Planificación, tecnología y rigor en el procedimiento son factores determinantes en la construcción de un piso industrial. Expertos del rubro entregan con detalles las principales claves para una construcción de alto estándar.
El exitoso desarrollo y crecimiento tecnológico que ha experimentado el sector de los pisos industriales en Chile durante los últimos años, especialmente en el último lustro, se debe principalmente a un mejoramiento continuo en la forma de “hacer bien las cosas”, lo cual le ha permitido situarse hoy a un nivel de talla internacional, si se considera el alto estándar alcanzado en múltiples proyectos de gran envergadura construidos durante los últimos años.
La actualidad de los pisos de hormigón en el país, en cuanto a estándares de diseño, ejecución y calidad de la obra terminada, indica que es posible responder a exigentes especificaciones técnicas que se deben cumplir en proyectos que, por sus características, requieren agilidad, velocidad y eficiencia durante su etapa de construcción, así como rapidez en la puesta en marcha y la minimización del riesgo y necesidad de intervención por trabajos de mantenimiento.
Sin embargo, lo descrito anteriormente solamente ha sido posible y será factible en proyectos futuros, siempre y cuando se mantenga la sinergia entre factores considerados clave, que serían determinantes para el logro de los objetivos y exigencias de un proyecto exitoso de pisos. En este sentido, es importante entender que los pisos son un elemento fundamental para el éxito de la operación y probablemente el principal activo de muchas plantas industriales como lo es, por ejemplo, en los centros de distribución logística. Así, para lograr que un piso sea capaz de responder a requerimientos exigentes y muy específicos, en muchos casos es necesario ir más allá de lo tradicional.
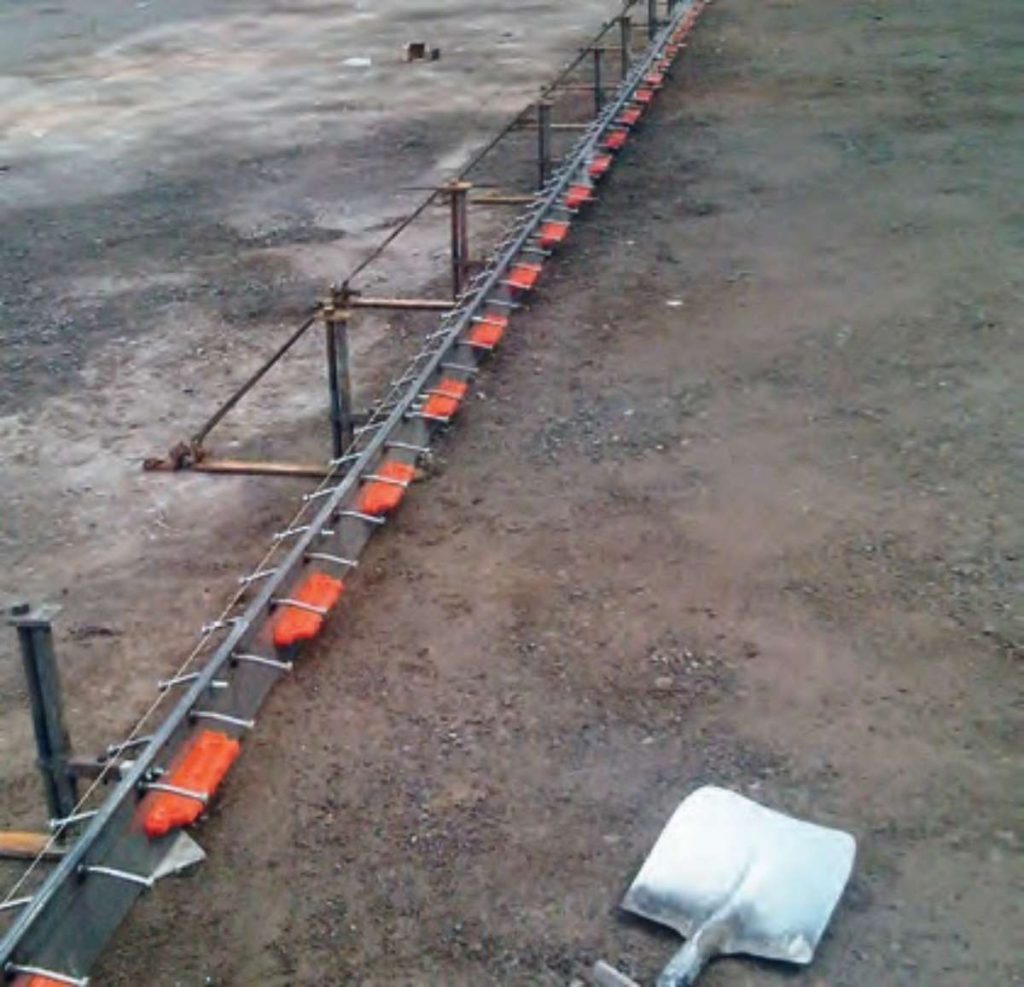
Vale la pena destacar que dentro de estos factores claves, se podrían considerar aspectos como el correcto diseño de acuerdo a las condiciones y uso del piso, uso y aplicación de buenas prácticas que aseguren un alto estándar de calidad y eficiencia, la incorporación de innovaciones tecnológicas que permitan implementar soluciones para casos y situaciones complejas, así como la permanente coordinación entre proyectista, ejecutor, inspección y mandante a lo largo del desarrollo del proyecto desde la fase de planificación hasta el comienzo de la operación.
No obstante, más allá de la importancia y obvia relevancia de cada uno de los aspectos antes mencionados, lo que marca la diferencia, es el alto profesionalismo y constante compromiso por parte de los ejecutores, a lo largo de las diferentes etapas del proyecto, independiente del tamaño, urgencia o presupuesto que se maneje.
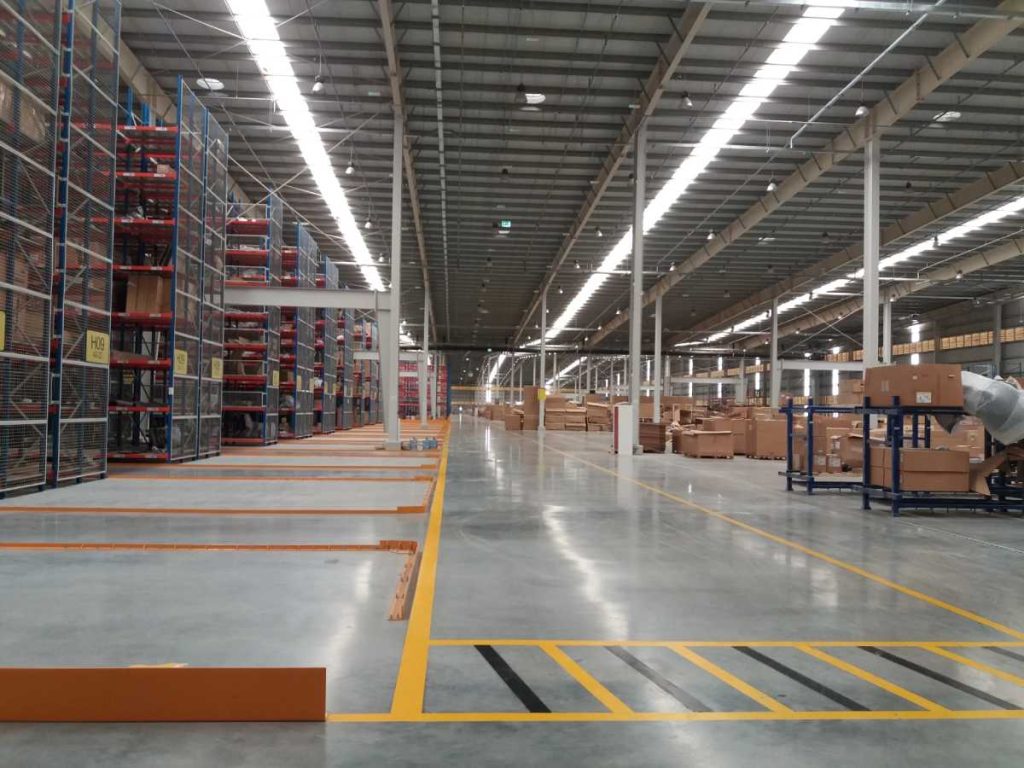
Por lo tanto, conscientes de la importancia de lo anteriormente expuesto, en el presente artículo se reúne la opinión de algunos expertos, de modo de conformar, a partir de su conocimiento y experiencia, un conjunto consolidado de prácticas y recomendaciones para una correcta y cada vez mejor práctica de construcción de pisos de hormigón en Chile.
Recomendaciones que hacen la diferencia
El diseño y la construcción de un piso de hormigón resultan fundamentales para el desempeño de cualquier actividad industrial. Desde ahí, las buenas prácticas en su ejecución deben ser estrictas para responder a las distintas solicitaciones de la industria.
Ya sea un centro de distribución, una fábrica u otra instalación, las compañías requieren y exigen una correcta instalación de un piso competente para el desarrollo de sus actividades y desde esa perspectiva el adecuado diseño del piso es fundamental, incluyendo desde un comienzo la correcta definición y especificación de la ejecución y terminaciones que aseguren su vida útil.
Y es que según Agustín Escámez, director general de Monofloor, “controlar todos los condicionantes que rodean la construcción de un piso industrial, es garantía de durabilidad, buen acabado del piso y rendimiento de la actividad para la que está destinado”. Es una partida crítica puesto que de ella no solo depende la operación y la producción de la industria, sino que también gran parte del ciclo de la estructura. “Una superficie apropiada no solo garantiza el funcionamiento de las máquinas de operación logística, sino también, la velocidad operativa en toda la edad del edificio”, añade Rodrigo Varela de Gestión Arquitectónica RVDLC.
Antes de entregar las recomendaciones para una óptima ejecución del proyecto de pisos, los expertos advierten prestar atención a un paso anterior, que dice relación con conocer detalladamente el uso que tendrá el piso. Se trata de un trabajo que debe quedar en manos de diseñadores y técnicos especialistas, para que puedan especificar la mejor solución para responder a las necesidades identificadas. “Tras un correcto diseño, la elección de los materiales adecuados es fundamental: tipo de hormigón y su debida dosificación, que debe ser estudiada con minuciosidad, tipo de armado y la elección de revestimiento cementoso o resinoso adecuado al uso”, indica Escámez.
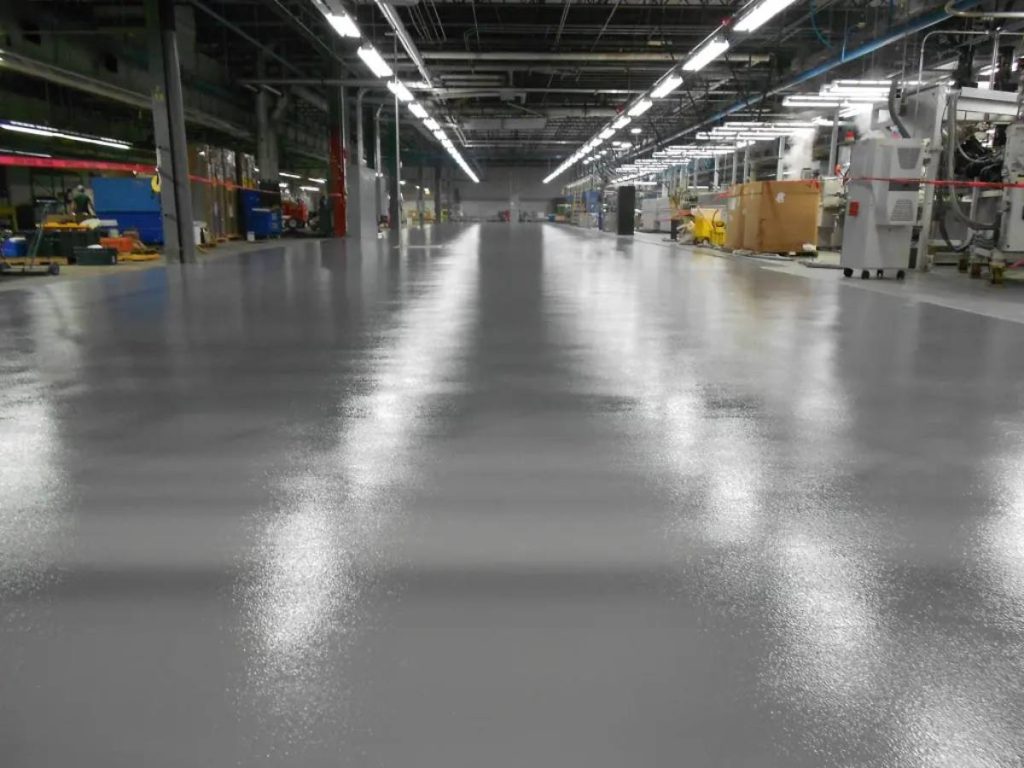
Otro tema crítico a considerar con antelación, dice relación con las juntas. Una frase recurrente entre los especialistas de todo el mundo es que “los pisos mueren por sus juntas”, afirma los expertos. Es por ello que una de las recomendaciones es que las juntas sean preformadas con protección de los labios junto con conectores de doble movimiento para que las losas se muevan libremente y no se generen tensiones. “La eliminación total o la minimización de las llamadas ‘juntas de corte’ o ‘juntas de contracción’ es una recomendación básica a la hora de pensar en la durabilidad futura de un piso y de su costo de mantención”, añaden.
Otro ítem relevante dice relación con las restricciones y el tipo de hormigón adecuado para cada situación. En el caso de las primeras, Juan Pablo Covarrubias advierte que “una nivelación con tolerancias altas del piso evitaría restricciones” y, a su vez, respecto del hormigón, “se debe tener especial cuidado en la fluidez elegida, el tiempo que esta fluidez se mantiene (uso correcto de aditivos) y una cantidad de mortero suficiente que permita trabajar correctamente la superficie”, precisa.
Finalmente, para mejorar la productividad en la ejecución del piso, una de las recomendaciones es emplear equipos y herramientas de última tecnología como sería el Laser Screed, Bump Cutter, Channel Folat, platachos anchos, ente otros.
Tal como se ha señalado y luego de revisar los puntos críticos que hay que considerar y atender antes de ejecutar un proyecto de pisos, los principales expertos congregados por Revista Hormigón al Día han coincidido en las siguientes recomendaciones para ejecutar un piso de hormigón convencional:
1. Solicitar los ensayos de las bases y consultar al mandante por el futuro uso de la bodega. Recepcionar el lugar y hacer un levantamiento topográfico. Se aceptan tolerancias negativas (0 a -1cm ya que normalmente el diseño de los pisos es de espesor mínimo.
2. Tras la fase de diseño, viene la fase constructiva. Se procede con la dirección de la obra. Se estiman los días de ejecución. Se coordina con el servicio de hormigón. Se recomienda que el galpón debe estar terminado, techado y cerrado para favorecer el hormigonado. Uno o dos días antes, se colocan los moldajes, juntas y refuerzos de acero. La instalación de las juntas de construcción debe ser exquisita en su nivelación y fijación, siendo recomendable un rango de error de +2 mm. Para ello se deben utilizar aparatos de nivel adecuados.
3. El día del hormigonado, y dependiendo del tipo de aplicación, puede ser necesario instalar algún material que procure la reducción del coeficiente de roce de la base con el hormigón.
4. Una vez está lista la preparación del terreno, se realiza el vaciado del hormigón directo o con bomba a una temperatura no inferior a 5º C y no superior a 35º Celsius (según NCh170). No debe haber diferencia de tiempo entre un hormigonado y otro (se precisa que los camiones estén cada diez o 15 minutos en obra).
Un asentamiento constante a la recepción del hormigón debe ser garantía de homogeneidad de fraguado. El cono no debe diferir más de 3 cm del cono de diseño, que debe ser fluido en el caso de utilizar maquinaria de extendido (mínimo cono: 12 cm). También se debe testear la base a través de ensayos normalizados (ensayos Próctor, densidad in situ, CBR y ensayos de Placa de carga).
5. Tras ello, se procede a nivelar con máquinas láser. Su manejo debe ser realizado por personal cualificado y se debe comprobar el nivel de acabado cada 300 m2 de extendido mediante topografía.
6. En caso de aplicar endurecedores en base a cuarzo con medios mecánicos es fundamental contar con agua de exudación suficiente para su hidratación. No se puede agregar agua externamente ya que se corre el riesgo de zonas blandas o delaminación. La dosis de endurecedor deberá ser de entre 2,5 a 5 kg por m2 (Zona central de Chile). El no uso de endurecedor superficial es posible bajo ciertas condiciones de materiales y de procedimientos de terminación con acabados mecánicos de desnificacion de la superficie. O, después de aplicado el endurecedor, se pasan herramientas sobre la superficie de forma manual para rectificar la planimetría. Enseguida, se realiza el alisado mecánico para cerrar los poros del hormigón.
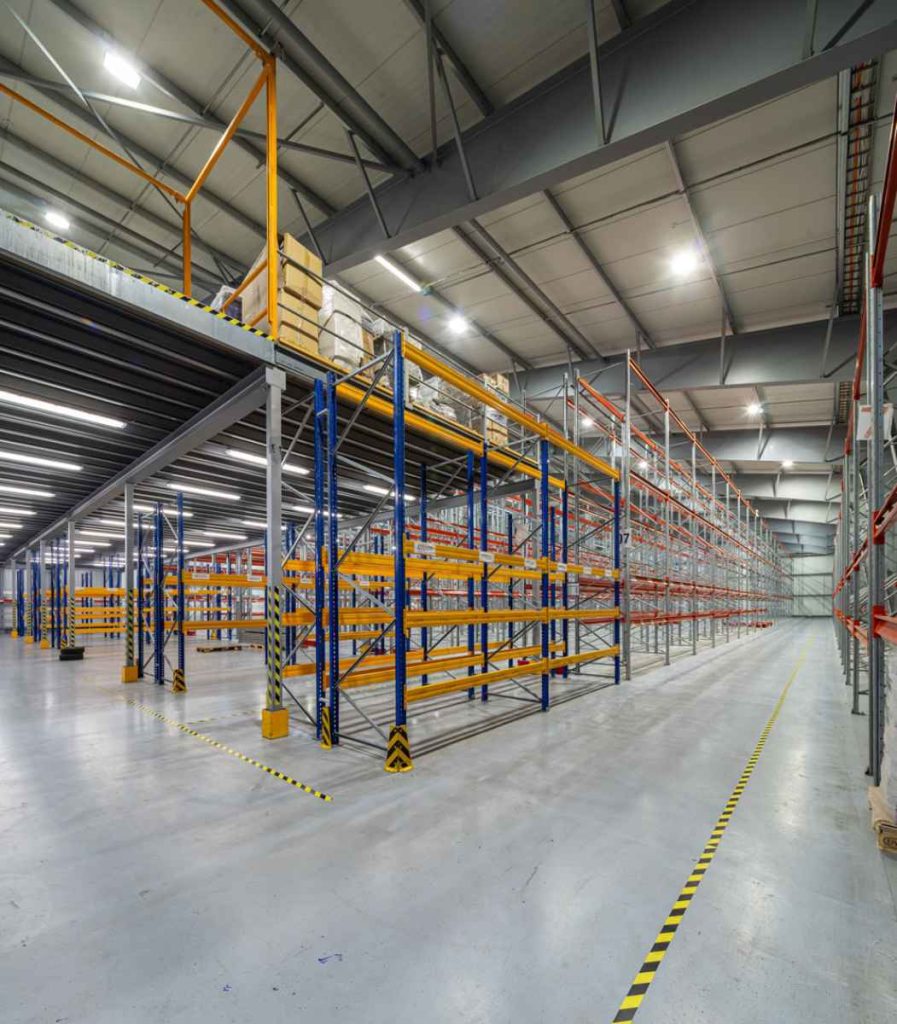
7. Transcurridas 12 a 24 horas, se procede con el aserrado del hormigón (salvo sea un piso continuo). Para ello, se implementa una cortadora tradicional o Softcut desde las 6 hr (máquina de corte en fresco) que induce la fisura y se evita la retracción.
8. Finalizado el proceso anterior, viene la fase de curado del hormigón. Se debe humectar y poner un plástico o elemento que retenga el agua. Se tiene que esperar mínimo siete días.
9. En el intertanto se continua con el relleno de juntas, epóxico, semirrígido o poliurea, o sellado, para lo cual se utiliza poliuretano o siliconas.
10. Según la especificación del proyecto, se realiza un trabajo de pulido o aplicación de endurecedores. finalmente, se limpia para la entrega definitiva.
Más referencias
A lo anterior, también se añaden las siguientes consideraciones en la planificación de este proceso constructivo.
Logística constructiva: Previo a la ejecución de los pavimentos, la Administración de la Obra debe programar reuniones de coordinación con los diferentes actores de la actividad.
En estas reuniones deberán proponerse y coordinarse las actividades previas y durante la ejecución de los pavimentos. En esta fase se recomienda:
- Coordinación para actividades de recepción de nivelación de la base.
- Presentación de muestra de moldaje para aprobación de la ITO.
- Estudio y programación de fechas para la secuencia de hormigonado.
- Presentación de proveedores de la actividad: hormigones, bombeo, endurecedores, aplicadores de pavimentos, equipos, etc.
- Presentación y aprobación de equipos y personal propuesto por los aplicadores para la ejecución de los pavimentos.
- Presentación y aprobación de requerimientos de hormigón especificados y de los procedimientos a emplear por los aplicadores.
- Coordinación para la logística de hormigonado: posición de las bombas, accesos, programación de los camiones mixer, pruebas de laboratorio, etc.
- Revisión de condiciones generales del terreno previo a la ejecución de fajas iniciales.
El contratista debe celebrar contratos con proveedores y subcontratistas que garanticen que los servicios, insumos o equipos proporcionados por los subcontratistas o proveedores cumplan los requerimientos del mandante, expresados a través de las especificaciones técnicas.
Con todo, el espesor máximo de la capa de nivelación será de 10 a 20 milímetros, mientras que la tolerancia final a producir será de +0 –3 milímetros.
Verificación topográfica: Se realiza mediante una cuadrícula lienzada de 3×3 metros, con lectura de 9 puntos: 3 superiores, 3 de tipo intermedio y 3 inferiores.
Se efectúa mediante nivel óptico, a una distancia inferior a 25 metros. Se debe registrar en cartilla y plano referido a los ejes del proyecto.
Las áreas que no cumplan con la disposición de nivelación requerida se marcan mediante un anillo tizado e identifican con una banderilla plástica numerada, montada sobre estaca.
Trazado de hormigonado: el área se examina en detalle por los controladores, en forma anterior a la ejecución.
Hormigonado: Vaciado con control de nivelación, cerchado y vibración en puntos muertos como pies de columnas, bordes de moldes, muros y a todo elemento que quede embebido en los hormigones.
Son las principales recomendaciones para el desarrollo de un piso de hormigón estándar. Criterios puestos en común entre los diversos expertos del rubro que Revista Hormigón al Día ha sintetizado para colaborar en el fortalecimiento de las buenas prácticas del sector en la ejecución de estas partidas relevantes para la industria.