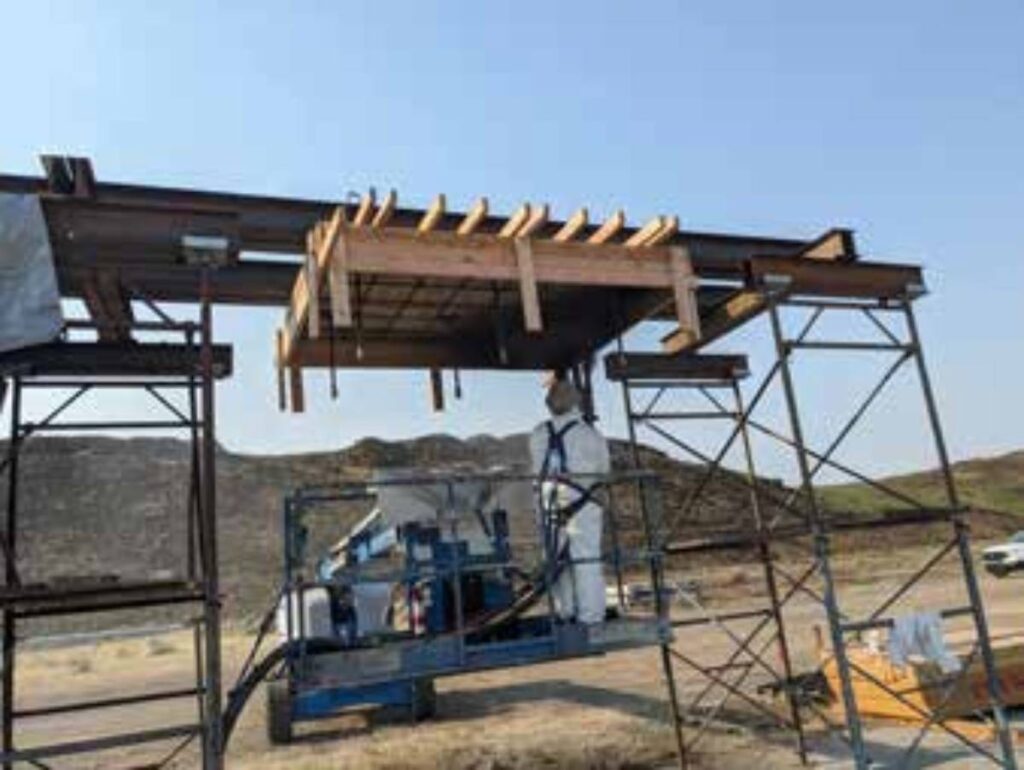
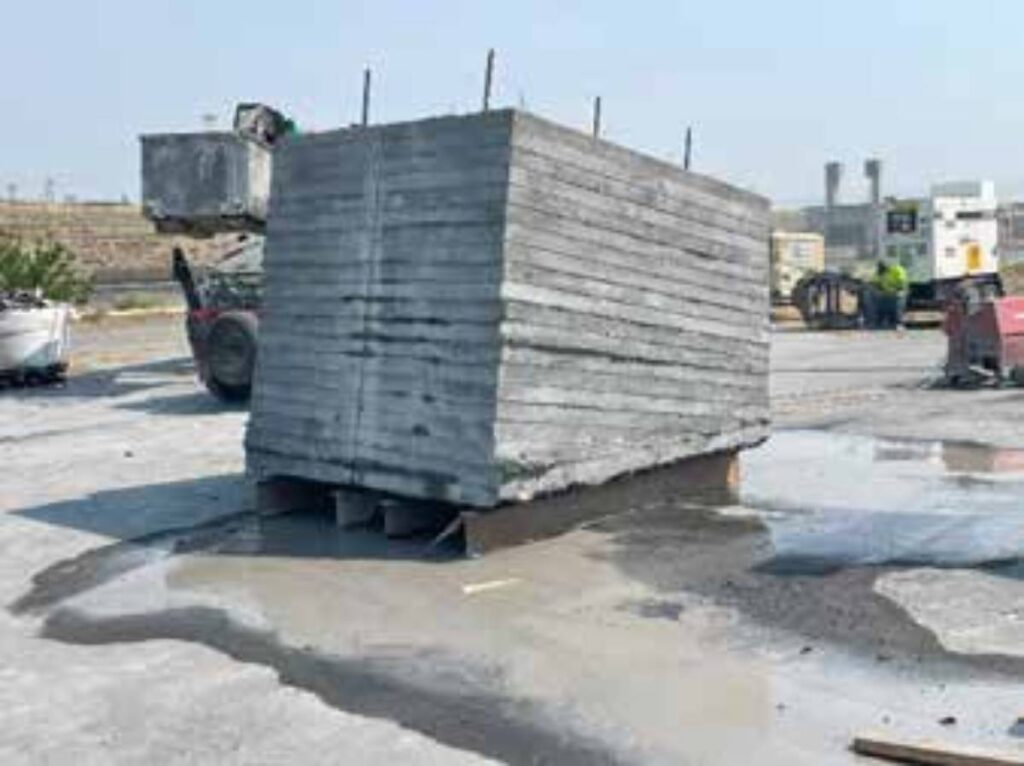
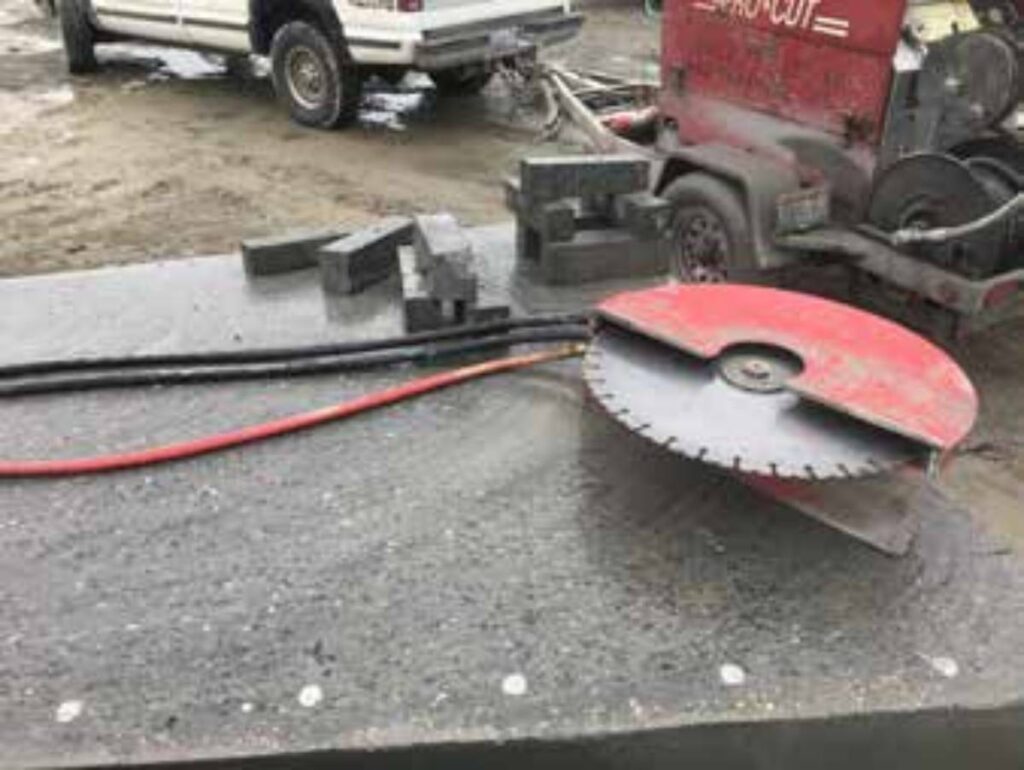
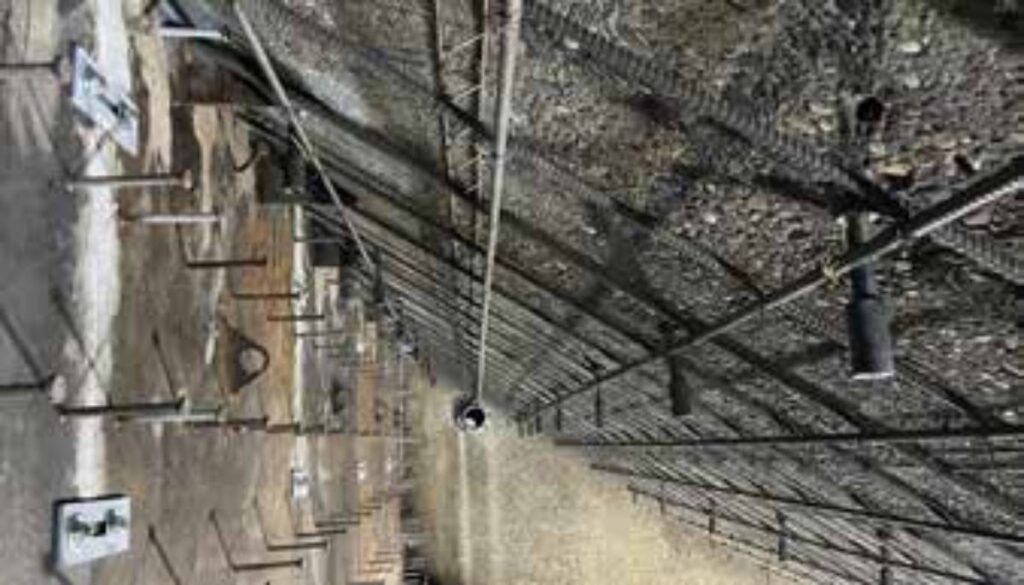
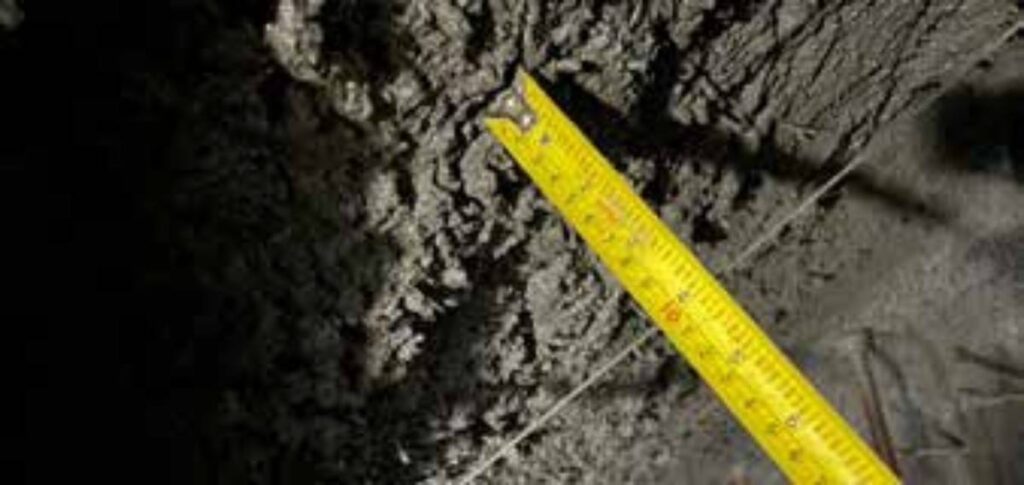
Acceso a la zona de obra
Se instaló un andamio seccional dentro del área del tubo de aspiración, desde el nivel de piso hasta el techo. La elevación de la plataforma de trabajo se redujo según fuese necesario durante la construcción a medida que avanzaba la colocación del shotcrete.
Preparación de superficie – Acero de refuerzo – Anclajes suplementarios
Previo a la colocación del shotcrete, todas las superficies de hormigón existentes que recibirían al hormigón proyectado se prepararon utilizando una técnica de arenado abrasivo según ICRI CSP 7.
El borde de ataque se cortó con sierra y se removió el hormigón para obtener una sección de shotcrete de al menos 63 mm de espesor. Se instaló un encofrado de acero permanente de 1,9 m de altura recto y a plomo, con una separación de 50 mm desde el mamparo temporal de la compuerta tipo stop log. Se instalaron anclajes suplementarios que incluyeron anclajes socavados de 13 mm y 25 mm de diámetro. Las mallas de acero de refuerzo #5 y #9 se instalaron según el plano.
Colocación del shotcrete y acabado final
La colocación del shotcrete acelerado de mezcla húmeda, reforzado con fibra de acero y modificado con humo de sílice, comenzó después de que toda la preparación de la superficie, los anclajes suplementarios y el acero de refuerzo fueran instalados y aprobados. El shotcrete se colocó en capas consecutivas hasta un máximo de 100 mm de espesor hasta que se terminaba una sección completa.
Se utilizó alambre de piano de acero para el control de nivelación entre las capas. El material para la capa final de 50 mm se construyó utilizando la gradación #2 para áridos que aparece en ACI 506R, humo de sílice y shotcrete de mezcla seca reforzado con fibra de polipropileno. El acabado final se realizó con un cepillo ligero, con una tolerancia de 6 mm en 3 metros.
Control de calidad de la producción y aseguramiento de la calidad
Inspectores calificados monitorearon en todo momento el trabajo. Después de la producción diaria, los inspectores completaron informes de verificación que se entregaban diariamente. Se realizaron pruebas de campo para registrar la temperatura ambiente, la temperatura del hormigón entregado, los contenidos de aire en la dosificación y en la inyección y los tiempos de fraguado inicial y final. Se realizaron ensayos del shotcrete en moldes de viga para determinar la resistencia a la compresión a edad temprana utilizando un ensayador de vigas de extremo.
El contratista disparaba un panel de ensayo de producción de shotcrete cada 38 m3 del shotcrete colocado o uno por día, lo que ocurriese más frecuentemente. Los testigos se extrajeron de los paneles de ensayo para determinar:
- Resistencia a la compresión a 7, 28 y 56 días
- Absorción hervida y volumen de los vacíos permeables según ASTM C642 a 28 días
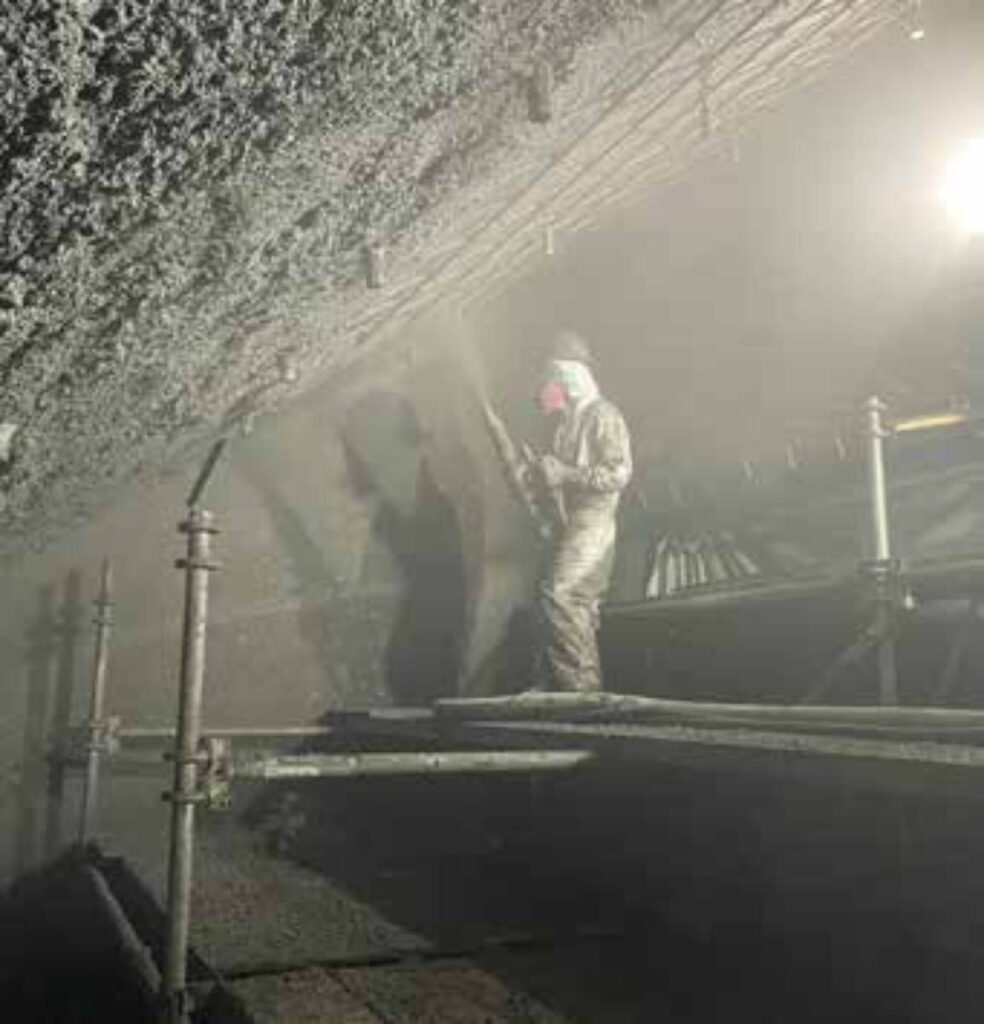
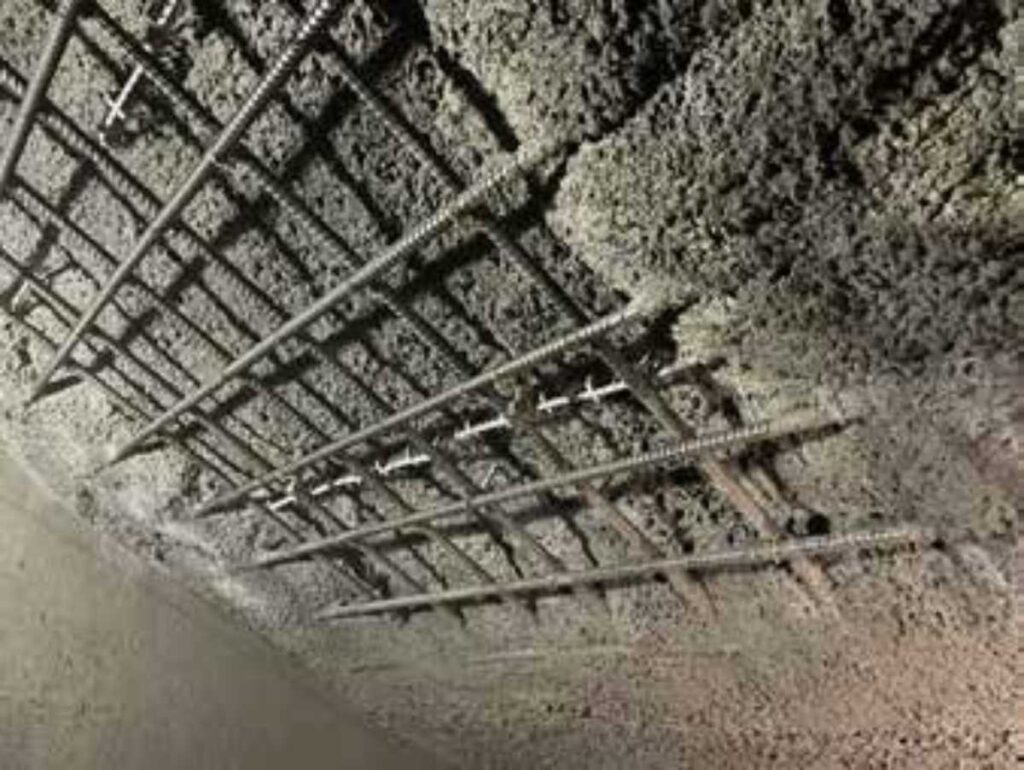
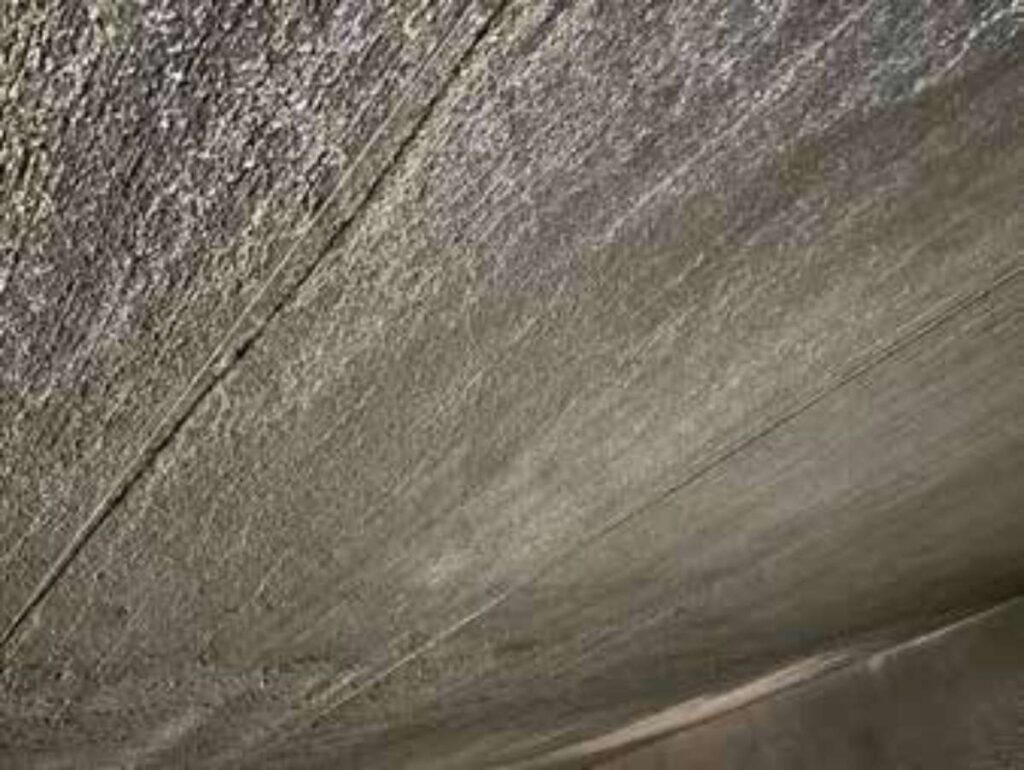
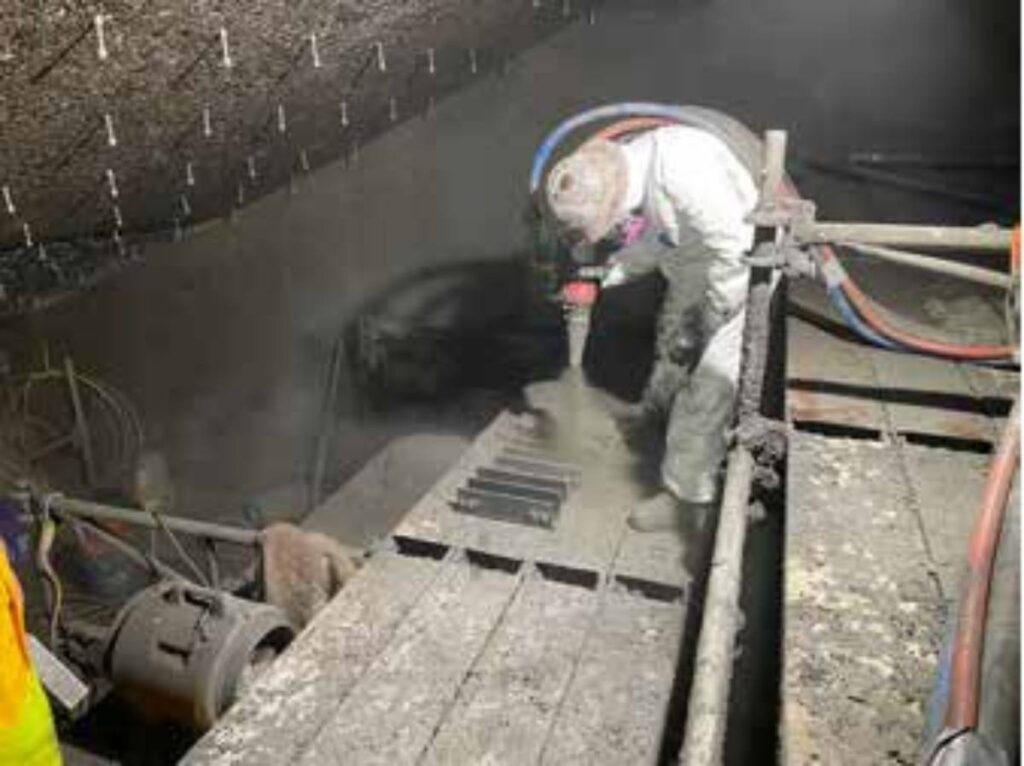
Se realizaron pruebas de adherencia para determinar la resistencia a la adherencia del shotcrete al sustrato de hormigón preparado. El ensayo de resistencia a la adherencia se realizó después de que el shotcrete aplicado al sustrato original de hormigón preparado hubiera curado por un mínimo de 7 días. Los ensayos de resistencia a la adherencia también se realizaron para evaluar la adherencia entre las capas de hormigón.
Desafíos del proyecto
- Difícil acceso debido a que el lugar de la obra se encuentra en el interior de la estructura de la represa
- Limitaciones de las grúas puente y requisitos de uso compartido
- Eliminación de materiales de residuo
- Filtraciones en las juntas de las compuertas desmontables
- Condiciones climáticas: Veranos calurosos e inviernos fríos
- Contrato plurianual, 2016-2024
- Retrasos en la actividad de construcción, ocho meses de paralización por COVID
- El cemento Portland cambió de Tipo I a Tipo IL en 2023
- El cambio de fuente de cenizas volantes en 2021 resultó perjudicial para el desarrollo de la resistencia del diseño de mezcla del hormigón; como resultado, las cenizas volantes se eliminaron del diseño de mezcla durante la fase 2024
- Espacio confinado, ventilación temporal, controles de polvo/vapor, iluminación
Resumen
La construcción de la Unidad No. 2 (2017), Unidad No. 3 (2020 y Unidad No. 1 (2024) demostró que se puede aplicar con éxito un shotcrete de alta calidad, acelerado, de mezcla húmeda, con fibras de acero y modificado con humo de sílice, con espesores de hasta 1,90 metros en superficies superiores. La modificación estructural a los tubos de aspiración se completó utilizando shotcrete de mezcla húmeda, a excepción de la capa de acabado final de shotcrete, de 50 a 100 mm, la que se construyó utilizando shotcrete de mezcla seca.
Referencias
1. Radomski S., Morgan D.R., Zhang L., Graham D., Structural Modifications to Hydroelectric Turbine Draft Tube Ceiling, Shotcrete Magazine. Summer 2019, pp 22-34.
2. Zhang L., Radomski S., Morgan D.R., Graham D., Structural Modifications of Draft Tubes Using Overhead Wet-Mix Steel Fiber Reinforced Shotcrete, Concrete Repair Bulletin, International Concrete Repair Institute, Inc. July/August 2022, pp 20-28.